Shrinkage plastic refers to the volume reduction of plastic materials as they cool after molding. This phenomenon impacts the accuracy and quality of molded parts.
If you’re involved in manufacturing, knowing how shrinkage affects plastics and how to measure and manage it is crucial.
This article will cover the causes of shrinkage, its measurement, and ways to control it effectively.
Understanding Shrinkage in Plastic Materials
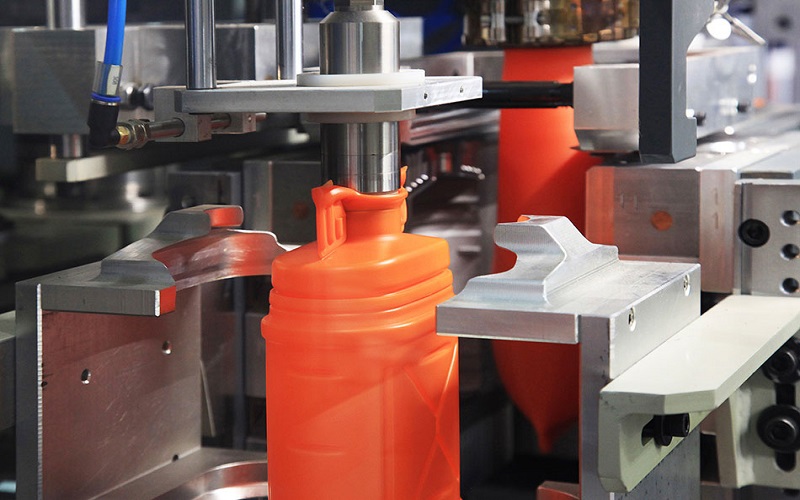
Shrinkage in plastic materials is the phenomenon where the volume of polymers contracts. This contraction predominantly occurs during the cooling phase of the injection molding process, while the part is still in the mold.
As the molten plastic cools, it solidifies and shrinks, a process influenced by molecular interactions within the material. The majority of shrinkage occurs while the part is in the mold, with additional, albeit smaller, shrinkage continuing after the part is ejected.
Several factors contribute to this shrinkage. For instance, plastics with higher molecular weight tend to shrink less due to stronger intermolecular forces. Additionally, fillers and fibers incorporated into the plastic can alter its shrinkage behavior, often reducing the overall shrinkage compared to virgin polymers. However, post-ejection shrinkage can still occur as the part continues to cool and stabilize. Temperature and moisture content are critical in stabilizing the shrinkage once the part has cooled down.
Excessive shrinkage can pose significant challenges, such as warpage and internal stresses, leading to deformations in the final plastic parts. Understanding these nuances is crucial for designing and manufacturing high-quality plastic components that meet precise specifications.
Next, we will explore how to measure shrinkage rates accurately, ensuring that these factors are accounted for in the production process.
Measuring Shrinkage Rates in Plastics
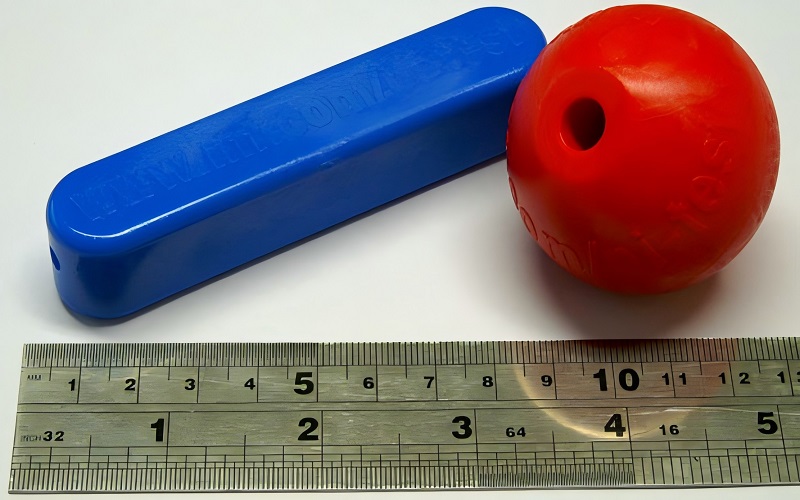
Accurate measurement of shrinkage rates ensures the dimensional accuracy of plastic parts. Plastic shrinkage is typically quantified in thousandths of an inch per linear inch, with common shrinkage rates ranging from 0.001 to 0.020 per inch.
To achieve reliable measurements, inspections of molded parts should be conducted at least one day after ejection. This delay allows the parts to stabilize and provides a more accurate representation of their final dimensions.
