Tooling plastic is vital in injection molding. It is used to create the molds that shape molten plastic into finished products. Knowing about tooling plastic can improve manufacturing outcomes.
This guide explores its importance, materials, and mold types.
Understanding Plastic Injection Molding Tooling
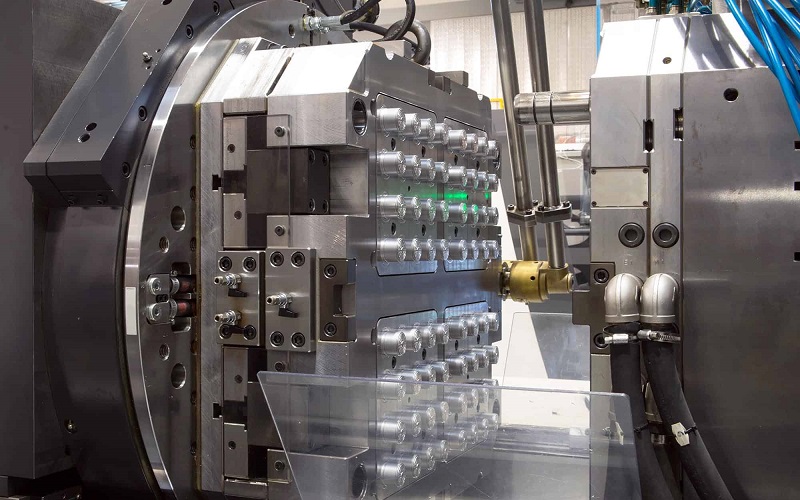
Injection molding tooling is a sophisticated process combining science and creativity to manufacture precision-molded parts. This injection moulding process involves injecting molten plastic resin into a mold to produce components, making it central to production using an injection moulding machine and plastic injection tooling.
High-quality tooling is essential for producing precision parts. The complexity and tight tolerances of the tooling are critical to success. Tooling engineers must consider factors like material, shape, and specific features during the design phase to ensure the final product meets required standards and specifications.
Injection molding tooling involves understanding material properties, optimizing mold design, and managing costs. Molds shape and hold molten plastic under high pressure, requiring meticulous control for consistency and quality. Properly designed cooling lines within the mold help regulate temperature, ensuring the plastic solidifies uniformly. Scientific molding techniques provide highly accurate steps to achieve top-quality parts consistently.
Materials Used in Injection Mold Tooling
Injection molding tooling utilizes various materials, including plastic materials, each selected for its properties and application suitability. Commonly used materials include steel, aluminum, and alloys, favored for their durability, thermal conductivity, and ability to withstand high pressures and temperatures.
Steel and aluminum are commonly used in injection mold tooling. Aluminum molds are lightweight and offer excellent thermal conductivity, making them cost-effective for low-volume production. Steel is preferred for high-volume production due to its ability to tolerate higher temperatures and pressures, resulting in longer mold life and better surface finish. Alloy materials enhance performance by combining properties of different metals, improving durability and finish.
High-performance materials like PEEK and Ultem are notable in demanding applications due to their exceptional thermal and chemical resistance. Tool steel and hard aluminum alloys are suitable for custom molds where precision and durability are crucial. The choice of material affects the tooling process, quality, and longevity of the final products.
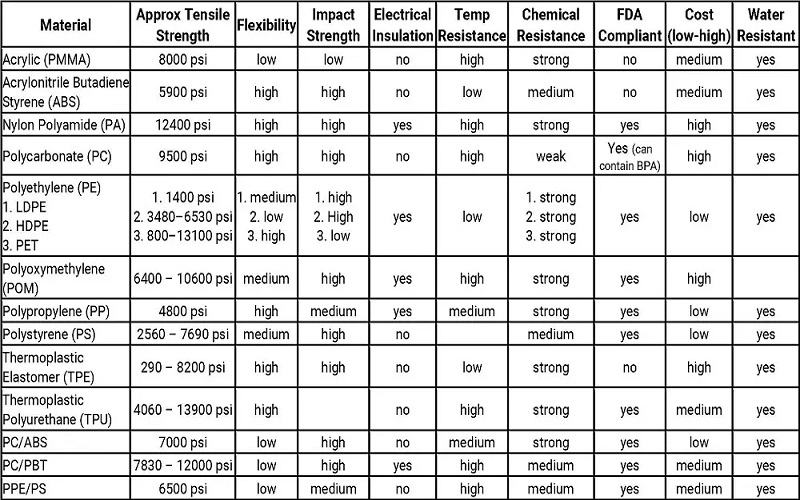
Types of Injection Molds
Injection molds can be categorized based on various features, including feeding systems, cavity numbers, and cavity retaining plate designs. Knowing these types helps in selecting the right mold for specific applications.
