Trying to decide between plastic vs nylon for your next project? This article compares their properties, applications, durability, and environmental impact to help you choose the best material for your needs.
Understanding Plastic and Nylon
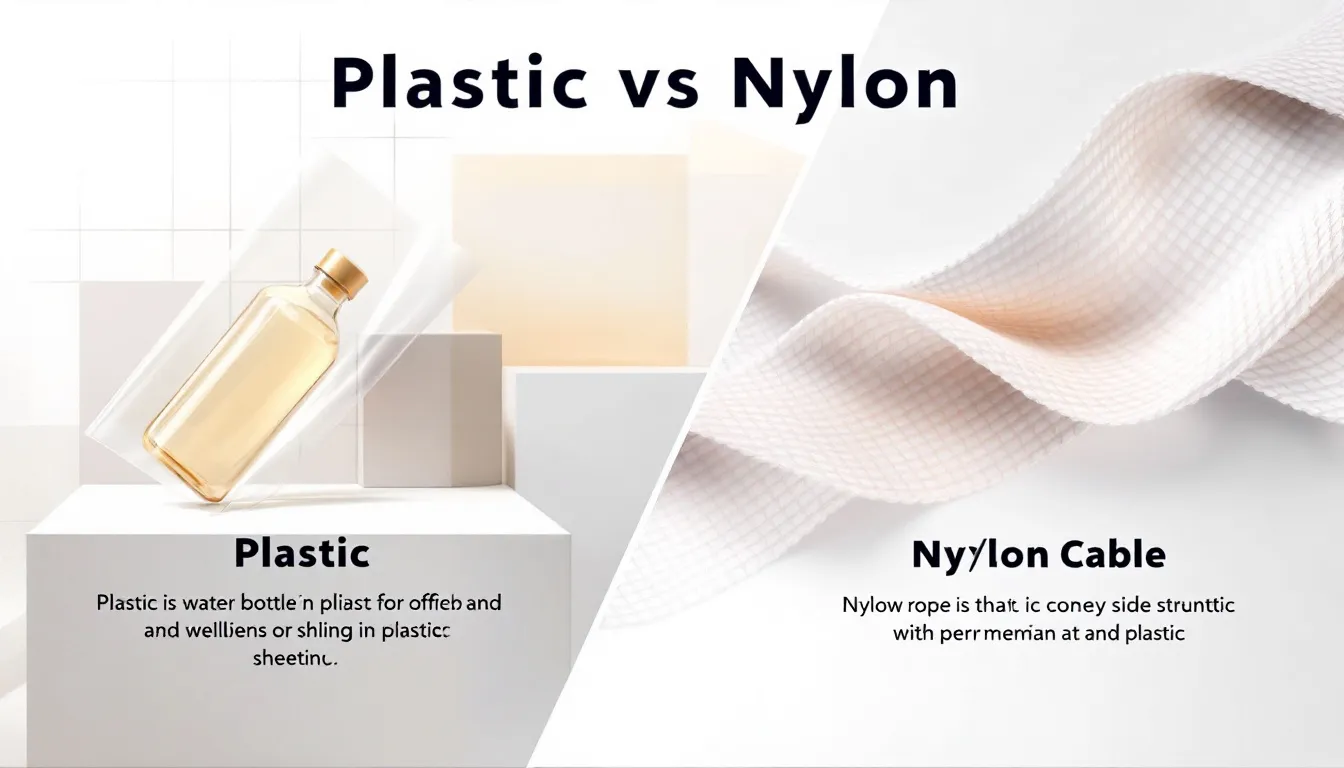
Plastic is a broad category encompassing various synthetic materials, including engineering plastic. The term “plastic” covers an array of materials, each with unique properties and uses. From packaging to automotive parts, plastics are integral to modern life. The creation of plastic products through processes like plastic injection molding allows for mass production of diverse items, catering to numerous industries.
Nylon material, also known as polyamide, is a high-performance plastic made from synthetic polymer nylon polymers, including pure nylon. Invented by DuPont in 1939, nylon material quickly became popular in the 1940s and 1950s for its durability and versatility. Its popularity surged in the following decades, with significant growth in textile consumption during the 1960s to 1980s.
