Thermoplastic elastomer injection molding combines easy processing with flexibility. This guide discusses its benefits, challenges, design tips, and advanced techniques for producing high-quality parts.
Advantages of Thermoplastic Elastomer Injection Molding
Thermoplastic elastomers (TPEs) and thermoplastics offer unmatched versatility, allowing for flexible customization to suit a plethora of applications and environments, including flexible pvc solutions. This adaptability, derived from carefully selected raw materials, has cemented TPEs as a cornerstone in various plastic polymer industries, driving steady market growth.
One of the most significant benefits of TPE materials is their consistency. Unlike other materials that require extensive compounding, TPEs maintain consistent elastic properties across different batches, ensuring uniformity and reducing the risk of variability in end products. This consistency translates into faster processing and shorter fabrication times, which ultimately lead to reduced production costs.
Moreover, TPEs can be processed at high temperatures, making them ideal for both injection molding and extrusion processes. This high-temperature resistance, combined with their abrasion resistance, allows for the creation of intricate and durable parts. Additionally, TPEs offer a wide range of color matching and clarity options, which is particularly beneficial for applications such as medical tubing where both aesthetics and rubber like properties are crucial.
In essence, the advantages of TPE injection molding lie in its cost-effectiveness, processing efficiency, and the ability to produce high-quality, customizable parts.
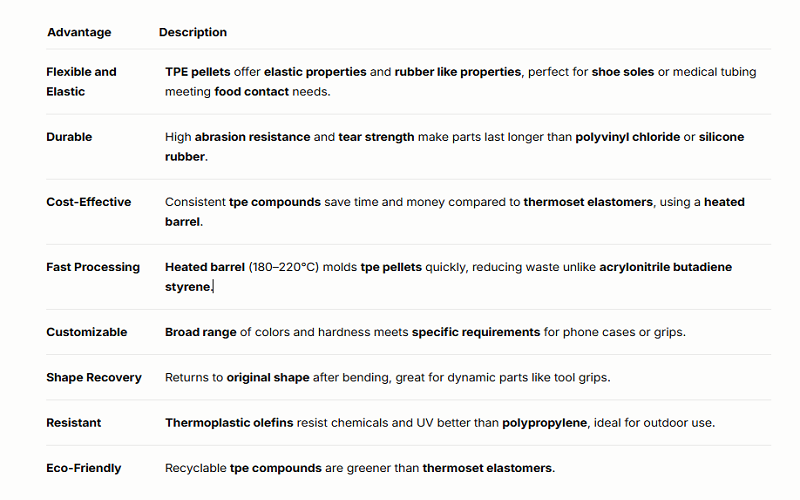
Challenges in Thermoplastic Elastomer Injection Molding
Despite the numerous advantages, TPE injection molding comes with its own set of challenges. One significant hurdle is achieving high heat resistance, particularly for components used in demanding environments such as under the hood of cars and trucks, where materials like silicone rubber may sometimes be considered for comparison. The temperature resistance of TPE materials, including thermoplastic olefins, is influenced by high temperature applications, stress duration and type, as well as the part’s shape, which can be affected by heated conditions.
Another challenge is dealing with uneven shrinkage, which can affect the molding process, part removal, appearance, fit, and finished part, particularly when tear strength is critical for durability. Mitigating this requires designing the part to accommodate potential shrinkage during the cooling phase, ensuring dimensional accuracy, unlike some thermoset elastomers that have different curing behaviors.
Addressing these challenges requires a deep understanding of material properties and precise control over the injection molding process. Careful management of these factors allows manufacturers to overcome obstacles and produce high-quality TPE parts.
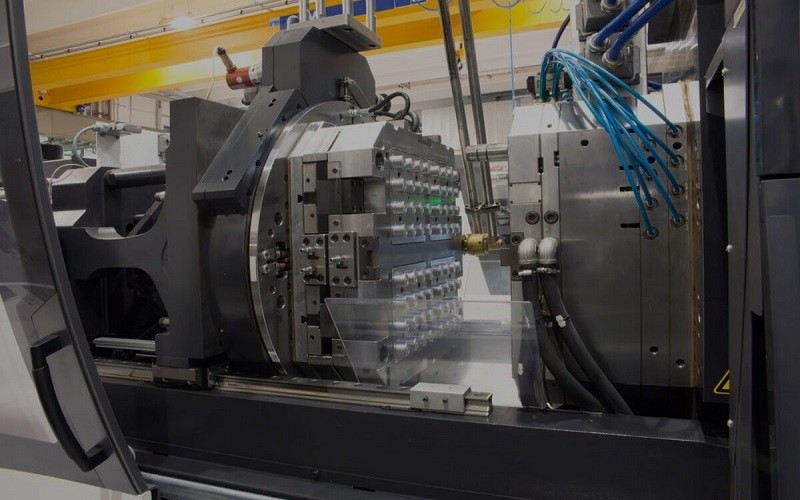
Key Design Guidelines for TPE Injection Molding
Designing for TPE injection molding demands careful consideration of several factors to ensure high-quality parts. Proper mold venting and sprue design, supported by a precisely controlled heated barrel, facilitate the smooth flow of TPE material into the mold cavity. This helps in reducing defects and achieving the desired shape across a broad range of applications.
