PPA plastic, or Polyphthalamide, is a high-performance plastic known for its high heat resistance, strength, and low moisture absorption. Industries like automotive and electronics rely on PPA plastic due to these properties that enable it to perform well in extreme conditions.
This article breaks down what PPA plastic is, its standout properties, and why it’s a top choice in demanding applications.
What Is PPA Plastic?
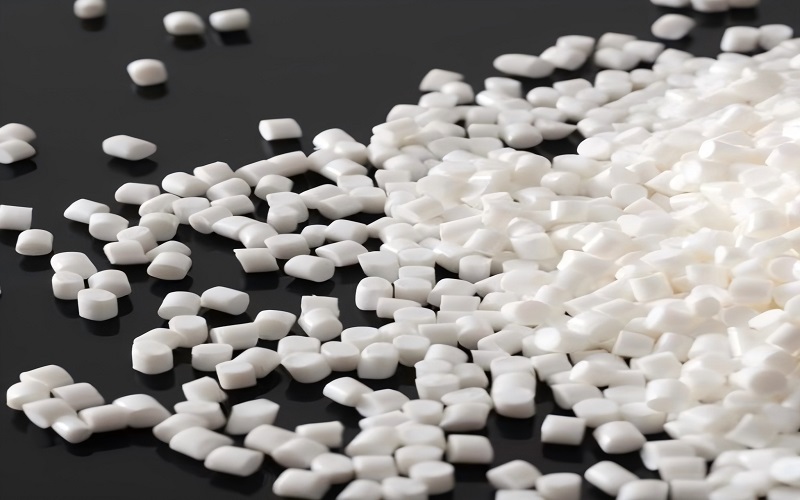
Polyphthalamide (PPA) plastic is a high-performance resin that belongs to the family of semicrystalline partially aromatic polyamide. Known for its high stiffness, excellent heat resistance, and low moisture absorption, PPA based resins exhibit extraordinary mechanical strength, fatigue resistance, and thermal stability, making it ideal for demanding applications such as pump wear rings, mechanical components, and infrared soldering environments.
PPA stands out from other engineering plastics due to its remarkable combination of specific properties. PPA’s chemical structure, with a robust polymer backbone and strong polymer chain interactions, imbues it with superior mechanical strength, higher thermal capabilities, and chemical resistance, even under relatively high processing temperatures, positioning it as a top choice for applications where these attributes are paramount, including plastic rubber composites for enhanced durability.
Key Characteristics of PPA Plastic
Polyphthalamide (PPA) plastic boasts a high melting point and a glass transition temperature exceeding 150°C, which ensures its temperature stability in high-temperature environments. Additionally, PPA has a heat distortion temperature above 280°C, making it suitable for applications that require durability under intense heat, such as fuel cut-off valves in the oil industry.
One of PPA’s standout features is its low moisture absorption compared to traditional polyamides like Nylon 66 within the nylon family. This characteristic contributes to greater mechanical stability and excellent dimensional stability, making PPA more effective in humid environments.
Furthermore, PPA’s superior chemical resistance, including against harsh substances like acetic acid, allows it to perform exceptionally well in harsh chemical environments, outlasting other polyamides such as PA6 and PA66.
PPA maintains its mechanical properties at elevated temperatures better than many other nylons, including PA6, PA66, and PA46. This makes it an ideal choice for high-temperature applications and demanding industrial settings where both heat resistance, high heat resistance, exceptional heat resistance, and mechanical integrity are critical, despite being a higher priced thermoplastic.
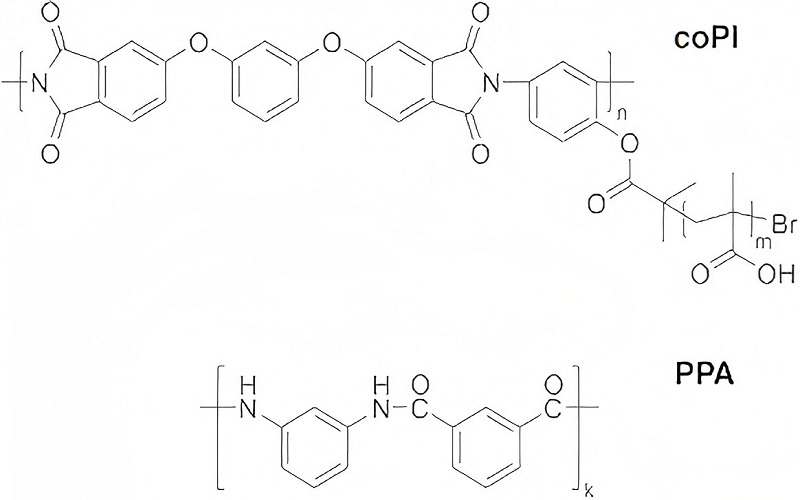
Applications of PPA Plastic in Various Industries
The versatility of PPA plastic is evident in its widespread use across multiple industries. Its exceptional thermal and mechanical properties make it suitable for high-temperature applications, including:
- Automotive components
- Electrical connectors
- Aerospace parts
- Industrial machinery
This adaptability allows PPA plastic to meet the demanding requirements of various sectors.