Today, nylon production continues to be significant, with an estimated 8.9 million tons produced worldwide as of 2020. Known for its high-temperature strength and durability, nylon remains a staple in various industries.
Types of Plastics and Nylons
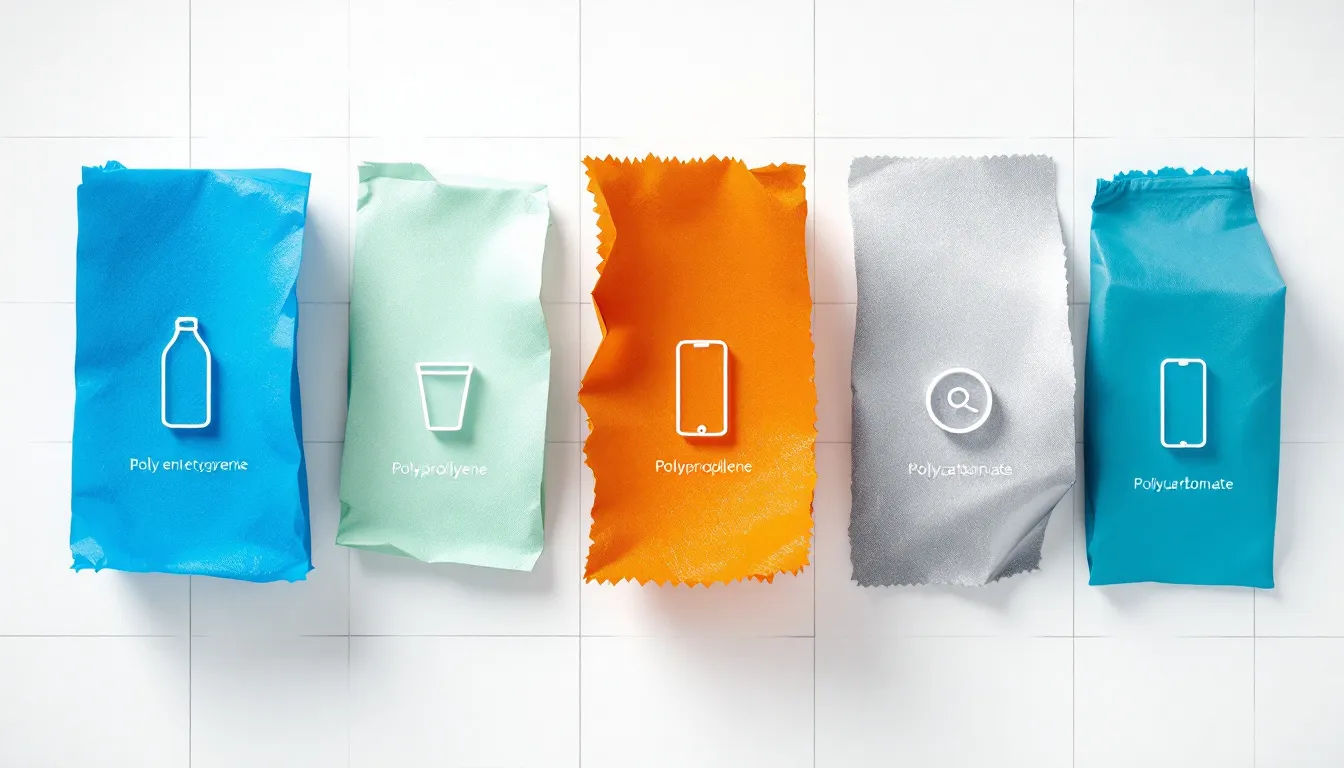
Plastics come in numerous types, each serving different purposes. Polyethylene, known for its flexibility and low density, is widely used in packaging. On the other hand, polypropylene has a higher melting point, making it suitable for higher temperature applications. Such differences underline the versatility of plastics in addressing diverse requirements.
Nylon, being a high-performance plastic, also comes in various grades. Nylon 6 is appreciated for its toughness, making it ideal for textiles. Nylon 6,6 offers excellent wear resistance, while Nylon 12 stands out for its low moisture absorption, enhancing dimensional stability. Each type of nylon caters to specific applications, showcasing the material’s adaptability.
