PP injection molding is a manufacturing process that uses polypropylene to produce durable and versatile plastic parts.
This article will explain the key aspects, benefits, and common challenges of PP injection molding.
Whether you are new to the process or looking to optimize it, you will find practical insights and tips here.
Key Takeaways
- Polypropylene (PP) is a versatile thermoplastic with various forms, including homopolymer and copolymers, each offering distinct properties for numerous applications.
- The polypropylene injection molding process requires careful control of temperature, pressure, and speed to optimize part quality and mitigate common challenges like warping.
- Despite its advantages, such as cost-effectiveness and durability, polypropylene also has drawbacks, including susceptibility to UV degradation and dimensional changes due to thermal expansion.
Understanding Polypropylene (PP)
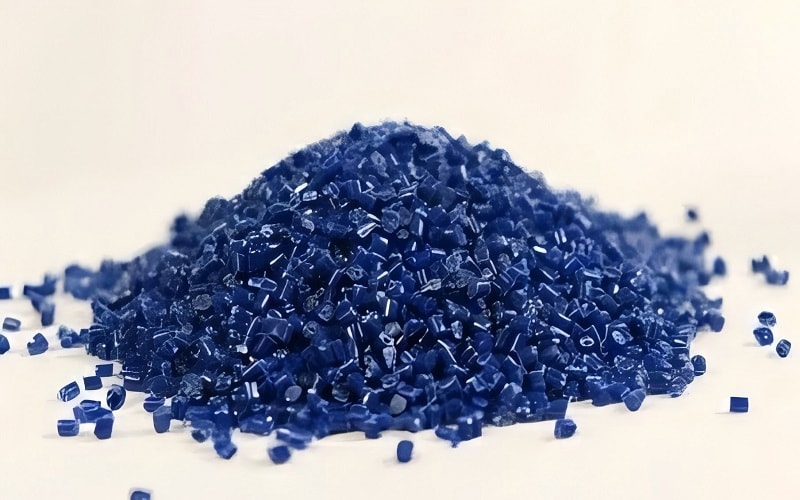
Polypropylene (PP), also known as polypropene, is a versatile thermoplastic polymer and plastic polymer derived from the polymerization of propylene monomers.
Its widespread use in consumer products, medical devices, and automotive components speaks volumes about its adaptability.
The ability to customize and mold polypropylene plastic into various shapes and forms has earned it the nickname ‘the steel of the plastic industry’. Major suppliers like LyondellBasell, Braskem, and Exxon Mobil continue to drive the production and supply of this essential material.
The process of chain-growth polymerization used to produce polypropylene ensures that the polymer chains are long and uniform, contributing to its excellent performance characteristics. From household items to industrial applications, polypropylene’s significance in the plastic industry cannot be overstated.
But what makes this material so special? Understanding the different types of polypropylene and their unique properties clarifies what makes this material special.
Types of Polypropylene
Polypropylene comes in several forms, each with distinct properties suited for various applications.
The most commonly used type is homopolymer polypropylene (PPH), which offers excellent strength and stiffness, making it ideal for a wide range of uses.
Whether it’s for packaging materials, textiles, or automotive parts, homopolymer polypropylene’s robustness ensures durability and reliability.
Copolymers of polypropylene are divided into random and block copolymers, each having unique attributes. Random copolymers are known for their clarity and flexibility, making them suitable for applications requiring transparency and flexibility.
On the other hand, block copolymers are tougher and more resilient, which can be further enhanced by increasing the ethylene content, thus expanding their application range.
Key Properties of PP Plastic
One of the standout features of polypropylene is its moisture resistance, thanks to its semi-crystalline structure, which results in low moisture absorption of less than 0.01% over 24 hours.
This property makes it an excellent choice for applications that require resistance to water and moisture. Additionally, PP’s chemical resistance to diluted bases and acids further enhances its utility.
Polypropylene also boasts impressive fatigue strength, allowing it to retain its shape under repeated bending and flexing, which is crucial for applications like living hinges.
Its thermal stability is another significant advantage, with a Vicat softening temperature of about 150 degrees Celsius (302 degrees Fahrenheit). This makes it suitable for applications exposed to high temperatures.
The material’s toughness and flexibility, combined with its low density, contribute to its widespread use in various industries. Whether it’s for automotive parts, consumer goods, or medical supplies, the unique properties of polypropylene ensure that it meets the demands of diverse applications.
