Looking for the strongest plastics? This article covers the top seven materials known for their durability and impact resistance. Discover their key properties and uses in high-stress and demanding environments.
Key Takeaways
- The selection of plastics for specific applications depends on mechanical properties like tensile strength, impact resistance, abrasion resistance,and chemical resistance, which determine their performance under various conditions.
- Plastics such as Polycarbonate, PEEK, and PETG are highlighted for their excellent impact resistance and durability, making them suitable for industries like medical, aerospace, and packaging.
- Consideration of environmental factors, application needs, and budget constraints is essential for making informed decisions about the right plastic material for a project.
Understanding the Strength of Plastics
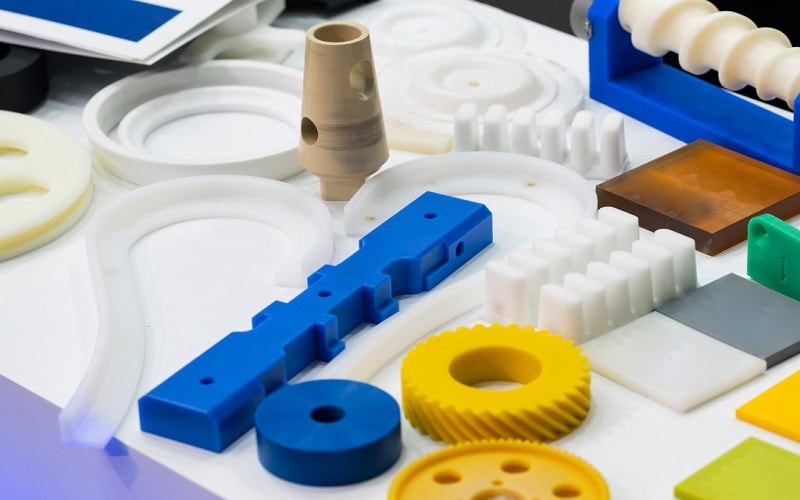
The strength of plastics is influenced by various mechanical properties, including tensile strength, impact resistance, and chemical resistance. These properties determine how well a plastic can bear loads, endure sudden forces, and resist chemical degradation.
Selecting the right plastic is not just about choosing a material that is strong but also one that fits the specific needs of the application, from load-bearing capabilities to environmental exposure.
Different applications require specific mechanical properties like strength and flexibility. Assessing the intended use, including load requirements and environmental exposure, helps in selecting the right plastic.
Understanding key factors such as tensile strength, impact resistance, and chemical resistance is crucial for making an informed decision.
Tensile Strength
Tensile strength measures how much force a plastic can withstand when being stretched before it breaks. This property is vital for applications where the plastic will be subjected to physical stress, such as in structural components or high-stress environments.
For instance, Polyamide-Imide (PAI) maintains higher strength at elevated temperatures compared to many thermoplastics at room temperature. This characteristic makes it ideal for applications where both heat resistance and mechanical properties are crucial.
Moreover, plastics with high tensile strength offer excellent dimensional stability, meaning they maintain their shape and size under various conditions.
This rigidity is essential for applications like electrical connectors and mechanical parts, where precision and reliability are paramount. Ensuring that the material can withstand high impact forces without deforming allows manufacturers to produce durable components with high impact strength.
Impact Resistance
Plastic material’s impact resistance is the ability of a plastic to resist fracture and deformation under temporary forces.
This property is crucial for ensuring that plastics can endure sudden forces without fracturing. Impact-resistant plastics are designed to absorb and dissipate energy from impacts, providing toughness and resistance to cracks.
For example, higher impact resistance means that a plastic requires greater force to crack, making it suitable for protective applications. Impact resistance plastics are essential in many industries due to their durability.
Choosing the right impact-resistant plastic can significantly enhance the performance and lifespan of the final product, from automotive components to consumer electronics. Selecting suitable impact-resistant materials greatly influences a project’s overall efficiency and durability.
Chemical Resistance
Chemical resistance refers to a plastic’s ability to resist degradation from exposure to various chemicals.
This property is essential in environments where the material will come into contact with harsh chemicals, such as in chemical tanks or industrial applications. For instance, materials like PTFE are highly resistant to a wide range of chemicals, making them ideal for use in corrosive environments.
In addition to resisting chemical attack, good chemical resistance also contributes to the overall durability and longevity of the plastic. For example, PETG maintains its integrity at elevated temperatures, withstanding conditions like boiling water. This makes it suitable for applications that require both thermal stability and chemical resistance, ensuring that the material remains reliable under challenging conditions.
