Having trouble with your TPU print? This guide demystifies TPU filament and offers tips on perfecting your 3D printing process for flexible and durable results.
Understanding TPU Filament
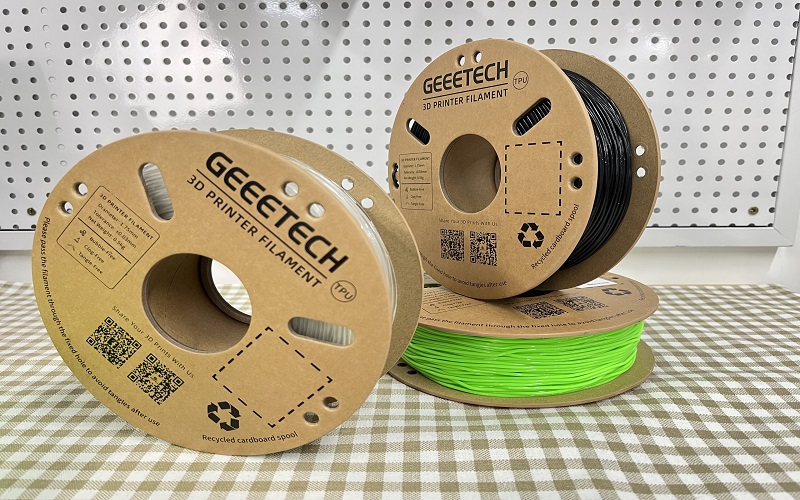
TPU filament, short for Thermoplastic Polyurethane, is a type of Thermoplastic Elastomer (TPE) recognized for its flexibility, strength, and durability. Unlike rigid filaments such as PLA, TPU, including high speed TPU, bends and flexes without breaking, making it a popular material for applications needing high elasticity and resilience.
Its rubber-like properties, especially in softer TPUs, are perfect for creating durable, flexible parts that endure significant wear and tear. Additionally, TPU filaments are increasingly popular among 3D printing enthusiasts for their unique characteristics.
Common applications for TPU filament include gaskets, seals, shock absorbers, and even flexible medical devices. Its durability surpasses that of other thermoplastic elastomers, making it a go-to choice for projects that demand both flexibility and strength, particularly with high speed TPU and softer TPUs.
Whether you’re a hobbyist creating customized parts or a professional producing high-quality flexible components, TPU filament provides a versatile and reliable solution as a popular material.
Material Properties of TPU
TPU filament has unique properties making it suitable for various applications. Its standout feature is its elasticity; TPU can stretch over five times its original shape before breaking, highlighting its flexibility and durability. This is ideal for flexible parts that need to bend and endure high stress, strain, and deformation.
TPU filament also boasts excellent abrasion resistance, withstanding continuous friction without significant wear. Its material properties include shock absorption, impact resistance, and vibration dampening, making it suitable for applications requiring flexibility and toughness.
Adjusting the infill density allows you to achieve the desired level of flexibility or rigidity, whether you’re printing soft, flexible parts or more rigid components. This enables you to flex the design to meet specific requirements.
Chemical Composition of TPU
The unique properties of TPU filament arise from its chemical composition. TPU is a block copolymer made up of hard and soft segments, with their arrangement impacting its flexibility and mechanical strength.
Different isocyanates in the production process result in varying mechanical strengths and resistance characteristics, enabling manufacturers to create TPUs with unique characteristics tailored properties for specific applications.
For instance, polyether-based TPUs are known for their superior flexibility at low temperatures, making them ideal materials for applications that require durability in cold conditions. Plastics are often utilized in such scenarios due to their versatile properties.
Preparing for TPU Printing
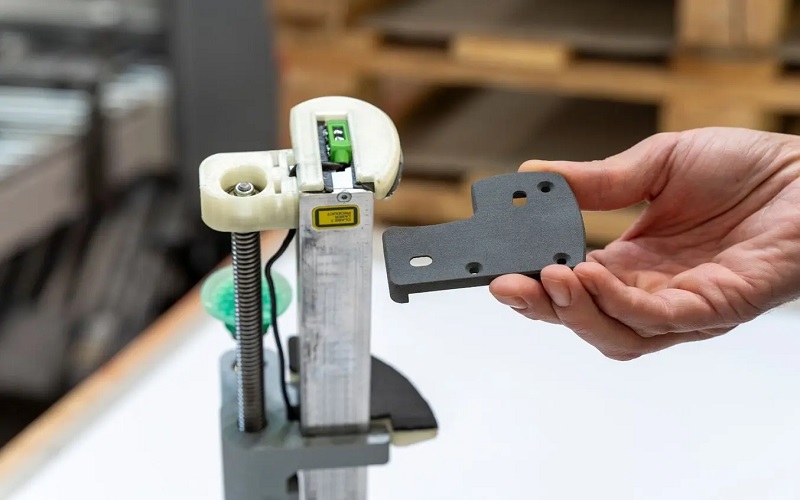
Preparing for TPU printing involves careful planning to ensure high-quality results. TPU can be challenging due to its flexible nature, leading to issues like jamming, stringing, and clogging if not handled properly. Understanding the specific requirements for printing TPU is essential for successful prints.
