Thin wall injection molding is a manufacturing process used to create parts with thin walls, typically less than 2mm thick.
This method is crucial for reducing material and production costs while ensuring high precision and strength.
In this article, we’ll delve into the design considerations, material selections, and process optimizations essential for successful thin wall injection molding.
Understanding Thin Wall Injection Molding
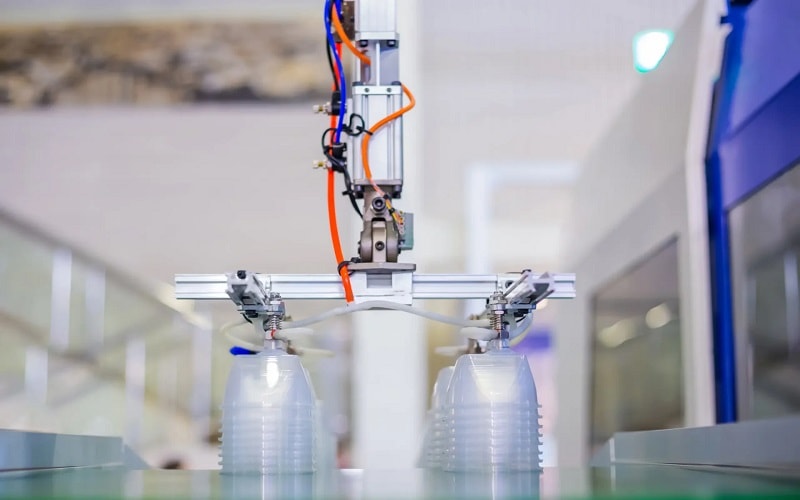
Thin wall injection molding is an advanced form of traditional injection molding where the wall thickness of the parts is typically less than 1mm (0.04 inches) and can go up to 2mm (0.08 inches). This precise technique has gained significant traction due to the rising costs of plastic materials and energy, as well as the market’s demand for quicker delivery times.
But what exactly qualifies as a “thin wall”? Factors like the process-to-wall thickness ratio, plastic viscosity, and heat transfer coefficient play a role.
For instance, in the packaging industry, a thin wall is generally considered to be less than 0.025 inches (0.62mm). This distinction is crucial because the thinner the wall, the more challenging it becomes to maintain the structural integrity of the thinner walls of the thin walled parts and the wall thicknesses of these components.
The thin wall injection molding process involves injecting molten plastic into a mold cavity at high speeds and pressures, which requires highly specialized equipment and techniques. This process differs significantly from traditional methods, where thicker walls allow for more leniency during manufacturing.
These intricacies set the foundation for the design and material selection stages. Each step in the process requires meticulous planning to meet desired specifications without compromising quality or functionality.
Key Materials for Thin Wall Injection Molding
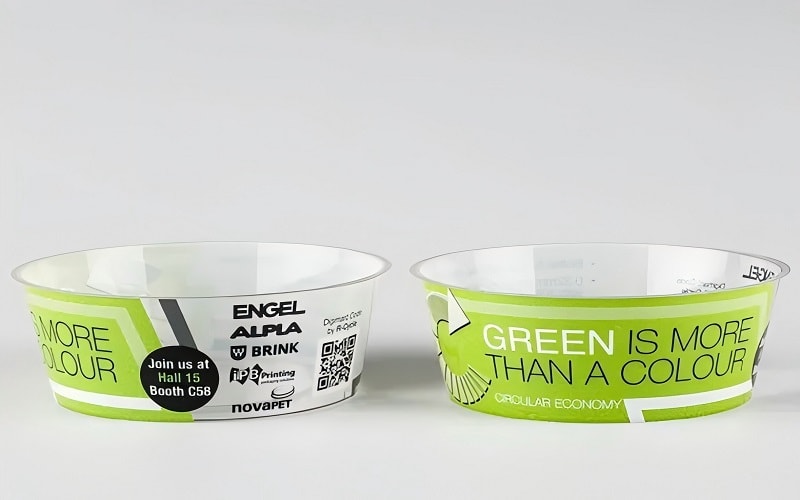
Material selection is crucial in thin wall injection molding. High-density polyethylene (HDPE) and low-density polyethylene (LDPE) are popular for their excellent flow characteristics, ideal for thin wall designs. These materials’ ability to flow easily through narrow sections of the mold ensures that the final product is both sturdy and precise.
Another excellent material for thin wall parts is polypropylene (PP), which is known for its flexibility and is often used in applications requiring living hinges.
Additionally, liquid silicone rubber (LSR) is noted for its exceptional flow properties, making it suitable for thin wall applications despite the potential risk of flash. Polycarbonate, on the other hand, poses challenges due to its tendency to stick, making it difficult to fill thin geometries effectively.