Polycarbonate (PC)
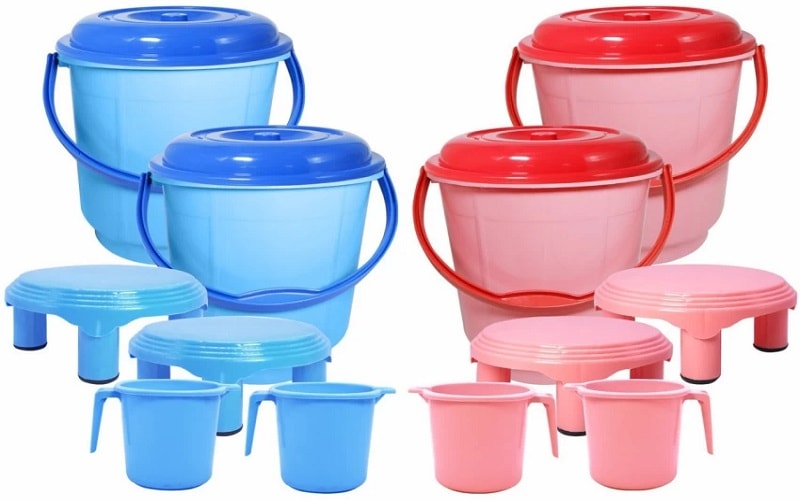
Polycarbonate is renowned for its excellent impact resistance, making it one of the strongest plastics available. It can withstand impact strength of up to 70 kJ/m2, with Notched IZOD metrics ranging from 90.0 to 200.0 j/m2. This high impact resistance makes polycarbonate an ideal choice for applications that require both durability and safety, such as protective goggles and architectural glazing.
Beyond its impact resistance, polycarbonate also offers high clarity and dimensional stability across a wide temperature range. These properties make polycarbonate useful in a wide variety of applications such as injection molded electronic equipment housings and automotive parts.
Its optical clarity and safety features make it a popular choice for eyewear lenses, where both protection and visibility are crucial.
Polyether Ether Ketone (PEEK)
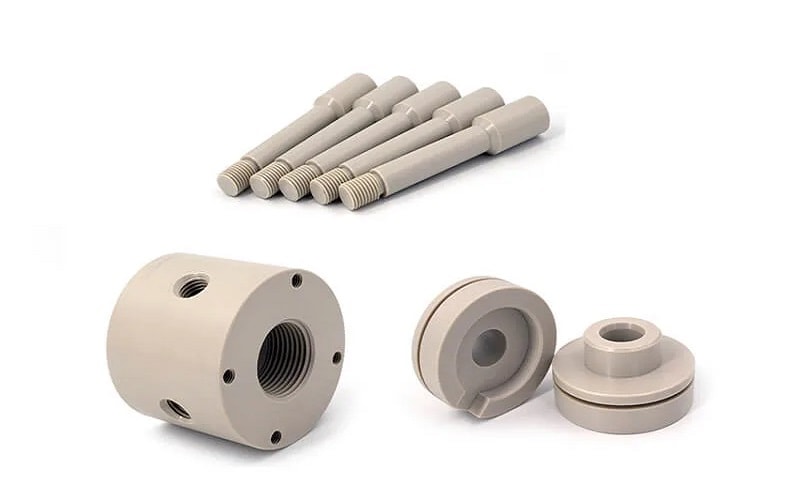
Polyether Ether Ketone (PEEK) is recognized for its unique combination of high strength, heat resistance, and chemical resistance. This high-performance plastic maintains its structural integrity even under extreme thermal conditions, making it suitable for demanding applications.
PEEK’s excellent chemical resistance further enhances its suitability for challenging environments, such as in aerospace components and medical implants.
PEEK is extensively used in applications where both durability and performance are critical. Its ability to withstand high temperatures and resist chemical degradation makes it a reliable material in fields that demand the highest standards of performance and safety. Whether in the medical or aerospace industry, PEEK’s properties ensure that it remains a top choice for advanced applications.
