Polycarbonate moulding involves injecting melted polycarbonate into intricately designed molds to create various high-quality plastic parts.
This process is crucial for producing durable and reliable components used in industries such as automotive, electronics, and medical devices.
In this article, you will learn about the methods, design guidelines, and applications of polycarbonate moulding.
Understanding Polycarbonate Moulding
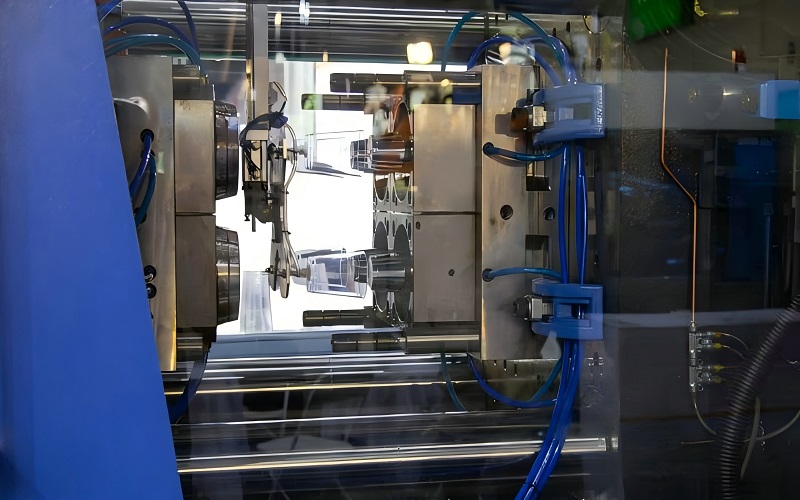
Polycarbonate injection molding is a specialized process that involves injecting melted polycarbonate, a thermoplastic polymer, into a mold at high pressure and temperature. This method is essential for creating various plastic parts and components that are integral to many industries.
From automotive parts to consumer electronics, plastic injection molding and injection molding polycarbonate enables the mass production of high-quality, durable, and complex plastic parts.
One of the standout features of polycarbonate material is its impressive combination of properties. Known for its strength, transparency, impact resistance, temperature stability, and chemical resistance, polycarbonate grades, characterized by their carbonate groups in the polymer chain, are a go-to heat resistant polymer for applications that demand reliability and performance.
Popular brands of polycarbonate resins, such as Lexan® from SABIC and Makrolon® from Bayer MaterialScience, are widely used in the industry due to their consistent quality and performance, including polycarbonate PC for applications like control panel overlays.
The polycarbonate injection molding process not only ensures high-speed production at a low cost per part but also allows for consistent part production, maintaining quality and durability over time. This process also supports additional features in polycarbonate parts, such as UV additives and UL 94 flammability standards, further enhancing their suitability for various applications.
Design Guidelines for Polycarbonate Moulding
Effective design is pivotal in polycarbonate injection molding, ensuring both functionality and manufacturability of the parts.
The molds for polycarbonate components, created by skilled injection molders, must be designed slightly oversized to accommodate shrinkage during the cooling process. Adhering to design for manufacturability (DFM) principles is essential to leverage the full potential of injection molding, making sure that the parts not only meet the required specifications but also can be produced efficiently in the desired shape.
Designers must follow specific guidelines tailored to the intended use of the polycarbonate parts, whether produced through injection molding or alternative processes like vacuum forming. Key design considerations include wall thickness, rib thickness, and draft angles, which are critical for ensuring compatibility with the mold halves used in the molding process.
Each of these elements plays a critical role in the overall quality and structural integrity of the molded parts. By focusing on these aspects, designers can ensure the production of high-quality polycarbonate components that meet the desired performance standards.
