Silicone injection molding is a process for creating detailed, durable silicone parts by injecting liquid silicone rubber into a mold.
It’s essential in industries like medical, automotive, and electronics.
This article covers the key techniques, benefits, and applications of silicone injection molding.
Understanding Silicone Injection Molding
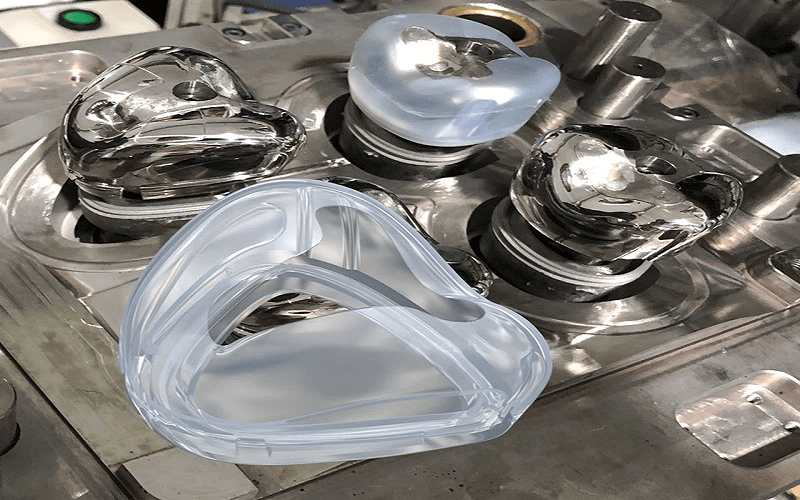
Injection molding started in the 19th century, initially aimed at creating billiard balls from celluloid. The post-World War II era saw a surge in demand for low-cost, mass-produced items, pushing the injection molding industry into prominence.
The introduction of liquid silicone rubber (LSR) in the late 1970s, an inorganic polymer made of silicon, oxygen, carbon, and hydrogen, marked a significant technological advancement.
Today, liquid silicone rubber molding, or LIM molding, excels in producing parts with complex shapes and intricate details due to LSR’s low viscosity.
Platinum-cured silicone rubbers offer enhanced performance characteristics, including improved tensile strength, clarity, and consistency without peroxide residue.
This evolution distinguishes liquid silicone injection molding from high consistency rubber (HCR) and thermoplastic processes, yielding superior outcomes in various applications.
The Silicone Injection Molding Process
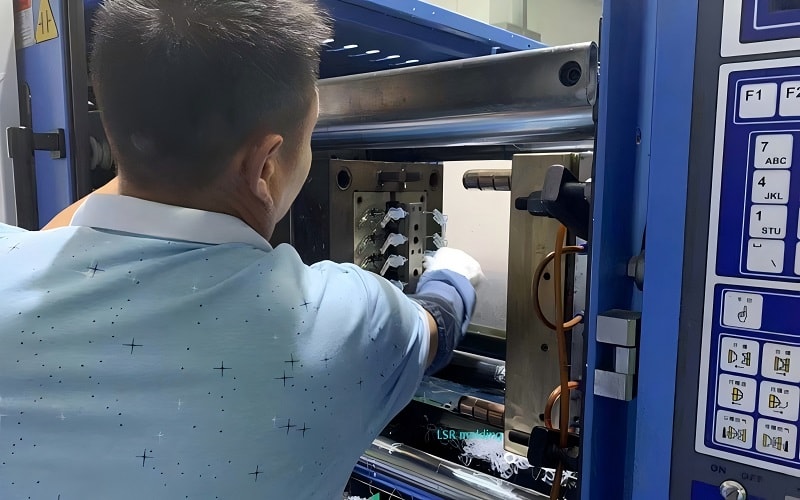
The silicone rubber injection molding process enables the production of highly detailed and intricate silicone parts, primarily driven by the liquid injection molding process using liquid silicone rubber (LSR) and lsr injection molding, a versatile material with excellent performance characteristics.
LSR molding process is divided into four main phases: material preparation, injection, curing, and demolding. Each phase is crucial for ensuring the quality and precision of the final product.
Material Preparation
Material preparation is fundamental to the injection molding process. It starts with the precise mixing of two room temperature compounds, Part A and Part B liquids, which must be blended uniformly to achieve a homogenous mixture essential for consistency and quality.