Store TPU filament in a dry place with a desiccant to prevent moisture absorption, as TPU is hygroscopic and degrades quickly when exposed to humidity. Drying the filament before printing can help mitigate moisture-related issues.
Selecting the right printer and adjusting the necessary print settings are also crucial steps in printed log preparation.
Choosing the Right 3D Printer
Choosing the right 3D printer is essential for successful TPU printing. Not all printers are equipped to handle TPU’s unique properties, so selecting a high-quality, industrial-grade printer can significantly enhance the final output quality. The extruder is one of the most critical components to consider.
Direct drive extruders are highly recommended for TPU printing as they prevent filament buckling by shortening the filament path. While firmer TPU varieties may print well with a bowden extruder, direct drive extruders generally offer better control and reduce the risk of filament coiling or jamming. Additionally, using a bowden tube can also be beneficial in certain setups.
Using a printer compatible with TPU and equipped with the right extruder can significantly improve the quality and consistency of your prints and allow you to successfully print.
Essential Printer Settings for TPU
Fine-tuning your printer settings is crucial for successful TPU printing. The recommended nozzle temperature for TPU filament typically ranges between 210-250 °C, depending on the brand.
Adjusting the extruder temperature can help mitigate under-extrusion issues, while inadequate temperatures may lead to clogs or bubbles in your prints.
Maintaining a consistent and relatively low print speed, or even slower speeds, is also important for TPU printing. Keeping the print speed at or below 25mm/s helps avoid clogs due to TPU’s softness. Additionally, setting a low retraction distance of about 2mm and a low retraction speed can ensure smooth extrusion and reduce the risk of filament buckling.
Carefully adjusting these settings can help you achieve high-quality TPU prints with minimal issues.
Optimizing the TPU Printing Process
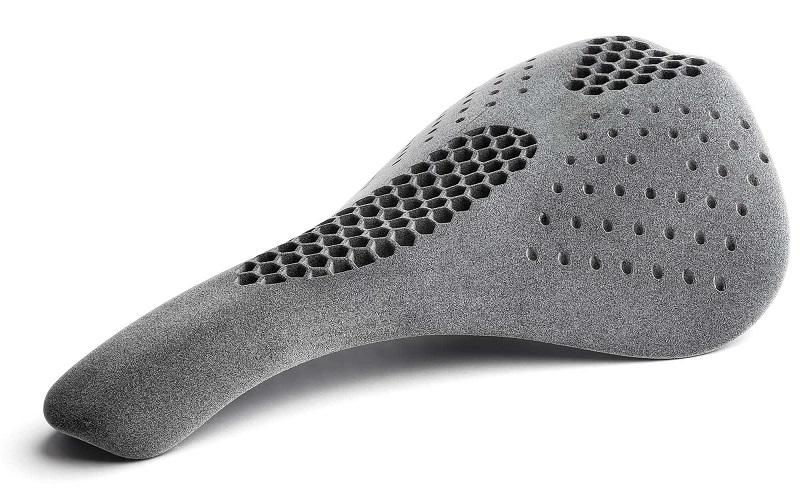
Optimizing the TPU printing process involves various techniques to ensure the best print quality. Given TPU’s flexibility, maintaining consistent filament flow can be challenging, leading to issues like warping and print failure. However, several strategies can help mitigate these problems and enhance your overall printing experience.
Applying heat treatments such as annealing can strengthen TPU parts and improve their flexibility. Additionally, techniques like sanding, polishing, and tumbling can enhance the surface smoothness of TPU prints, although TPU’s ductility can make these processes somewhat challenging.
Coatings can also improve the durability and appearance of TPU parts, offering additional chemical and UV protection.
Managing Print Speed and Retraction
Managing print speed and retraction is essential for high-quality TPU prints. The ideal print speed for TPU is between 15 to 20 mm/s, starting slower for better control and fewer issues. A slow and consistent feed rate improves TPU print quality and helps mitigate problems such as stringing.
