Are you trying to choose between thermoplastic vs thermoset materials? Understanding the difference is crucial because each has specific properties and applications.
In this guide, we’ll break down their characteristics, uses, and the main differences to help you make an informed decision.
Understanding Thermoplastics and Thermosets
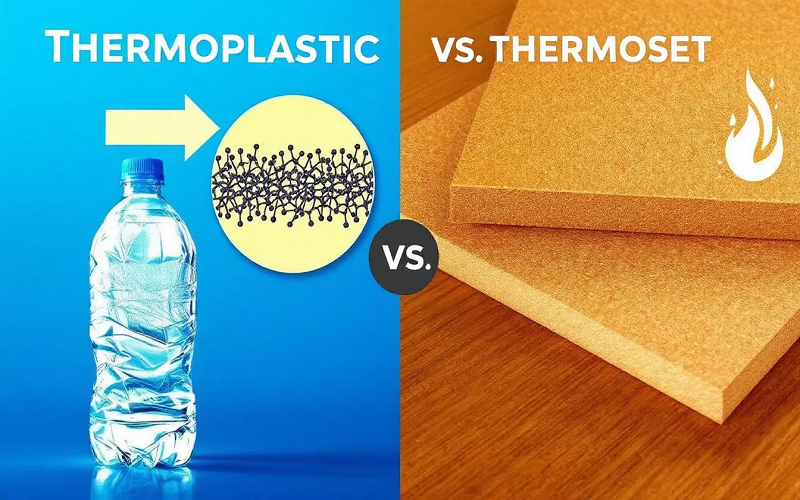
Thermoplastics and thermosetting plastics are two distinct classes of plastic materials, each with unique properties and applications. Thermoplastic materials are versatile and can be reheated, reshaped, and recycled multiple times without undergoing any permanent chemical changes. This makes them ideal for applications where flexibility and recyclability are essential.
On the other hand, thermosetting plastics, or thermosets, undergo a chemical reaction during the curing process that creates permanent bonds, making them rigid and unable to be reshaped or recycled once set. This irreversible hardening process gives thermosets enhanced durability and heat resistance, making them suitable for applications that require high-performance materials.
Characteristics of Thermoplastics
Thermoplastic materials are known for their ability to be easily recycled by reheating and forming them into new shapes. They begin to soften at high temperatures and eventually melt above their glass transition temperature, allowing for easy processing and reshaping.
Thermoplastic polymers’ versatility and suitability for various applications stem from this property. They also resist chemicals and detergents, further expanding their range of uses. Common examples of thermoplastics are polyester, polyethylene terephthalate, and polypropylene. Other examples include polystyrene, Teflon, and acrylic.
Thermoplastics are also characterized by their good electrical insulation properties and high impact and corrosion resistance. These materials can be reshaped and recycled, making them environmentally friendly and cost-effective. Their lower tensile strength compared to thermosetting plastics can limit their use in high-stress applications.
Despite this, their ease of processing and repairability make thermoplastics a popular choice for many industries.
Characteristics of Thermosets
Thermosetting plastics maintain their shape and structural integrity even at high temperatures. This is due to the irreversible hardening process they undergo during curing, which involves forming permanent chemical bonds that cannot return to a liquid state upon reheating. This makes thermosets ideal for applications requiring high temperatures and mechanical stress.
Thermosetting plastics offer unique advantages: flame resistance, chemical resistance, toughness, and elasticity. Phenolic resin, silicone, polyurethane, and epoxy resins are common examples of thermoset materials. These materials find use in various applications.
These materials are often used in applications where durability and stability are critical, such as in electronics, heavy machinery, and chemical processing equipment. Once set, thermosets cannot be recycled or remolded, which can limit their use.
Key Differences Between Thermoplastics and Thermosets
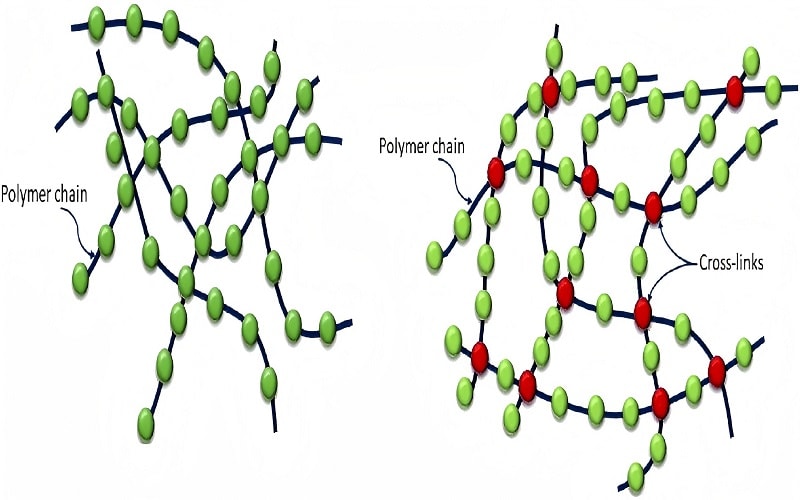
The key difference between thermoplastic and thermosetting plastic lies in their chemical structure and heat behavior. Thermoplastics are synthesized through an addition polymerization process, which allows them to be heated, reshaped, and cooled multiple times without undergoing permanent chemical changes. This property is ideal for applications requiring flexibility and recyclability.
