Polystyrene injection molding is a precise, cost-effective method for creating lightweight, durable plastic components.
This article explains the process, discusses its key benefits, and offers best practices to help you achieve optimal results in your manufacturing projects.
Understanding Polystyrene (PS)
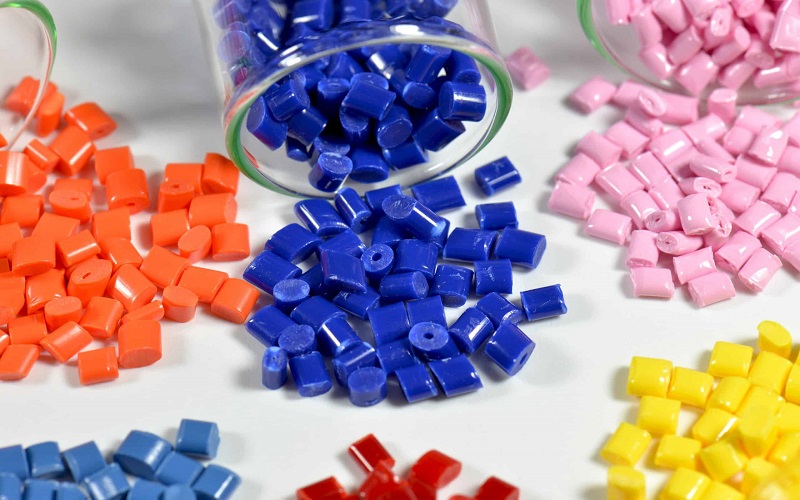
Polystyrene is a synthetic thermoplastic polymer made from styrene, classified as a commodity thermoplastic. Its unique properties, such as being lightweight, hydrophobic, and chemically stable, make it a popular choice in various industries.
Polystyrene is extensively used in disposable tableware, containers, and packaging materials, showcasing its versatility in being molded into polystyrene foam, film, and rigid plastic forms. Its moldability and low shrinkage make it a preferred choice for numerous applications in manufacturing, leveraging the diverse polystyrene components that form its structure.
Understanding the types of polystyrene and their chemical structure helps in appreciating its wide range of applications. From general-purpose polystyrene (GPPS) to high-impact polystyrene (HIPS), expanded polystyrene (EPS), and extruded polystyrene (XPS), each type offers distinct advantages suited to specific needs. Explore the following sections to learn more about these types and their chemical properties.
Types of Polystyrene
Polystyrene comes in several forms, each with its specific applications. General Purpose Polystyrene (GPPS) is recognized for its clarity and is frequently used in disposable items, despite its relative brittleness.
On the other hand, High Impact Polystyrene (HIPS) overcomes this brittleness by blending polystyrene with rubber, significantly increasing its impact resistance. This makes HIPS ideal for consumer products that require higher durability.
Expanded Polystyrene (EPS) is another important type, commonly used for insulation, packaging, and cushioning due to its lightweight and resilient properties. Each type of polystyrene, whether GPPS, HIPS, or EPS, offers unique benefits that cater to different industrial needs, from clear, rigid plastics to lightweight, cushioning materials.
Chemical Structure and Properties
The chemical formula of polystyrene is represented as (C8H8)n, indicating its polymeric nature. It comprises recurrent styrene molecules, contributing to its chemical resistance and lack of reactivity with other materials. This stability, coupled with its low viscosity, facilitates its flow during the injection molding process, making it a highly moldable material.
Polystyrene’s physical properties include naturally transparent rigidity and brittleness in its unmodified form. It has a glass transition temperature of 100°C, which affects its thermal responsiveness in various applications.
Modified forms, such as styrene-co-methyl methacrylate, can enhance clarity or toughness, while polystyrene generally exhibits a lower melting point (around 240°C) compared to high-temperature polymers, though certain copolymers may approach a high melting temperature for improved thermal stability.
The material’s mechanical robustness is reflected in its tensile strength, typically ranging from 35 to 55 MPa. Additionally, polystyrene is an excellent electrical insulator, making it ideal for electrical components. These properties make polystyrene a versatile material suitable for a wide range of applications.