PPA plastic finds applications in various sectors due to its unique properties, including ppa material.
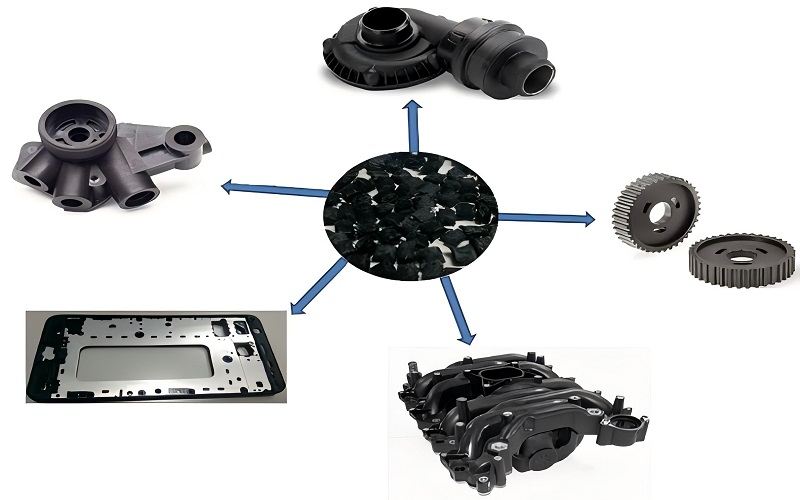
Automotive Industry
PPA plastic plays a crucial role in the automotive industry. It is essential for components that need to endure high temperatures and mechanical stress. It is commonly used in fuel lines, coolant lines, fuel line connectors, thermostat housings, and gas pipes.
These applications benefit from PPA’s heat resistance and mechanical integrity, ensuring reliable performance under the hood.
The commercial utility of PPA in the automotive sector is undeniable, as it helps maintain the efficiency and durability of critical systems. Automotive manufacturers utilize PPA’s properties to produce components that meet stringent performance standards and enhance overall vehicle reliability.
Electronics Industry
PPA plastic plays a crucial role in the electronics industry, where its durability and high-temperature resistance are highly valued. It is used in applications such as surface mount devices and LED mounts, which require materials compatible with lead-free soldering processes.
The inclusion of flame retardants in PPA plastic is particularly important for electronic components, as it enhances fire safety by inhibiting or delaying combustion. The combination of excellent electrical properties and heat resistance makes PPA a preferred choice for various electronic applications, ensuring both performance and safety.
Industrial Applications
Beyond automotive and electronics, PPA plastic is extensively used in other industrial applications, particularly those requiring high temperature and chemical resistance. Its mechanical strength and ability to withstand aggressive chemicals such as brake fluid, synthetic engine oil, and sulfuric acid make it ideal for demanding environments.
PPA’s performance under such conditions is exemplified in components like air coolant pumps, which must operate reliably despite exposure to harsh substances and high temperatures. This versatility underscores PPA’s value in industrial settings, where durability and resilience are paramount.
Modifications and Enhancements of PPA Plastic
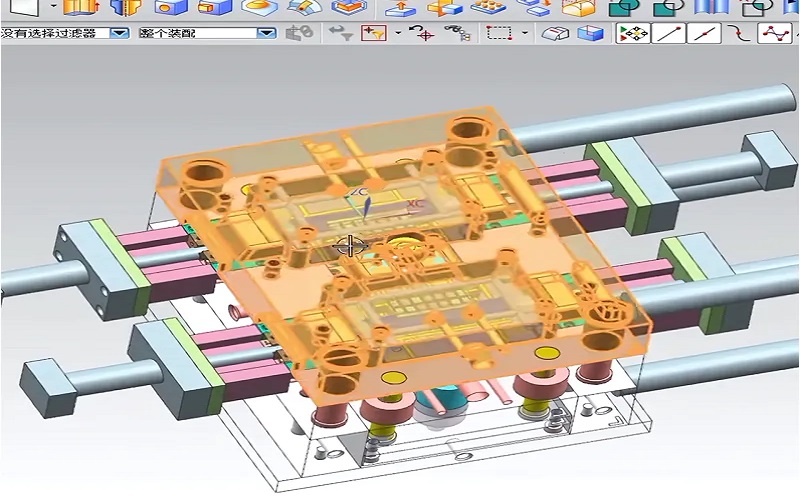
Various modifications and additives can further enhance the performance of PPA plastic. These enhancements can tailor PPA to specific applications, improving properties such as strength, flexibility, and impact resistance.