ISO standards play a pivotal role in standardizing the shrinkage measurement process. These guidelines specify how to inject test samples from both thermoplastics and thermosets, ensuring uniformity in shrinkage testing. By adhering to these standards, manufacturers can consistently measure and compare shrinkage rates across different materials and processes.
Understanding these measurement techniques is crucial as we delve into the factors influencing shrinkage rates.
Factors Influencing Shrinkage Rates
Shrinkage rates in plastics are influenced by a myriad of factors, each playing a critical role in the final dimensions of the molded part. The type of material, the presence of fillers and fibers, and the cooling rates during the molding process all contribute to different shrinkage outcomes.
At the molecular level, shrinkage begins when the plastic material melts and subsequently cools. The alignment of plastic molecules during the molding process, influenced by shear and extensional forces, also impacts shrinkage behavior.
Effectively managing these factors requires a detailed understanding. The following subsections will explore how polymer type and crystallinity, fillers and fiber reinforcement, and temperature and cooling rates specifically affect shrinkage rates. These insights will provide a comprehensive understanding of how to control and predict shrinkage in various injection molding scenarios.
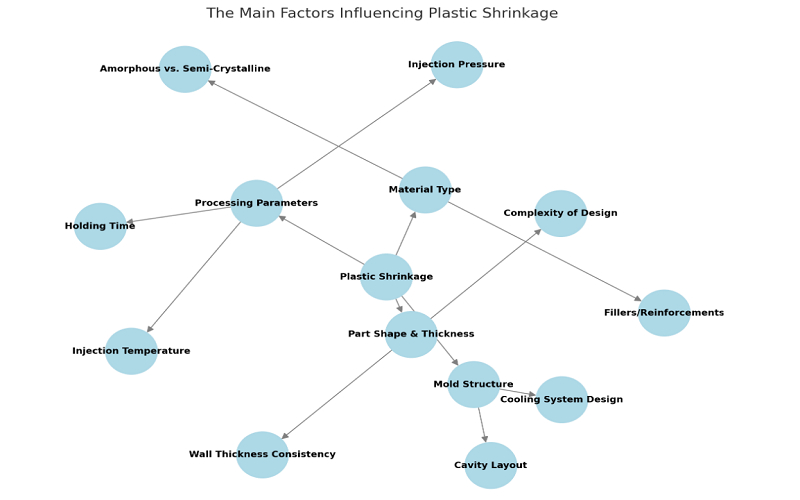
Polymer Type and Crystallinity
The type of plastic material used in the injection molding process significantly impacts the shrinkage of the final molded part. Semi-crystalline materials, for example, maintain their orientation in the direction of flow during cooling, leading to higher shrinkage rates compared to amorphous materials.
Crystallinity in polymers influences how they shrink as they cool. More crystalline materials tend to experience greater shrinkage compared to semi-crystalline ones.
Amorphous polymers, on the other hand, continue to contract until they reach a temperature where their molecular structure becomes fixed. Selecting the appropriate polymer type for specific applications ensures that shrinkage is kept within acceptable limits.
Fillers and Fiber Reinforcement
Additives like fillers and fibers can significantly influence the shrinkage behavior of polymers filled plastic materials. Fillers generally increase the stiffness of the plastic, which may result in greater shrinkage during cooling.
However, filled resins usually shrink less than unfilled ones. The direction of fiber alignment plays a crucial role in shrinkage behavior; shrinkage is reduced along the fiber direction but may increase transversely.
Reinforced plastics, such as those filled with long glass fibers, are less prone to shrinkage compared to non-reinforced types. Understanding the role of fillers and fibers helps manufacturers better predict and manage the shrinkage behavior of their materials.
Temperature and Cooling Rates
Temperature and cooling rates are critical factors that can lead to significant variations in the final shrinkage of molded parts.
Thinner wall sections cool more quickly, resulting in reduced shrinkage compared to thicker sections. The cooling rate during the molding process can influence the extent of shrinkage, with different cooling periods leading to varying shrinkage outcomes.
Controlling temperature and cooling rates helps manufacturers manage the shrinkage behavior of their plastic materials more effectively. This knowledge is essential for optimizing the injection molding process and producing high-quality parts.
Impact of Unequal Shrinkage
Unequal shrinkage in molded parts, often referred to as warpage, can lead to significant quality issues. Uneven cooling of molded parts causes internal stresses, which can result in warping and dimensional changes. Thinner sections and complex shapes are particularly susceptible to warpage due to unequal shrinkage.
