Plastic PP, or polypropylene, is a versatile and low-cost thermoplastic used in many industries. This article explains its properties, types, applications, and best practices for injection molding.
Understanding Plastic PP
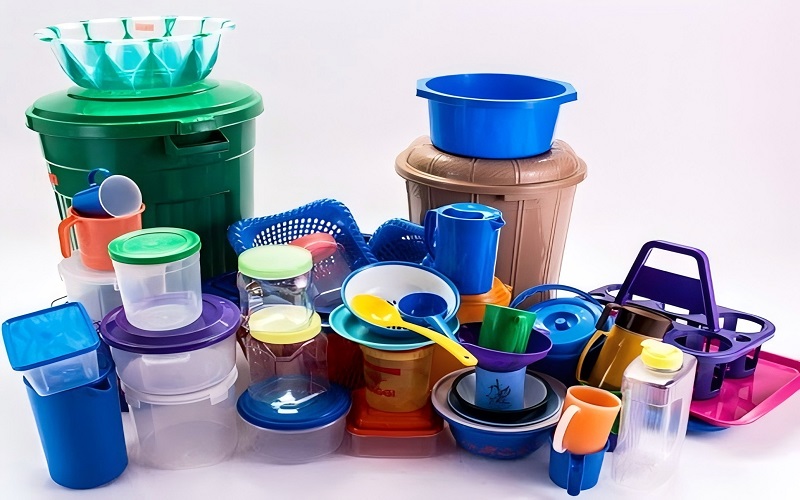
Polypropylene (PP) is a thermoplastic polymer made from propylene monomers, commonly abbreviated as PP and also known as polypropene. Known for its tough and flexible properties, polypropylene plastic, a plastic polymer, has earned its place as a staple in the plastic industry due to its low cost and versatility.
This material can be customized in various ways, making it suitable for a wide range of applications, from everyday consumer products to specialized industrial components.
Types of Polypropylene
Polypropylene comes in two main types: homopolymers and copolymers. Homopolymer polypropylene is known for its excellent strength and stiffness, making it ideal for applications requiring high rigidity. In contrast, copolymers, which include block copolymers and random copolymers, offer enhanced flexibility and impact resistance, making them suitable for more dynamic applications.
Each type of polypropylene is better suited for specific applications. For instance, homopolymers might be used in products like piping systems where rigidity is essential, while copolymers are more suited for applications like automotive bumpers, where flexibility and impact resistance are key.
Key Properties
Polypropylene boasts a semi-crystalline structure with an ordered molecular arrangement, contributing to its mechanical strength and durability. It exhibits good fatigue strength and a low coefficient of friction, enhancing its utility in various mechanical applications. Additionally, polypropylene is resistant to a wide range of bases and acids, although it has poor resistance to chlorinated solvents and aromatics.
However, polypropylene has some drawbacks, including poor bonding properties, challenging its use in applications involving paints or adhesives. Its melting temperature is higher compared to polyethylene, which allows it to perform better in thermal environments. However, its high thermal expansion coefficient needs to be managed during processing to ensure dimensional accuracy.
Common Applications
Polypropylene’s versatility makes it a popular choice across multiple industries. In the automotive sector, its lightweight and durable properties make it ideal for various molded plastic components, such as car battery cases and dashboards. For consumer products, polypropylene’s flexibility and resilience are leveraged to create containers, toys, and household items.
In the medical field, polypropylene is favored for its ability to be sterilized and its chemical resistance, making it suitable for chemically resistant medical supplies like syringes and specimen bottles. Its application in these diverse fields underscores the material’s adaptability and the critical role it plays in modern manufacturing.
