In injection molding, SPI surface finishes ensure high-quality and consistent parts. This article explains SPI surface finishes, their importance, and how to choose the right SPI surface finish for your project.
Understanding SPI Surface Finish Standards
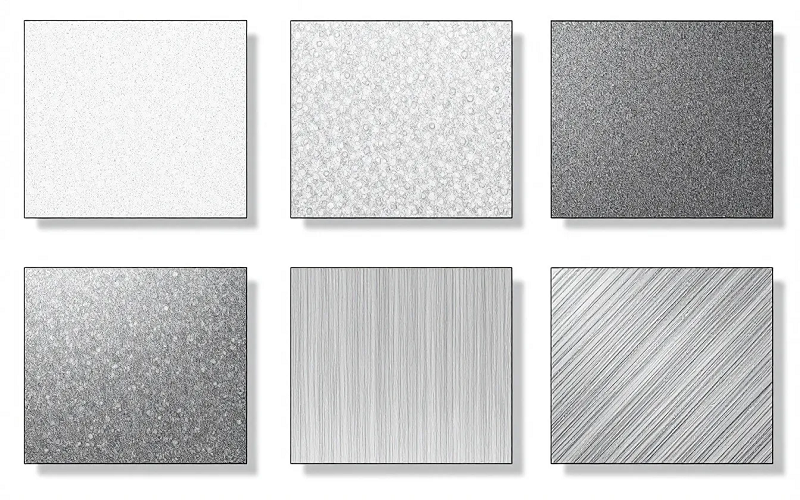
In the world of injection molding, the injection molding surface finishes of your mold is paramount. Improving the mold surface finish directly enhances the final appearance and functionality of the molded products.
Surface finishes impact not only the aesthetic quality but also lead to better visual and functional outcomes in injection molded parts. This is where the Society of the Plastics Industry (SPI) surface finish standards come into play.
The SPI guidelines offer a standardized method for describing the surface finish of injection molded plastic components. Established by the Society of the Plastics Industry, these standards create a common language for surface finishes, ensuring consistent quality and reliability in the appearance of injection molded parts. The twelve SPI finishes range from polished to coarse, encapsulating different levels of texture and finish.
Compliance with SPI standards is crucial for manufacturers, as it ensures that the parts meet specific visual and functional requirements. Following these guidelines ensures a high level of surface quality, free from visible machining marks and surface imperfections, critical for both aesthetic and practical applications.
The Twelve Grades of SPI Surface Finishes
The SPI surface finishes are divided into twelve distinct grades, ranging from A1 to D3, each representing different levels of smoothness and texture. These grades help manufacturers select the appropriate finish based on the desired outcome for the final product. For instance, the SPI A1 grade, known for its super high gloss, has a typical surface roughness average (RA) of 0.012 to 0.025 micrometers, with a surface roughness ra μm that makes it ideal for optically clear components, including vdi surface finishes.
Lower SPI numbers indicate less deviation from a perfect finish, allowing for smoother surfaces. Grades A and B are known as the smoothest available finishes within the SPI standard. On the other end of the spectrum, SPI grades D1 to D3 provide rough textured finishes, with D3 being the roughest, ranging from 3.20 to 18.0 micrometers in roughness average.
Grasping these grades helps in selecting the appropriate surface finish for your injection molded parts. Whether you need a high polish for aesthetic purposes or a textured finish for enhanced grip, the SPI grades provide a clear framework for achieving the desired surface quality.
Glossy Finishes: High Polish for Visual Appeal
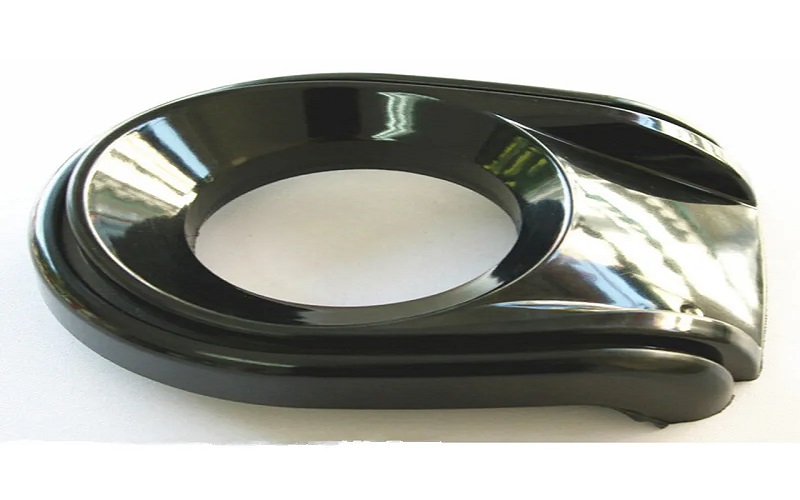
Glossy finishes are the epitome of visual appeal, characterized by their shiny and reflective surfaces. These finishes are often utilized in products like mirrors, clear packaging, and other items where aesthetics are paramount. The SPI grades A1, A2, and A3 fall within this category, with A1 being the highest gloss suitable for optically clear components.