The PP Injection Molding Process
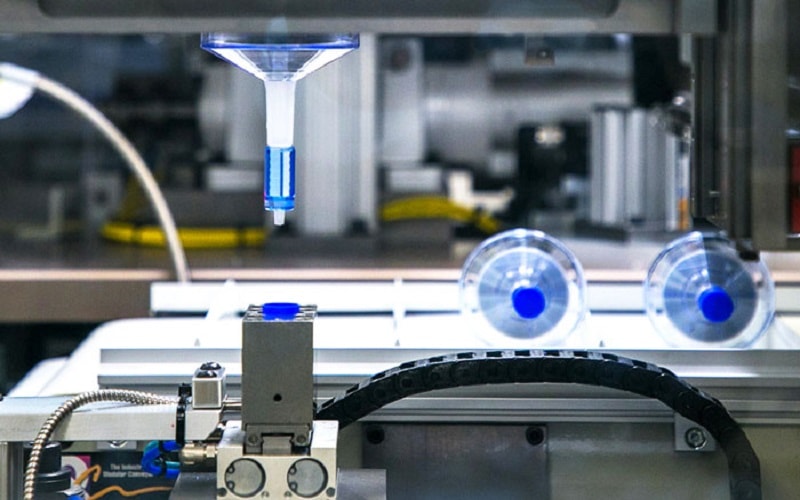
The polypropylene injection molding process begins with heating the material to its melting point and injecting it into a mold to form the desired shape. Polypropylene is typically available in the form of resins or pellets, which are melted and molded to produce high-quality plastic components through injection molding plastic. This primary manufacturing process ensures consistent and affordable production of various products.
A key advantage of polypropylene in injection molding is its low melt viscosity, which facilitates easier molding of thin features and reduces cycle times. This characteristic not only enhances productivity but also allows for the efficient molding of intricate designs.
Proper management of injection speed, pressure, and temperature settings is essential to optimize the polypropylene injection molding process and achieve superior product quality.
Ideal Conditions for PP Injection Molding
Maintaining ideal conditions during the polypropylene injection molding process is crucial for producing high-quality parts. The melt temperatures for polypropylene should ideally be maintained between 400°F and 500°F to avoid quality issues and ensure proper flow of the material. The melting point range of polypropylene is approximately 164 to 170 degrees Celsius, which must be carefully monitored during the process.
Mold temperatures play a significant role in the final product’s quality, with ideal ranges between 20 and 80°C helping to reduce stress and surface defects. Maintaining an injection pressure between 800 to 1,500 psi is also crucial for effective mold filling and minimizing defects such as flashing.
These parameters must be meticulously controlled to prevent issues and ensure the production of high-quality injection molded parts.

Common Challenges in PP Injection Molding
Before: Despite its advantages, polypropylene injection molding comes with its own set of challenges. One common issue is warping and dimensional inaccuracies caused by the material’s high thermal expansion coefficient. This can lead to parts that do not fit together properly or have uneven surfaces.
After: Despite its advantages, polypropylene injection molding comes with its own set of challenges:
- Warping and dimensional inaccuracies caused by the material’s high thermal expansion coefficient
- Parts that do not fit together properly
- Uneven surfaces
Another challenge is polypropylene’s poor bonding properties, which can result in parts sticking to the mold during the injection process and causing defects. Additionally, the material’s flammability poses safety risks, particularly in high-temperature environments.
Addressing these challenges requires careful process control and optimization to ensure the production of reliable and high-quality polypropylene components.
Advantages and Disadvantages of PP Injection Molding
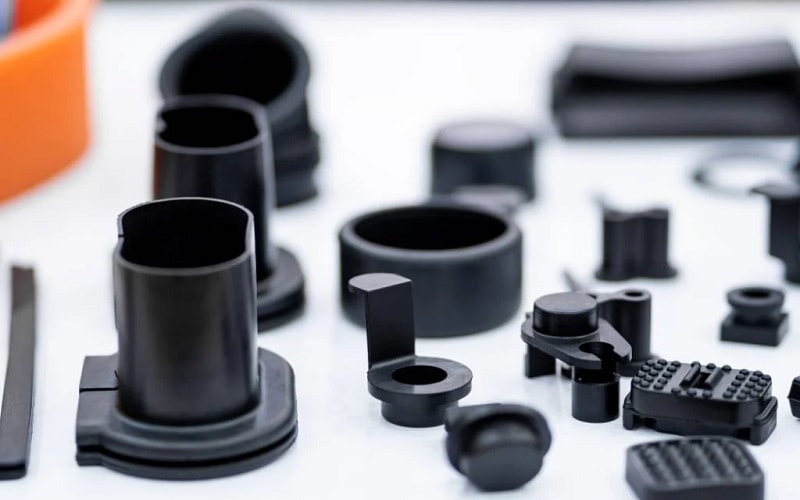
Polypropylene injection molding offers several advantages, making it a popular choice in various industries. The material is:
- Relatively inexpensive and easy to obtain, providing a cost-effective solution for manufacturers
- Durable and flexible in nature
- Strongly resistant to fatigue and chemical corrosion
These qualities further enhance its appeal.