The primary types include single-cavity molds, multi-cavity molds, and family molds, each serving different production needs and offering unique advantages.
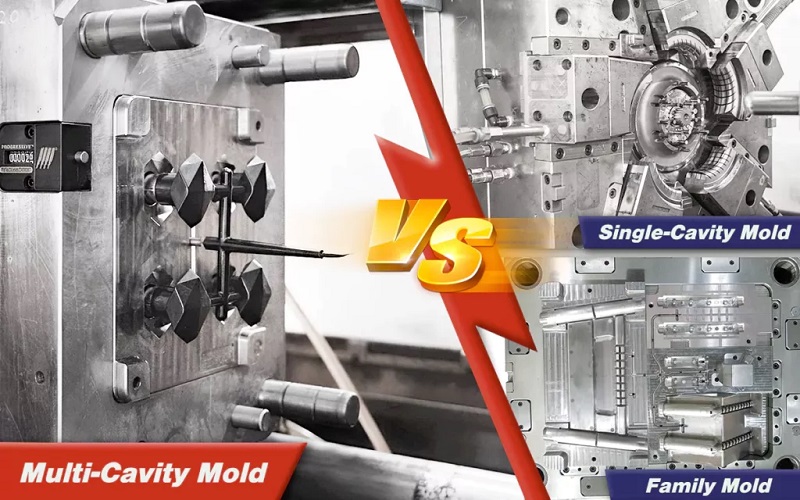
Single-Cavity Molds
Single-cavity molds produce one component per cycle, making them cost-effective and easier to manage, especially for low-volume production or prototyping. They are ideal for applications requiring precision and control, allowing meticulous monitoring of each part produced.
The simple design of single-cavity molds results in fewer variables to control, leading to consistent quality. They are often used when producing high-quality, precision parts is more critical than quantity, making them invaluable for introducing new products or initial production runs in injection molding operations.
Multi-Cavity Molds
Multi-cavity molds revolutionize mass production by enabling the simultaneous production of multiple identical parts. This significantly boosts production speed and efficiency, making them preferred for high-volume manufacturing. Producing several parts in a single cycle reduces the cost per piece, crucial in competitive markets.
Designing multi-cavity molds requires precise balancing to ensure uniform fill and consistent quality across all parts, involving sophisticated tooling and careful engineering. Despite the increased complexity, the benefits of higher output and efficiency make multi-cavity molds indispensable in large-scale production.
Family Molds
Family molds produce various plastic parts simultaneously, each with different shapes and sizes, making them efficient for manufacturing sets of related components. Their design requires careful handling of volume and complexities to ensure proper fit and orientation of each part.
Balancing the volume of each cavity in a family mold ensures uniform fill and prevents issues like warping or short shots. Effective management of these complexities leads to consistent quality, making family molds a versatile and cost-effective solution for producing multiple different parts in one cycle.