A static mixer is typically used to ensure thorough integration in the mixing process, preparing the mixture for the subsequent molding phases.
Injection Phase
In the injection phase, liquid silicone rubber is injected into the mold using a specialized machine with a reciprocating screw or ram injector. Precise control over injection parameters ensures that the material fills every intricate feature of the mold.
The term “shot” refers to the specific amount of LSR administered, with continuous pressure preserving mold integrity until completion.
A cool runner system prevents premature curing of silicone in the runners. Molds and silicone are heated using electrical heaters or water circulation to optimal temperatures between 250° to 300°, ensuring smooth flow into thin cross-sections without requiring highly polished surfaces.
Curing Process
After injection, the curing process begins, transforming the liquid silicone rubber into a solid state under heat. Compression molding, which involves applying pressure to shape the material, can complement this process by enhancing material distribution in thicker sections.
Elevated temperatures and molding pressures enhance curing, ensuring the material sets properly and achieves the desired mechanical properties.
Upon completing the cure cycle, the molded silicone can be removed without distortion or tearing.
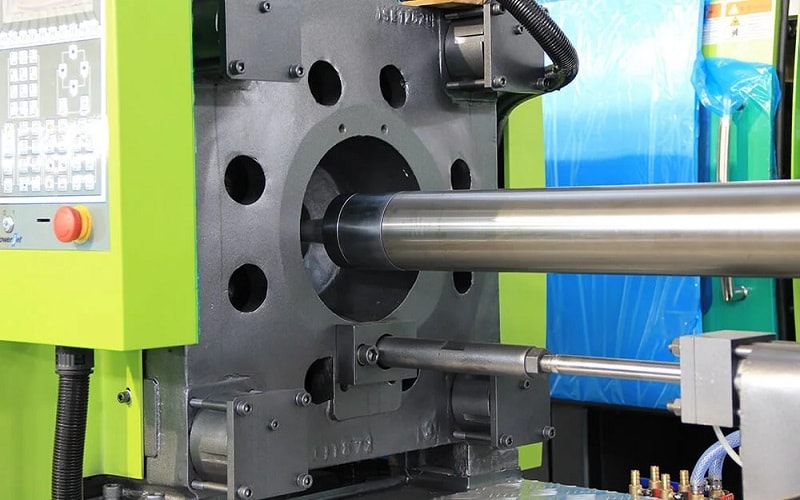
Demolding
The final phase, demolding, is vital for preserving the integrity of the molded components. Mold design facilitates easy removal of cured silicone parts without damage, typically done manually rather than using ejector pins.
Allowing silicone parts to reach a specific degree of stiffness before demolding prevents distortion and maintains quality.
Advantages of Silicone Injection Molding
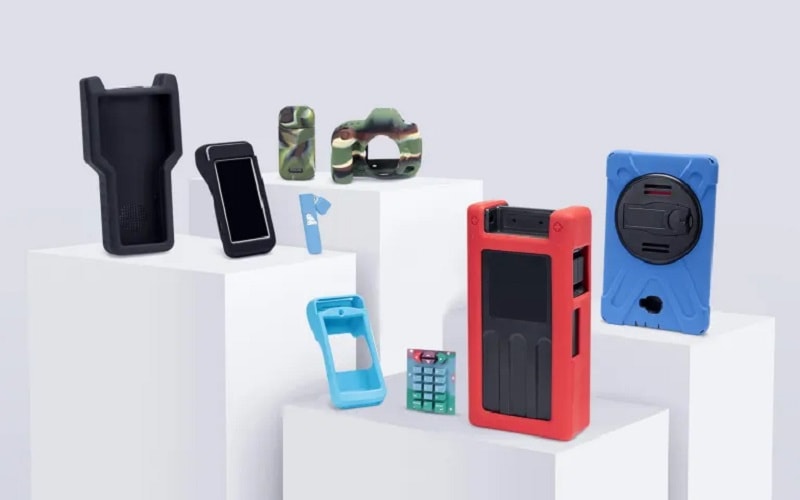
Silicone injection molding offers numerous advantages, making it a preferred choice for many industries. The introduction of liquid silicone rubber in the 1970s provided remarkable design flexibility and the ability to create intricate shapes and structures difficult to achieve with traditional methods.