The ability to mixing nylon with other materials further expands its utility. For instance, adding glass fibers can significantly enhance the tensile strength of nylon parts. The ability to customize nylon makes it a preferred choice in engineering plastics and specialized fields requiring tailored performance.
Mechanical Properties Comparison
Nylon excels in mechanical properties, notably for its high abrasion resistance and capacity to endure significant mechanical stress. While it is lighter than traditional materials like steel and aluminum, it may not be as strong. However, the addition of glass fibers can increase nylon’s tensile strength, although it reduces flexibility.
Tensile strength often dictates the choice of material for mechanical equipment. Nylon’s high tensile strength, especially when reinforced, makes it a strong contender for demanding applications. Yet, its inherent flexibility and lighter weight can be advantageous in certain contexts.
Material selection becomes a balancing act between strength and flexibility. Its capacity to endure mechanical stress while remaining durable makes nylon a compelling option for various applications, from textiles to industrial components.
Thermal Properties
Nylon exhibits impressive thermal properties. Nylon 6, for example, melts at around 215°C to 220°C, whereas Nylon 6,6 melts at approximately 255°C to 265°C. This high melting point necessitates higher mold temperatures during the manufacturing process. The glass transition temperature for Nylon 6 ranges between 50°C to 60°C, and for Nylon 6,6 between 60°C to 70°C.
Although nylon has a high melting point, it can begin to decompose around 300°C, potentially compromising its mechanical properties and structural integrity. While nylon has notable fire resistance, it can ignite under extreme conditions. Nylon’s low thermal conductivity and moderate thermal expansion make it an effective insulating material.
Nylon Type | Melting Point |
Nylon 6 | 220°C |
Nylon 66 | 260°C |
Nylon 12 | 178°C |
Nylon 11 | 188°C |
Nylon 6/12 | Between Nylon 6 and Nylon 12,usually around 200-220°C |
Nylon 6-10 | 245°C |
Nylon 46 | 295°C |
Nylon 610 | 220°C |
Nylon 12,12 | Between Nylon 12 and other nylons,often cited around 190-200°C |
Chemical Resistance
Nylon’s chemical resistance adds to its versatility. The molecular structure of nylon, composed of long-chain molecules with amino or functional groups, enables it to withstand various environmental conditions. Nylons generally resist most organic solvents and certain salts but can be harmed by strong acids, alcohols, and alkalis.
However, nylon is not invincible. It is susceptible to hydrolysis when exposed to strong acids, which can degrade its properties. Understanding these limitations is crucial when selecting nylon for applications involving chemicals.
Applications in Different Industries
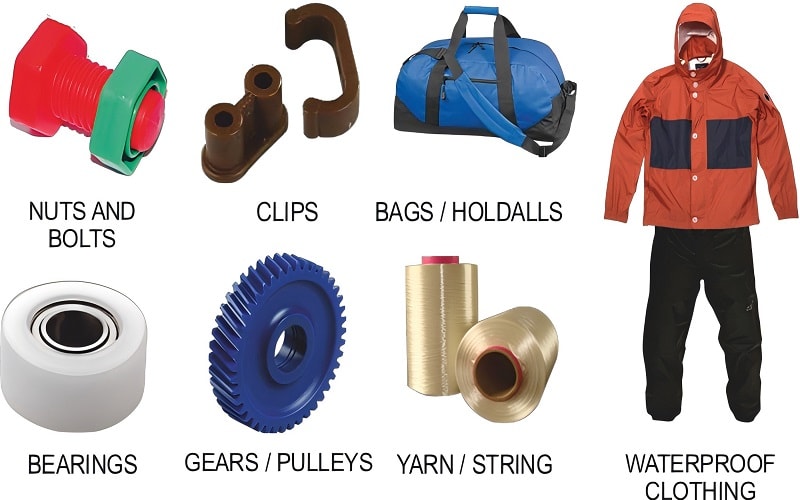
Nylon’s applications span a wide range of industries. In the automotive sector, it’s used for components like engine covers and fuel tanks due to its strength and durability. Consumer goods also benefit from nylon’s versatility, finding its way into products like cookware and clothing. Moisture resistance makes it ideal for food packaging applications.
