Short run plastic molding is ideal for quickly producing small quantities of plastic parts. It’s commonly used for prototyping, market testing, and specialized projects without the high costs of traditional molding.
In this article, we will cover its benefits, challenges, and the scenarios where it excels.
Understanding Short Run Plastic Injection Molding
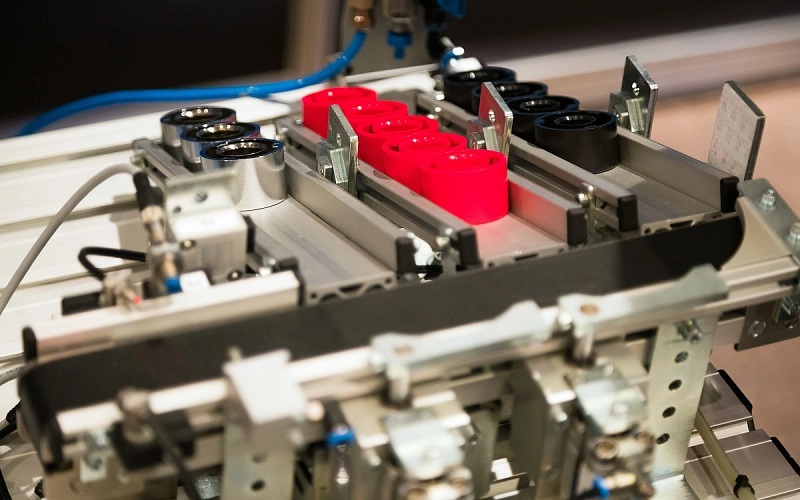
Short run plastic injection molding is a manufacturing process designed specifically for producing limited quantities of plastic parts. Unlike traditional injection molding, which is geared towards high-volume production, short run injection molding is focused on producing specialty parts, prototypes, and conducting test runs.
Typically, this method produces quantities ranging from a few dozen to a few thousand units, making it ideal for projects with lower demand or continuous product development cycles. Additionally, short run molds are an effective solution for these specific needs.
The production process for short run plastic injection molding is notably quicker, often taking just 1 to 2 weeks. This speed is achieved through the use of more flexible and economical tooling options, such as aluminum molds, which allow for rapid adjustments and modifications. This flexibility not only reduces lead times but also ensures that the manufacturing process can keep pace with evolving design requirements and market conditions.
Key Advantages of Short Run Plastic Injection Molding
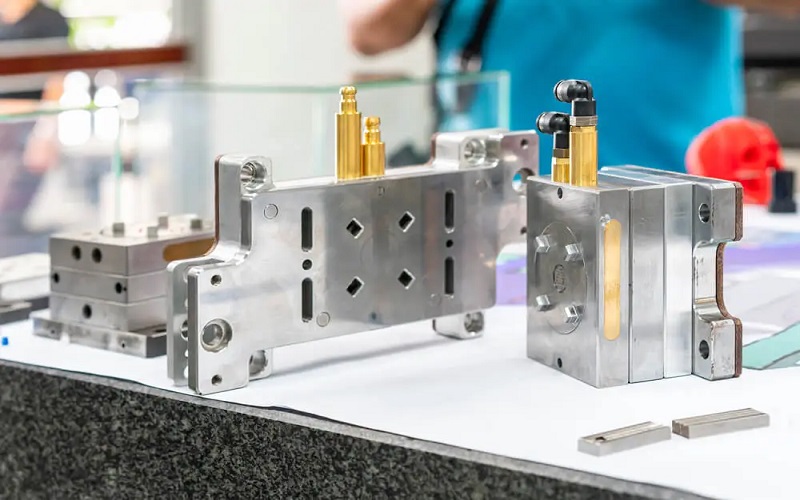
One of the main advantages of short run injection molding is its cost-effectiveness. Lower tooling and production costs make this method an attractive option for businesses looking to produce high-quality plastic parts without significant financial investment. The high levels of automation in short run injection molding also contribute to its efficiency, reducing labor costs and minimizing human error in the production process.