Advantages of Polypropylene Injection Molding
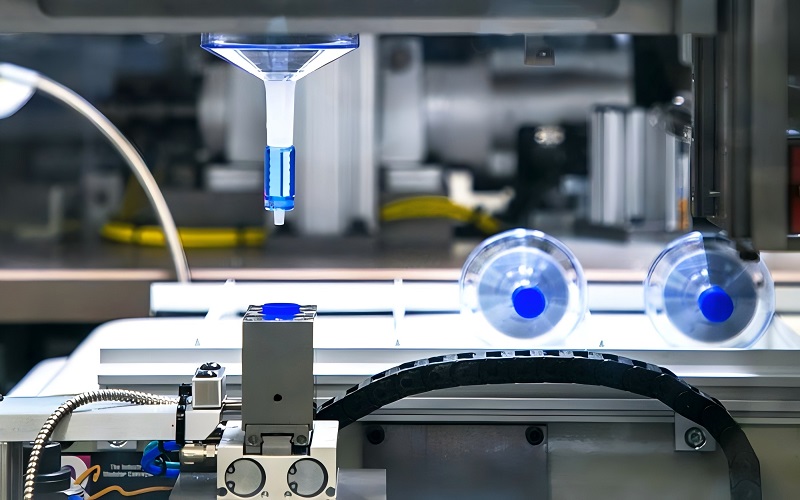
Polypropylene injection molding offers numerous advantages, making it a preferred choice in various industries. This polypropylene injection molding process leverages the unique properties of polypropylene, such as its low melt viscosity, excellent moisture resistance, and cost-effectiveness, to produce high-quality products efficiently.
These advantages enable manufacturers to produce durable and flexible products in large volumes while minimizing defects.
Cost-Effectiveness
One of the most significant advantages of using polypropylene in injection molding is its cost-effectiveness. Polypropylene ranks among the least expensive thermoplastics available in the market, making it an attractive option for manufacturers looking to produce high-quality products at a lower cost. This affordability is particularly beneficial for large-scale manufacturing, where cost savings can be substantial.
Moreover, the cost-effectiveness of polypropylene does not come at the expense of quality. Despite its low cost, polypropylene retains excellent mechanical properties, making it a reliable material for a wide range of applications, from automotive parts to household goods.
Moisture Resistance
Polypropylene is renowned for its moisture resistance, which is a crucial property for many applications. This material exhibits a moisture absorption rate of less than 0.01% over a 24-hour period, making it highly resistant to moisture. This resistance is particularly beneficial for products like food containers, where exposure to high humidity environments is common.
The waterproof characteristics of polypropylene make it an ideal choice for plastic containers, providing safety and durability. This property also extends the lifespan of products, ensuring they remain functional and safe for use over extended periods.
Low Melt Viscosity
Another notable advantage of polypropylene is its low melt viscosity, which significantly enhances the injection molding process. The low viscosity allows for faster injection cycles, reducing production time and increasing efficiency. This property also enables the material to quickly fill molds, ensuring precision and reducing the likelihood of defects.
Polypropylene’s low melt viscosity is particularly advantageous for creating thin molding features, such as living hinges, which require precise and efficient molding. This efficiency and precision make polypropylene a preferred choice for manufacturers looking to optimize their production processes.
Challenges with Polypropylene Injection Molding
While polypropylene injection molding offers numerous benefits, it also presents several challenges. These include high thermal expansion, poor bonding properties, and sensitivity to ultraviolet (UV) light. Addressing these challenges is crucial for ensuring the quality and durability of the final products.
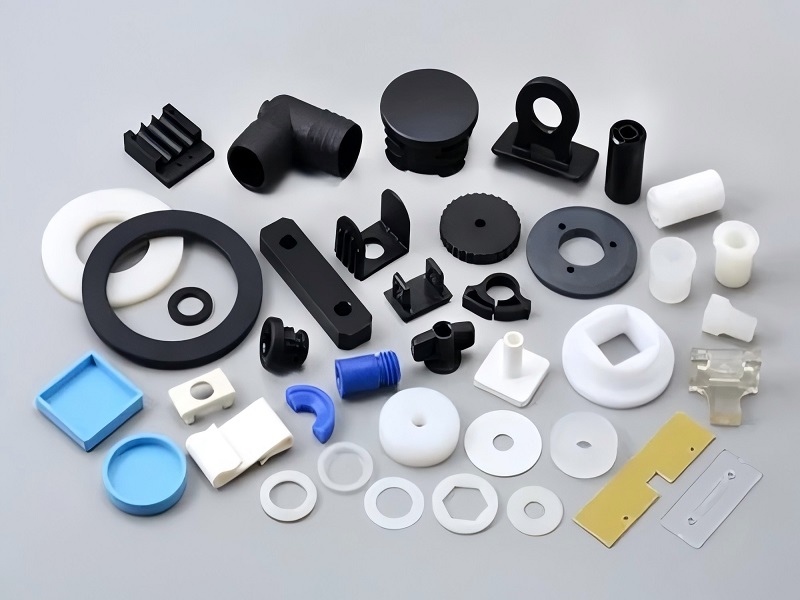
High Thermal Expansion
Polypropylene exhibits a notable thermal expansion, which can lead to dimensional changes in molded parts when exposed to varying temperatures. This high thermal expansion coefficient is a critical consideration in applications requiring dimensional stability, such as precision components.