In contrast, thermosetting plastics rely on condensation polymerization, which creates permanent chemical bonds that prevent them from being reshaped once cured. This process enhances thermosets’ durability and heat resistance, suiting them for high-performance applications.
The distinct material properties of thermoplastics and thermosets influence their applications, with thermoplastics being more flexible and moldable, while thermosets offer greater durability and thermal stability.
Melting and Curing Process
Thermoplastics soften when heated, allowing easy shaping and molding into various forms. This makes them suitable for manufacturing processes like injection molding, blow molding, and extrusion. Heated thermoplastics melt and can be injected into molds to create complex shapes quickly and efficiently.
Thermosetting plastics undergo a curing process forming permanent chemical bonds, making remelting impossible once set. The curing process of thermosets forms irreversible bonds, ensuring the material maintains its shape and properties even under high temperatures.
Specialized methods like reaction injection molding (RIM) process thermosets, allowing them to cure within the mold and achieve final properties.
Physical Properties
Thermoplastics and thermosets possess distinct physical properties influencing their applications. Thermosetting plastics achieve high tensile strength and melting points due to their cross-linked molecular structure, ideal for high-performance applications.
They are known for their exceptional thermal stability under high temperatures, which ensures they maintain their structural integrity in demanding environments.
Thermoplastics may not provide the same level of structural integrity as thermosetting plastics. While offering flexibility and ease of processing, thermoplastics generally have lower tensile strength and may not perform as well under high temperatures.
Notable differences include thermal stability, tensile strength, and dimensional stability, critical factors in selecting the appropriate material for specific applications.
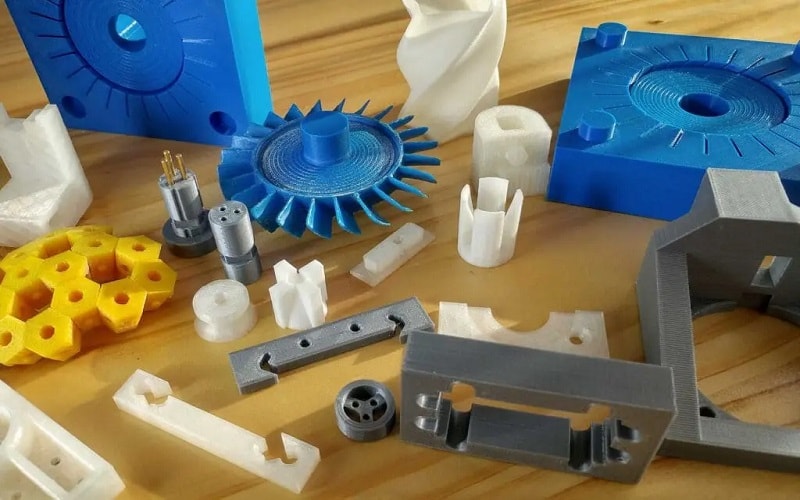
Recyclability and Environmental Impact
Thermoplastics can be reshaped and remolded multiple times without permanent chemical changes, making them recyclable. This makes them environmentally friendly and cost-effective, as they can be recycled through remelting, grinding into granules, or mixing with virgin resin. Recycling thermoplastics reduces waste and minimizes environmental impact.
Thermosetting materials cannot be remolded or recycled once set due to their irreversible chemical structure. This lack of recyclability can be a significant limitation, especially where environmental considerations are critical. While thermosetting materials offer superior durability and heat resistance, their inability to be recycled makes them less environmentally friendly compared to thermoplastics.