Advantages of Polystyrene Injection Molding
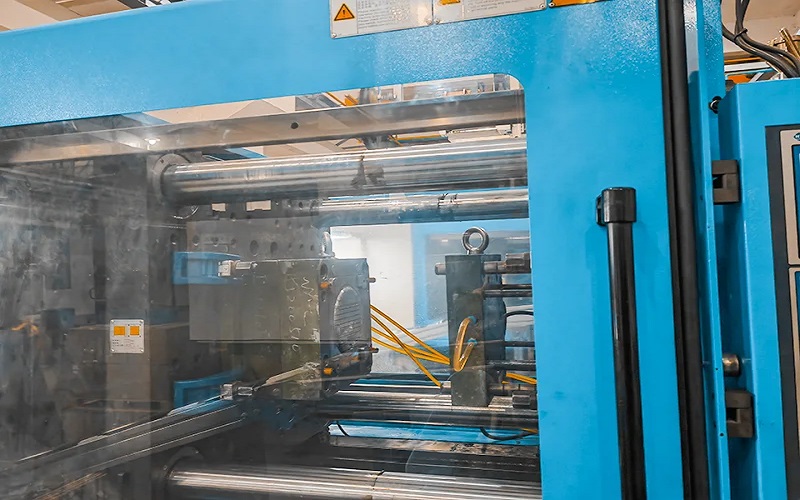
Polystyrene, where polystyrene begins as a versatile synthetic polymer, is a favored material in plastic injection molding due to its low cost and favorable mechanical properties.
The injection molding process using polystyrene produces high-precision and repeatable parts with minimal waste, making it an economically efficient method for mass production. This efficiency is further enhanced when polystyrene is blended with other polymers, allowing for a broader range of applications in injection molded plastics, including household appliances.
The lightweight plastic and low-cost nature of polystyrene make it an ideal choice for various industries, contributing to its widespread use in manufacturing.
The performance of polystyrene can be significantly improved when blended with other polymers, allowing for a range of applications, though care must be taken to manage potential styrene exposure during processing to ensure safety.
The specific advantages of using polystyrene in injection molding include the following:
Lightweight and Durable
Polystyrene’s lightweight nature makes it a preferred choice in many manufacturing applications. This characteristic not only allows for easier handling and transportation of products but also enhances its durability due to its hydrophobic properties, which resist moisture.
These characteristics make polystyrene ideal for a range of products across multiple industries.
Excellent Dimensional Stability
Polystyrene exhibits excellent dimensional stability and good dimensional stability due to its amorphous nature, which reduces shrinkage during the injection molding process.
Its low shrink rate, typically less than 0.5%, ensures that the dimensions of the molded parts are maintained accurately. The material does not absorb water, preventing swelling and helping in retaining its size.
These properties make polystyrene a reliable choice for applications requiring high precision and consistent quality.
Low Cost and High Efficiency
Polystyrene injection molded parts are economically efficient, with costs typically ranging from $0.20 to $3 per unit, depending on the component’s dimensions, complexity, and batch size. This low cost makes polystyrene an ideal choice for mass production, offering consistent quality and high precision in the final products.
Complex or larger polystyrene items can cost up to $8 each, reflecting its broad applicability across various industries.
Key Considerations in Polystyrene Injection Molding
Successful polystyrene injection molding requires careful consideration of various factors, including processing parameters, mold design, and material selection.
Although polystyrene is an economically efficient method for mass-producing identical parts with consistent quality, it has its challenges, such as a low melt flow index, a higher melt flow index, and high melting point. It is crucial to select a reliable PS injection molding company. This choice will help determine the best approach for specific applications.
Understanding the specific requirements of polystyrene injection molding, such as part complexity, production volume, and quality standards, is essential for optimizing the process and achieving high-quality results. Key considerations to ensure successful polystyrene injection molding include the following:
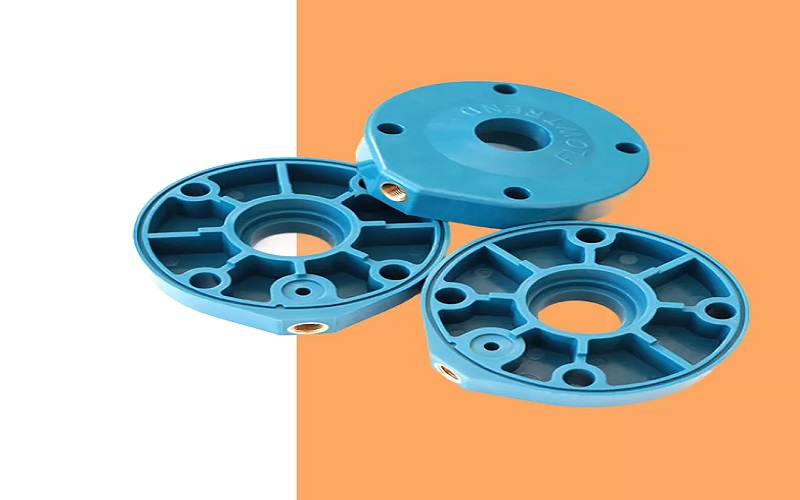
Processing Parameters
The key processing parameters for polystyrene injection molding include temperature, pressure, and cooling rates. Maintaining optimal injection speed is crucial to avoid defects such as flow lines and ensure uniform part density. Different grades of polystyrene may require specific temperature adjustments during molding to achieve the desired results.