Advancements in thermoplastic injection molding technology have improved efficiency and precision, with automated systems enhancing the overall production process.
Reduced Cycle Time
A notable benefit of silicone injection molding is reduced cycle time, allowing for faster completion and significantly boosting overall manufacturing efficiency.
Cycle times for components like keypads range from 30 seconds to 2 minutes, increasing output and reducing production costs, making the process more economically viable.
High Precision and Tight Tolerances
Silicone injection molding excels in achieving high precision and tight tolerances, producing consistently high-quality parts with accurate dimensions.
Controlled injection parameters ensure 95 to 99 percent mold filling, minimizing variance and enhancing dimensional consistency. This precision is crucial for applications requiring exact measurements.
Maintaining precision is especially important in industries where slight deviations can compromise functionality. In medical and automotive applications, the consistency and accuracy of silicone parts are crucial for reliable performance under various conditions.
Minimal Waste
Silicone injection molding is praised for minimal waste production. Implementing a cold runner system significantly reduces excess material, contributing to cost savings and eco-friendliness, and supporting sustainability in manufacturing.
Reducing waste enhances the overall economic efficiency of the production process in silicone injection molding.
Key Applications of Silicone Molded Parts
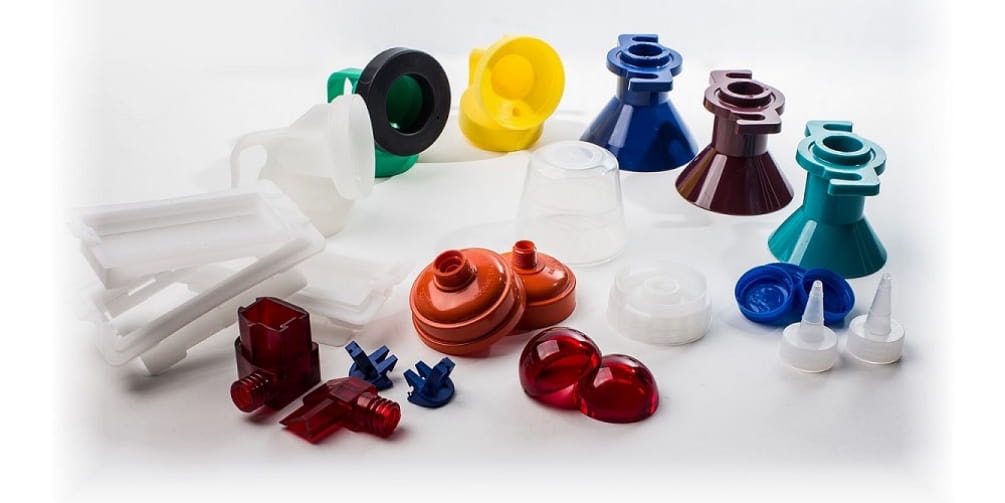
Silicone molded parts are used in many industries due to the unique properties of liquid silicone rubber. This versatile material has significantly evolved, enhancing heat resistance and mechanical properties, making it suitable for various applications.
Applications of silicone molded parts range from medical devices to automotive components and consumer products.
Medical Devices
In medical technology, liquid silicone rubber is valued for its flexibility, inertness, and biocompatibility, making it ideal for applications requiring prolonged human contact.
LSR components are used in drug delivery devices and surgical instruments due to their chemical resistance and ability to maintain sterility, ensuring patient safety and effective device functioning.
LSR is also used to create critical components like seals and valves that must perform reliably in demanding environments.
Silicone’s resistance to bacteria growth and ability to withstand sterilization processes like steam autoclaving make it indispensable in the medical field, particularly when considering lsr materials.
Automotive Components
The automotive industry greatly benefits from the unique properties of silicone molded parts. Liquid silicone rubber is favored for its resistance to extreme temperatures and environmental conditions, making it reliable for automotive applications, from gaskets to cushioning pads and ruggedized electronic devices.
Silicone parts in vehicles can endure harsh conditions, ensuring consistent performance and longevity. Consequently, the use of silicone components in the automotive sector is increasing, offering solutions that combine durability with flexibility.