Flexibility is another key benefit. Short run plastic injection molding allows for greater design modifications and the production of small batches, sometimes as few as 100 units. This flexibility is invaluable for meeting specific market demands and testing new products without committing to large-scale production. Additionally, the faster production cycles and reduced lead times facilitate a quicker time to market, enabling businesses to respond rapidly to market changes and customer feedback.
Moreover, short run injection molding provides a cost-effective way to test the market without large-scale production risks. Companies can produce small quantities of a new product to gauge market interest and gather feedback before deciding to invest in high-volume production. This approach not only reduces financial risk but also allows for more informed decision-making based on real-world data.
Challenges in Short Run Plastic Injection Molding
Despite its many advantages, short run plastic injection molding does come with some challenges. One of the primary drawbacks is the higher per-unit cost compared to high-volume production. This is primarily due to the less optimized production processes and the smaller quantities involved, which prevent manufacturers from benefiting from economies of scale.
Tooling durability is another concern. In short run plastic injection molding, the tooling, often made from aluminum, may wear out more quickly than the hardened steel molds used in high-volume production. Although aluminum molds are recognized for their durability and can handle up to 10,000 shots, they are not as long-lasting as steel molds. Additionally, the limited material choices available in short run injection molding can be a constraint for some projects.
However, the use of aluminum molds in short run injection molding can also serve as a cost-effective insurance policy against production tool failures. Opting for aluminum molds allows manufacturers to quickly produce molds or make adjustments without significant delays or costs, ensuring smooth production despite unexpected challenges.
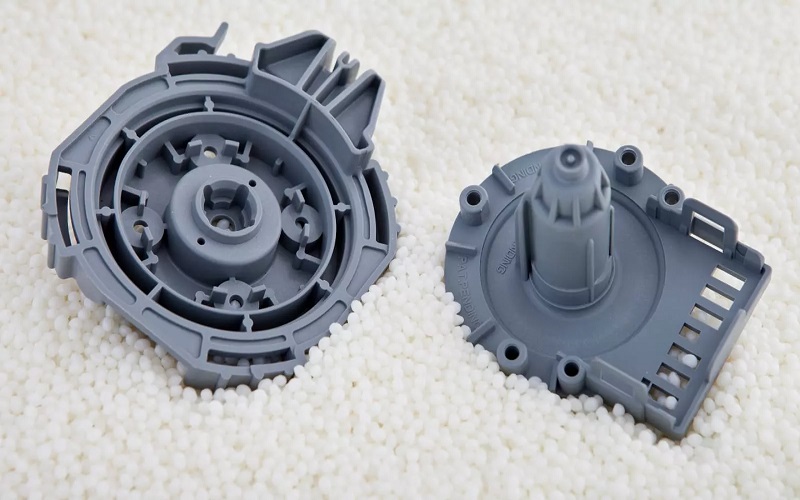
The Role of Aluminum Molds in Short Run Production
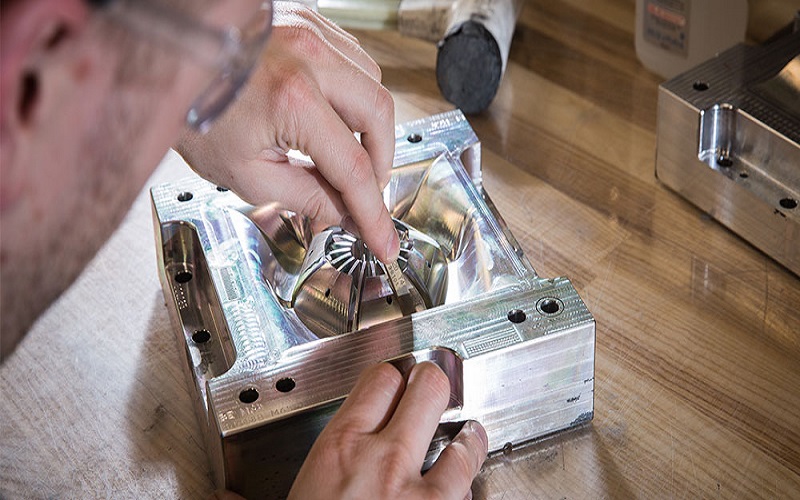
Aluminum molds play a crucial role in the landscape of short run injection molding. They are generally cheaper compared to steel molds, significantly reducing overall production costs. This cost efficiency is particularly important in short run low volume production scenarios where managing expenses is critical. Additionally, the simpler design of aluminum injection molds allows for faster production times, which is essential when speed is of the essence.