The material choice can make or break the thin wall injection molding process. Polyolefin materials like PP and PE, along with PET, PS, and ABS, are commonly used for their balanced properties. However, some mold material struggle to fill geometries with thin walls, so it’s crucial to consider the part’s geometry and specific application requirements when selecting a material.
Careful material selection ensures the final product meets design specifications while maintaining structural integrity and functionality.
Design Considerations for Thin Wall Parts
When designing thin wall parts, maintaining uniform wall thickness and incorporating structural features are paramount. These factors are crucial for reducing defects and enhancing the structural integrity of the parts.
Let’s delve deeper into these design considerations to understand how they impact the overall quality and durability of thin wall parts.
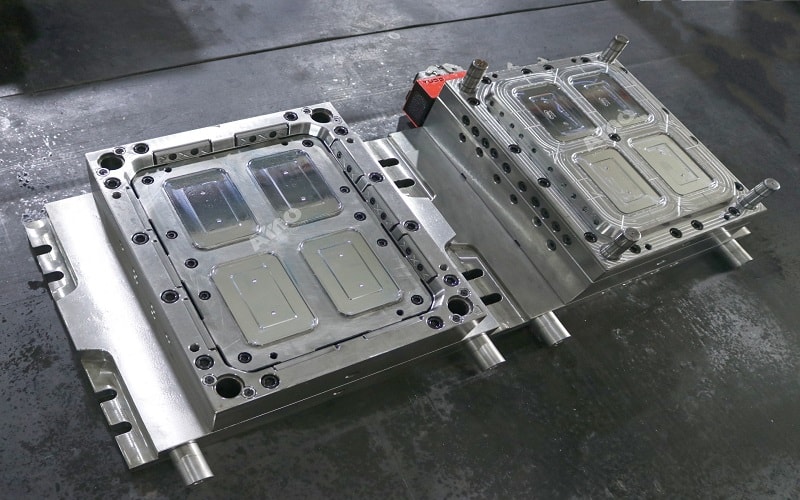
Maintaining Uniform Wall Thickness
Uniform wall thickness is the cornerstone of successful thin wall injection molding. When wall thickness varies, it can lead to cosmetic texture inconsistencies and unformed areas, ultimately compromising the part’s quality. To prevent such issues, it’s essential to keep the wall thickness around 0.9mm or thicker during the injection process. This consistency helps in maintaining the structural integrity and durability of the parts.
Achieving uniform wall thickness requires a well-designed cooling system. Optimized cooling channels ensure even cooling, preventing warping and other defects. Precise machining techniques in mold construction also play a crucial role in maintaining consistent wall thickness across the part.
Additionally, controlling mold plate deformation to below 0.05mm is vital for maintaining wall thickness at 0.5mm. Monitoring the flowable channel thickness during production can help avoid uneven flow paths. This attention to detail in the design and manufacturing process ensures that the final product is free from defects, making it both aesthetically pleasing and functionally robust.
Adding Structural Features
Incorporating structural features such as cross support ribs, gussets, and bosses is essential for enhancing the structural integrity of thin wall parts.
These features help distribute stress more evenly across the part, reducing the likelihood of warping and other structural issues. However, they must be designed carefully to avoid creating warping or sink marks.
For instance, integrating ribs into the design can significantly enhance the part’s strength, but they should be placed strategically to avoid interference with the overall aesthetics and functionality of the part. By adding these structural features, manufacturers can achieve lighter parts without compromising on quality.
Optimizing the Injection Molding Process
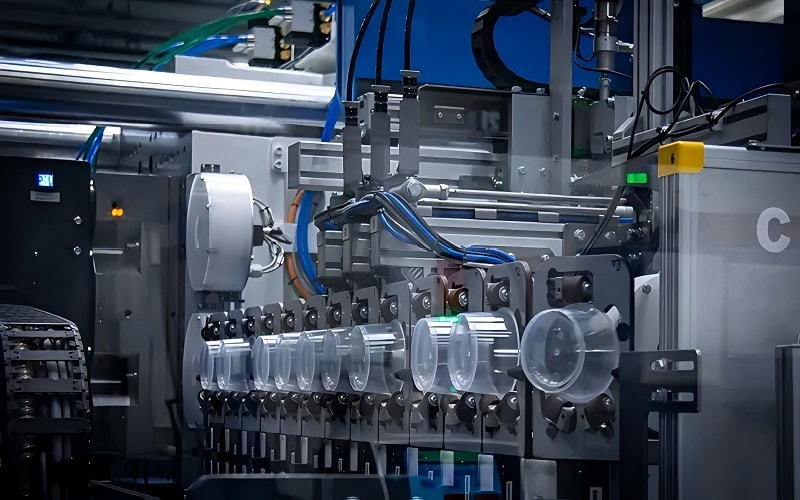
Optimizing the injection molding process is crucial to producing high-quality thin wall parts. This involves fine-tuning various aspects of the process, such as injection speeds and cooling channels, to ensure that the plastic material flows smoothly and cools evenly.