Consumer Products
Silicone’s versatility is also valued in the consumer products industry for its softness and temperature resistance. Liquid silicone rubber is ideal for kitchenware and electronic goods, with products incorporating features like soft-touch surfaces and water-resistant designs for enhanced safety and usability.
Besides kitchen utensils and electronic covers, silicone is used in various consumer goods for its durability and comfort. Its moldability into intricate and functional designs makes it a popular choice for innovative and reliable products.
Design Considerations for Silicone Injection Molding
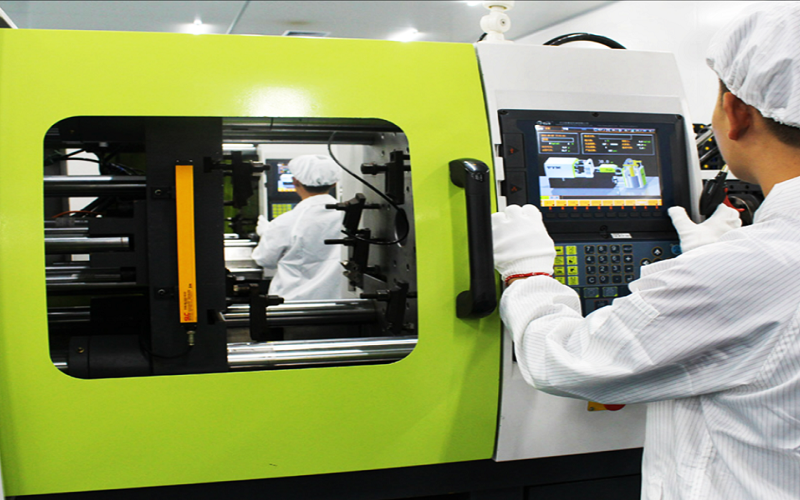
Designing for silicone injection molding requires careful consideration to ensure the final product’s success. Uniform wall thickness, proper draft angles, and avoiding undercuts are key elements to address during the design phase to prevent issues like dimensional inaccuracies, warpage, and complications during demolding.
Uniform Wall Thickness
Maintaining uniform wall thickness is crucial for the integrity of silicone molded parts. For smaller parts, a thickness of 0.025 to 0.030 inches is recommended, while larger parts should have at least 0.040 to 0.050 inches. Uniformity reduces the risk of weak points and defects, improving overall integrity.
In liquid silicone rubber molding, wall thickness can be as thin as 0.010 inches, depending on adjacent thicker sections. Consistency helps avoid issues like dimensional inaccuracies and warpage, ensuring the final product’s quality.
Proper Draft Angles
Draft angles facilitate the easy removal of parts from the mold. While a 1-degree draft is typical, some shallow designs can manage with zero draft.
However, using a draft angle of less than 0.5° can complicate demolding and should be avoided.
Proper draft angles ensure efficient production and preserve the integrity of molded parts.
Avoiding Undercuts
Undercuts can complicate the ejection process in silicone injection molding. Designers can minimize undercuts by incorporating pass-thru coring and other techniques, streamlining production and ensuring the final product meets desired specifications without compromising quality.
Quality Control in Silicone Injection Molding
Quality control is paramount in silicone injection molding to maintain high standards. Inspections range from partial checks to full production part approval processes (PPAP), based on critical dimensions specified in CAD models to ensure consistency and accuracy.
The measurement process often involves using coordinate-measuring machines (CMM) to assess critical dimensions. Automated technologies have been integrated into the inspection process for in-process checks without additional costs or delays, meeting diverse industry standards to ensure only top-quality parts qualify.