The degree of thermal expansion in polypropylene is influenced by its crystalline structure, which affects how the material expands and contracts with temperature fluctuations. In applications where precision is crucial, careful design considerations are necessary to manage this property effectively.
Poor Bonding Properties
One of the significant challenges of working with polypropylene is its poor bonding properties. This material exhibits weak adhesion, complicating processes that require joining or coating with other materials. This weak adhesion poses significant challenges during the injection molding process, where strong bonds are often necessary for product integrity.
To address this issue, manufacturers may need to employ specialized adhesives or surface treatments to enhance bonding. Addressing these bonding challenges is essential for producing high-quality polypropylene products.
UV Sensitivity
Another challenge with polypropylene is its sensitivity to ultraviolet (UV) light. Prolonged exposure to UV light can lead to degradation, affecting the material’s physical properties and longevity. To prevent this, polypropylene products often require protective additives or coatings that shield them from UV rays.
These protective measures help enhance the durability and lifespan of polypropylene products, ensuring they remain functional even under extended UV exposure. These protective strategies are vital for maintaining the quality of polypropylene products used outdoors.
Best Practices for Polypropylene Injection Molding
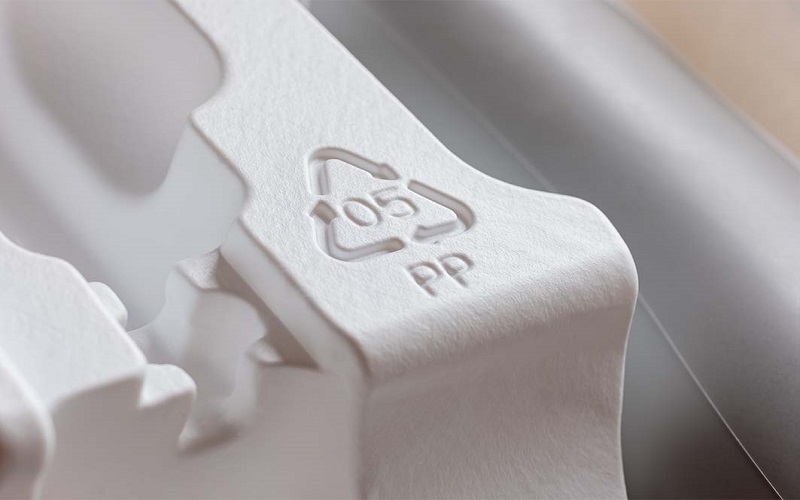
Adhering to best practices is key to achieving optimal results in polypropylene injection molding. This includes controlling mold temperature, adjusting injection speed and pressure, and incorporating thoughtful design considerations.
These practices help ensure the production of high-quality, defect-free polypropylene products.
Mold Temperature Control
Maintaining proper injection mold temperature is crucial in the injection molding process. As molten plastic cools in the mold, it contracts until it is fully structured. To achieve this, mold temperature is controlled by injecting water or oil into the cooling system, maintaining temperatures between 20-80°C.
Proper temperature control ensures that the molded parts cool uniformly, minimizing defects and ensuring dimensional accuracy. This practice is vital for producing high-quality polypropylene products.
Injection Speed and Pressure
The speed and pressure at which polypropylene is injected into the mold play a critical role in the quality of the final product. Higher injection speeds can help reduce the cycle time, increasing production efficiency. However, these high speeds may require adjustments to reduce defects and ensure consistent product quality in the pp injection molding process.