Manufacturing Processes for Thermoplastics and Thermosets
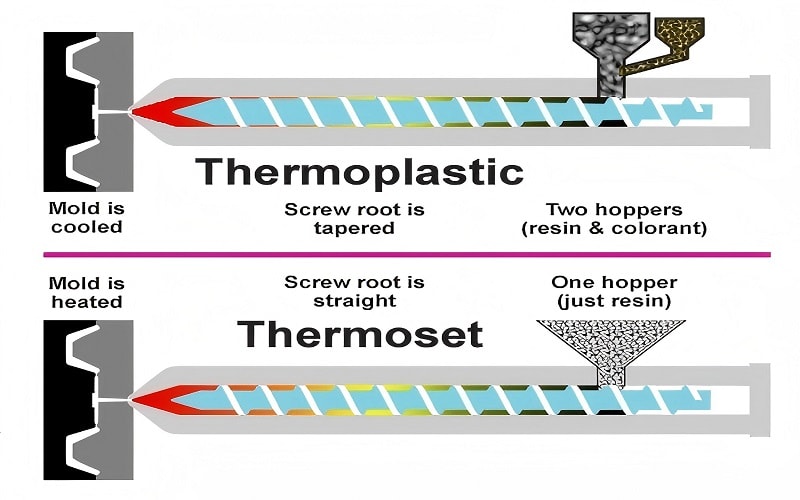
Thermoplastics and thermosets undergo different manufacturing processes tailored to their unique properties. Thermoplastics can be processed using techniques such as injection molding, blow molding, extrusion, and thermoforming. These methods efficiently produce complex shapes and components, making thermoplastics highly versatile for various applications.
Thermosetting polymers are typically fabricated using techniques like reaction injection molding and resin transfer molding. These methods involve heating and mixing polymers, followed by molding and curing to achieve the final product. The curing process ensures thermosets maintain their structural integrity and properties, suiting them for high-performance applications requiring durability and heat resistance.
Injection Molding Process
Injection molding is a key method for manufacturing both thermoplastics and thermosets, allowing efficient production of complex shapes. For thermoplastics, the process involves melting the material, injecting it into a mold, and cooling it quickly to create the final product. This method is widely used for producing plastic parts like automotive components, consumer goods, and packaging materials.
In thermoset injection molding, cold material is injected into a hot mold, where it chemically cures and hardens, making remelting impossible afterward. This process grants thermosets heat resistance and durability, suiting them for applications like electrical components and disc brake pistons.
While thermoplastics are remoldable and processed more easily, thermosets provide enhanced performance for high-stress applications, highlighting the differences in thermoset vs thermoplastic materials.
Other Molding Techniques
Blow molding manufactures thermoplastic products, particularly hollow items like bottles and containers. The process involves inflating heated plastic within a mold, allowing it to take shape and cool. This technique efficiently produces large volumes of uniform products, making it popular in the packaging industry.
Reaction injection molding (RIM) is popular for creating thermosetting plastics. This process includes heating and mixing polymers, followed by molding and curing to achieve the final product. RIM allows the production of complex geometric shapes and high-performance components, suiting it for automotive and aerospace applications.
Applications and Uses in Industry
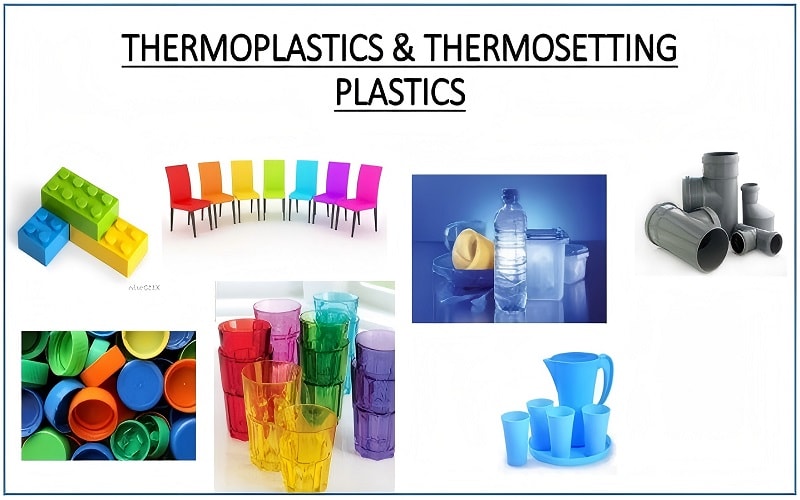
Both thermoplastics and thermosets have unique properties suiting different applications. Understanding these properties helps select the right material for specific industry needs.
Thermoplastics suit flexible and recyclable applications, while thermosets are favored for durability and heat resistance in high-performance environments.
Thermoplastic Applications
Thermoplastics commonly manufacture plastic bags and packaging materials due to their ease of processing and recyclability. Their versatility extends to medical device production, where their ability to be easily shaped and sterilized is highly valued. Thermoplastics are also found in heavy appliances, showcasing their capability to endure demanding conditions.
