Tooling for plastic injection molding involves creating molds that shape plastic into precise parts. It’s vital for high-quality manufacturing. This article covers strategies, tool types, materials, and key components to help you optimize your molding process.
Understanding Injection Molding Tooling
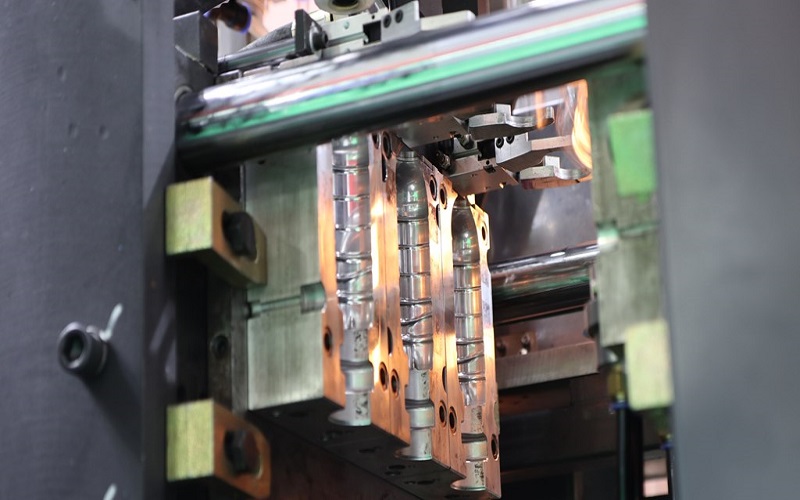
Tooling in injection molding refers to the process of designing and engineering the tools required to produce parts through this method.
These tools, known as injection molds, are critical as they shape molten plastic resins into precise injection molded parts using a metal mold, ensuring high-quality results across various industries. Plastic injection tooling is essential for achieving this precision. Tooling engineers play a vital role in this process, particularly in the realm of plastic injection.
The success of injection molding heavily relies on meticulous tooling that meets tight tolerances for precision. Factors such as production volumes, costs, and part geometry complexity significantly influence mold design. Additionally, the choice of materials in the tooling process affects accuracy and reliability, impacting injection molded parts quality.
Injection molding machines are used to operate these molds, injecting molten plastic into the mold cavities to form the parts. Prototype tooling is often employed to create initial samples for testing and validation before full-scale production begins.
Key Types of Injection Molding Tools
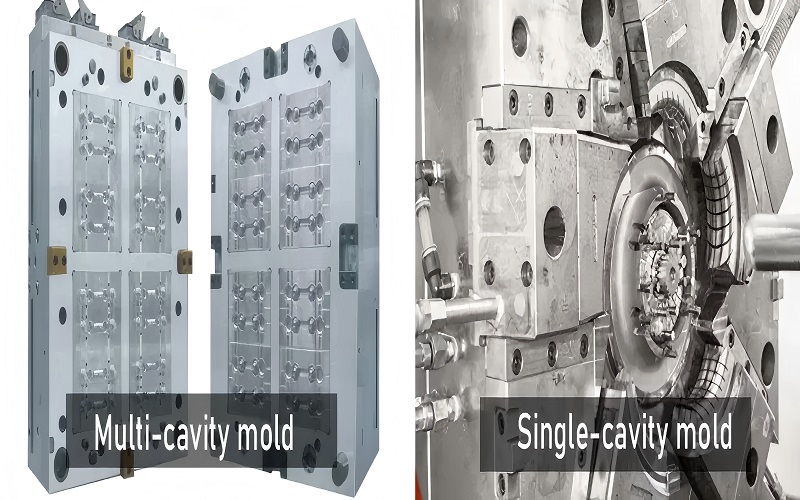
Injection molding utilizes a variety of molds to meet specific manufacturing requirements, and selecting the right type of tool is crucial for optimizing production efficiency and meeting product specifications. There are two distinct approaches in injection mold tooling: hard tooling and soft tooling. Additionally, stack molds are used to increase output capacity with multiple mold parting surfaces.
Understanding the different types of tools, including single-cavity, multi-cavity, and family tools, can help manufacturers choose the best option for their needs.