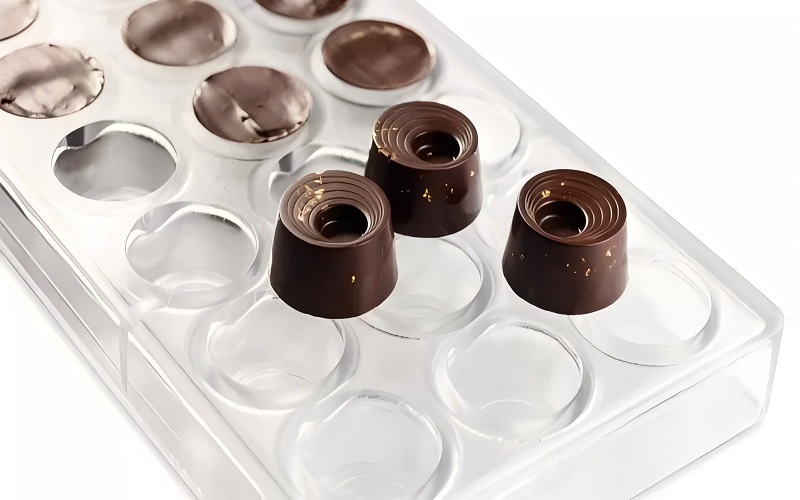
Wall Thickness
Wall thickness is a crucial parameter in polycarbonate injection molding, directly impacting the structural integrity and overall quality of the parts. The advised minimum wall thickness for polycarbonate components is typically around 0.040 inches (1 mm), while the maximum recommended thickness is 0.150 inches (3.8 mm).
Maintaining uniform wall thickness helps in achieving better flow of the molten plastic, reducing the risk of defects such as weld lines and surface imperfections.
Thin wall molding is particularly challenging but offers significant advantages, such as reduced material usage and shorter cycle times. This technique focuses on manufacturing plastic parts with reduced wall thickness and thin walls, which, although more complex, can lead to lightweight and cost-effective components.
Ensuring uniform thickness across the part is essential to avoid issues related to uneven cooling and potential warping.
Rib Thickness
Ribs are structural elements that add strength and support to polycarbonate parts, and their thickness is a key design consideration. Ideally, the rib thickness should be between 0.5 and 0.6 times the thickness of the adjoining wall to ensure optimal structural integrity and resistance to warping. This guideline helps in preventing warping and maintaining the overall strength of the molded part, which is crucial for its performance and durability.
Proper rib design not only enhances the part’s mechanical properties but also contributes to a more efficient and reliable molding process. By adhering to recommended rib thickness guidelines, designers can create polycarbonate parts that are both robust and free from common manufacturing issues.
Draft Angles
Draft angles are essential in the design of polycarbonate parts to facilitate easy removal from the molds. A draft angle of 0.5° to 1° per side is commonly recommended to ensure smooth ejection of the parts without causing damage.
Properly applied draft angles prevent damage to both the part and the mold during ejection, ensuring a smooth manufacturing process and maintaining the quality of the final product.
Incorporating appropriate draft angles is a simple yet effective design strategy that can significantly improve the efficiency and reliability of the injection molding process. By reducing the risk of defects and ensuring easy part removal, designers can enhance the overall quality and consistency of polycarbonate components, especially when considering sharp corners.
The Polycarbonate Moulding Process
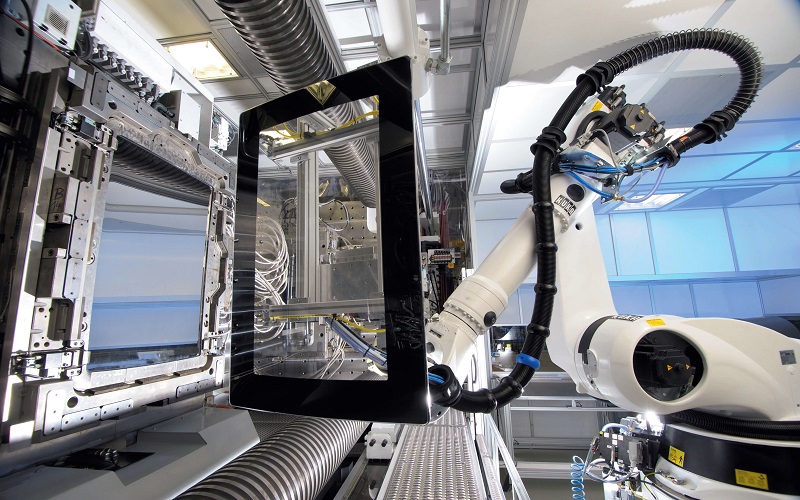
The polycarbonate injection molding process consists of several key phases, each playing a critical role in transforming raw polycarbonate pellets into high-quality plastic parts. The processing parameters typically begin with:
- Material preparation, where thermoplastic granules are dried to remove moisture and mixed with a masterbatch for color.