In the industrial sector, nylon is used for manufacturing gears, bearings, and machine components due to its durability and mechanical properties. Recycled nylon, known as Nycycle, plays a crucial role in reducing landfill waste and ocean pollution by reusing discarded nylon materials.
The extensive range of applications underscores nylon’s adaptability and benefits across various fields, from enhancing product performance to contributing to environmental sustainability.
Environmental Impact
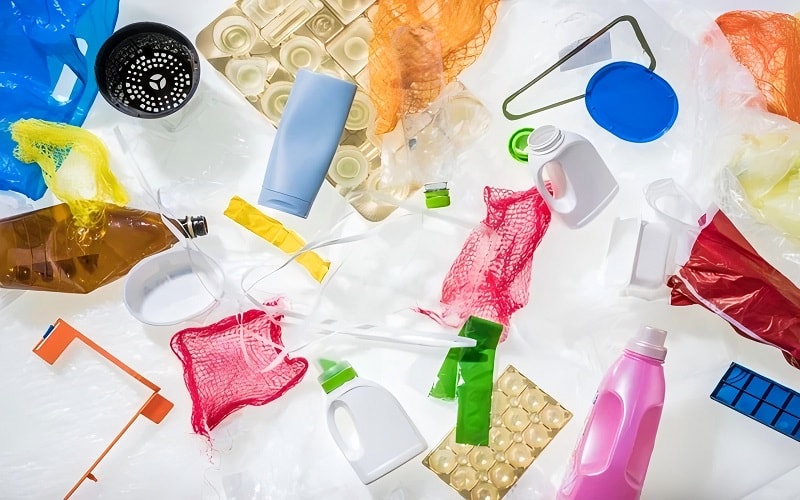
Despite its many advantages, nylon poses environmental challenges. Nylon takes 30–40 years to decompose, contributing to long-term environmental waste. Incineration of nylon emits hazardous smoke and toxic fumes, harming air quality and public health.
The production processes for nylon also leave a significant environmental footprint. For example, in carpet manufacturing, nylon has a greenhouse gas footprint of 5.43 kg CO2 equivalent per kg, highlighting its substantial impact on the environment.
Cost Considerations
Producing nylon generally costs more than other plastics like polypropylene due to its enhanced strength and temperature resistance. The manufacturing process requires more energy, adding to the overall cost.
The demand for nylon in high-performance applications often justifies its higher price. Market fluctuations in raw materials directly affect production costs. However, producing recycled nylon consumes less energy and resources, making it a more cost-effective and environmentally friendly option.
Processing Techniques
Nylon is often molded using injection techniques, which are ideal for producing a high volume of parts. Proper mold design is essential in nylon injection molding, affecting material flow and part ejection. Extrusion is another method used, allowing nylon to be shaped into different profiles like rods and sheets.
CNC machining offers precision in creating shapes from solid nylon pieces through a subtractive manufacturing process. Each technique has its advantages, ensuring the production of high-quality nylon parts for different applications.
Durability and Longevity
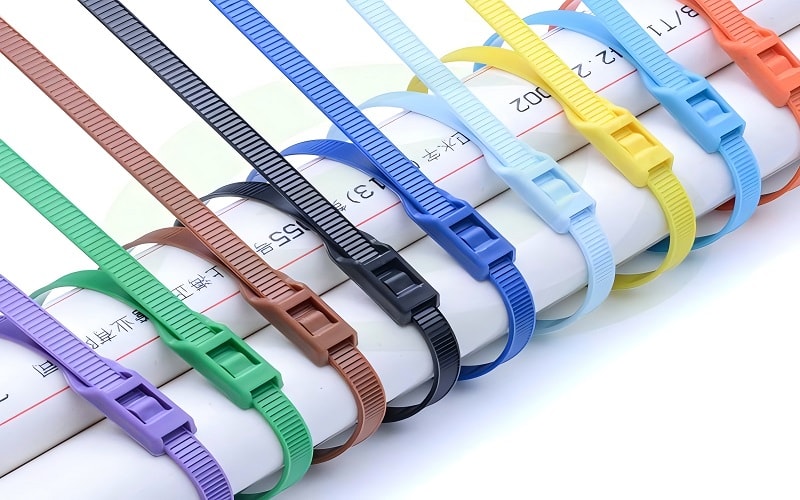
Nylon’s durability is one of its standout features. Nylon’s high fatigue resistance makes it suitable for applications subject to repeated stress. Adding glass fibers further enhances its tensile strength, improving performance in demanding applications.