Materials such as ABS and Polycarbonate typically yield better results with high gloss finishes due to their inherent properties. Various finishing techniques, including polishing and coating, can enhance the surface quality, achieving the desired aesthetic and functional attributes. For instance, using ultra-fine diamond paste as a final polish can significantly enhance the visual quality of molded parts.
These high-polish finishes require more polishing and meticulous attention to detail, but the result is a striking, high-gloss surface that stands out in the market. Whether for consumer electronics or luxury items, the visual appeal of glossy finishes can set your product apart.
Semi-Glossy Finishes: Balancing Shine and Function
Semi-glossy finishes strike a balance between shine and functionality, making them a popular choice for a variety of applications. The SPI grades B1 to B3 represent semi-gloss finishes, with B1 being the finest and B3 having a normal semi-gloss appearance. These finishes offer a moderate level of shine without being overly reflective, making them suitable for both aesthetic and practical uses.
The finishing method for SPI semi-glossy surfaces involves using specific grades of sandpaper. For example, B-1 finishes use 600 grit, B-2 uses 400 grit, and B-3 uses 320 grit. This method ensures a consistent and controlled surface texture that meets the desired level of shine through surface finishing.
In industrial applications, semi-glossy finishes are often utilized for parts where aesthetic appeal is secondary to functionality. This makes them popular in automotive and household items, where a moderate shine is sufficient to enhance the product’s appeal without compromising its practicality.
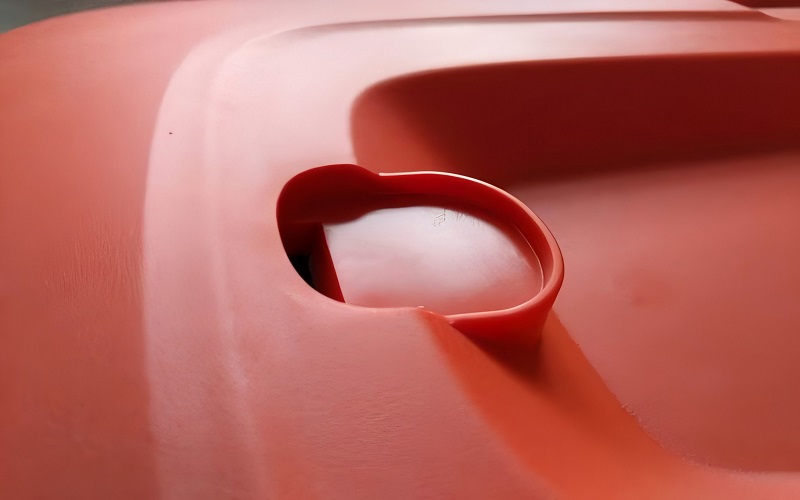
Matte Finishes: Practical and Subdued
Matte finishes are known for their practical and subdued appearance, making them ideal for products that require a non-glossy look. Categorized under SPI grades C1 to C3, these finishes provide different levels of surface roughness, with C1 offering the finest normal matte finish, often achieved through processes like electrical discharge machining for precise texturing. Matte finishes minimize light reflection, giving products a dull and muted appearance.
These finishes are particularly favorable for consumer goods, such as injection molded keyboards and laptop frames, where a practical, non-reflective surface is desirable. The matte texture helps conceal fingerprints effectively, which is beneficial for frequently handled items like gadgets and tools.
Choosing the right matte finish helps manufacturers balance functionality and aesthetics, keeping the product appealing and practical for everyday use.