The blow molding process commonly makes hollow plastic items like bottles and containers. This technique efficiently produces uniform products, making thermoplastics a popular choice in packaging.
Their good electrical insulation properties and high impact resistance make them suitable for various consumer goods and industrial applications,including piping systems that require flexibility and resistance to environmental stress.
Thermoset Applications
Thermosets are commonly used in electronics, heavy appliances, machinery, and chemical processing equipment due to their superior structural integrity and stability under harsh conditions.
Motor components and construction machinery are prime examples where thermosetting plastics provide optimal performance. These materials offer strong dimensional stability and are often used in applications requiring durability and heat resistance.
In chemical processing equipment, thermosets are favored for withstanding high temperatures and corrosive environments. Their good electrical insulation properties and resistance to chemical degradation make them ideal for high-performance applications, ensuring long-lasting and reliable performance.
Advantages and Disadvantage
Choosing between thermoplastics and thermosetting plastics involves weighing their advantages and disadvantages. Understanding these pros and cons helps make informed decisions based on specific project requirements and constraints.
Category | Thermoplastics | Thermosets |
Advantage 1 | Recyclable, easy to process | High heat resistance, corrosion-resistant |
Advantage 2 | Cost-effective, impact-resistant | High strength, dimensionally stable |
Advantage 3 | Ideal for pallets, piping systems | Good insulation, suits electronics |
Advantage 4 | Easy to color, modifiable | Durable, chemically resistant |
Disadvantage 1 | Poor heat resistance (>120°C deforms) | Non-recyclable, hard to dispose |
Disadvantage 2 | Limited chemical stability | Complex processing, high cost |
Disadvantage 3 | Lower strength than thermosets | Brittle, low impact resistance |
Disadvantage 4 | UV aging (needs stabilizers) | Low design flexibility (cannot reshape) |
Pros and Cons of Thermoplastics
Before:
Thermoplastics offer several advantages, making them suitable for a wide range of applications. Their resistance to detergents and chemicals, good electrical insulation properties, high impact and corrosion resistance, and recyclability are significant benefits.
These properties make thermoplastic materials versatile and environmentally friendly, as they can be recycled multiple times, reducing waste and production costs. Thermoplastics are easily repaired, allowing for longer product life and less waste.
After:
Thermoplastics offer several advantages, including:
- Resistance to detergents and chemicals
- Good electrical insulation properties
- High impact and corrosion resistance
- Recyclability
These properties make thermoplastic materials versatile and environmentally friendly, as they can be recycled multiple times, reducing waste and production costs. Additionally, thermoplastics are easily repaired, allowing for longer product life and less waste.
However, thermoplastics also have limitations. They tend to be more expensive than thermosetting plastics, especially when higher-grade materials like polyamide-imides are used. Their lower tensile strength compared to thermosetting plastics can be a drawback for applications requiring high mechanical strength. Thermoplastics soften when exposed to heat, which can limit their use in high-temperature environments.
Pros and Cons of Thermosets
Thermosetting plastics have key advantages, including withstanding high temperatures without losing shape. They offer excellent heat resistance, good electrical insulation, corrosion resistance, and dimensional stability, ideal for high-performance applications. Cost-effective tooling and a wide range of finishes and colors enhance thermosets’ appeal in various industries.
However, thermoset plastics also have drawbacks. Once cured, they cannot be recycled or remolded, which can be a significant limitation in terms of environmental impact and material reuse. Additionally, repairing thermosets is challenging, as they cannot be reshaped once set.
Despite these limitations, their high mechanical strength and thermal stability make thermosets a valuable choice for specific applications that require durability and heat resistance.
Cost Considerations
When it comes to cost, thermoplastics are generally priced lower than thermosets, making them a more economical choice for many applications. However, some high-grade thermoplastics can be more expensive than thermosets, depending on the specific material and application.
The inclusion of fillers and additives for cross-linking contributes to the higher cost of thermosets. Therefore, it’s essential to consider the specific requirements and budget constraints of your project when selecting between these two materials.