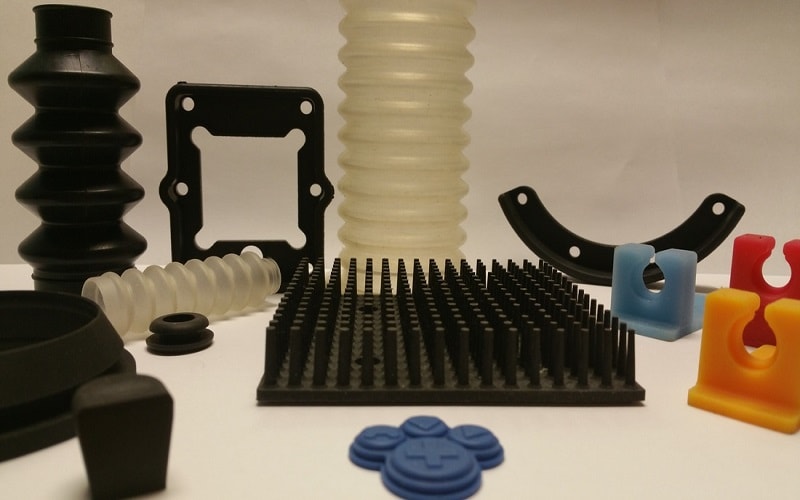
Custom Solutions in Silicone Injection Molding
Custom solutions in silicone injection molding offer tailored options to meet specific business needs, including additives like pigments for color and flame retardants for safety.
Custom silicones may be processed with techniques like heat curing or using catalysts to achieve desired material properties.
Customized silicone solutions undergo iterative testing and optimization to meet defined performance criteria, ensuring the final product meets and exceeds specific application requirements, providing reliable and high-quality silicone molded parts.
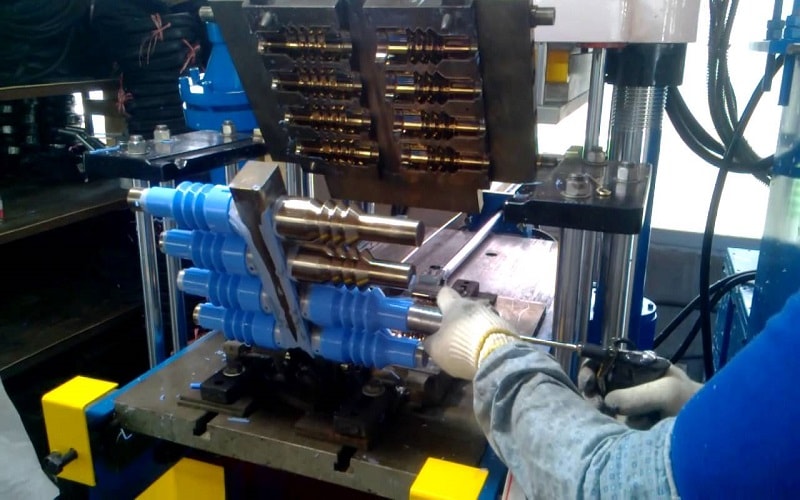
Summary
Silicone injection molding, with its intricate process and versatile applications, offers numerous advantages that make it an indispensable manufacturing technique. From reduced cycle times and high precision to minimal waste, the benefits are clear and impactful.
By understanding the nuances of material preparation, injection, curing, and demolding, manufacturers can achieve exceptional results. Liquid silicone rubber’s unique properties open up a world of possibilities across industries, including medical, automotive, and consumer products.
Embracing these techniques ensures not only the success of molded components but also the advancement of innovative solutions in various fields.
Frequently Asked Questions
What are the main phases of the silicone injection molding process?
The main phases of the silicone injection molding process are material preparation, injection phase, curing process, and demolding. Each phase is essential for achieving high-quality and precise final products.
Why is liquid silicone rubber preferred for injection molding?
Liquid silicone rubber is preferred for injection molding because its low viscosity enables the creation of intricate parts while ensuring high precision and tight tolerances.
This material also exhibits excellent performance characteristics, making it ideal for various applications.
What are some key applications of silicone molded parts?
Silicone molded parts are prominently used in medical devices, automotive components, and consumer products due to their flexibility, durability, and resistance to extreme conditions. These properties make them a preferred choice in various industries.
How does silicone injection molding minimize waste?
Silicone injection molding minimizes waste by utilizing a cold runner system, which significantly reduces excess material and promotes cost savings.
This approach not only enhances economic efficiency but also supports eco-friendliness in the production process.
What are the critical design considerations for silicone injection molding?
The critical design considerations for silicone injection molding involve maintaining uniform wall thickness, ensuring adequate draft angles, and avoiding undercuts to prevent defects and enhance production efficiency. Addressing these factors is essential for a successful molding process.