Careful control of processing conditions is necessary to ensure the quality of polystyrene during injection molding. Increased temperature improves moldability but can negatively affect the glossiness and strength of the final product. Maintaining pressure after injection helps reduce overall shrinkage rates of polystyrene parts.
Adjusting packing pressure along with cooling rates can help maintain product consistency and reduce defects. Effective quality control involves monitoring manufacturing processes and processing parameters to ensure dimensional accuracy and consistent quality.
Mold Design
Accurate mold design and manufacturing are critical to the success of polystyrene injection molding. Shrinkage during cooling of polystyrene can range from 0.2% to 0.8%, which must be carefully considered in mold design. Incorporating draft angles of 0.5 to 1% in mold design facilitates easier part ejection, reducing the risk of damage during removal.
Improper design can lead to cracking during ejection, especially in areas lacking sufficient draft. Maintaining uniform wall thickness is essential to minimizing defects and ensuring the integrity of polystyrene molded parts. A recommended wall thickness variation of no more than 25% is critical to avoid defects in molded polystyrene parts.
Ribs in molded polystyrene parts should be 60% to 50% of the wall’s thickness to prevent sink marks.
Material Selection
Before:
Selecting the right type of polystyrene is crucial for the success of injection molding processes in various applications. Factors to consider when selecting the type of polystyrene include mechanical strength, flexibility, transparency, and environmental conditions.
After incorporating the keyword:
After considering the feedback, we decided to enhance the project by integrating various components to improve overall functionality.
When selecting the type of polystyrene for injection molding processes, consider the following factors:
- Mechanical strength
- Flexibility
- Transparency
- Environmental conditions
This careful selection is crucial for the success of your applications.
While polystyrene generally does not require drying before injection molding, pre-drying is recommended when using recycled material or in high humidity conditions. Choosing materials with low shrinkage rates can significantly mitigate the effects of warping and shrinkage during the injection molding process.
Applications of Polystyrene Injection Molding
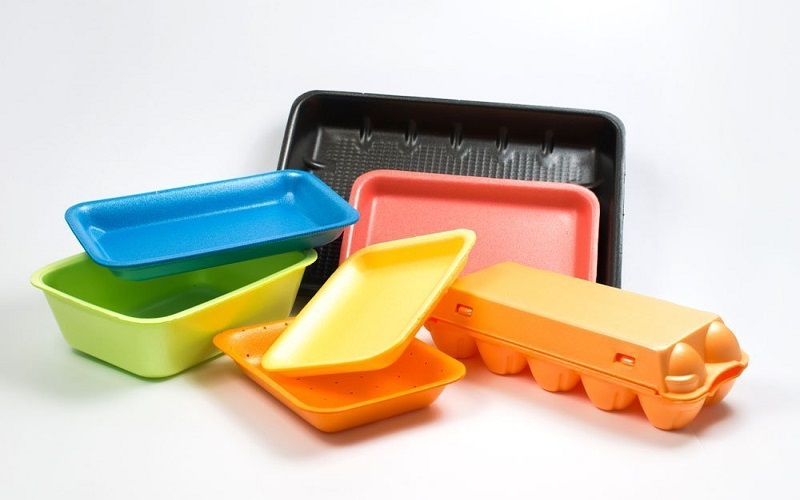
Polystyrene is utilized in various industries, including food packaging, automotive parts, electronics, and consumer goods. Its non-toxic and odorless nature makes it widely used in the food packaging sector.
Common consumer products made from polystyrene include disposable cutlery, plastic cups, and protective casings for electronics. Polystyrene is utilized in the automotive industry. It is commonly used for components such as instrument panels and children’s protective seats.