Material properties, mold design, and processing parameters all influence the extent of warpage. Internal stresses resulting from unequal shrinkage can cause cracks in molded plastic parts, compromising their structural integrity.
Designing molds and processes that minimize the detrimental effects of unequal shrinkage is crucial.
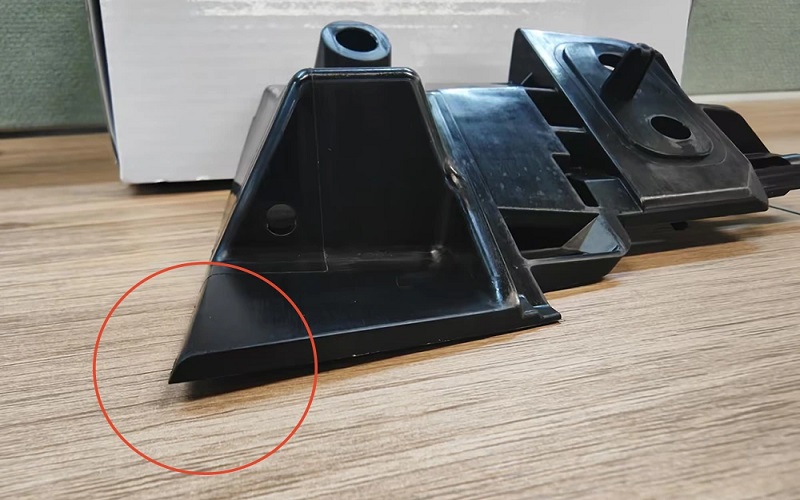
Managing Shrinkage in Injection Molding
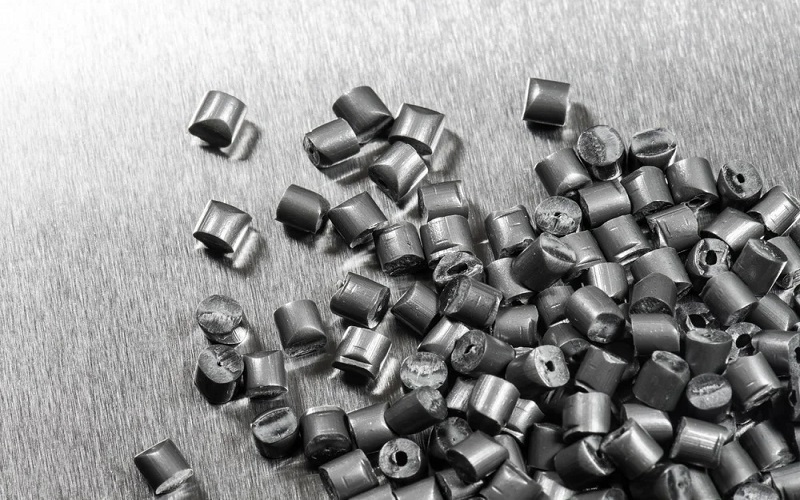
Managing shrinkage in the injection molding process involves a combination of material selection, mold design, and processing parameters. The geometry and thickness of a molded part significantly affect its shrinkage behavior. Proper mold design, including the placement of cooling channels and gates, can minimize the risk of warping.
Shrinkage issues can be addressed by changing temperatures and pressures. Additionally, adjusting packing and cooling times can also help.
Mold engineers often rely on experience and trial and error to control post mold shrinkage effectively. Manufacturers who understand and manage these factors can produce high-quality plastic parts with minimal defects.
Simulation Software
Simulation software is an invaluable tool for predicting and managing shrinkage in injection molding. These tools enable manufacturers to visualize expected shrinkage, allowing for proactive adjustments in both part design and processing conditions. Identifying potential problems early in the design cycle, simulation software minimizes the risk of shrinkage-related issues.
Advanced simulation software can diagnose root causes of shrinkage and implement effective corrective measures in production. This technology is essential for optimizing the injection molding process and ensuring high-quality outcomes.