Acrylonitrile Butadiene Styrene (ABS)
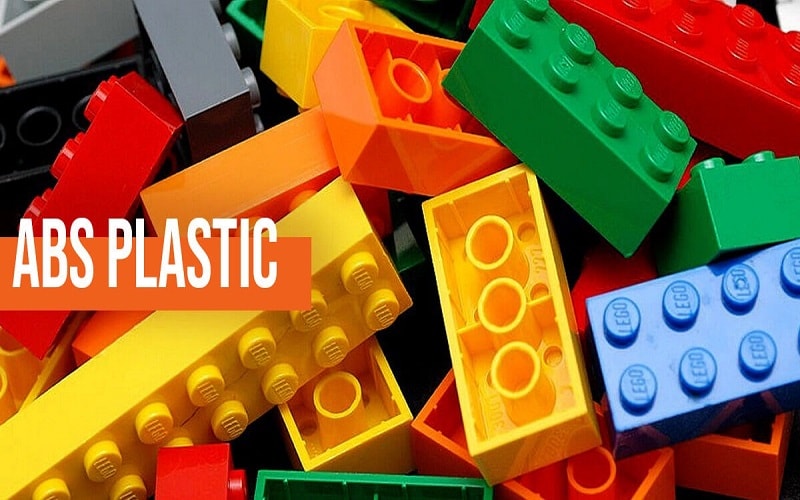
Acrylonitrile Butadiene Styrene (ABS) is known for its high impact resistance, with a Notched IZOD impact resistance range of 200.0 to 215.0 j/m2. This makes ABS an excellent choice for applications where durability and impact resistance are paramount.
Common applications of ABS include automotive parts like instrument panels, consumer electronics, and children’s toys, showcasing its versatility and durability.
ABS’s strong mechanical properties, including good impact strength and heat-resisting properties, make it an attractive material for various applications.
Its production allows for processes such as extrusion to create continuous profiles, and its electrical insulating properties make it ideal for electronic device housings. These characteristics ensure that ABS remains a popular choice for a wide range of industries.
High-Density Polyethylene (HDPE)
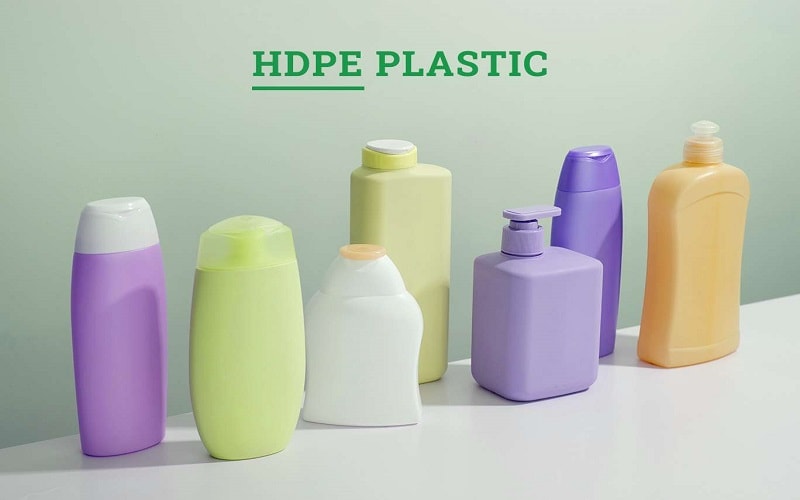
High-Density Polyethylene (HDPE) is known for its strength, endurance, and chemical stability. With a density ranging from 0.93 to 0.97 g/cm³, HDPE exhibits rigidity and strength, making it suitable for various applications.
Its versatility, lightweight nature, and good impact resistance make it a preferred choice for packaging solutions and other demanding uses.
HDPE’s impressive strength and low moisture absorption contribute to its stability in humid environments. Common applications for HDPE include chemical tanks, marine construction, outdoor equipment, and prosthetics, where its properties ensure reliability and durability.
HDPE maintains its performance across various temperature conditions, with a melting point around 130-137°C.
Polyamide-Imide (PAI)
Polyamide-Imide (PAI) is celebrated for its toughness, strength, and stiffness, as well as its good chemical resistance and low thermal expansion.
With an impact resistance measured at a minimum of 100.0 j/m2 and a maximum of 150.0 j/m2, PAI can withstand significant physical stress. These properties make it suitable for high-stress applications such as bearings, bushings, pump and valve parts, and semiconductor machinery.
Despite its challenging processing requirements due to expense and difficulty, PAI remains a top choice for applications where its unique properties are needed. Its ability to endure harsh environments and maintain performance over time ensures that PAI continues to be a reliable material for critical components.