Single-Cavity Tools
Single-cavity molds produce one part per cycle, making them ideal for prototyping, bridge production, and low-volume manufacturing. Each injection cycle with a single cycle mold creates one component, offering advantages such as precision and customization in part production.
These molds are particularly useful for producing limited parts to evaluate and understand design feasibility.
However, single-cavity molds can lead to longer cycle times and increased tooling costs per part, making them less suitable for high-volume manufacturing.
Multi-Cavity Tools
Multi-cavity molds facilitate the simultaneous production of multiple identical parts, enhancing production efficiency by reducing cycle times and costs. Industries such as automotive, consumer goods, and electronics frequently utilize multi-cavity molds due to their ability to support rapid mass manufacturing.
Designing these molds presents challenges, such as ensuring uniform filling, cooling, and ejection for all cavities, but the benefits in terms of production speed and cost-effectiveness are significant.
Family Tools
Family tools in injection molding allow for the production of multiple distinct same part in one cycle, simplifying production and reducing tooling costs for manufacturers.
These molds are particularly beneficial when producing parts that are used together in an assembly, as they streamline the manufacturing process and offer economic advantages.
Material Choices for Injection Mold Tooling
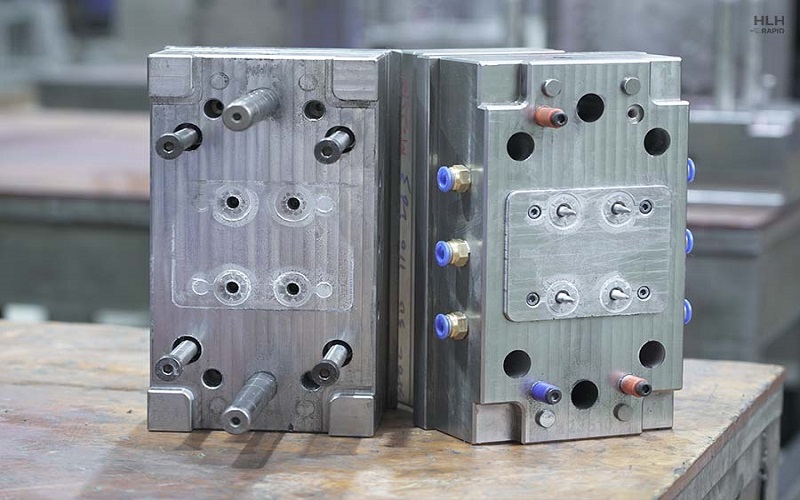
The most commonly used materials for injection molding tooling are steel and aluminum, each offering distinct advantages. Tool steel is favored for its hardness and wear resistance, making it ideal for high-volume production. Aluminum, on the other hand, is lightweight and cost-effective, known for its good thermal conductivity, which benefits the prototyping phase.
Material selection for injection molding is determined by factors such as durability, cost, performance, and specific application needs. Choosing the appropriate tooling material is crucial for maintaining dimensional tolerances and ensuring the longevity of the mold material.
Steel Tooling
In high-volume production, the durability and performance of injection molds significantly impact overall production efficiency. Tool steel, known for its hardness, is often used in injection molds due to its ability to withstand high wear.
These durable, high-pressure, high-performance steel molds are essential for meeting the demands of mass production, ensuring that high quality parts are consistently produced.
Aluminum Tooling
Aluminum tooling offers lower costs and faster production times, making it economically advantageous for businesses. Its lightweight nature and excellent thermal conductivity make aluminum ideal for prototyping and low-volume runs.
However, aluminum molds are softer and cannot be hardened like steel, which impacts their durability in high-volume production. Overall, aluminum tooling provides an efficient and cost-effective solution for manufacturers focusing on shorter production cycles.
Copper Alloy Tooling
Copper alloys provide excellent thermal conductivity, making them highly suitable for specialized applications in tooling. The exceptional thermal conductivity of copper alloys allows for efficient heat dissipation during the injection molding process, which is particularly beneficial for high temperatures, high-speed injection molding or tooling for heat-sensitive materials.