- The granules are then funneled into an injection molding machine, where they are heated to a molten state.
- The molten material is injected into the mold.
This structured approach ensures the production of durable and precise plastic material components.
Maintaining a constant mold temperature is crucial for ensuring proper material flow and solidification. The process includes four key phases: filling, switchover, pressure, and cooling. Each phase must be carefully controlled to ensure the production of parts that meet the desired specifications. The mold must be cleaned, and tool vents cleared to avoid gassing issues prior to the injection molding process.
Once the injection molding process is complete, the ejection tool removes the finished product from the mold. Additional post-molding work may be required to achieve the final product.
This comprehensive process allows for high-volume production of injection molded plastic parts with significant efficiency and low cost per unit, making it a preferred method for manufacturing complex polycarbonate components.
Key Parameters in Polycarbonate Moulding
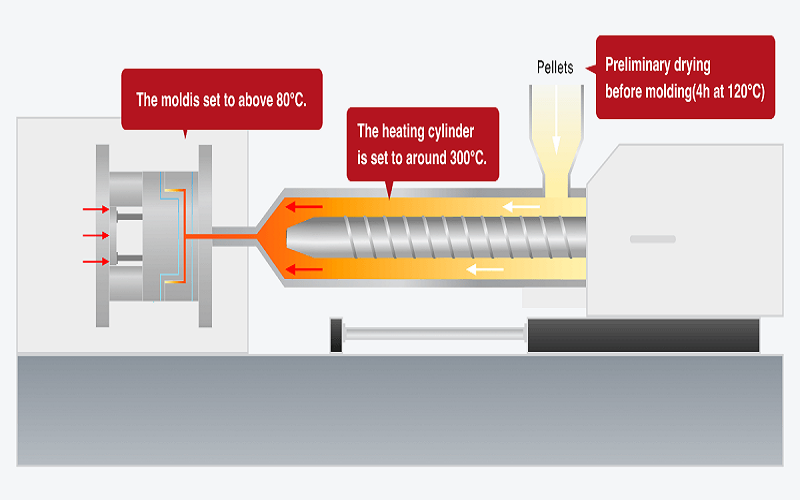
Several key parameters within the polycarbonate injection molding process can influence its efficiency and the quality of the final parts. These parameters include injection temperature, injection pressure, and cooling time, all of which must be precisely controlled to ensure optimal results.
Proper control of these settings not only ensures the uniform melting and flow of materials but also enhances the structural integrity and overall quality of the molded parts.
Maintaining a steady mold tool temperature is vital as it enables easier material flow and helps set the molten resin to solid form. Additionally, back pressure in the injection process helps enhance melt uniformity by controlling temperature and viscosity.
By focusing on these critical parameters, manufacturers can achieve high-quality polycarbonate parts with excellent optical clarity, excellent part-to-part repeatability and tight tolerances.
Injection Temperature
Injection temperature plays a critical role in achieving high-quality polycarbonate parts and injection speed, particularly when considering the molten polycarbonate injection molding temperature and injection molded parts. The process refers to the precise management of thermal conditions to ensure optimal material behavior.