However, it’s not without its drawbacks. Polypropylene has an average shrinkage rate of 1% to 3%, which can lead to dimensional challenges in certain applications. Balancing the benefits with the challenges is crucial for successful polypropylene injection molding. While its cost-efficiency and durability are significant advantages, issues like shrinkage and susceptibility to UV degradation must be addressed to ensure optimal performance.
Benefits of PP Injection Molding
One of the primary benefits of polypropylene injection molding is its cost-effectiveness. Compared to other thermoplastics, polypropylene is relatively inexpensive, making it a practical choice for a wide range of applications. Its flexibility and strength make it suitable for various uses, including automotive parts like door trims and instrument panels.
Polypropylene’s lack of BPA and excellent moisture resistance make it ideal for manufacturing food containers, ensuring safety and compliance with food safety standards. Its popularity in the automotive industry is also due to its affordability and ease of molding, which helps reduce production costs while maintaining quality.
Drawbacks of PP Injection Molding
Despite its many advantages, polypropylene injection molding has some notable drawbacks. The material is sensitive to UV light, leading to degradation and loss of structural integrity when exposed to sunlight for extended periods. This limits its use in outdoor applications without proper UV stabilization.
Another challenge is polypropylene’s poor adhesion to paint, making it difficult to achieve a desired finish on products without special surface treatments. High thermal expansion can also cause dimensional changes under temperature fluctuations, potentially affecting fit and functionality in certain applications.
Additionally, limited resistance to high temperatures increases the risk of structural failure in hot environments.
Applications of Polypropylene Injection Molding
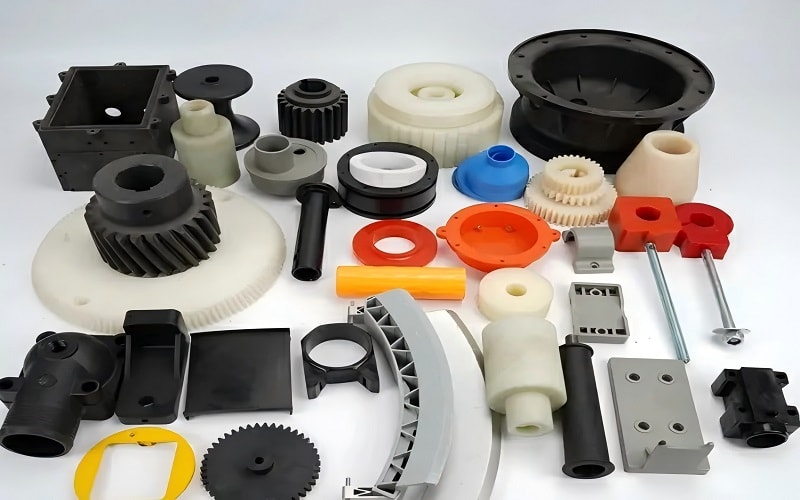
Polypropylene’s adaptability and unique properties make it suitable for a wide range of applications across various industries. From consumer goods to automotive components and medical supplies, the versatility of polypropylene injection molding and polypropylene pp injection molding is unmatched. Its ability to be molded into complex shapes and forms enhances its applicability in diverse sectors.
In the consumer goods sector, polypropylene is used for manufacturing items such as furniture, ropes, tapes, carpets, and camping equipment. Its lightweight and durable nature make it ideal for producing safe plates, food trays, and cups, as well as children’s toys.
In the automotive industry, polypropylene is used to fabricate lightweight components that require electrical resistance and durability. In the medical field, it is used for making syringes, trays, and other chemical-resistant and sterilizable items.