Nylon’s resistance to wear makes it ideal for components like bearings and gears. Incorporating EuroPlas Anti-UV Additive can significantly extend nylon’s durability and lifespan, ensuring long-term performance.
Customization and Blending
Customization is a significant advantage of nylon. Nylon can be formulated with various additives to enhance mechanical performance and meet specific application needs. Blending nylon with carbon or glass fibers improves its strength and durability.
Manufacturers can create tailored nylon products for specific processes, including extrusion and injection molding. Reinforced nylon variants, such as those filled with carbon fiber, offer increased stiffness and strength for heavy-duty tasks. This flexibility enables nylon to meet diverse and demanding application requirements.
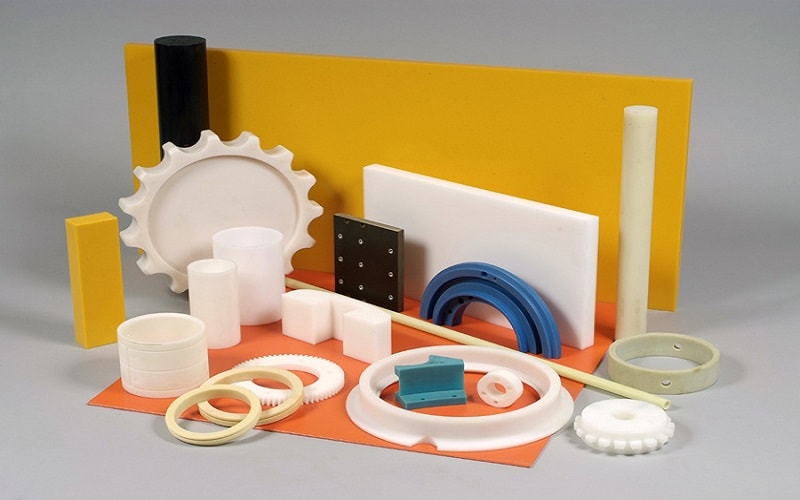
Summary
Choosing between plastic and nylon depends on various factors, including mechanical properties, thermal resistance, chemical resistance, and environmental impact. Nylon stands out for its high tensile strength, durability, and versatility, making it suitable for numerous applications.
Whether you’re in manufacturing, industrial applications, or consumer goods, understanding the differences and advantages of these materials can help you make an informed decision. Embrace the benefits of nylon and plastic, and select the material that best meets your needs and sustainability goals.
Frequently Asked Questions
What are the main differences between nylon and plastic?
The main difference between nylon and plastic lies in their properties; nylon is a high-performance plastic known for its strength and durability, whereas other plastics like polyethylene and polypropylene emphasize flexibility and heat resistance.
How does nylon’s chemical resistance compare to other materials?
Nylon offers good chemical resistance to most organic solvents and certain salts, but it is susceptible to degradation from strong acids, alcohols, and alkalis. Therefore, when selecting materials, consider these limitations for your specific application needs.
What are the environmental impacts of using nylon?
Using nylon has notable environmental impacts, as it takes 30–40 years to decompose and emits hazardous fumes when incinerated, in addition to having a substantial greenhouse gas footprint during production.
Why is nylon more expensive to produce compared to other plastics?
Nylon is more expensive to produce than other plastics because it requires more energy and involves higher manufacturing costs due to its superior strength and temperature resistance.
Can nylon be customized for specific applications?
Absolutely, nylon can be customized by blending it with additives such as carbon fibers and glass fibers to tailor its properties for particular applications. This versatility makes it an ideal choice for a wide range of uses.