Too high a melt temperature can lead to material degradation and internal stresses, while too low a temperature may result in poor material flow and incomplete parts, affecting heat resistance and properties like flame retardant performance.
Proper temperature control is influenced by several factors, including:
- The type of material
- Residence time
- Mold temperature
- The material’s melting point
Modern injection molding machines assist with temperature regulation through multiple heating zones in the heated barrel, ensuring consistent quality production.
Maintaining a constant barrel temperature is vital for the quality production of polycarbonate parts. Proper control of injection temperature minimizes cooling stresses and enhances the overall properties of the finished parts, including their flame retardant characteristics.
The temperature at which polycarbonate is injected can significantly impact the flow rate and part quality, making it a critical parameter in the injection molding process refers to achieving reliable outcomes.
Injection Pressure
Injection pressure is essential for driving molten material into the mold effectively. The primary role of injection pressure in the molding process is to drive material flow into the mold, ensuring that the cavity is completely filled and the part is properly formed. Proper control of injection pressure is crucial for maintaining the structural integrity and dimensional accuracy of the molded parts.
Additionally, variations in injection pressure can influence shrinkage rates, impacting the final dimensions of the molded parts. By optimizing injection pressure settings, manufacturers can ensure the production of high-quality polycarbonate components with minimal defects and consistent performance.
Cooling Time
Cooling time is a crucial phase in the polycarbonate molding process, determining how quickly a part solidifies and stabilizes. Accurate cooling time management ensures that polycarbonate parts achieve the desired structural integrity and surface quality. Proper cooling minimizes defects such as warping and shrinkage, ensuring the final product is both stable and high in quality.
Excessive heat at the gate during molding can lead to significant shrinkage in polycarbonate parts, highlighting the importance of precise temperature and cooling control. By managing cooling time effectively, manufacturers can produce polycarbonate parts that meet stringent quality standards and performance requirements.
Techniques in Polycarbonate Moulding
Polycarbonate injection molding is known for its versatility in producing complex shapes and designs. Various polycarbonate injection molding techniques are used to enhance the capabilities of the injection molding process, allowing manufacturers to create parts with specific properties and functionalities. These techniques include thin wall molding, over molding, and structural foam molding, each offering unique advantages and applications.
The ability to produce high-precision, intricate parts through polycarbonate injection molding opens up a wide range of possibilities for innovation in product design and manufacturing. By leveraging these advanced techniques, manufacturers can meet the diverse needs of different industries and create complex plastic parts that drive progress and innovation, including high-quality injection molded polycarbonate parts.
Thin Wall Moulding
Thin wall molding is designed to create lightweight plastic parts with significantly reduced wall thickness. This technique focuses on manufacturing parts with minimal material usage while maintaining their structural integrity and performance.
Thin wall molding is particularly beneficial in applications where weight reduction is critical, such as in automotive and consumer electronics industries.
However, thin wall molding presents unique challenges, including the need for precise control over the molding process and the use of advanced injection molding machines. By overcoming these challenges, manufacturers can produce high-quality, lightweight polycarbonate parts that meet the demands of modern applications.
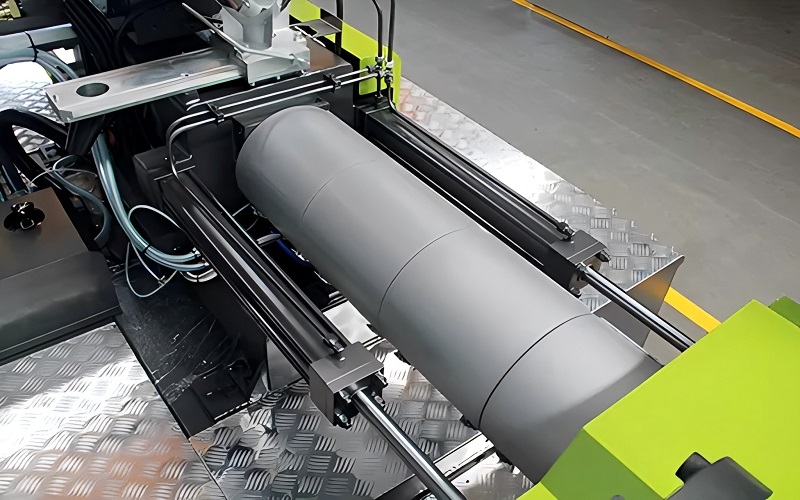
Over Moulding
Over molding allows for the integration of different materials into a single component for enhanced functionality. This process involves constructing multi-component pieces with one component cooling first as a core, followed by the injection of additional materials. Over molding enables the creation of complex plastic parts with diverse physical properties and improved aesthetic appeal.