Furthermore, aluminum molds provide a high degree of flexibility in design adjustments, making them ideal for applications like prototyping and managing production uncertainties. By offering both cost and time efficiency, aluminum molds enable manufacturers to meet quick-turn demands without incurring significant overhead costs, thus playing a vital role in the short run production landscape.
Furthermore, aluminum molds provide a high degree of flexibility in design adjustments, making them ideal for applications like prototyping and managing production uncertainties. By offering both cost and time efficiency, aluminum molds enable manufacturers to meet quick-turn demands without incurring significant overhead costs, thus playing a vital role in the short run production landscape.
Benefits of Using Aluminum Molds
Using aluminum molds in short run injection molding offers numerous benefits. Here are some of the main advantages:
- Lower tooling costs: The softer material of aluminum reduces tooling expenses.
- Faster manufacturing process: Aluminum molds speed up the manufacturing process, resulting in reduced production costs.
- Quicker turnaround times: Aluminum molds provide faster transitions from design to production.
These efficiencies make aluminum molds a great choice for short run injection molding.
Aluminum molds also offer significant flexibility for design changes. The ease with which these molds can be adjusted or refined makes them particularly suitable for rapid prototyping and design testing. This flexibility ensures that any necessary modifications can be made quickly and efficiently, enabling manufacturers to iterate on their designs and bring products to market faster than ever before. An aluminum mold can significantly enhance this process.
Ideal Applications for Short Run Plastic Injection Molding
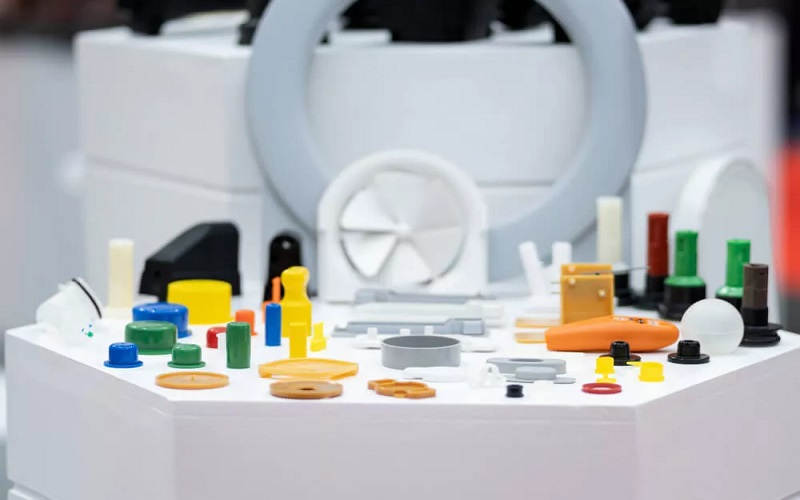
Short run plastic injection molding is ideally suited for a variety of applications. One of the most common uses is prototyping, which allows companies to test designs and gather feedback before committing to larger production runs. This method is also effective for market testing, enabling businesses to produce small quantities of a product to gauge market interest and make informed decisions about scaling up production.
In addition to prototyping and market testing, short run molding is valuable for bridge production and producing specialized components. Bridge tools can facilitate production during product ramp-up phases, serving as a temporary solution while awaiting full production molds. This process is also ideal for producing specialized components, particularly in niche markets that require customized orders and design flexibility.
Comparing Short Run and High Volume Production
When comparing short run injection molding to high volume production, several key differences emerge. High volume production can yield tens of thousands to even millions of parts produced, focusing on efficiency and uniformity in manufacturing processes. This scale allows for significant economies of scale, leading to lower per-unit costs as output increases. However, the initial investment for high volume production is usually significant due to the costs of advanced tooling and setup.