Textured Finishes: Enhancing Grip and Aesthetics
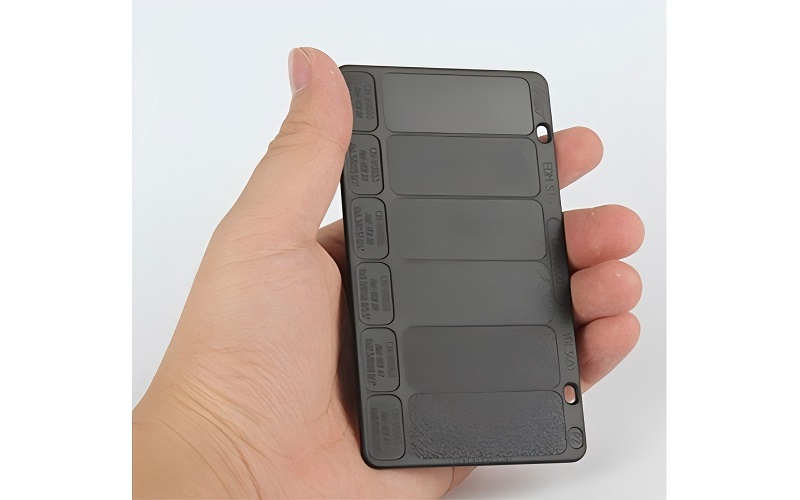
Textured finishes are designed to enhance both grip and visual appeal, making them suitable for specific applications. Represented by SPI grades D1 to D3, these finishes range from satin textured (D1) to rough textured (D3). The rough texture of SPI D-3 finishes can effectively conceal surface textures and minor scratches.
Textured finishes improve the grip of products, making them easier to handle. This is particularly advantageous in applications where user interaction is frequent, such as tools or automotive parts. SPI D-2 finishes, for example, are produced through dry blasting with specific oxide materials, creating a dull texture that enhances grip.
Incorporating textured finishes allows manufacturers to produce items that are both visually appealing and practical, offering improved handling and durability.
Choosing the Right SPI Finish for Your Material
Selecting the right spi mold finishes for your material is crucial, as different injection molding materials yield varying results when paired with specific SPI finishes. The type of material determines the results from polished or textured molds, impacting the overall appearance and functionality of the product. For instance, materials like ABS and Polycarbonate are more compatible with high gloss finishes.
Each SPI finish grade is designed for specific applications, ranging from aesthetic demands to functional requirements. The choice of SPI finish directly influences the final appearance and functionality of injection molded components, ensuring that the part meets both functional and aesthetic requirements.
Recognizing how processing conditions and material properties interact is key to optimizing surface quality in molded parts. Environmental conditions during molding, such as temperature and humidity, can also impact the surface quality of the finished product.
Cost Implications of SPI Surface Finishes
The choice of surface finish for injection molds can significantly impact production costs, with more complex finishes being pricier. Polishing time increases with the complexity of the injection mold finish, leading to higher production costs. For instance, achieving a high-polish finish like SPI A1 requires meticulous polishing, which can be time-consuming and expensive.
The intricacy of the mold design also affects the cost, as more complex molds require additional finishing time and resources. Production volume can influence the unit cost of the molded parts, with higher volumes typically lowering the per-unit cost due to economies of scale.
Ultimately, the overall expense of injection molded parts is influenced by the chosen SPI finish grade, with higher grades necessitating more extensive polishing and processing. Knowing these cost implications helps manufacturers make informed decisions that balance quality and budget.
Achieving Optimal Surface Quality
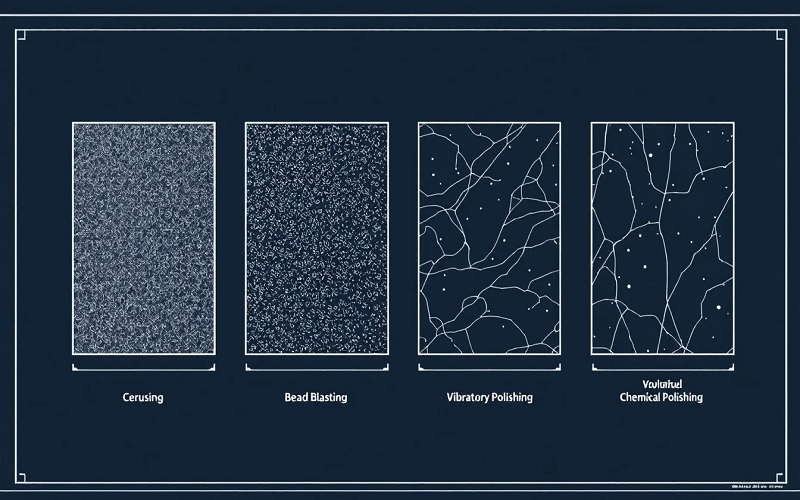
Achieving optimal surface quality starts with choosing the right material with suitable flow characteristics, as this influences the surface finish and overall quality of the injection molded part. Proper maintenance of molds, including regular cleaning and inspection, is essential to prevent defects and maintain the desired surface quality over time during the injection molding process.