The versatility of polystyrene allows it to be used in a myriad of applications, from food packaging to medical products and consumer goods. This section will explore these applications in detail, highlighting the benefits and specific uses of polystyrene in different industries.
Food Packaging
Polystyrene is widely utilized in food packaging due to its lightweight and non-toxic nature, making it beneficial for automation processes. Expanded Polystyrene (EPS) is specifically valued for its insulation properties and is commonly used for packaging applications.
Common food packaging items made from polystyrene include yogurt containers, disposable cutlery, and foam trays. Polystyrene is often utilized to make disposable food containers, enhancing convenience for consumers.
In the packaging industry, polystyrene is used in products such as cups, plates, and trays. However, biodegradable plastics are emerging as sustainable alternatives to traditional polystyrene, offering reduced environmental impact.
Innovative materials, such as plant-based plastics, recycled paper, and mushroom-based materials, are being researched to replace polystyrene in applications like food packaging.
Medical Products
Polystyrene is widely used in the medical field for various applications such as test tubes and petri dishes. Its radiation resistance ensures that medical products can be efficiently sterilized without compromising their integrity.
Common medical products made from polystyrene include test tubes, petri dishes, and other laboratory equipment.
Consumer Goods
Polystyrene is a good choice for plastic cutlery because it is highly moisture resistant. In the consumer electronics sector, polystyrene is commonly used for housings and casings. Other consumer applications of polystyrene include automotive components like dashboards and knobs, as well as optical components such as lenses.
Polystyrene plastics is widely used in various consumer goods due to its advantageous properties, including pure polystyrene.
Enhancing Polystyrene Properties
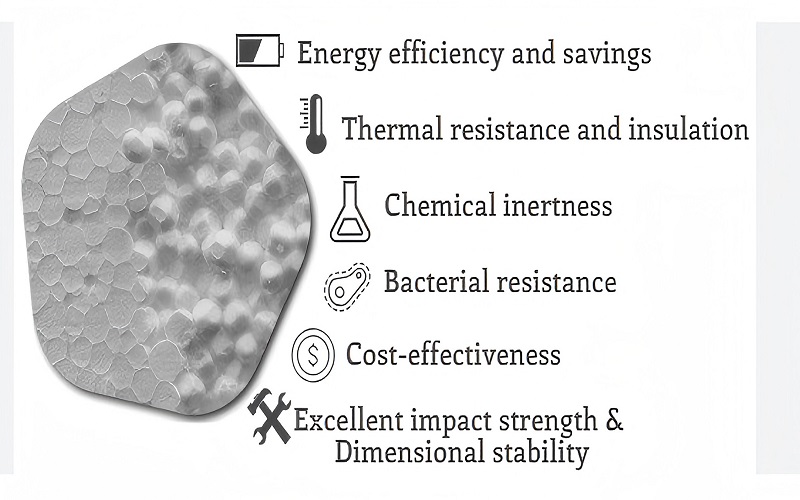
Polystyrene’s properties can be enhanced through various methods, improving its performance and expanding its range of applications.
Co-polymerization, blending with other plastics, and the use of additives are key techniques to enhance the material’s properties. These modifications can address the disadvantages of polystyrene, such as brittleness and low impact resistance, making it more versatile for different industrial needs.
Enhancing polystyrene properties allows manufacturers to produce more durable, versatile, and aesthetically pleasing products. Methods to enhance polystyrene properties and their benefits include the following:
Co-Polymerization
Co-polymerization involves combining polystyrene with other materials to enhance its mechanical and physical properties. For instance, polystyrene co polymerization with acrylonitrile and butadiene boosts both impact strength and thermal stability.
Co-polymerization enhances the versatility and durability of polystyrene, broadening its range of applications.
Blending with Other Plastics
Blending polystyrene with other plastics and plastic material is another method used to enhance its properties. This process can improve the impact resistance and flexibility of polystyrene, making it suitable for more demanding applications.
Improved impact resistance and flexibility expand the applications of polystyrene across various industries.
Additives and Modifications
Additives such as colorants and UV stabilizers play a crucial role in enhancing the properties of polystyrene. Colorants can be incorporated into polystyrene to enhance its aesthetic qualities, providing a wide range of colors for different products. UV stabilizers enhance the resistance of polystyrene to degradation caused by ultraviolet light, extending the lifespan and usability of products made from polystyrene.