In contrast, short run injection molding is less optimized and generally incurs higher per-unit costs. The production processes are designed to be flexible rather than efficient, which can elevate costs. Additionally, lead times for tooling are generally longer in high volume production due to the complexity of the molds required. Short run injection molding, on the other hand, can achieve faster turnaround times, making it more suitable for projects that require quick market responses.
Another key difference lies in the material options available. High volume production typically offers a wider range of softer materials compared to short run injection molding. This limitation can be a constraint for some projects, but it is often offset by the flexibility and speed that short run molding provides.
Rapid Prototyping with Short Run Molding
Rapid prototyping is one of the standout benefits of short run plastic injection molding. This method enables businesses to create models and rapid prototypes quickly, facilitating the transition from design to production. Simpler mold creation processes in short run injection molding speed up time-to-market, helping businesses respond quickly to market changes and customer feedback. Additionally, rapid tooling enhances the efficiency of this process.
Aluminum molds are particularly beneficial for rapid prototyping, enabling designers to receive new iterations of their products in as little as two days. This speed allows for quick testing and adjustments before committing to large-scale production, significantly reducing development costs and risks. Additionally, short run injection molding can serve as a temporary solution during the tooling phase for high-volume production, ensuring that product development cycles remain uninterrupted.
Industries such as automotive have effectively used short run injection molding to rapidly prototype parts, allowing for quicker iterations in design and reduced time-to-market. This method has also been employed by companies to test product designs before committing to high-volume production, showcasing its versatility and effectiveness in various contexts.
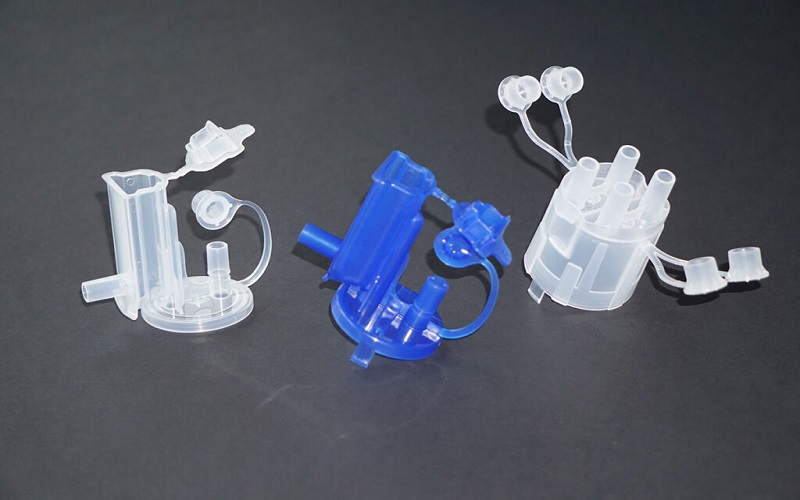
Cost Considerations for Short Run Projects
When embarking on short run plastic injection molding projects, it’s crucial to consider the various cost factors involved. The primary expense is typically the tooling cost, which can vary significantly based on the design complexity and production volume. Complex part designs necessitate more intricate molds, which can substantially increase tooling costs and production times.
Other cost considerations include setup time, material expenses, and labor costs. Setting up injection molding machines involves configuring the equipment for the specific part being produced, which adds to the overall cost. Material expenses depend on the type of thermoplastics used, with costs generally ranging from $1 to $5 per kilogram.
Labor costs, including setup, monitoring, and maintenance, are also crucial factors when calculating the total expenses for short run projects. However, the cost per part generally decreases with larger production volumes, as fixed costs are spread across more units.
How to Choose a Short Run Injection Molding Service
Choosing the right short run injection molding services is essential for ensuring the success of your project. One of the first factors to consider is the experience of the service provider, as this often correlates with reliability and quality assurance. Evaluating the supplier’s facilities and capabilities is also important; visiting their site can provide valuable insights into their machinery and operational standards.
Additionally, it’s crucial to ask potential suppliers about their quality control processes to understand their commitment to maintaining high standards. Establishing a feedback loop with your supplier fosters continuous improvement and addresses any potential issues proactively.