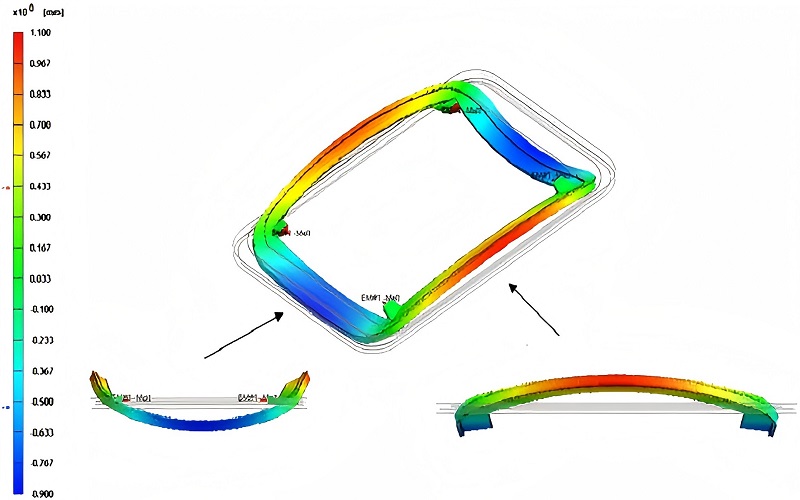
Material Selection
Selecting the right plastic materials is crucial for managing shrinkage. Materials with low and consistent shrinkage rates are essential for high-precision injection molded parts. A material supplier typically provides data sheets that include shrinkage ranges for various wall thicknesses, aiding in material selection.
Choosing materials with appropriate shrinkage characteristics ensures the dimensional accuracy and quality of plastic parts. This selection process is a critical step in the injection molding process.
Common Shrinkage Values for Different Plastics
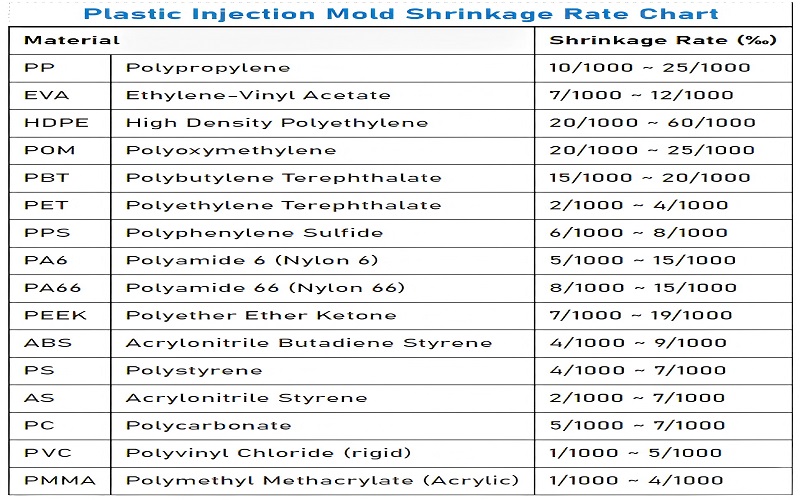
Different plastics exhibit varying shrinkage rates, making it essential to refer to material data sheets for guidance. High-density polyethylene, polypropylene, and polycarbonate are examples of materials with high shrinkage rates. Polypropylene, for instance, has a shrinkage percentage between 1.0% and 2.5%.
High-Density Polyethylene (HDPE) typically shows a shrinkage rate of 1.5% to 4.0%. Liquid Crystal Polymer (LCP) can have a shrinkage percentage ranging from 0.1% to 0.6%, while polycarbonate generally experiences a shrinkage rate of 0.6% to 0.8%.
These common shrinkage values aid in selecting the appropriate materials for specific applications, including considerations of the material shrinkage rate.
Practical Tips for Reducing Shrinkage
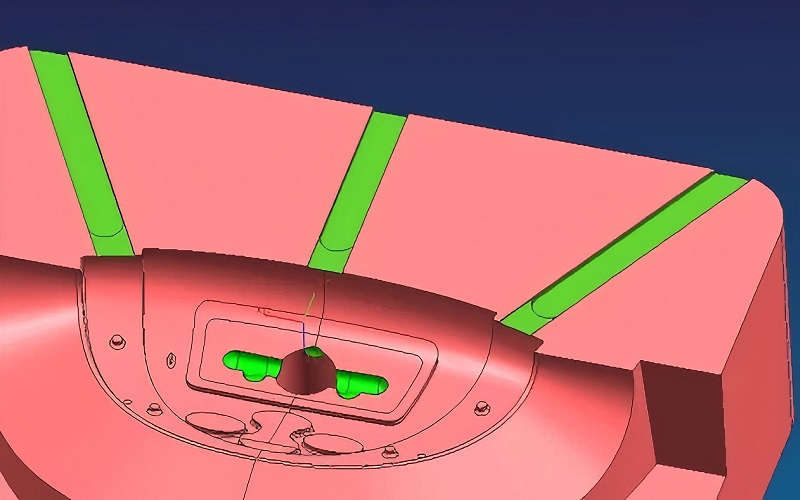
Reducing shrinkage in injection molding requires a combination of design adjustments and process optimizations. Designing mold components with uniform wall thickness can help achieve even cooling and minimize shrinkage. Mold cavities should be slightly oversized to accommodate the anticipated shrinkage of the plastic material.