Key Components of Injection Mold Tooling
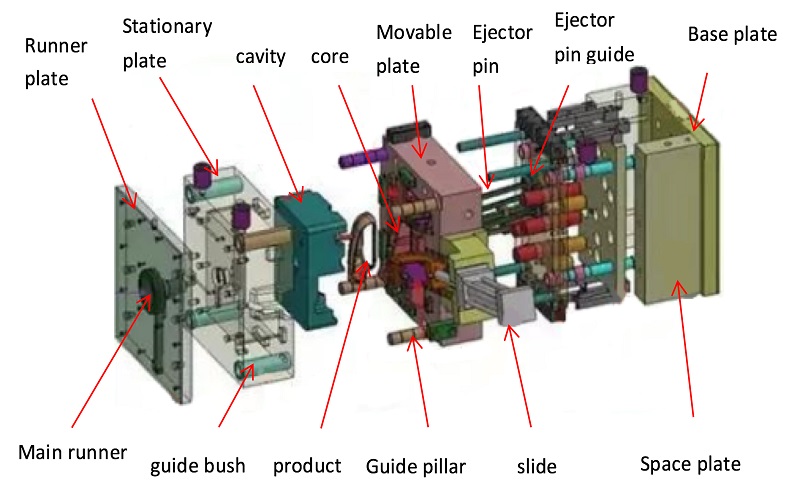
Key components of injection mold tooling are crucial in shaping the final product. The mold cavity, a hollow space inside the mold, shapes the molten plastic. The mold core forms the internal surfaces of a plastic part, significantly influencing its structural integrity.
Core pins create holes, channels, or internal cavities in molded parts, while inserts create specific features. Sprues connect the injection nozzle to the mold cavity, and the runner system guides molten plastic from the machine’s nozzle to the mold cavities.
Venting systems allow air to escape during the injection process, preventing defects. Cooling systems manage mold temperatures, ensuring the quality of the molded parts.
The ejection system, including ejector pins, removes molded parts from the mold without damage. Proper alignment ensures accurate and secure mold placement during operation, affecting the quality and efficiency of the molded part. Designing and maintaining these components is crucial for high-quality parts and efficient production.
The Role of Cooling Systems in Injection Molding
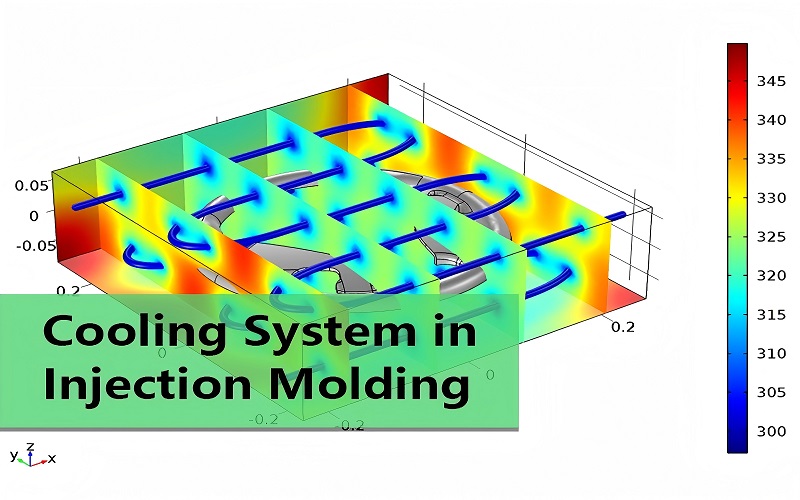
The cooling phase in injection molding allows the injected plastic to solidify before ejection from the mold. This phase can account for up to 75% of the total cycle time, significantly affecting efficiency. Effective cooling design mitigates defects, reduces rework, and minimizes material waste during production.
Cooling channels ensure even mold cooling, preventing defects like sink marks and warping. Conformal cooling channels offer better thermal management for complex geometries compared to straight-line channels. Design features like baffles and bubblers enhance coolant flow and improve temperature distribution.
Different cooling methods are used depending on mold requirements. Air cooling is often used for slender cores, while water cooling is preferred for larger molds. The choice of cooling method impacts the quality and consistency of the final product, making it a critical aspect of injection molding.
Choosing the Right Tooling Material
Choosing the right material for tooling is vital, impacting durability and production efficiency. Durability, cost, and performance are key factors in selecting materials for injection molding tooling. Essential criteria include strength, function, cost, and molding parameters.
Commonly used materials include H-13 Tool Steel, known for its versatility and balance between hardness, toughness, and polishability. P-20 Tool Steel excels in machinability, suitable for prototypes or lower-volume production runs. Stainless steel is ideal for applications requiring corrosion resistance, especially with resins that produce corrosive gases.
Production run volume and part complexity are critical in choosing the right material. Proper material selection affects tool longevity and production aspects, including cost per unit and overall efficiency. Single-cavity molds are often preferred for their lower tooling costs and enhanced process control.