Let’s explore these process optimizations in more detail.
High Injection Speeds
High injection speeds are essential for thin wall molding as they ensure that the plastic fills the mold cavity quickly enough to prevent defects like short shots and weak knit lines.
Typically, high injection speeds of around 400 mm/s are required for thin wall parts. The screw in thin wall injection processes should also reach these speeds to maintain consistency.
Achieving these high speeds relies on high acceleration and deceleration rates. An acceleration rate of more than 8 G is necessary for thin wall injection molding. Round corners and edges in designs facilitate smooth material flow and easier part ejection, further enhancing the final product’s quality.
To increase injection speed, one can use increased oil pump capabilities or implement double pump injection, which can raise speed by 70%. However, excessive injection speeds and pressures can cause defects such as jetting and part distortion, so it’s crucial to strike a balance between speed and quality.
Effective Cooling Channels
Effective cooling channels are vital in thin wall molding as they expedite the cooling process and maintain dimensional stability. Placing cooling channels close to the molding surface ensures that the parts cool evenly, preventing defects such as warping and sink marks.
Challenges in thin wall molding can lead to uneven cooling, which may cause warping and cracks. Maintaining consistent wall thickness is crucial to ensure even cooling and avoid these defects. Effective cooling systems enable manufacturers to produce high-quality parts with minimal defects.
Choosing the Right Equipment
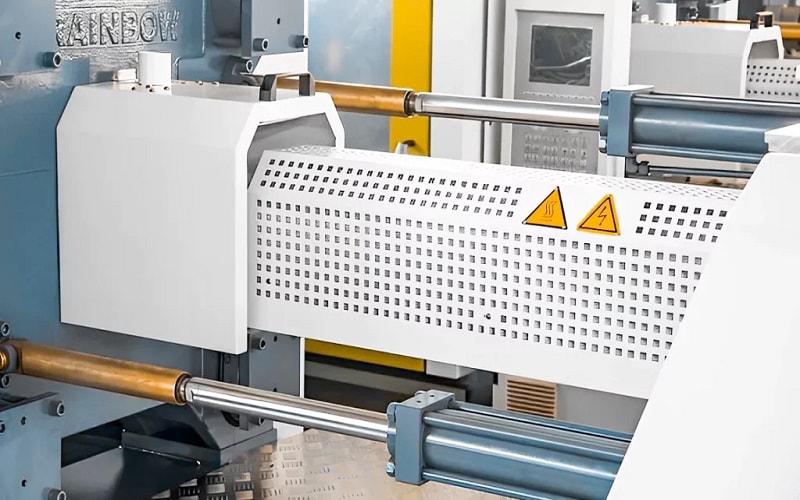
Choosing the right equipment is vital for successful thin wall injection molding. Specialized machines meet rigorous production demands, achieving cycle times as quick as two seconds, significantly enhancing efficiency.
These machines often feature hybrid drives for improved energy efficiency. High injection pressures exceeding 2,000 bar ensure proper flow and quality, while advanced clamping units maintain precise mold alignment.
While thin-wall-capable machines tend to be more expensive than general-purpose machines due to the need for precise computer control, the investment is justified by the high-quality parts they produce. For instance, the e-speed injection molding machine is designed specifically for efficiently producing thin wall plastic parts at remarkable speed.
Common Challenges and Solutions
Thin wall molded parts are challenging to fill compared to thicker parts, which can lead to defects. Neglecting material flow considerations can result in short shots and uneven filling. Therefore, maintaining consistent injection speeds and pressures is critical to achieving high-quality parts in thin wall injection molding.
Excessive injection speeds and pressures can cause defects like jetting and part distortion. Inadequate mold venting can trap air and gas, leading to burns and voids. Proper mold maintenance prevents contamination and ensures consistent production.
Cycle time can be reduced by handling mold opening and ejection simultaneously. Low acceleration, however, negatively impacts average injection speed, affecting the molding cycle. By addressing these challenges, manufacturers can improve the quality and efficiency of their thin wall molding processes.