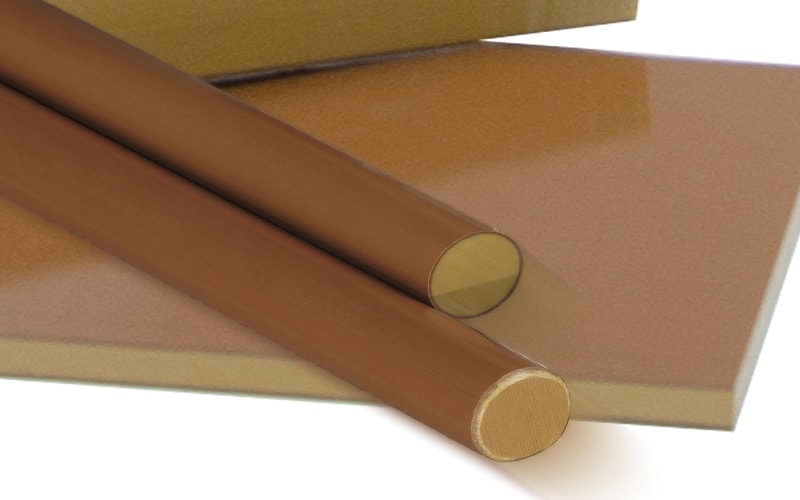
Polyethylene Terephthalate Glycol (PETG)
Polyethylene Terephthalate Glycol (PETG) is known for its impressive impact strength, making it highly durable and resistant to cracking. This material also possesses good chemical resistance, allowing it to endure exposure to various solvents and acids. The inclusion of glycol in PETG’s composition enhances its ductility and reduces brittleness compared to standard PET.
Common applications of PETG include food storage components and medical devices, where its properties ensure safety and reliability. PETG’s ability to be easily thermoformed adds to its versatility, making it a popular choice for packaging and retail displays.
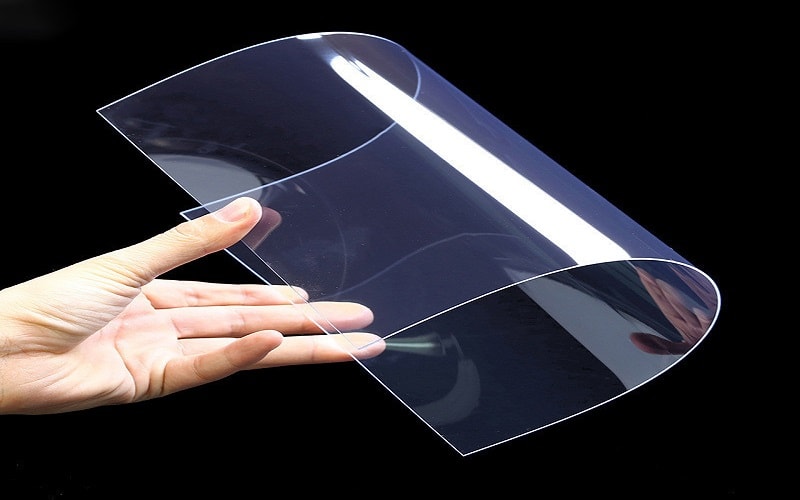
Polytetrafluoroethylene (PTFE)
Polytetrafluoroethylene (PTFE) exhibits low thermal expansion, high fatigue resistance, and good impact resistance. Its impact resistance is superior to many other plastics, including PEEK and most polycarbonates. These properties make PTFE suitable for load-bearing applications, although it tends to creep under pressure.
PTFE’s excellent wear and weather resistance make it ideal for harsh environments. Its ability to maintain performance under extreme conditions ensures that PTFE remains a reliable material for various demanding applications, such as valve parts and other critical components.
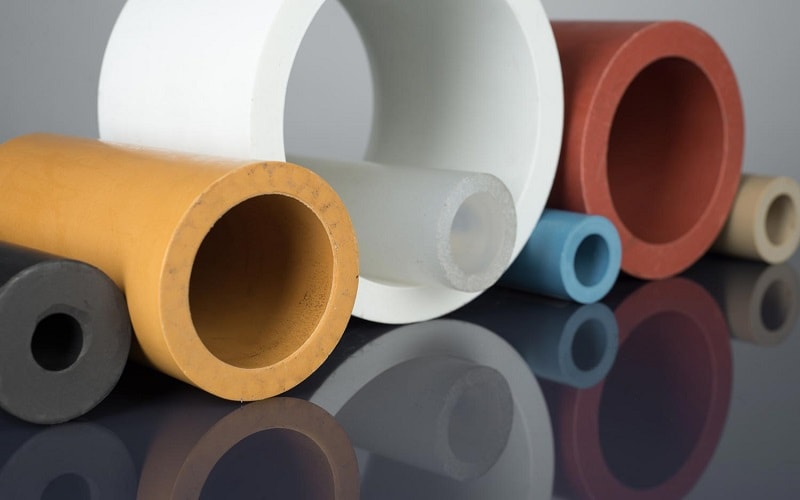
Choosing the Right Strong Plastic for Your Project
Choosing the right impact-resistant plastic can significantly influence the performance and longevity of a production run. Strong plastics such as polycarbonate, PEEK, and PETG are utilized across various industries, including medical, aerospace, and packaging, making them some of the best impact resistant plastic options available.