Common Issues and Troubleshooting in Injection Mold Tooling
Injection mold tooling faces challenges like flow marks and sink marks, which can affect part quality. Flow marks result from limited flow areas, inadequate melt temperatures, or insufficient injection pressure. Sink marks are caused by insufficient holding time and can be exacerbated by high melt temperatures.
Other issues include flash, occurring when clamping force is lower than injection pressure or if there are gaps in the mold. Warpage is often due to uneven cooling rates, requiring adjustments in temperature and pressure. Uniform wall thickness avoids defects like sink marks and warping.
Proper maintenance, including regular cleaning and lubrication, extends the lifespan of injection mold tooling and ensures consistent part quality and operational efficiency. Troubleshooting and addressing issues like burn marks, voids, bubbles, jetting, and weld lines prevent material degradation and ensure high-quality parts.
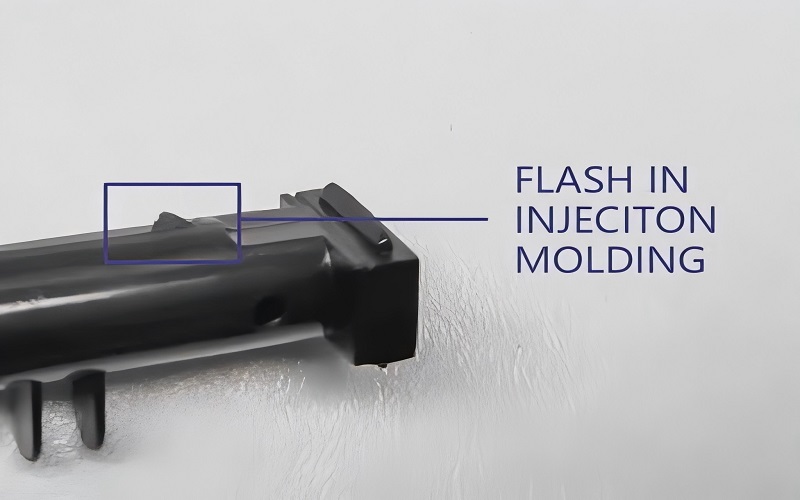
Importance of Tooling Design in Injection Molding
The injection mold tool design significantly influences the quality of the final molded parts. Proper venting allows gases to escape during the injection process, preventing defects. The part line location affects the potential for flashing, minimized through meticulous mold design.
Draft angles facilitate easier removal from the mold and prevent warping. Eliminating undercuts and unnecessary features in part design can reduce tooling costs and simplify part ejection. Using a core cavity design molds complex shapes more cost-effectively while improving surface finish and ejectability.
Designing self-mating parts can reduce the need for multiple molds, lowering manufacturing expenses. Tooling design is crucial as it directly impacts the efficiency, cost, and quality of the injection molding process.
Cost Optimization Strategies in Injection Mold Tooling
Factors like material type, mold complexity, surface finish, mold size, and the number of cavities significantly affect injection mold tooling costs. Minimizing cosmetic finishes can decrease production costs, as finer finishes often require additional machining and handling.
Conducting a design for manufacturability (DFM) analysis identifies potential design flaws and improvement opportunities before production. Effective cost management in injection molding tooling positively impacts overall quality and efficiency.
The aim is to balance quality, efficiency, and budget.
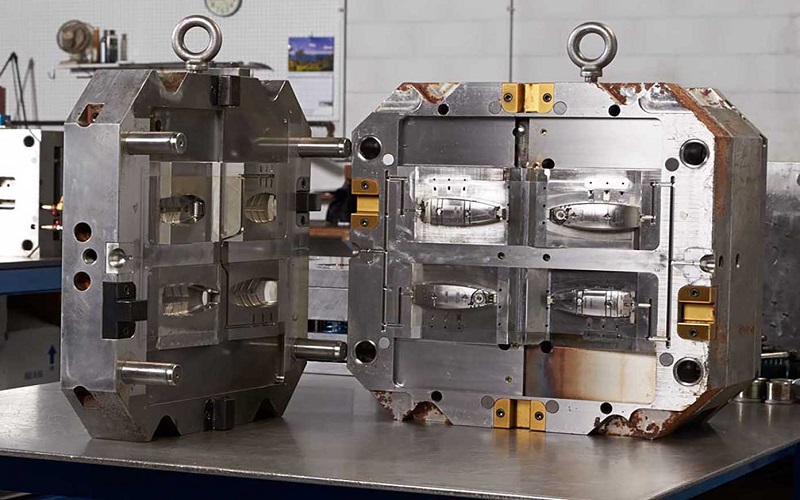
Evolution of Injection Mold Tooling
Injection mold tooling has evolved with increased complexity, efficiency, and technological integration. The development of synthetic plastics in the early 20th century expanded injection molding’s scope, enabling the production of complex shapes quickly and cost-effectively using an advanced molding machine.