These properties make copper alloys an invaluable choice for certain specialized applications.
Essential Components of Injection Mold Tooling
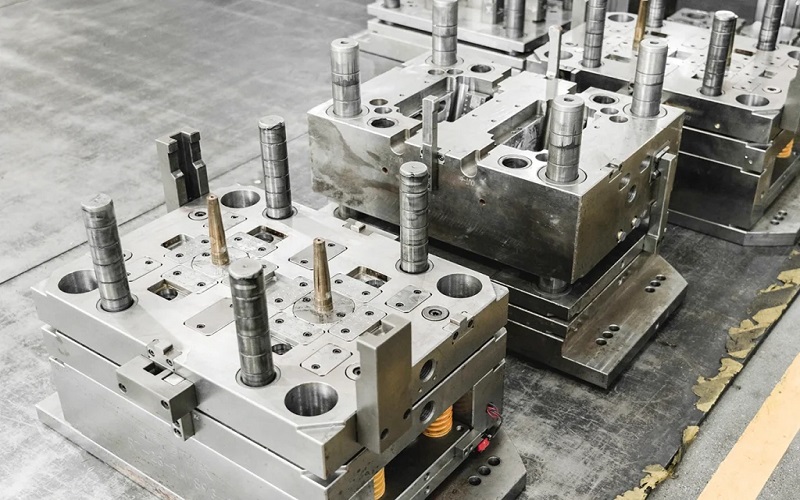
Injection molds are complex assemblies composed of numerous essential components, including:
- Slides
- Guides
- Lifters
- Pins
- Bushings
- Ejectors
- Alignment devices
Mold clamps secure mold halves to molding platens using large bolts or magnets. Core pins are used to create holes, channels, or internal cavities in molded parts, while cavity inserts and metal inserts are specialized components used to create specific features or geometries.
Baffles and diffusers optimize coolant flow in the cooling system of the mold, ensuring efficient cooling and preventing defects. These components work together to ensure optimum flow, precision, repeatability, and safety in the molding process.
Mold Cavities and Cores
Mold cavities are critical spaces within the injection mold where the molten plastic takes shape to form the final product. These cavities define the exterior surfaces of the molded parts, while the mold core forms the internal surfaces, crucial for defining the product’s shape.
Together, they ensure that the final product meets the desired specifications.
Runner Systems
Runner systems play a crucial role in directing molten plastic from the injection nozzle to the mold cavities. These systems facilitate the flow of molten plastic to ensure effective cavity filling during the injection molding process.
Copper alloys are often employed in tooling for their superior heat dissipation properties, enhancing cooling efficiency in runner systems.
Ejector Systems
Ejector systems are responsible for removing the solidified plastic parts from the mold, ensuring the integrity of the molded part. Precision is crucial in the ejector system to prevent damage to the part during ejection.
Ejector pins push the molded part off the core after it solidifies, completing the injection molding cycle.
Factors Influencing Tooling Design
Several factors influence the design of injection mold tooling, including part geometry, production volume, and surface finish. Each of these factors plays a crucial role in determining the complexity, cost, and efficiency of the tooling process.
By understanding these factors, manufacturers can optimize their tooling designs to meet specific production requirements and achieve high-quality results.
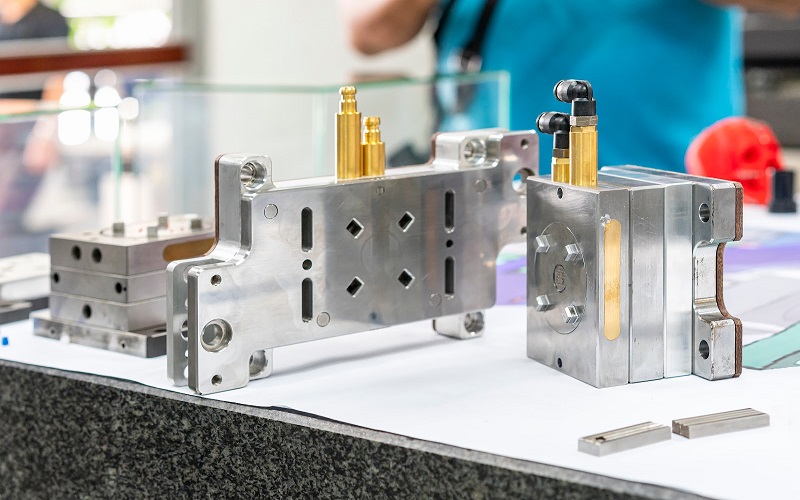
Part Geometry
Part geometry plays a crucial role in tooling design, influencing the complexity required to create parts effectively. Complex geometries require advanced mold designs with more moving parts, which can introduce more variables and risk maintaining tight tolerances.