These modifications not only improve the appearance and durability of unmodified polystyrene products but also open up new opportunities for design and function in various applications.
Sustainability and Environmental Impact
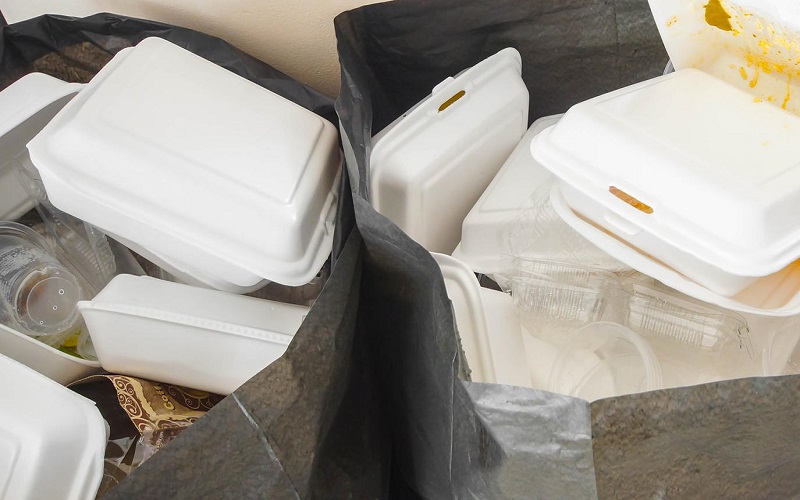
Polystyrene can persist in the environment for hundreds of years, posing long-term pollution risks. Sustainable design considerations include the entire lifecycle of products, recycling options, minimizing waste, disposal impact, and exploring alternatives to reduce the ecological footprint. Addressing these environmental concerns is crucial for the responsible use of polystyrene in manufacturing.
Sustainability and environmental impact considerations for polystyrene include recycling and waste management, lifecycle assessment, and sustainable alternatives.
Recycling and Waste Management
Recycling polystyrene typically involves collecting the material, compacting it to reduce volume, and then shipping it to recycling facilities for pelletizing.
Implementing best practices in polystyrene use can further reduce waste and enhance overall sustainability. Managing waste and reducing environmental impact make recycling polystyrene crucial.
Proper waste management practices can significantly mitigate the environmental impact of polystyrene. By promoting recycling and responsible disposal, we can ensure a more sustainable future for this versatile material.
Lifecycle Assessment
Proper assessment of polystyrene items includes evaluating production, use, and post-consumer stages to better understand their overall ecological footprint. Specialized facilities exist that can recycle polystyrene into new products, reducing landfill waste.
However, polystyrene is often not accepted in curbside recycling programs due to contamination challenges. Environmental conditions, such as exposure to UV light and chemicals, should be considered when choosing the right polystyrene material.
Sustainable Alternatives
New biodegradable options such as wood foam derived from cellulose fibers offer a more sustainable packaging solution compared to traditional polystyrene.
Various eco-friendly packaging options, such as recycled foam and wood-based foams, provide sustainable alternatives to polystyrene, often resulting in less environmental impact. Using paper void fill instead of polystyrene for packaging can offer moderate protection while being easily recyclable, addressing environmental concerns.
Innovative materials like Korrvu packaging reduce plastic usage while maintaining protective packaging during transit by suspending items between layers of plastic, making it easier to recycle. Corrispring, made from biodegradable corrugated cardboard, serves as a cushioning alternative to polystyrene, offering easier recycling and less environmental harm.
Wood foam, such as Fibrease, is derived from cellulose fibers and provides a comparable protective performance to synthetic foams while being recyclable through paper collections, including foam form options.
Common Challenges and Solutions in Polystyrene Injection Molding
Various challenges can arise during the polystyrene injection molding process, which can affect product quality and efficiency. Warping and shrinkage are common issues that impact part quality and dimensional accuracy.
Dimensional inaccuracies can create parts that do not meet specifications or fit properly in assembly. To mitigate these issues, it is essential to optimize processing parameters and mold design to ensure consistent results.
Common challenges in polystyrene injection molding include warpage, shrinkage, surface defects, and consistency in quality control, along with their solutions.