Balancing injection speed and pressure is essential to optimizing the injection molding process. Managing these parameters effectively helps produce high-quality polypropylene products with minimal defects.
Design Considerations
Thoughtful design considerations are crucial for successful polypropylene injection molding. The minimum draft angle for injection molding polypropylene is 1 degree, which facilitates the ejection of parts from the mold. Additionally, maintaining a recommended wall thickness range of 0.635 mm to 3.81 mm helps ensure structural integrity.
Placing the gate on the thickest wall segment of the part ensures effective flow into the cavity, while incorporating generous radii can enhance durability and prevent stress concentration. These design practices are essential for producing robust and reliable polypropylene products.
Processing Parameters for Polypropylene Injection Molding
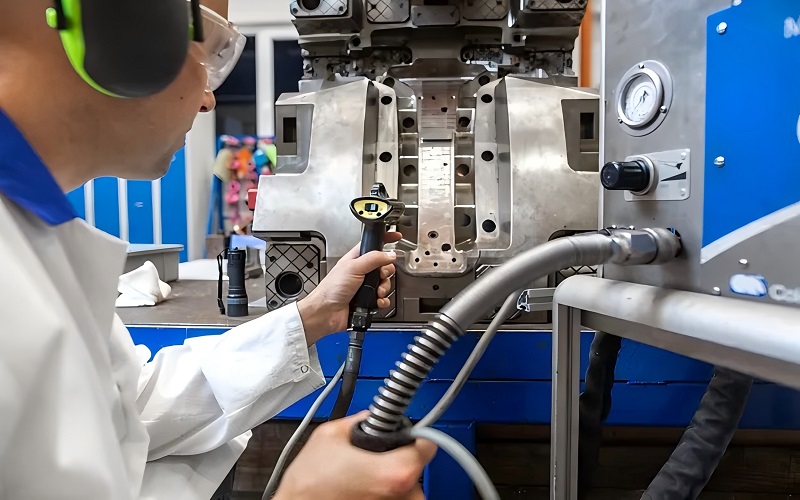
Understanding the processing parameters is crucial for successful polypropylene injection molding. Key parameters include the melting point, shrinkage rates, and cooling time, all of which significantly impact the quality and precision of the final products.
Proper management of these parameters ensures efficient production and high-quality outcomes.
Melting Point
The melting point of polypropylene typically ranges from 160 to 175 degrees Celsius, though it can vary slightly depending on its formulation. Monitoring this melting point is essential for determining the appropriate temperature settings during the molding process. The correct melting point ensures the material flows properly into the mold, forming the desired shape without defects.
Maintaining the right temperature range, typically between 220°C to 280°C, is crucial for processing polypropylene. This range ensures that the material remains in a molten state long enough to fill the mold but cools quickly enough to maintain its structure and properties.
Shrinkage Rates
Polypropylene exhibits a higher shrinkage rate when molded at elevated temperatures, which can affect the dimensional accuracy of the final product. The shrinkage rate of filled polypropylene may vary, often leading to lower shrinkage values depending on the fill material used. Accurately accounting for these shrinkage rates in mold design is essential for producing precise and reliable parts.
Understanding the shrinkage behavior of polypropylene is critical for avoiding dimensional inaccuracies and defects such as sink marks. Proper mold design and process control help mitigate the effects of shrinkage, ensuring the final product meets the required specifications.
Cooling Time
Proper cooling time is essential to avoid warping and other defects in polypropylene parts. If parts are ejected too early, they may not have fully solidified, leading to deformation. Maintaining appropriate mold temperature and cooling medium stability ensures that the parts cool uniformly, preserving their dimensional accuracy and mechanical properties.
The use of cold runner molds can assist in maintaining consistent cooling times, which is crucial for high-quality production. Properly managing the cooling phase of the injection molding process helps produce defect-free polypropylene products with excellent structural integrity.