For instance, polycarbonate is commonly found in medical applications, greenhouses, safety glasses, headlight bezels, and riot shields. PEEK is used in a variety of advanced applications, including aerospace components and medical device parts. PETG can be easily thermoformed, making it a versatile choice for packaging and retail displays.
Understanding your project’s specific needs is key to selecting the right material.
Application Needs
Impact-resistant plastics preserve their structural integrity when under stress. This property is essential for ensuring precision and accuracy in CNC machining.
These materials extend tool lifespan and cause less wear and tear, enhancing productivity. Impact resistance in machining leads to higher-quality finished products, ensuring customer satisfaction.
Knowing the properties of impact-resistant plastics is crucial for informed project decisions. From environmental projects using HDPE geomembranes to machine parts made from PAI, understanding material performance under stress and specific conditions is essential.
Environmental Factors
ABS plastic is generally unsuitable for outdoor applications due to its poor resistance to UV radiation. Exposure to UV light can deteriorate the structural integrity of certain plastics, reducing their overall impact resistance. The material’s melting point typically ranges between 200-240°C, limiting its use in high-temperature environments.
PAI, on the other hand, is known for its exceptional high-temperature strength and low temperatures toughness, making it suitable for various harsh environments.
HDPE’s flexibility and resistance to corrosion make it a favorite in construction, while PTFE’s excellent wear and weather resistance ensure its reliability in demanding conditions.
Budget Considerations
Material costs can vary widely, so it’s vital to balance budget constraints with performance requirements. Achieving cost-effectiveness means balancing desired plastic performance with the available budget.
Making cost-effective decisions without compromising quality ensures long-term performance and viability of the chosen material.
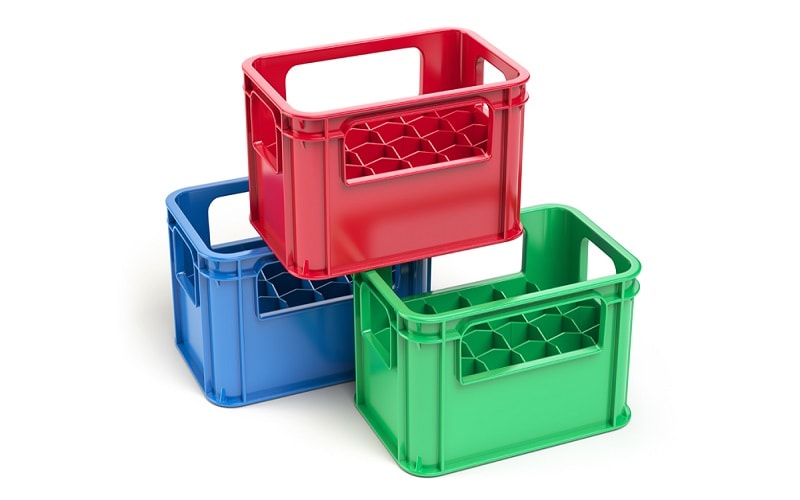
Summary
This guide has explored the top seven strongest plastics known for their impact resistance and durability.
From polycarbonate’s excellent impact strength to PEEK’s combination of high strength and chemical resistance, each material offers unique properties suitable for various applications.
By understanding the mechanical properties and specific needs of your project, you can make informed decisions about the right impact-resistant plastic to use. Choose wisely and ensure your products stand the test of time and force.
Frequently Asked Questions
What is the most impact-resistant plastic?
Polycarbonate (PC) is the most impact-resistant plastic, renowned for its exceptional strength and durability. This makes it an ideal choice for various applications where resistance to impact is crucial.
Why is chemical resistance important in plastics?
Chemical resistance in plastics is essential for ensuring durability and longevity when exposed to harsh chemicals, preventing degradation and maintaining performance in critical applications.
What are common applications of HDPE?
HDPE is commonly utilized in chemical tanks, marine construction, outdoor equipment, and prosthetics, owing to its strength and stability. Its excellent impact resistance makes it suitable for a variety of applications.
How does PEEK perform under extreme conditions?
PEEK performs exceptionally well under extreme conditions, retaining structural integrity in high temperatures and demonstrating outstanding chemical resistance, thus making it ideal for critical applications such as aerospace and medical implants.
What makes PETG a versatile material?
PETG is a versatile material due to its impressive impact strength, chemical resistance, and ease of thermoforming, which make it ideal for diverse applications like food storage components and medical devices.