Shrinkage during the cooling phase is another critical aspect to consider. Accounting for this shrinkage is necessary to maintain the dimensional accuracy of the molded parts, especially when compared to materials like polyvinyl chloride. Additionally, understanding the elongation at break value is crucial, as it indicates how much the TPE can be stretched before it fails.
The tensile modulus of TPEs, which measures their stiffness, is another important factor, distinguishing them from rigid plastics like acrylonitrile butadiene styrene. High breaking strength signifies the material’s ability to withstand significant stretching without breaking, making it suitable for various applications.
Detailed planning and adherence to guidelines are crucial for achieving high-quality TPE parts. Two-component (2K) processing, which combines different materials or colors in a single step, can further enhance design flexibility and product functionality.
Processing Techniques for TPE Injection Molding
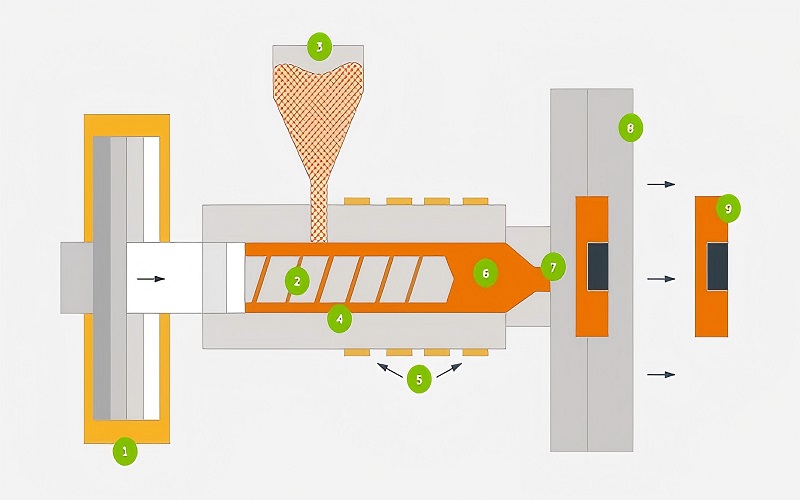
The primary technique for processing TPE material is injection molding, where TPE is melted and injected into a mold cavity under high pressure. Keeping the runner temperature, typically between 170°C and 240°C, at the right level is crucial for optimal results. Different TPE grades require varying settings for cylinder and mold temperatures, often between 15°C and 60°C, including considerations for the melting point.
Standard equipment can be used for TPE injection molding, typically requiring clamp forces between 2.0 to 3.0 tons per square inch of surface area. Hot runner systems enhance the efficiency of TPE injection molding by minimizing material waste.
The cooling phase is a critical step in the process, allowing the molten TPE to solidify before being removed from the mold. Properly designed ejector mechanisms prevent damage to the parts during ejection.
Selecting the Right TPE Material for Your Application
Choosing the right TPE material involves considering several mechanical properties such as hardness and tensile strength to meet specific performance requirements, including suitability for food contact applications. The hardness of a thermoplastic elastomer is measured using the Shore scale, with common scales including Shore A, Shore D, and Shore C.
TPEs are known for their excellent chemical resistance and can be formulated to be flame resistant, making them ideal for products like shoe soles. Additionally, TPE materials are eco-friendly, often made from recyclable and non-toxic plastics that retain their original shape after deformation. Other properties to consider include UV stability and electrical properties, as well as tpe pellets used in compounding.
Cost is another critical factor, as high-performance TPEs can be more expensive, impacting the overall project budget. Visual and tactile characteristics, such as surface texture and gloss level, also play a significant role in consumer preferences.