Key modifications include reinforcing agents, impact modifiers, and heat stabilizers.
Reinforcing Agents
Incorporating glass fibers into PPA formulations significantly improves stiffness, strength, and resistance to creep under load. Mineral acids contribute to dimensional stability and reduce material shrinkage, making PPA parts more reliable in maintaining their shape and size, such as in water heater manifolds.
The combination of glass fibers and mineral fillers enhances the overall mechanical properties of PPA, resulting in a material that can withstand greater mechanical stress and maintain its integrity in demanding applications like sports equipment. Additionally, blending PPA with nylon enhances impact resistance, further broadening its utility.
Impact Modifiers
Elastomers are commonly used as impact modifiers in PPA to prevent crack propagation and enhance stiffness and overall toughness. These additives improve the material’s resilience, making it more suitable for applications subjected to harsh conditions and physical stress, such as air coolers.
The incorporation of impact modifiers ensures that PPA maintains mechanical integrity even in challenging environments, extending the lifespan of components and reducing the likelihood of failure.
Heat Stabilizers
Heat stabilizers play a critical role in enhancing the thermal stability of PPA plastic, preventing degradation at high temperatures. This is particularly important for applications in automotive under-the-hood components, electrical connectors, and various industrial components that operate under extreme heat, including those exposed to transformer oil.
Heat stabilizers help PPA maintain performance and reliability in high-temperature applications, ensuring components withstand prolonged heat exposure without compromising structural integrity.
Processing and Manufacturing Considerations
Processing PPA plastic requires careful consideration of various factors to achieve consistent part quality. Injection molding is the primary method used, allowing for efficient production of complex geometries.
However, specialized equipment and safety measures are essential to handle the high temperatures involved.
Injection Molding Techniques
Injection molding of PPA plastic often necessitates processing temperatures that can reach as high as 350°C (662°F) to ensure proper flow and material integrity. Careful control of these temperatures is crucial to achieve optimal results and avoid defects in the final products.
Specialized machinery that maintains high temperatures is critical for efficient and safe production, ensuring PPA components meet stringent quality standards.

Machining and Surface Finishing
Machining and surface finishing are critical steps in working with PPA plastic to achieve the desired specifications and functional requirements. Techniques such as milling, turning, and drilling require robust tools that can withstand most PPA grades’ high melting points.
CNC machining is often preferred for producing complex shapes with high precision, and PPA’s low moisture absorption contributes to its dimensional stability during these operations, especially for components like supply lines.
Effective machining and surface finishing ensure that the final PPA components meet stringent design and performance criteria.
Comparing PPA with Other Engineering Plastics
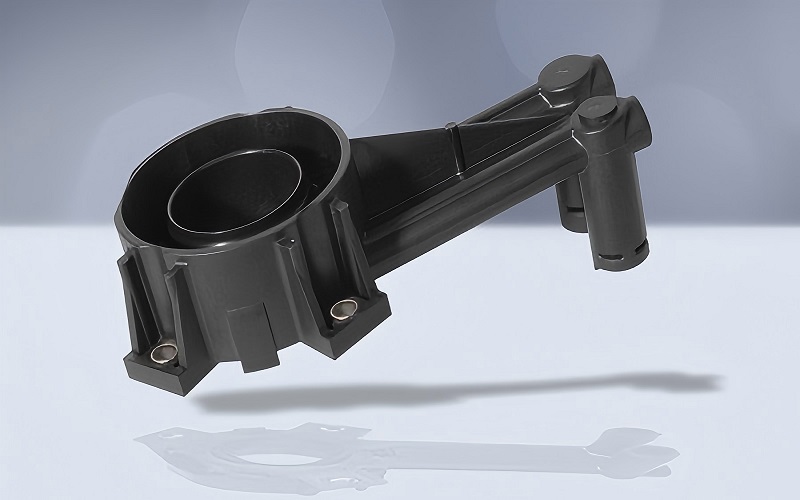
Polyphthalamide (PPA) plastic stands out when compared to other engineering plastics due to its high heat deflection temperature, which exceeds 280°C, making it suitable for high-temperature applications such as fuel modules. Its mechanical attributes, including high tensile strength and stiffness, make it ideal for structural applications, especially in comparison to PA66, which exhibits higher strength and stiffness at elevated temperatures.
Blending PPA with other materials, such as nylon, enhances toughness while maintaining dimensional stability and demonstrating effective chemical resistance compared to other nylons, particularly in environments involving formic acid. PPA’s superior performance in maintaining mechanical properties at elevated temperatures and in harsh chemical environments sets it apart from alternatives like PA6, PA66, and PA46.