One benefit of over molding is the flexibility it offers in material selection and design. By mixing different materials, manufacturers can produce parts that are both functional and visually appealing, catering to the specific needs of various industries.
Structural Foam Moulding
Structural foam molding is a manufacturing technique used to create large, lightweight plastic parts. This method utilizes a blowing agent to create a foamed interior with a solid exterior, resulting in parts that are both strong and lightweight. Blow molding is particularly beneficial for producing parts that need to be durable yet easy to handle.
The benefits of structural foam molding include the ability to produce large parts with reduced material usage and weight, making it ideal for applications in industries such as automotive, aerospace, and consumer goods. By leveraging this technique, manufacturers can achieve significant cost savings while maintaining high-quality standards.
Advantages and Disadvantages of Polycarbonate Moulding
Polycarbonate injection molding offers multiple advantages across various applications. The material’s high impact strength, UV resistance, optical clarity, and ability to withstand high temperatures make it an excellent choice for creating durable and reliable parts. Injection molding also allows for high-volume production with reduced labor costs due to automation, further enhancing its appeal.
However, there are also disadvantages to consider:
- Polycarbonate is generally more expensive compared to other plastic options, impacting the affordability of production.
- The high-cost status of polycarbonate as a raw material and the initial investment required for injection molding machinery and tooling can be significant barriers for some manufacturers.
- Injection molding is not suitable for low-volume production due to the high upfront investment for molds.
Despite these challenges, the pros of polycarbonate injection molding generally outweigh its cons in many applications. When cheaper thermoplastics are insufficient to meet design requirements, polycarbonate’s unique properties make it the preferred choice. By carefully considering the advantages and disadvantages, manufacturers can make informed decisions about when to use polycarbonate injection molding for their specific needs.
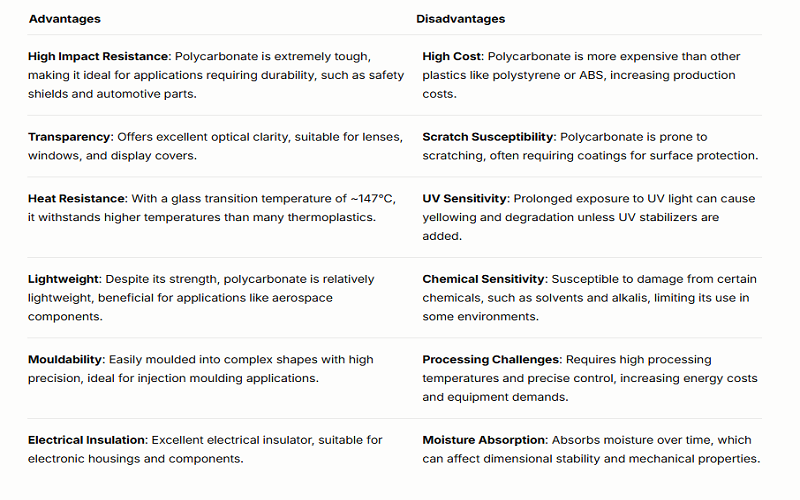
Common Issues and Troubleshooting in Polycarbonate Moulding
Polycarbonate injection molding can present multiple challenges, but most are straightforward to resolve. Common issues include:
- Flash: occurs when molten resin escapes from the mold, which can often be resolved by increasing clamp pressure and adjusting mold temperature and injection parameters.