Good communication and a strong working relationship with your supplier can make a significant difference in the overall success of your short run injection molding project.
Case Studies: Successful Short Run Injection Molding Projects
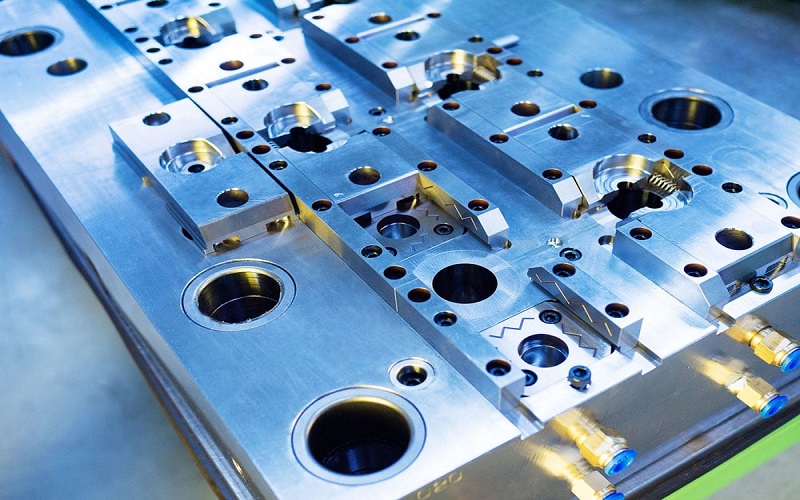
One notable example of a successful short run injection molding project involves an appliance manufacturer who employed a short-run injection mold as a bridge tool. This strategy was used to maintain production while their primary tool was being repaired, effectively minimizing downtime and ensuring a steady supply of parts. This case highlights the versatility and practicality of short run injection molding in overcoming production challenges and maintaining operational continuity.
Such case studies underscore the broader applicability of short run injection molding across various industries. From rapid prototyping to market testing and bridge production, the flexibility and efficiency of short run injection molding make it an invaluable tool for modern manufacturers seeking to innovate and adapt quickly.
Summary
Throughout this guide, we’ve explored the many facets of short run plastic injection molding. From its cost-effectiveness and flexibility to the critical role of aluminum molds, this manufacturing process offers a robust solution for producing limited quantities of plastic parts. While there are challenges to consider, such as higher per-unit costs and tooling durability, the benefits often outweigh the drawbacks for many applications.
In conclusion, short run plastic injection molding provides a powerful tool for rapid prototyping, market testing, and producing specialized components. By understanding the advantages and challenges, as well as how to select the right service provider, businesses can leverage this method to stay competitive and responsive in an ever-changing market landscape. Embrace the possibilities of short run plastic injection molding and harness its potential to drive your projects forward with confidence.
Frequently Asked Questions
What is short run plastic injection molding?
Short run plastic injection molding is a targeted manufacturing method for creating limited quantities of plastic components, ideal for specialty items, prototypes, and test runs, usually ranging from a few dozen to a few thousand units. This approach is efficient for testing concepts before full-scale production.
What are the main advantages of using short run injection molding?
Using short run injection molding offers cost-effectiveness with reduced tooling expenses, flexibility for design changes, quicker turnaround times, and a lower risk approach for market testing. These advantages make it an appealing option for many projects.
What are some challenges associated with short run plastic injection molding?
Short-run plastic injection molding often faces challenges such as higher per-unit costs, quicker wear of tooling, and limited material choices, necessitating careful management of tooling durability. These factors can impact both production efficiency and overall project budget.
Why are aluminum molds commonly used in short run production?
Aluminum molds are preferred in short run production due to their cost-effectiveness, quicker production times, and design flexibility, making them ideal for rapid tooling and prototyping. This approach streamlines the manufacturing process and reduces overall expenses.
How do I choose the right short run injection molding service?
To choose the right short run injection molding service, prioritize providers with relevant experience, assess their facilities and capabilities, and inquire about their quality control processes. Establishing a feedback loop will help ensure continuous improvement and address issues proactively.