The manufacturing process can be tailored to specific methods, influencing processing speed and production quality. Careful selection of the right tpe pellets ensures the success of applications.
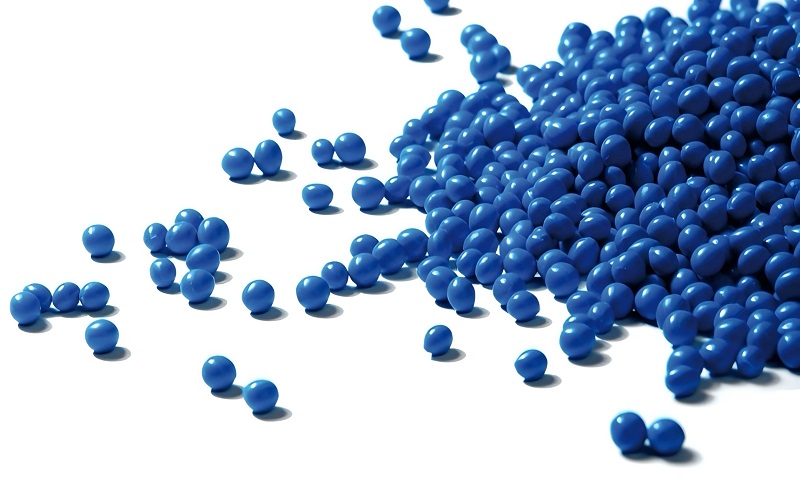
Enhancing Performance of TPE Molded Parts
Enhancing the performance of TPE molded parts is crucial for ensuring their quality and durability. Aging can result in reduced mechanical properties and a degraded appearance due to environmental exposure. Adding specific stabilizers or additives can enhance UV resistance, improving durability against sunlight exposure and contributing to material stability, structure, and styrenic block copolymers.
Compression set tests are essential for determining the resilience of TPEs, measuring their ability to return to their original thickness after being compressed. A low compression set indicates better suitability for sealing applications.
Stress cracking, which leads to brittleness, can be managed by carefully controlling material temperature and injection conditions. Focusing on these aspects improves the performance and lifespan of TPE molded parts.
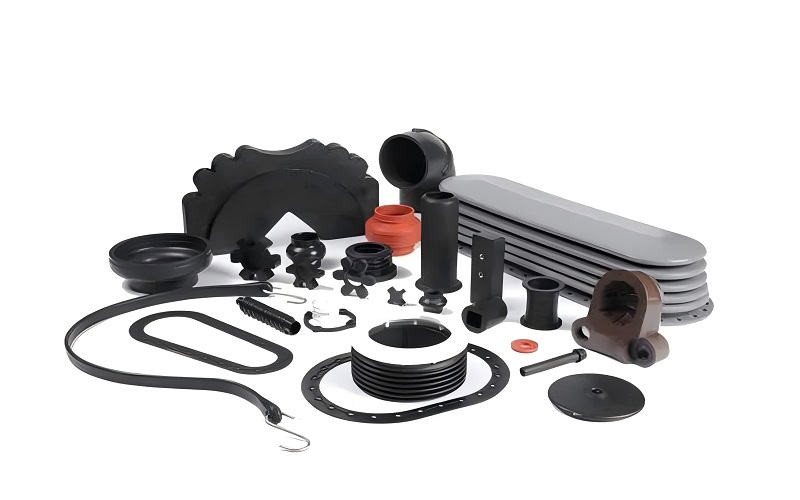
Common Applications of TPE Injection Molding
TPEs are extensively used in various industries due to their unique properties. In the medical sector, TPEs are commonly used for tubing and grips, thanks to their biocompatibility and flexibility in medical devices, meeting specific requirements for safety and performance.
The automotive sector relies heavily on TPEs for components such as door seals and bumpers due to their durability and flexibility, often outperforming materials like polypropylene in elasticity. TPEs are also popular in consumer products like power tools, where they enhance grip and comfort through shock-absorbing features.
In the electronics industry, tpe compounds are used for phone cases and connectors, benefiting from their impact resistance and insulating properties. The intended use environment, whether indoor or outdoor applications, influences the required material characteristics, including UV exposure and temperature resilience.