- Weld lines: arise from multiple flow fronts and poor bonding, forming visible seams that can weaken the part’s structure.
- Vacuum voids
- Warping
- Sink marks
By addressing these common issues, you can improve the quality of your molded parts.
Addressing these issues requires a thorough understanding of the injection molding process and careful control of key parameters. For example, vacuum voids are often caused by inadequate holding pressure or improper mold alignment, while warping can be managed through optimizing cooling time and holding pressure.
By implementing effective troubleshooting methods, manufacturers can maintain the quality and consistency of their polycarbonate parts.
Sink Marks
Sink marks are small depressions found in thicker areas of the molded polycarbonate product. These marks are typically caused by incorrect cooling time, excess heat at the gate, and pressure issues. Significant shrinkage during cooling can also lead to the formation of sink marks in polycarbonate parts.
To address sink marks, it is advised to reduce mold temperature and increase holding pressure during the molding process. By carefully controlling these parameters, manufacturers can minimize the occurrence of sink marks and ensure the production of high-quality polycarbonate parts.
Warping
Warping in polycarbonate parts is primarily caused by non-uniform cooling throughout the molding process. Ensuring uniform cooling rates and appropriate wall thickness can help prevent warping and maintain the part’s structural integrity. Cooling channels in the mold design and post-molding annealing are effective strategies to achieve uniform cooling and reduce warping.
Flow-induced residual stress can also contribute to warping. To mitigate this, reducing shear stress during cavity filling is essential. By implementing these strategies, manufacturers can produce polycarbonate parts that are stable and free from warping.
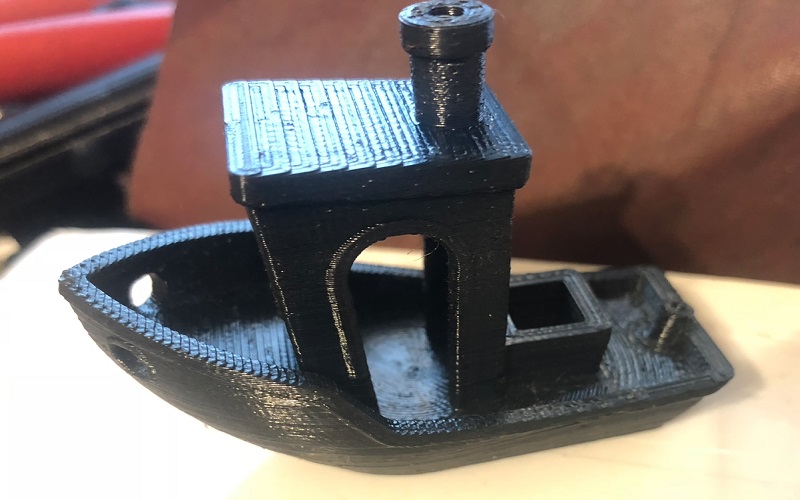
Surface Defects
Surface defects such as:
- Jetting, which occurs when molten resin does not adhere to the mold surface, creating wavy folds
- Flow lines, which are patterns or lines that appear off-tone, caused by slow injection speeds or fluctuations in flow rates
- Burn marks, which can affect the appearance and performance of polycarbonate parts
These defects can significantly impact the quality control of the final product.
Burn marks appear as rusty discolorations on the surface of molded parts, typically due to excessive heating or fast injection speeds. To prevent these defects, manufacturers should optimize processing conditions, maintain clean molds, and use mold release agents effectively. By addressing these issues, manufacturers can ensure the production of high-quality polycarbonate parts with excellent surface finishes.