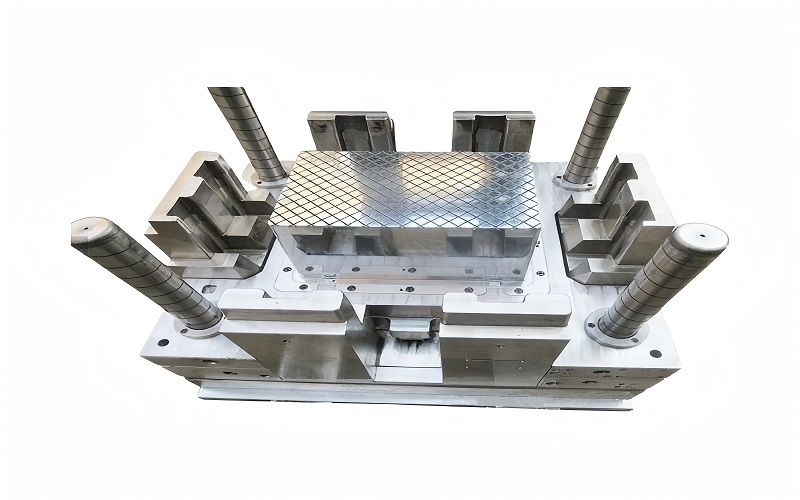
Warpage and Shrinkage
The typical shrinkage percentage for injection molded polystyrene ranges from 0.4% to 0.7%. Approximately 10% of the overall shrinkage happens after the ejection of the part. This applies specifically to polystyrene.
Uneven cooling during the molding process leads to warpage, causing parts to distort as they cool. Warpage occurs due to uneven cooling, which creates internal stresses within the molded part.
Addressing these issues involves optimizing cooling rates and ensuring uniform wall thickness to reduce internal stresses and maintain dimensional accuracy.
Surface Defects
Surface defects like voids, sink marks, and delamination can occur during the injection molding process. Voids in molded polystyrene can arise from inadequate filling during the injection process, highlighting the need for precise fill analysis. Surface imperfections like sink marks can be minimized by ensuring that rib thickness is appropriate relative to the part’s wall thickness.
Surface delamination arises from contaminants not bonding with the plastic, leading to separation into layers. Proper process control and material handling are essential to prevent these defects.
Consistency and Quality Control
Quality control in polystyrene injection molding is essential to ensure that products meet specified standards and function as intended.
Dimensional accuracy in injection molded products directly impacts their fit, function, and aesthetic quality. Tighter tolerance requirements increase the cost of mold and parts, necessitating careful consideration during the design phase.
Maintaining consistent quality through effective control measures leads to reduced waste and production costs, enhancing overall efficiency.
Summary
Polystyrene’s versatility, cost-effectiveness, and unique properties make it a staple in modern manufacturing. From food packaging to medical products and consumer goods, polystyrene proves its worth across various industries.
By understanding the types, properties, and best practices in polystyrene injection molding, manufacturers can optimize their processes and produce high-quality products.
Addressing sustainability and environmental concerns ensures that we use this valuable material responsibly. Embrace the potential of polystyrene and explore innovative solutions to enhance its properties and applications.
Frequently Asked Questions
What are the main types of polystyrene used in injection molding?
The main types of polystyrene employed in injection molding are General Purpose Polystyrene (GPPS), High Impact Polystyrene (HIPS), and Expanded Polystyrene (EPS). Each type serves distinct applications based on its unique properties.
Why is polystyrene a preferred material for injection molding?
Polystyrene is favored for injection molding because it is cost-effective, exhibits favorable mechanical properties, and allows for the production of high-precision parts efficiently. This combination makes it an ideal choice for manufacturers.
What are common applications of polystyrene in the food packaging industry?
Polystyrene is commonly applied in the food packaging industry for yogurt containers, disposable cutlery, foam trays, cups, plates, and trays owing to its lightweight and non-toxic properties. Its versatile nature makes it a preferred choice for various food packaging solutions.
How can the properties of polystyrene be enhanced for better performance?
Enhancing the properties of polystyrene for better performance can be achieved through co-polymerization, blending with other plastics, and the incorporation of additives like colorants and UV stabilizers. These methods effectively improve its durability and functionality.
What are some sustainable alternatives to traditional polystyrene?
Sustainable alternatives to traditional polystyrene include biodegradable options such as wood foam made from cellulose fibers, recycled foam, and wood-based foams.
These materials, including Korrvu packaging and Corrispring, offer environmentally friendly solutions.