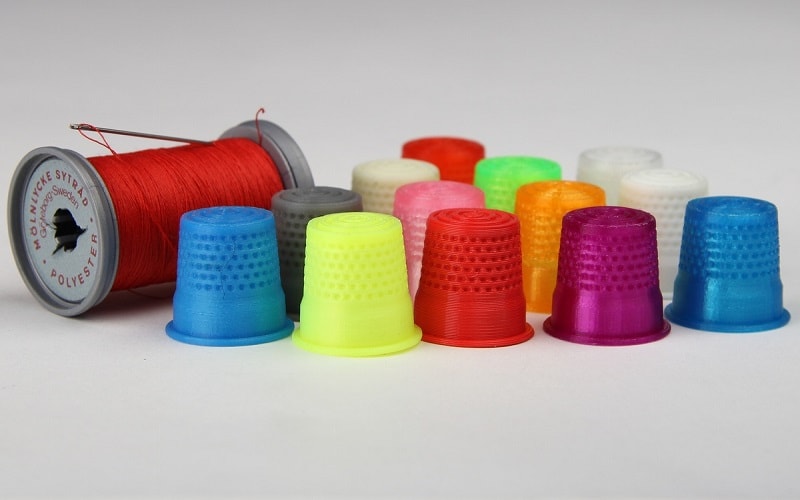
Choosing the Right Material for Your Project
Selecting the right material for your project requires a thorough understanding of the material properties and how they align with your specific needs.
Thermoplastic materials are ideal for applications that require flexibility, recyclability, and ease of processing. They are suitable for products that need to be reshaped or repaired and where environmental considerations are essential.
On the other hand, thermosetting plastics are better suited for applications that demand high mechanical strength, heat resistance, and durability. Projects that involve high temperatures, chemical exposure, and structural integrity can benefit from the superior performance of thermosets.
Understanding the difference between thermoplastic and thermosetting plastic is crucial for making informed decisions that ensure the success and longevity of your products.
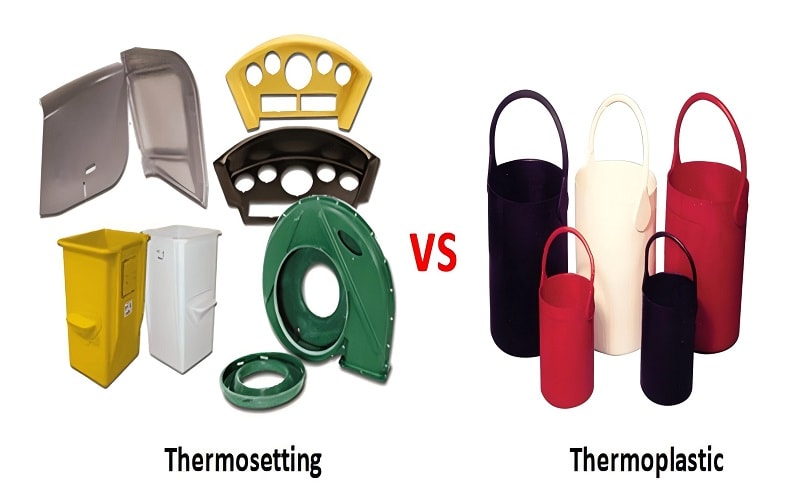
Summary
In conclusion, both thermoplastics and thermosetting plastics offer unique properties that make them suitable for a wide range of applications. Thermoplastics provide flexibility, recyclability, and ease of processing, making them ideal for products that require reshaping and environmental sustainability.
On the other hand, thermosets offer superior heat resistance, mechanical strength, and durability, making them suitable for high-performance applications that demand stability and reliability.
Ultimately, the choice between thermoplastics and thermosets depends on the specific requirements of your project. By understanding the key differences, manufacturing processes, and applications of each material, you can make informed decisions that ensure optimal performance, cost-effectiveness, and environmental sustainability. Choose wisely, and your project will benefit from the strengths of these versatile materials.
Frequently Asked Questions
What are the main differences between thermoplastics and thermosets?
The main difference between thermoplastics and thermosets lies in their properties; thermoplastics can be reheated and reshaped multiple times, whereas thermosets form permanent chemical bonds during curing, resulting in a rigid, non-recyclable material.
Can thermoplastics be used in high-temperature applications?
Thermoplastics are generally not suitable for high-temperature applications due to their tendency to soften under heat. For such environments, thermosets are recommended as they offer superior heat resistance.
What are some common applications of thermoplastics?
Thermoplastics are widely utilized in applications such as packaging materials, medical devices, and heavy appliances, owing to their ease of processing and recyclability. Their versatility makes them an essential material in various industries.
Why can’t thermosets be recycled?
Thermosets cannot be recycled due to their irreversible curing process, which creates permanent chemical bonds that inhibit reshaping or remolding. Consequently, once formed, these materials cannot be reused in their original state.
Which material is more cost-effective for my project?
Thermoplastics are typically more cost-effective, but it’s essential to consider the specific material and application, as high-grade thermoplastics may surpass the cost of thermosets. Evaluate your project’s requirements to make the best choice.