Consumer Goods
Polypropylene’s excellent resistance to water absorption makes it ideal for products that need to remain dry, such as food packaging.
Its durability and lightweight nature contribute to reduced shipping costs and easier handling.
Common household items made from polypropylene include kitchen appliances and furniture, showcasing its versatility in the consumer goods sector.
Popular applications in food packaging include foam boxes and PP plastic cups, which benefit from polypropylene’s moisture resistance and safety.
Toys, home appliances, carpets, and mats are also commonly manufactured using polypropylene, demonstrating its wide-ranging utility in everyday products.
Automotive Components
Polypropylene’s toughness and flexibility make it a preferred material in the automotive industry. Components such as battery cases and dashboards are often made from polypropylene due to its high strength and moisture resistance.
Using polypropylene in automotive applications offers advantages like reducing weight, which enhances fuel efficiency, a critical factor in modern vehicle design.
The material’s ability to withstand harsh environments and its electrical resistance further contribute to its suitability for automotive components. Incorporating polypropylene allows manufacturers to produce durable and reliable parts that meet stringent industry requirements.
Medical Supplies
The medical supplies industry greatly benefits from polypropylene’s unique properties. Its exceptional chemical resistance allows it to withstand sterilization processes, making it suitable for various medical applications.
Common uses include syringes, petri dishes, and other items that require sterile and chemical-resistant materials.
Polypropylene ensures the safety, durability, and effectiveness of medical supplies, which are essential in healthcare settings. Its ability to maintain integrity under sterilization conditions makes it a reliable choice for critical medical applications.
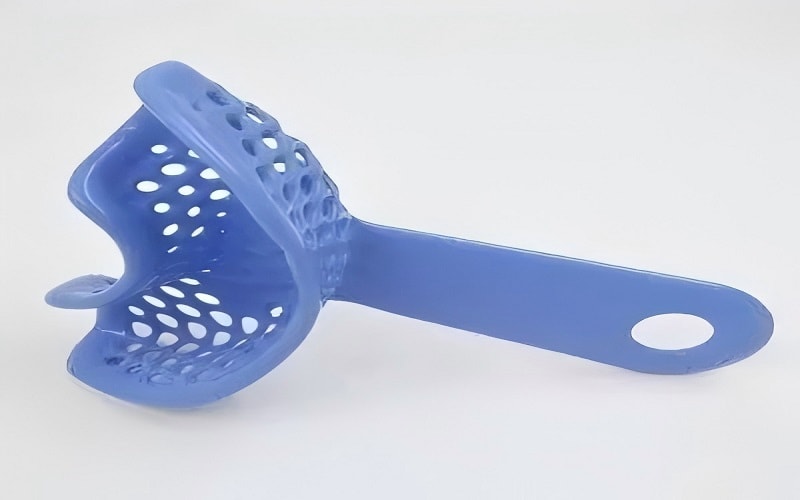
Design Guidelines for PP Injection Molding
Designing for polypropylene injection molding requires careful consideration of various factors to optimize performance and manufacturability. Ensuring the appropriate wall thickness and draft angles can significantly impact the quality and durability of the final product. Attention to details such as living hinges and radii can also enhance the functionality and lifespan of injection molded parts.
Following these design guidelines enables manufacturers to produce high-quality, reliable components tailored to specific application requirements.
Wall Thickness and Draft Angles
The recommended wall thickness for polypropylene parts ranges from 0.635 mm to 3.81 mm, ensuring sufficient strength while avoiding excessive material use. Maintaining this range helps prevent issues like warping and sink marks, which can compromise the quality of the final product.
Draft angles are equally important to facilitate the removal of parts from the mold without causing surface defects. A minimum draft angle of 1 degree is commonly used, with up to 5 degrees recommended for textured surfaces. For filled polypropylene, a draft angle of up to 10 degrees may be necessary to ensure smooth release from the mold.