These comparisons highlight why PPA grades might be chosen over other engineering plastics, offering a combination of high performance and reliability in demanding applications.
Design Guidelines for Using PPA Plastic
Designing with PPA plastic requires a thorough understanding of its unique properties and capabilities. Surface treatments like Teflon coating can enhance PPA’s good chemical resistance and reduce friction, making it more suitable for specific applications.

Structural Integrity and Optimization
Stiffness, high strength, and durability are key physical properties of PPA plastic that contribute to its structural integrity. PPA’s mechanical strength enables it to withstand significant loads without bending or breaking, making it ideal for structural components.
Maintaining consistent wall thickness is crucial for avoiding warping and internal stresses during molding. Additionally, PPA’s low thermal expansion coefficient aids in maintaining good dimensional stability and part integrity across temperature variations.
Thermal Management Strategies
Incorporating ribbing and gussets into designs can enhance the load-bearing capacity and rigidity of PPA components, optimizing their structural integrity. Considering the coefficient of thermal expansion of PPA is essential to prevent dimensional changes from temperature fluctuations.
Effective thermal management is crucial in applications that operate under high temperatures, ensuring the integrity and thermal performance of PPA components.
Environmental and Safety Aspects of PPA Plastic
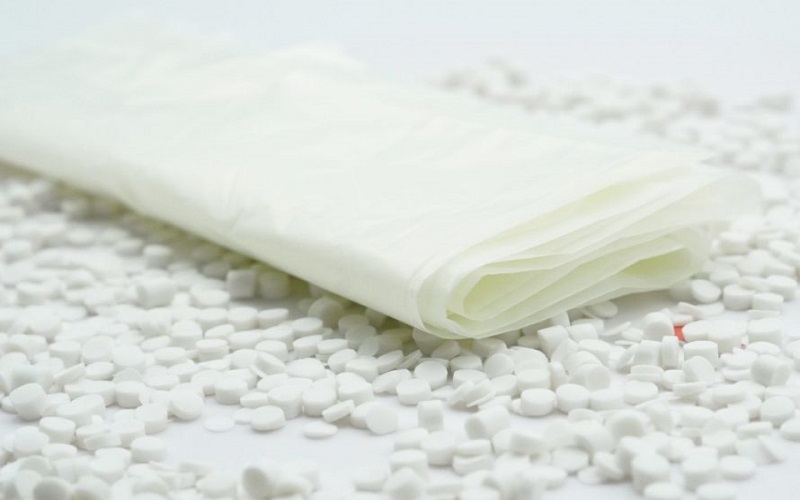
Polyphthalamide (PPA) plastic is fully recyclable through processes such as remelting or depolymerization, contributing to sustainability. Safety assessments have shown that PPA and its byproducts pose low toxicity risks under normal handling and usage conditions.
However, concerns about microplastics and their potential effects on health and ecosystems are ongoing. While PPA does not biodegrade naturally in the environment, its recyclability helps mitigate its environmental footprint.
Summary
Summarizing the key points, PPA plastic stands out due to its exceptional heat resistance, mechanical strength, and chemical stability. Its versatility across various industries, from automotive to electronics and industrial applications, underscores its value as a high-performance material.
As we look towards a future where advanced materials play a crucial role in innovation and sustainability, PPA plastic offers a compelling solution. By harnessing its unique properties and capabilities, manufacturers can create reliable, high-quality components that meet the most demanding requirements.
Frequently Asked Questions
What are the primary properties of polyphthalamide (PPA) plastic?
Polyphthalamide (PPA) plastic boasts high stiffness, excellent heat resistance, low moisture absorption, and remarkable mechanical strength, making it ideal for demanding applications. Its thermal stability and chemical resistance further enhance its suitability for various uses.
What industries commonly use PPA plastic?
PPA plastic is predominantly utilized in the automotive, electronics, and industrial sectors due to its high temperature and chemical resistance, making it suitable for applications such as fuel line connectors and electrical connectors.
How can the performance of PPA plastic be enhanced?
To enhance the performance of PPA plastic, incorporating reinforcing agents like glass fibers and mineral fillers, as well as using impact modifiers and heat stabilizers, is beneficial. These additives significantly improve strength, impact resistance, and thermal stability.
What are the processing considerations for PPA plastic?
PPA plastic is best processed through injection molding with specialized equipment due to its high-temperature sensitivity. Additionally, machining and surface finishing are essential to meet specific performance standards.
Is PPA plastic environmentally friendly?
PPA plastic is not biodegradable but is fully recyclable, which helps mitigate its environmental impact. Its low toxicity under normal usage conditions further supports its relative environmental friendliness.