Design considerations like wall thickness and additional features such as rotating mechanical racks or hydraulic components may be needed for complex molded components.
Production Volume
The production volume significantly determines tooling complexity and durability requirements, affecting overall design considerations. Higher production volumes necessitate robust tooling to endure repetitive cycles without failure. Effective tooling solutions are crucial to meet production demands reliably and efficiently, ensuring durability under high stress during low volume production and mass production.
Surface Finish
Surface finish is a critical aspect of tooling design, as it determines the texture or pattern of the molded part. Smooth, polished surfaces usually require additional finishing operations or specialized mold coatings.
Textured or patterned surfaces may require textured inserts or specific mold cavities during tooling fabrication, impacting the overall manufacturing process.
The Tooling Manufacturing Process
The injection mold tooling manufacturing process is systematic, encompassing design, prototyping, fabrication, and assembly. Each step ensures quality, reliability, and efficiency, starting with the design phase and moving through to the final assembly and testing of the mold to manufacture it. The mold is carefully manufactured to meet the required specifications, including scientific molding and injection molded components.
Achieving fine surface finishes often demands precise cooling strategies in the mold design, including effective cooling lines, influencing the overall fabrication process.
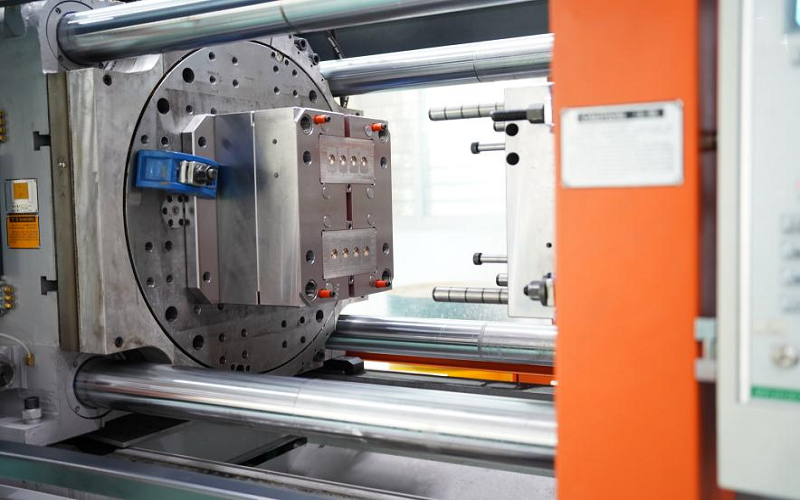
Design and Engineering
The initial stage of creating injection mold tooling involves mold design and layout preparation. This phase includes finalizing the mold core and cavity details along with a bill of materials.
CAD and CAM software are critical tools used to create detailed mold designs, ensuring high-precision results tailored to specific product requirements in computer aided manufacturing.
Prototyping
Prototyping in injection molding is a crucial step for testing and refining designs before full-scale production. Common techniques for prototyping include 3D printing and CNC machining, which help identify and address potential issues early in the design process.
This phase ensures that any design flaws are mitigated before committing to expensive full-scale tooling.
Fabrication and Assembly
CNC machining is the primary method used for fabricating injection molding tools, ensuring tight tolerances and precision. After the mold components are assembled, the mold undergoes rigorous inspection and testing to ensure proper alignment and fit of all components, resulting in high-quality tooling.
Precision tooling assembly techniques are crucial for the final product’s integrity and performance.