Common Uses of Injection Molded Polypropylene Products

Polypropylene injection molding is used to create a wide range of products across various industries. Its versatility, lightweight nature, and moisture-proof characteristics make it an ideal material for numerous applications, from automotive components to household goods and medical devices. Plastic injection molding is also a popular method in manufacturing.
These diverse uses highlight the material’s adaptability and critical role in modern manufacturing.
Automotive Components
In the automotive industry, polypropylene is increasingly favored for its durability and lightweight properties. Common automotive components made from polypropylene include:
- car battery cases
- dashboards
- instrument panels
- door trims
Using polypropylene for these parts allows manufacturers to create lighter vehicles that improve fuel efficiency without sacrificing strength.
The ability to manufacture polypropylene parts with precision and consistency makes it a valuable material in the automotive sector. Its application in various components showcases its adaptability and importance in modern vehicle design.
Household Goods
Polypropylene is widely used in household goods due to its flexibility, resilience, and lower density. Common household products made from polypropylene include kitchen appliances, home appliances, toys, furniture, carpets, and mats. Specific items such as food trays, cups, plates, and toys benefit from polypropylene’s lightweight and durable properties.
One of the significant advantages of using polypropylene in household goods is its lower density, which allows weight reductions for producers and sellers. This efficiency makes products more cost-effective to manufacture and transport, benefiting both manufacturers and consumers.
Medical Devices
Polypropylene’s chemical resistance and ability to be steam sterilized make it a suitable material for various medical applications. Common medical supplies made from polypropylene include petri dishes, syringes, specimen bottles, pans, vials, and pill dispensers. These properties ensure that medical devices manufactured from polypropylene are safe, reliable, and durable.
The use of polypropylene in medical devices highlights its versatility and importance in critical applications. Its ability to withstand sterilization processes and resist chemical degradation makes it a preferred choice in the medical field, ensuring the safety and efficacy of medical products.
Summary
Polypropylene injection molding is a versatile and efficient process that plays a crucial role in modern manufacturing. Its unique properties, such as low melt viscosity, moisture resistance, and cost-effectiveness, make it an ideal material for a wide range of applications, from automotive components to household goods and medical devices.
Understanding the advantages, challenges, and best practices associated with polypropylene injection molding is essential for optimizing production processes and achieving high-quality results.
Despite its many benefits, polypropylene injection molding does present some challenges, including high thermal expansion, poor bonding properties, and UV sensitivity. Addressing these challenges through careful design considerations, proper mold temperature control, and the use of protective additives or coatings is crucial for ensuring the quality and durability of the final products.
In conclusion, polypropylene injection molding offers numerous advantages that make it a preferred choice in various industries. By adhering to best practices and understanding the material’s properties and processing parameters, manufacturers can produce high-quality, reliable, and durable polypropylene products. Embracing the potential of polypropylene injection molding will undoubtedly lead to continued innovation and success in the plastic industry.
Frequently Asked Questions
What are the main types of polypropylene used in injection molding?
The primary types of polypropylene utilized in injection molding are homopolymers and copolymers, which encompass block copolymers and random copolymers. These materials offer distinct properties suitable for various applications in manufacturing.
What are the key properties of polypropylene that make it suitable for injection molding?
The key properties of polypropylene that make it suitable for injection molding include its semi-crystalline structure, good fatigue strength, low coefficient of friction, and resistance to various acids and bases. Its higher melting temperature compared to polyethylene also enhances its moldability and versatility in applications.
What are some common applications of polypropylene in various industries?
Polypropylene finds widespread use in automotive components, consumer products such as containers and toys, and medical supplies, including syringes and specimen bottles. Its versatility makes it a valuable material across multiple industries.
What are the advantages of using polypropylene in injection molding?
Utilizing polypropylene in injection molding offers significant advantages such as cost-effectiveness, excellent moisture resistance, and low melt viscosity, leading to high-quality production with minimal defects. These properties make polypropylene an ideal choice for efficient manufacturing processes.
What are the challenges associated with polypropylene injection molding, and how can they be addressed?
Polypropylene injection molding presents challenges such as high thermal expansion, poor bonding properties, and UV sensitivity. These issues can be effectively managed through careful design, precise mold temperature control, and the incorporation of protective additives or coatings.