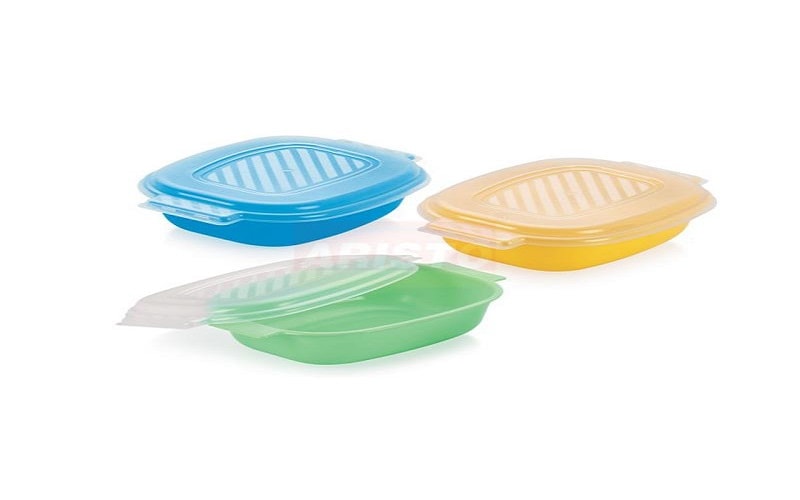
Living Hinges and Radii
Living hinges are critical components that allow parts to flex without the need for additional hardware. Designing living hinges with a thickness between 0.2 mm and 0.51 mm can significantly enhance their durability and functionality.
Incorporating generous radii in hinge designs further improves their longevity by reducing stress concentrations. These design considerations are essential for producing high-quality polypropylene components that meet the demands of various applications.
Optimizing the PP Injection Molding Process
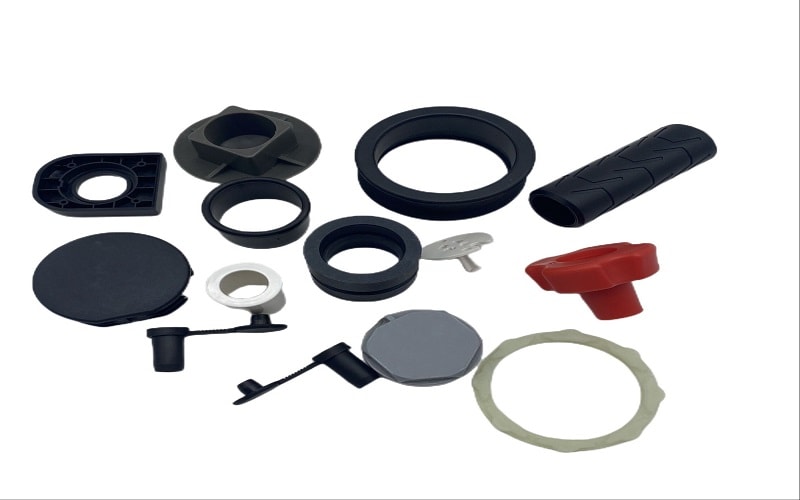
Optimizing the polypropylene injection molding process is critical to enhancing the efficiency and quality of the final products. This involves careful control of injection speed, pressure, and temperature settings, all of which play a pivotal role in minimizing defects and ensuring consistent part quality. Adhering to design guidelines and process optimizations leads to superior results in production runs.
Understanding the flow rate of polypropylene and its impact on tensile strength and impact resistance is also crucial. Commercial and fine tolerances must be maintained to ensure part functionality and manufacturability. This section explores the key aspects of controlling injection speed and pressure, as well as temperature management, to optimize the injection molding process.
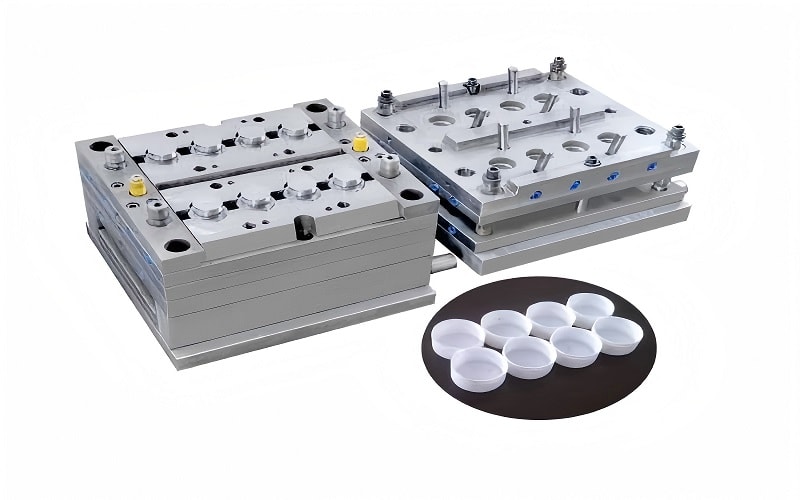
Controlling Injection Speed and Pressure
Balancing injection speed and pressure is essential to reduce defects and ensure consistent part quality. The recommended injection molding speed for the PP injection molding process should be fast enough to minimize internal stresses while ensuring complete mold filling. Adjusting the injection speed based on the part’s geometry and wall thickness can significantly improve the quality of the final product.