Common Challenges in Injection Mold Tooling
Design complexity and balancing different volumes are significant challenges associated with family molds. Prototyping serves to verify and refine mold designs before full-scale production, helping to mitigate part complexity and design flaws early in the process.
After assembly, molds are subjected to thorough testing to confirm they meet operational standards and performance specifications. To ensure quality in injection molding tooling, several key factors are important. These include the use of sensors, benchmarking, and achieving process repeatability.
Cost Optimization Strategies in Tooling
Injection mold tooling largely dictates overall project cost and quality of the end part. Several strategies for cost optimization and cost considerations exist in injection molding tooling, such as increasing the quantity of parts produced to significantly decrease the lower cost per unit by spreading the initial tooling expenses over a larger number of pieces.
Modifying existing molds instead of creating new ones for different part revisions can save on tooling costs and enhance efficiency. Family molds streamline processes and reduce tooling costs for manufacturers.
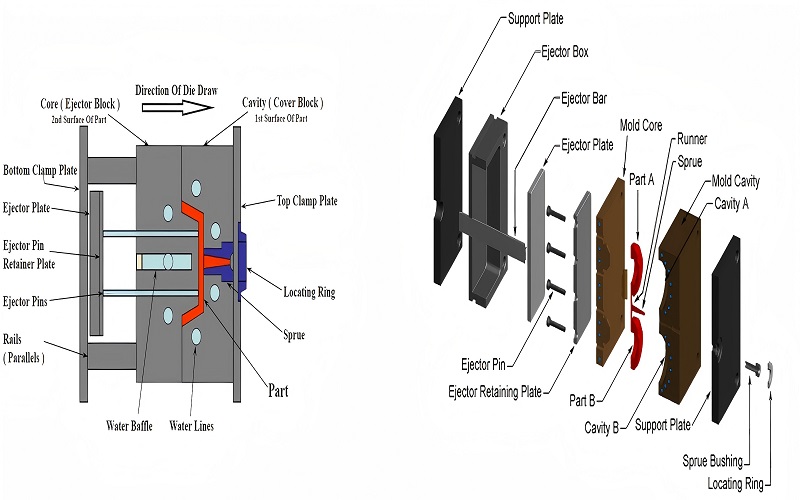
Summary
Injection molding tooling is a complex yet fascinating aspect of modern manufacturing that entails a meticulous process from design to production. High-quality tooling is crucial for producing precise and reliable parts that meet stringent standards across various industries.
Understanding the different types of molds, the importance of material selection, and the essential components of molds is vital for optimizing production efficiency and reducing costs. By considering factors such as part geometry, production volume, and surface finish, manufacturers can design effective molds that meet their specific needs.
The systematic process of tooling manufacturing, which includes design, prototyping, and assembly, ensures quality and reliability. Despite the challenges, employing smart cost optimization strategies can significantly enhance efficiency and reduce expenses.
With this knowledge, manufacturers can navigate the complexities of injection mold tooling with confidence and achieve outstanding results in their production processes.
Frequently Asked Questions
What tooling is used for injection moulding?
Injection moulding tooling typically utilizes steel, aluminum, or alloys, and is generally composed of two halves, though more complex designs with multiple sides or internal components can also be used.
What is injection molding tooling?
Injection molding tooling involves the design and creation of molds that shape molten plastic into specific parts during the injection molding process. These precision-engineered tools are essential for producing high-quality, consistent components.
What are the main types of injection molding tools?
The main types of injection molding tools are single-cavity molds, multi-cavity molds, and family molds, each tailored for specific production requirements ranging from prototyping to large-scale manufacturing. Understanding these differences is essential for selecting the right tool for your project.
Why is material selection important in injection mold tooling?
Material selection is essential in injection mold tooling as it directly influences the mold’s accuracy, durability, and performance. Choosing the right material, such as steel or aluminum, ensures the mold meets specific application requirements effectively.
What are the essential components of an injection mold?
The essential components of an injection mold include mold cavities and cores, runner systems, ejector systems, slides, and alignment devices, all of which play a critical role in ensuring precision and efficiency in the molding process. Understanding these components can enhance the overall effectiveness of manufacturing.