To prevent clogs and manage prints effectively, keep the retraction distance for TPU under 1 millimeter and minimize retraction speed. Controlling retraction settings can significantly improve the surface finish of TPU prints, reducing stringing and ensuring smoother, more uniform results.
Ensuring Bed Adhesion
Proper bed adhesion is crucial for successful TPU printing. Using a glue stick on glass or blue painter’s tape as a build surface can significantly improve adhesion. Ensure the print bed is adequately heated, even, and clean to facilitate proper adhesion for TPU prints.
Regularly checking if the first layer of your TPU print has sufficient squish can enhance adhesion. Avoid using rafts for TPU printing as they can inhibit bed adhesion. Proper preparation and maintenance of the print bed can help achieve consistent and reliable results.
Handling Common TPU Printing Issues
Handling common TPU printing issues is crucial for optimizing the printing process. Stringing and oozing are frequent challenges with TPU that can lead to imperfections in the final print, including excessive stringing. Using tools such as pliers and hobby knives can be effective for removing supports and cleaning up prints.
Maintaining a clean print environment and regularly checking your printer settings can help prevent and mitigate common printing problems. By being proactive and addressing issues as they arise, you can ensure your TPU prints are of the highest quality and free from defects, resulting in zero problems.
Post-Processing TPU Prints
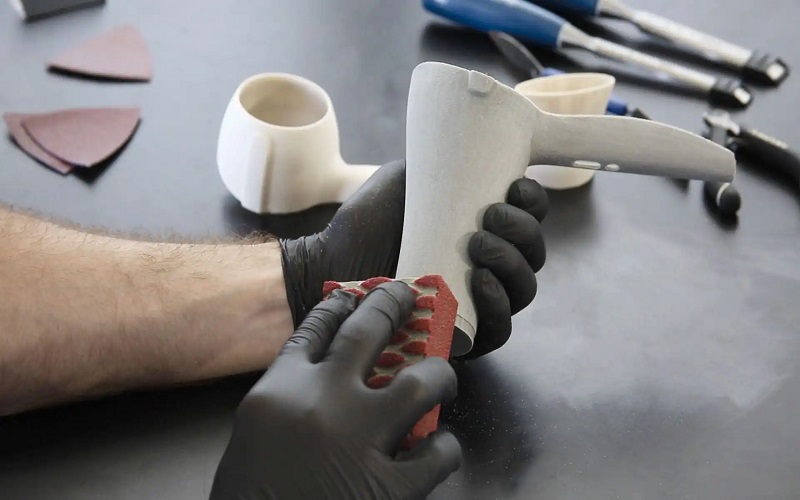
Post-processing TPU prints can be challenging due to the material’s ductility. Unlike more rigid filaments, TPU does not respond well to traditional post-processing methods like sanding, painting, or coating. However, several techniques can still enhance the appearance and functionality of your TPU prints.
Cooling TPU prints can help them contract and pop off the bed, making removal easier. A flexible, thin, and flat tool, such as a plastic scraper or painter’s knife, is recommended for removing TPU prints from the bed without causing damage.
Once removed, cleaning the prints with warm water and mild soap removes any residual debris or support structures.
Removing TPU Prints from the Bed
Removing TPU prints from the bed requires careful handling to avoid damaging the print. Cooling the print helps it contract, making removal easier. If glue stick or hairspray was used on the bed before printing, cleaning the bed with warm water and mild detergent can remove any residue.
A flexible, thin, and flat tool, such as a plastic scraper or painter’s knife, is recommended for removing TPU prints from the bed. Flexing the surface can often allow the print to be easily removed without damaging either the print or the bed.
Cleaning and Support Removal
Cleaning and support removal are essential steps in post-processing TPU prints. Start by removing any support structures from the print. Washing the print with warm water and mild soap removes any remaining debris or residue.
Using a soft brush effectively cleans the print without causing damage, ensuring a smooth and clean final product.
Smoothing TPU Surfaces
Smoothing TPU surfaces can be challenging due to the material’s durability and solvent resistance. One popular DIY method is using a heat gun, which allows for partial melting of the material to achieve a smoother surface.
However, this process requires careful control to avoid damaging the print, and proper ventilation and personal protective equipment (PPE) should be used to ensure safety.
Taking these precautions can help you achieve a smooth and professional finish on your TPU prints.