Technological advancements have significantly impacted the manufacturing process, allowing for greater precision and repeatability through optimum flow of materials into the mold. Considering part size and dimensions is crucial as larger parts may require bigger molds, impacting overall costs.
The future of injection mold tooling looks promising, with innovations aimed at enhancing efficiency and reducing costs.
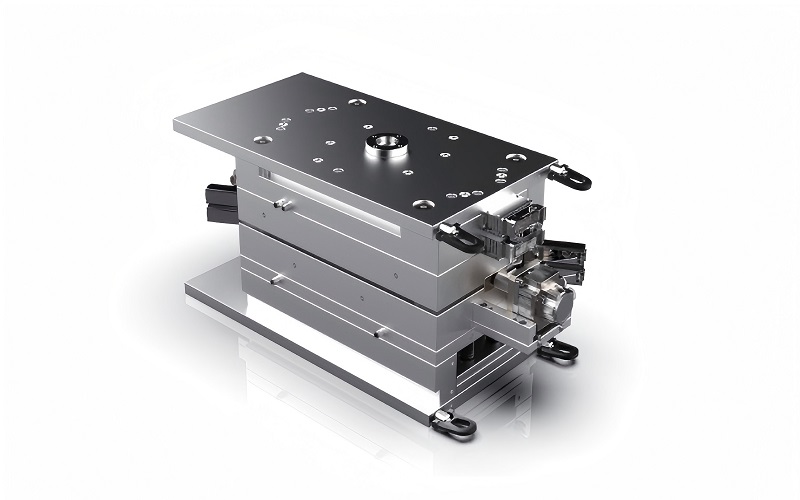
Summary
Injection molding tooling is a complex yet fascinating field that plays a critical role in modern manufacturing. From understanding the materials used to recognizing the importance of tooling design, every aspect of the process contributes to the production of high-quality plastic parts.
By mastering the principles and practices outlined in this guide, you can achieve success in your injection molding projects.
Remember, the key to excellence lies in continuous learning and improvement. Embrace the challenges, optimize your processes, and watch your manufacturing capabilities soar.
Frequently Asked Questions
What are the most common materials used in injection mold tooling?
Steel, aluminum, and various alloys are the primary materials employed in injection mold tooling due to their exceptional durability and thermal properties, making them suitable for high-pressure and temperature settings.
What are the differences between single-cavity and multi-cavity molds?
Single-cavity molds are designed to produce one component per cycle, making them simpler and more cost-effective, while multi-cavity molds can produce multiple identical parts simultaneously, enhancing efficiency and lowering the cost per unit. This key distinction can significantly impact production strategy and budgeting.
How can I reduce costs in injection mold tooling?
To reduce costs in injection mold tooling, implement strategies such as minimizing cosmetic finishes, conducting a design for manufacturability (DFM) analysis, and effectively balancing quality with budget and efficiency. These measures will enhance cost-effectiveness.
What role do cooling systems play in injection molding?
Cooling systems are essential in injection molding, as they enable the injected plastic to solidify efficiently, comprising up to 75% of the total cycle time. A well-designed cooling system enhances product quality and minimizes defects.
What common issues might I encounter in injection mold tooling, and how can I troubleshoot them?
You may encounter flow marks, sink marks, flash, warpage, and voids in injection mold tooling. Troubleshooting these issues typically involves adjusting melt temperatures, injection pressure, and cooling rates, along with maintaining the mold properly.