Implementing cooling channels in the mold design promotes uniform temperature distribution and reduces shrinkage discrepancies. Adjusting packing and cooling times, as well as mold temperature, can significantly impact shrinkage control.
Following these practical tips helps manufacturers reduce shrinkage and improve the quality of their plastic parts.
Methods to Determine Mold Shrinkage
Several standardized methods exist for determining mold shrinkage in plastic parts. One common technique is to compare the dimensions of the mold with those of the final product.
The shrinkage ratio can be calculated using the formula: shrinkage % = 100 × (mold dimensions – product dimensions) ÷ mold dimensions.
Visual inspections and measurements can be used alongside mathematical calculations to determine the accuracy of mold shrinkage. These methods ensure that shrinkage is accurately accounted for in the design and production processes.
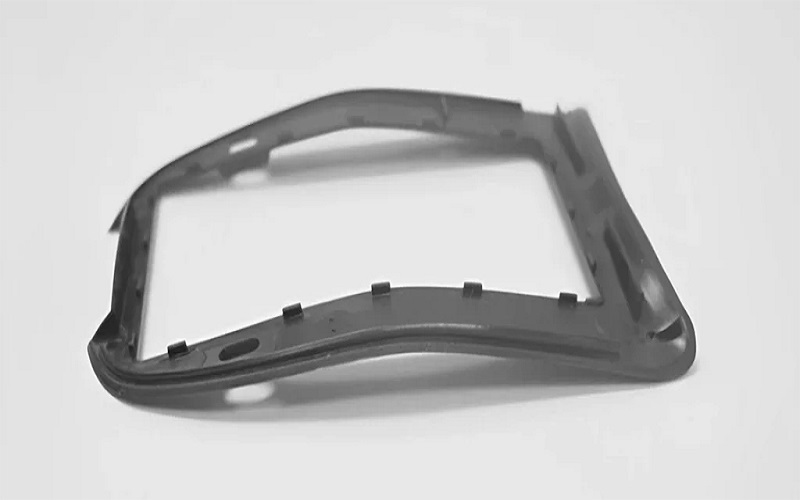
Case Studies: Successful Shrinkage Management
Real-world examples of successful shrinkage management highlight the practical application of the discussed concepts.
In an automotive project, advanced polymer PPS was selected for its thermal stability, reducing cycle times by 20% while ensuring high production efficiency.
A consumer electronics company used ABS for smartphone housings, employing in-mold decoration to enhance aesthetics and streamline production.
A medical device manufacturer achieved regulatory compliance and precision by using medical-grade polycarbonate and advanced mold design techniques. These case studies underscore the importance of effective shrinkage management in various industries.
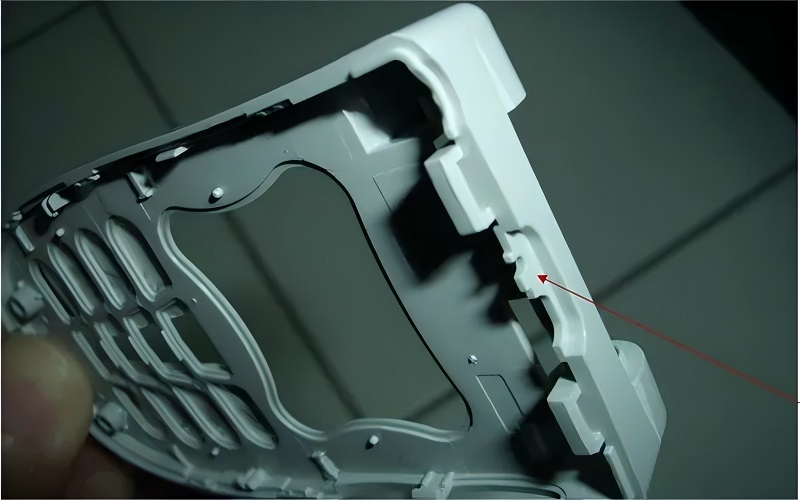
Summary
In summary, understanding and managing shrinkage in plastic materials is crucial for producing high-quality, accurate plastic parts.
By considering factors such as material type, fillers, temperature, and cooling rates, manufacturers can control shrinkage effectively. Practical tips and real-world case studies provide valuable insights into optimizing the injection molding process.
With the knowledge gained from this guide, you are now equipped to tackle shrinkage challenges head-on. Embrace these strategies to enhance your injection molding processes and achieve superior results.