Storing TPU Filament
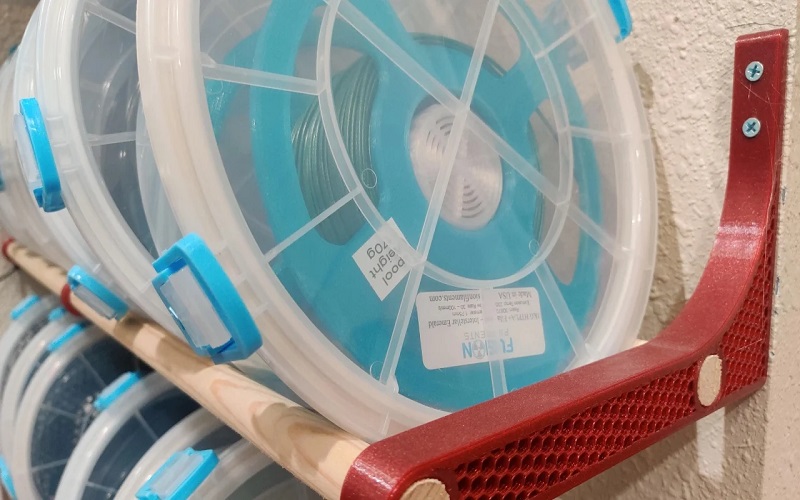
Proper storage of TPU filament is crucial for maintaining its quality and preventing printing issues. TPU is hygroscopic, meaning it absorbs moisture quickly, leading to problems like stringing and holes in your prints. To prevent this, store TPU filament in a dry and dark environment to prevent degradation.
One effective method is keeping TPU filament in a sealed bag with a desiccant to mitigate moisture absorption. Storing the filament in a humidity-controlled environment can significantly extend its shelf life and ensure optimal printing performance.
Taking these steps ensures that your TPU filament remains in excellent condition and ready for use.
Using Silica Gel and Filament Dryers
Using silica gel packs and filament dryers preserves the quality of TPU filament. Silica gel packs absorb moisture, maintaining the filament’s integrity during storage. Placing a few silica gel packs in the storage container with your TPU filament can significantly prevent moisture absorption.
Filament dryers use controlled heating for thorough drying of the file filament before use, especially beneficial if the filament has already absorbed some moisture.
Proper moisture control is essential for maintaining the quality of TPU filament, as moisture can lead to issues like stringing, under-extrusion, and poor print quality. By using silica gel and filament dryers, you can ensure that your TPU filament remains dry and ready for high-quality printing.
Proper Storage Conditions
Storing TPU filament in the right conditions is crucial for long-term quality. The filament should be kept in a cool and dry environment to maintain its integrity and prevent degradation. Vacuum-sealed bags or airtight containers with desiccant are ideal for preventing moisture ingress and ensuring the filament remains dry.
For optimal performance, you can also dry the filament using an oven or a filament dryer prior to printing. By adhering to these storage practices, you can significantly extend the shelf life of your TPU filament and ensure consistent print quality.
Troubleshooting TPU Print Quality
Troubleshooting TPU print quality involves addressing common issues that arise during the printing process. Common challenges include stringing, holes, and popping or sizzling sounds during printing, often caused by moisture in the filament. The flexibility and elasticity of TPU create unique printing challenges that require careful adjustments to achieve the best results.
To improve TPU print quality, it’s essential to address moisture issues by ensuring the filament is properly dried and stored.
Additionally, fine-tuning printer settings to accommodate TPU’s properties can help achieve better results. By understanding and addressing these common issues, you can ensure high-quality TPU prints with fewer defects and imperfections.
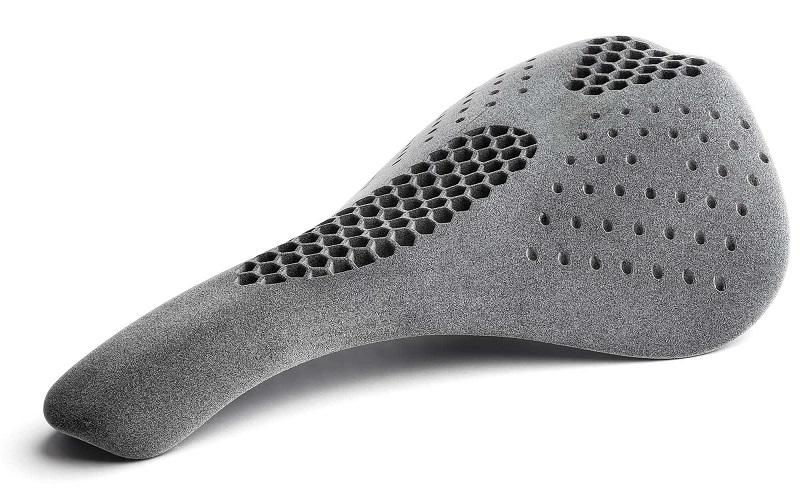
Addressing Extrusion Problems
Extrusion problems are a frequent issue when printing with TPU filament. Under-extrusion can occur due to insufficient temperature, filament buckling, or coiling in the extruder. To avoid these issues, reducing retraction settings can help prevent clogs and under-extrusion. Regularly cleaning the nozzle can also help prevent over-extrusion, ensuring a smooth and consistent filament flow.