Applications of Polycarbonate Moulding
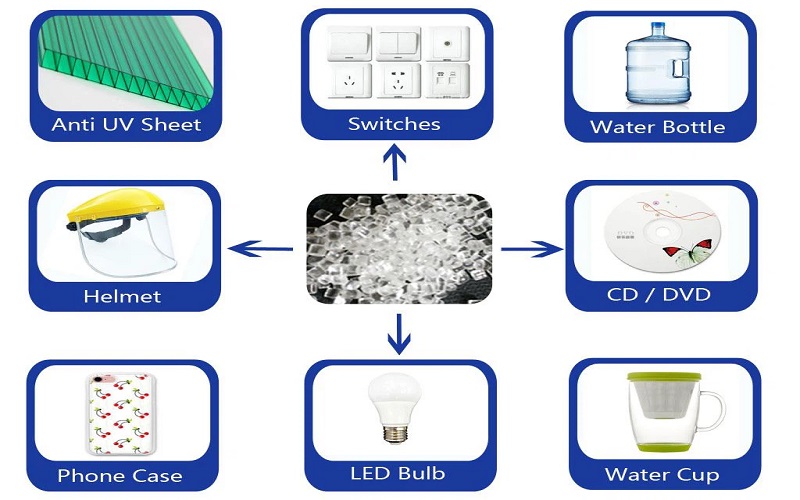
Polycarbonate’s unique properties make it suitable for various applications, including automotive components, medical devices, and consumer products.
In the automotive sector, polycarbonate is often used in the production of parts that require high strength and transparency, such as tail lights and dashboards. Motorcycle helmet visors are another notable example, highlighting the material’s impact resistance and optical clarity.
In the medical field, polycarbonate is used to create durable and reliable components, such as medical face shields, which emphasize the importance of quality and durability. The aerospace sector also benefits from polycarbonate’s properties, using it to produce lightweight and impact-resistant windows and interiors.
Consumer products widely utilize polycarbonate for durable components like transparent housings and safety equipment. The material’s optical properties make it ideal for producing high-quality eyeglass lenses for devices such as cameras and eyewear. Polycarbonate’s strength and durability are crucial in safety equipment and electronic components, making it a preferred choice for many applications.
Summary
Polycarbonate injection molding is a versatile and efficient manufacturing process that enables the production of high-quality, durable, and complex plastic parts. By understanding the intricacies of the process, including design guidelines, key parameters, and advanced techniques, manufacturers can leverage polycarbonate’s unique properties to meet the diverse needs of various industries.
The advantages of polycarbonate injection molding, such as high impact strength, UV resistance, and optical clarity, often outweigh its disadvantages, making it a valuable choice for many applications.
With careful consideration of the potential challenges and effective troubleshooting methods, manufacturers can achieve consistent quality and performance in their polycarbonate parts. Embrace the potential of polycarbonate injection molding to drive innovation and excellence in your manufacturing endeavors. sheet metal fabrication
Frequently Asked Questions
How to mold polycarbonate plastic?
To mold polycarbonate plastic, heat it to a temperature below its melting point until it becomes soft and glassy, then stretch it to fit the contours of your mold. This thermoforming process ensures precise shaping of the material.
What are the defects of polycarbonate molding?
Polycarbonate molding can result in surface defects such as blemishes, streaks, or haze. To achieve a flawless finish, ensure clean mold surfaces, optimize processing conditions, and utilize mold release agents and proper venting.
What is the problem with polycarbonate plastic?
The main issue with polycarbonate plastic is its chemical sensitivity; it can be affected by certain solvents and cleaning agents, which necessitates careful selection of compatible materials. Additionally, polycarbonate tends to be more expensive than other types of plastics.
Can polycarbonate be molded?
Yes, polycarbonate can be molded using various methods such as injection molding, extrusion, blow molding, and thermoforming. Its desirable properties make it suitable for applications requiring optical clarity and toughness.
What is polycarbonate injection molding?
Polycarbonate injection molding involves the high-pressure injection of melted polycarbonate into a mold to produce durable plastic parts. This method is widely used for creating strong, lightweight components in various industries.