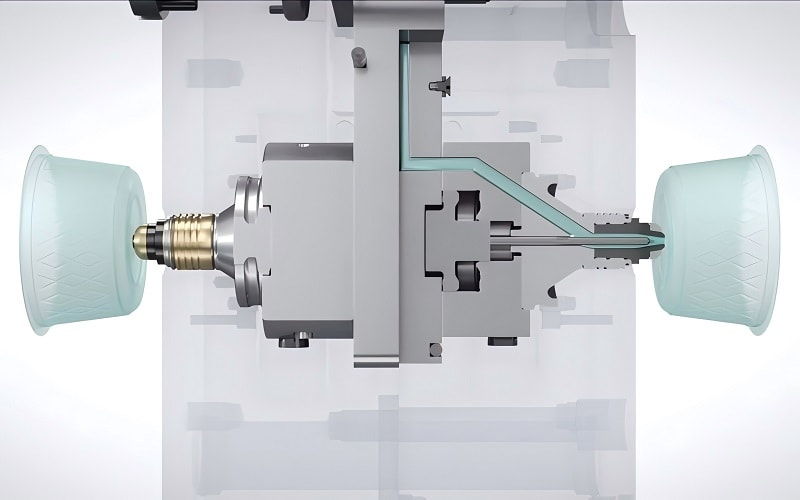
Advantages of Thin Wall Injection Molding
Thin wall injection molding offers several advantages, including significant reductions in material usage, which saves costs for manufacturers. This process also reduces resource consumption and weight, thereby decreasing transportation costs and environmental impact.
Industries such as automotive, electronics, and food packaging benefit from the lightweight components produced through thin wall injection molding. Thinner designs facilitate less fuel consumption during shipping due to the reduced overall weight of the products. This method is not only cost-effective but also environmentally friendly, making it a popular choice across various industries.
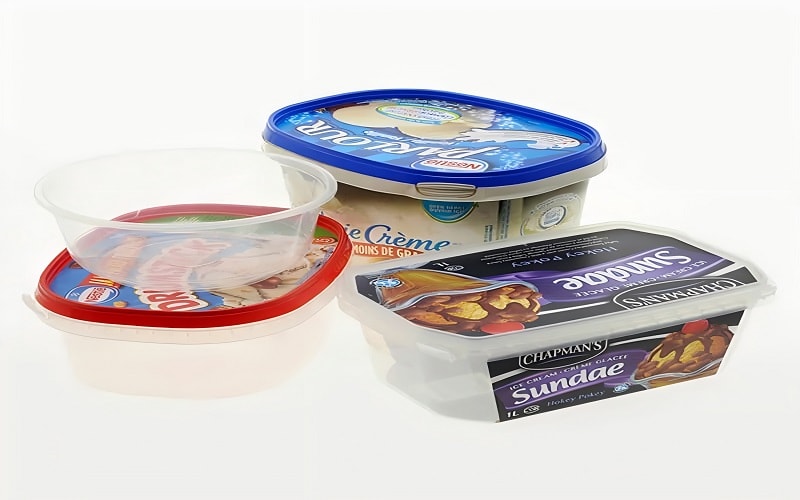
Summary
In conclusion, thin wall injection molding is a sophisticated process that offers numerous benefits, from cost savings to environmental advantages. By understanding the intricacies of the process, selecting the right materials, and optimizing design and equipment, manufacturers can produce high-quality thin wall parts efficiently. As industries continue to demand lighter, stronger, and more precise plastic parts, mastering thin wall injection molding will be a critical skill for staying competitive in the market.
Frequently Asked Questions
What is considered a thin wall in injection molding?
A wall thickness of less than 1mm is generally considered thin in injection molding, though some applications may reach up to 2mm. This understanding is crucial for achieving optimal product strength and quality.
Why are high injection speeds necessary for thin wall molding?
High injection speeds are necessary for thin wall molding to quickly fill the mold cavity, which helps prevent defects such as short shots and weak knit lines. This ensures better product quality and structural integrity in the final output.
What materials are best suited for thin wall injection molding?
For thin wall injection molding, materials such as HDPE, LDPE, polypropylene, and liquid silicone rubber are best suited due to their excellent flow characteristics.
How can structural integrity be maintained in thin wall parts?
To maintain structural integrity in thin wall parts, it is effective to incorporate design features like ribs, gussets, and bosses, which enhance strength and minimize defects such as warping. These features help ensure the part remains robust while maintaining its intended shape.
What are the common challenges in thin wall injection molding?
Common challenges in thin wall injection molding include filling difficulties, defects due to high injection speeds, inadequate venting, and uneven cooling, which can result in warping and cracks. Addressing these issues is crucial for achieving optimal results.