Using the right shore hardness of TPU, typically between 75A and 98A, can help better control the extrusion process. Ensuring that your printer settings are properly calibrated and that the filament path is clear can significantly improve the extrusion quality and overall print results, making TPU an ideal material for various applications.
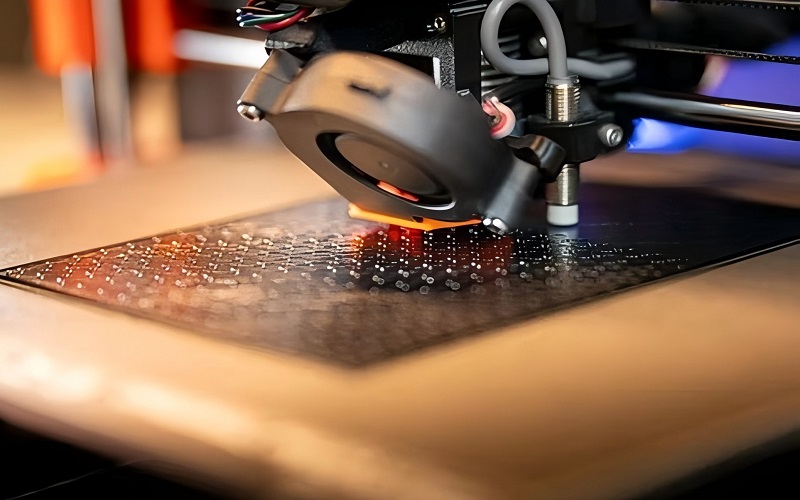
Improving Surface Quality
Improving the surface quality of TPU prints involves addressing moisture and fine-tuning printer settings. Absorption of too much moisture during storage can cause a blurred or uneven surface on TPU prints.
To enhance surface quality, consider the following steps:
- Fine-tune retraction settings
- Use support structures
- Choose a lower layer height
- Maintain an optimal printing temperature around 230 °C
By taking these steps, you can create smooth, high-quality surfaces on your TPU prints.
Summary
In summary, mastering TPU printing requires a comprehensive understanding of the material, careful preparation, and meticulous attention to detail during the printing process.
From understanding the unique properties and chemical composition of TPU to selecting the right printer and fine-tuning your settings, each step plays a crucial role in achieving high-quality TPU prints. Proper storage and post-processing techniques further ensure that your prints maintain their integrity and functionality.
By following the guidelines and tips outlined in this guide, you can overcome the challenges of TPU printing and unlock the full potential of this versatile material. Whether you’re creating flexible parts for personal projects or professional applications, TPU filament offers endless possibilities for innovation and creativity. Embrace the flexibility and strength of TPU and elevate your 3D printing projects to new heights.
Frequently Asked Questions
What are the main advantages of using TPU filament for 3D printing?
Utilizing TPU filament for 3D printing provides significant advantages such as outstanding flexibility, strength, and durability, making it particularly well-suited for applications like gaskets, seals, and flexible medical devices. These properties enhance the performance and longevity of the printed items.
How should I store TPU filament to maintain its quality?
To maintain the quality of TPU filament, it should be stored in a cool, dry environment using a vacuum-sealed bag or an airtight container with desiccant to prevent moisture absorption.
What printer settings are recommended for TPU printing?
For optimal TPU printing, it is advised to set the nozzle temperature between 210-250 °C, maintain a print speed at or below 25mm/s, and use a low retraction distance of approximately 2mm.
How can I improve bed adhesion for TPU prints?
To enhance bed adhesion for TPU prints, apply a glue stick or blue painter’s tape on a heated, clean, and level print bed. This method effectively increases the likelihood of successful prints.
What are common issues when printing with TPU and how can I address them?
Common issues when printing with TPU include stringing, under-extrusion, and poor surface quality. You can address these by properly drying the filament, fine-tuning printer settings, and maintaining optimal printing conditions.