Periodic inspection of mold surfaces during polishing helps identify and rectify imperfections for a better finish. Techniques such as sanding and using diamond pastes can significantly improve the overall quality and visual appeal of semi-glossy and glossy surfaces.
Injection molded acrylic is recognized for delivering superior surface quality in glossy finishes. Using these techniques and maintaining high standards ensures plastic injection molded parts and molded plastic parts meet the highest levels of surface quality, free from visible machining marks and imperfections.
Expert Tips for Mold Polishing and Texturing
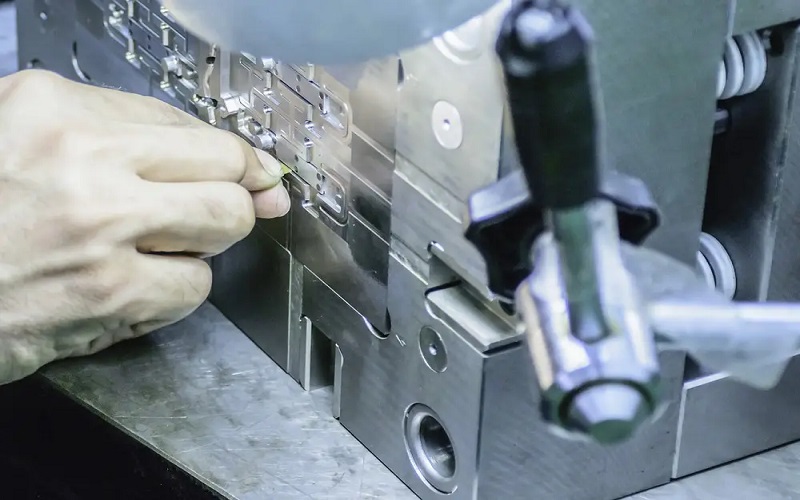
Polishing and texturing molds require a combination of skills and techniques to achieve the desired surface finish. Common finishing techniques include dry blasting, grit paper, stone abrasive, and diamond abrasive, used for achieving specific SPI surface finishes. Mechanical polishing, which uses tools like rotary machines, is efficient for larger molds and ensures a consistent finish.
Chemical polishing aims at smoothing complex mold surfaces using specific chemicals rather than mechanical action, while electropolishing utilizes an electrolytic process for high-quality finishes. Laser polishing employs concentrated laser energy to refine mold surfaces, achieving high-quality finishes even in intricate areas. Abrasive flow polishing uses a fluid medium with abrasive particles for complex shapes.
Using small rotary polishers or ultrasonic devices can enhance precision when working on intricate mold features. By employing these expert techniques, manufacturers can achieve the desired surface quality and functionality for their injection molded parts.
Summary
Choosing the right SPI surface finish for your injection molded parts is vital for achieving the desired aesthetic and functional outcomes. From glossy finishes that offer high visual appeal to practical matte and textured finishes that enhance functionality, each SPI grade serves a specific purpose.
Understanding the impact of material compatibility, cost implications, and maintenance techniques is crucial for making informed decisions.
By following the guidelines and expert tips provided, you can ensure that your injection molded parts meet the highest standards of quality and performance. Whether you’re producing consumer electronics, automotive components, or household items, the right surface finish can set your product apart in the market.
Frequently Asked Questions
What is the SPI surface finish?
The SPI surface finish is a standardized method for detailing the surface finish of injection molded plastic components, as defined by the Society of the Plastics Industry. This classification helps in ensuring consistency and quality in plastic manufacturing processes.
How many grades of SPI finishes are there?
There are twelve grades of SPI finishes, classified from A1 (super high gloss) to D3 (rough textured finish).
What materials are best suited for high gloss finishes?
For high gloss finishes, materials like ABS and Polycarbonate are best suited due to their inherent properties that enhance finish quality. Consider these materials for achieving a superior gloss effect.
How do SPI finishes impact production costs?
SPI finishes significantly impact production costs, as more intricate finishes like high-polish require additional polishing time and resources, increasing expenses. Therefore, choosing simpler finishes can help control costs effectively.
What techniques are used for mold polishing?
Mold polishing techniques encompass mechanical polishing, chemical polishing, electropolishing, laser polishing, and abrasive flow polishing. Each method offers unique benefits for achieving a smooth, high-quality finish.