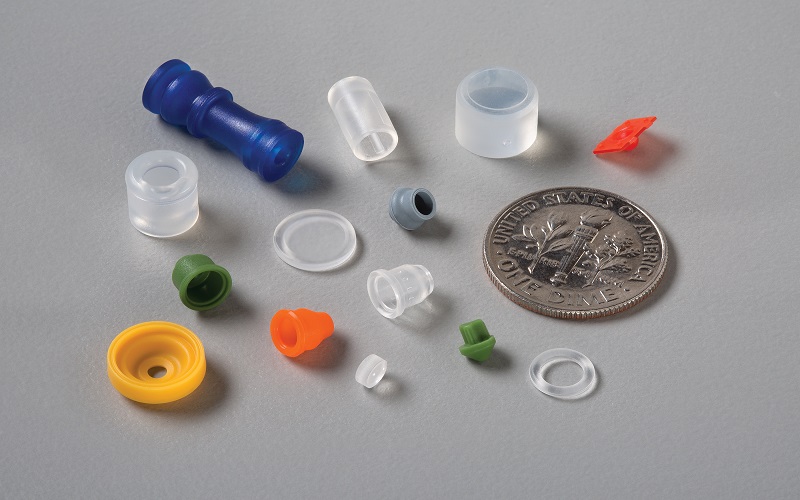
Advanced TPE Molding Techniques
Advanced techniques in TPE molding can further enhance the efficiency and quality of the produced parts. Extrusion blow molding allows for the creation of complex hollow parts, such as bottles, by blowing air into extruded TPE material within a mold.
Melt calendering is another technique that shapes TPEs into films or sheets by passing them through rollers, allowing for precise thickness control, surface finishes, and a soft touch that won’t tear.
The extrusion process offers a very good surface finish and a high degree of design freedom, making it a valuable technique for producing high-quality TPE parts.
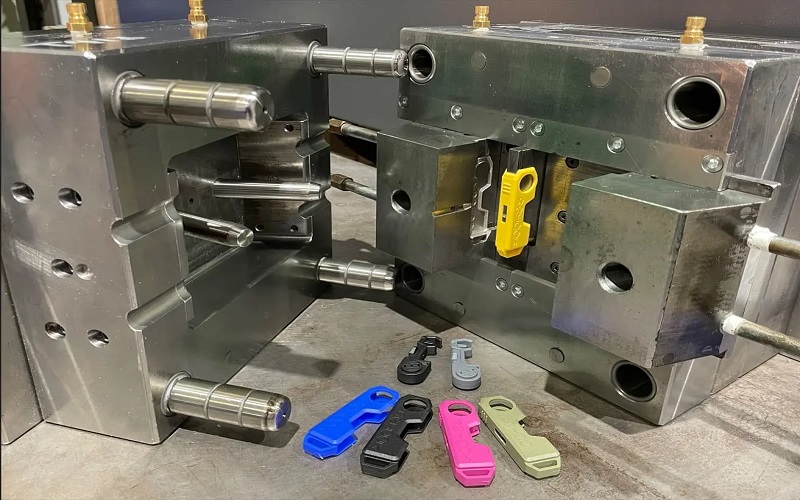
Summary
Mastering thermoplastic elastomer injection molding involves understanding its advantages, overcoming challenges, and adhering to key design and processing guidelines.
By selecting the right materials and employing advanced techniques, manufacturers can enhance the performance and quality of their TPE molded parts.
Embrace these insights to innovate and excel in your production processes, ensuring your products stand out in the market.
Frequently Asked Questions
What are the primary advantages of TPE injection molding?
The primary advantages of TPE injection molding include its versatility, cost-effectiveness, high-temperature resistance, and consistent material properties, ensuring it is suitable for a wide range of applications.
What challenges are commonly faced in TPE injection molding?
Achieving high heat resistance and managing uneven shrinkage are significant challenges in TPE injection molding that can affect dimensional accuracy during the cooling phase. Addressing these issues is crucial for producing high-quality components.
How can I select the right TPE material for my application?
To select the appropriate TPE material for your application, evaluate critical factors such as mechanical properties, chemical resistance, cost, and specific performance requirements. This comprehensive assessment will ensure that you meet the necessary performance standards for your project.
What techniques can enhance the performance of TPE molded parts?
To enhance the performance of TPE molded parts, focus on improving UV resistance, conducting compression set tests, managing stress cracking, and incorporating stabilizers or additives into the TPE material. These steps can significantly elevate the durability and functionality of your parts.
What are some common applications of TPE injection molding?
TPE injection molding is widely utilized in medical devices, automotive components, consumer products, and electronics, thanks to the material’s flexibility, durability, and impact resistance. This versatility makes TPE an ideal choice across various industries.