Higher injection pressure may be required for parts with complex geometries or thicker walls to ensure proper filling and minimize defects. Careful control of these parameters enables the production of high-quality, reliable injection molded parts using an injection molding machine that meet stringent industry requirements.
Temperature Management
Maintaining the correct melt temperature is crucial to prevent the solidification of the polymer before filling the mold. This ensures that the material flows smoothly and fills the mold completely, reducing the risk of defects. Optimal mold temperature is also essential for achieving uniform cooling and preventing warpage in molded parts.
Proper temperature management helps maintain the material’s properties, ensuring that the final product meets the required specifications. Monitoring and adjusting temperatures throughout the injection molding process enhances the quality and durability of polypropylene components.
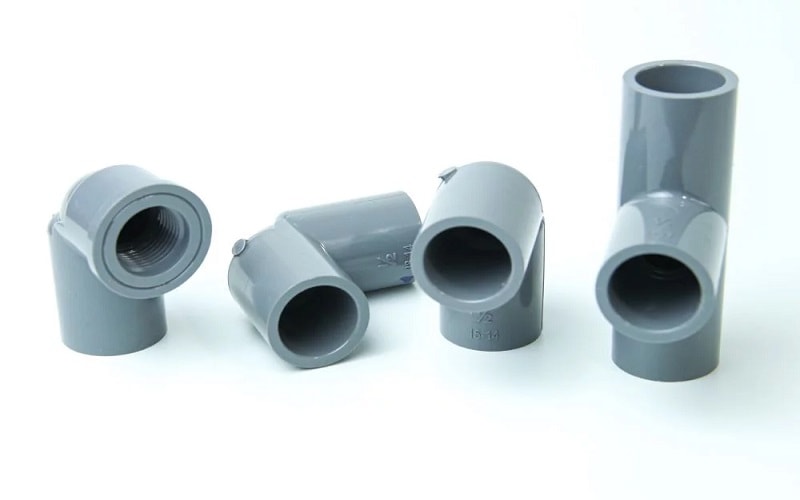
Summary
Mastering polypropylene injection molding requires a deep understanding of the material’s properties, types, and the intricacies of the molding process. From selecting the right type of polypropylene to optimizing injection speed, pressure, and temperature settings, each step plays a vital role in producing high-quality, durable plastic components. The advantages of PP injection molding, such as cost-effectiveness, flexibility, and chemical resistance, make it a preferred choice across various industries.
However, challenges like shrinkage, UV sensitivity, and poor adhesion to paint must be addressed to ensure optimal performance. By adhering to design guidelines and optimizing the injection molding process, manufacturers can overcome these challenges and harness the full potential of polypropylene. The future of polypropylene injection molding is bright, with endless possibilities for innovation and application.
Frequently Asked Questions
What are the ideal conditions for polypropylene injection molding?
The ideal conditions for polypropylene injection molding are melt temperatures between 400°F and 500°F, mold temperatures between 20°C and 80°C, and injection pressures ranging from 800 to 1,500 psi. Adhering to these parameters ensures optimal processing and quality of the final product.
What are the common types of polypropylene used in injection molding?
The common types of polypropylene used in injection molding are homopolymer polypropylene (PPH) and copolymers, which consist of random and block copolymers. Each type offers distinct properties suited for various applications.
What are the key properties of polypropylene plastic?
The key properties of polypropylene plastic include excellent moisture and chemical resistance, good fatigue strength, thermal stability, and notable toughness and flexibility. These characteristics make it a versatile material for various applications.
What are the benefits of using polypropylene in injection molding?
Using polypropylene in injection molding offers significant advantages such as cost-effectiveness, flexibility, strength, excellent moisture resistance, and suitability for food containers. These properties make polypropylene an ideal choice for a wide range of applications.
What are the common challenges in polypropylene injection molding?
Common challenges in polypropylene injection molding include warping and dimensional inaccuracies stemming from high thermal expansion, along with issues related to poor bonding properties and flammability. These factors can significantly affect the quality and performance of the final product.