TPU molding involves using thermoplastic polyurethane to manufacture parts that are both flexible and durable. This adaptable process is crucial in producing a range of products, from automotive components to medical devices.
In this article, we delve into what TPU molding is, its advantages, and how to optimize your molding techniques for the best results.
Understanding TPU Molding
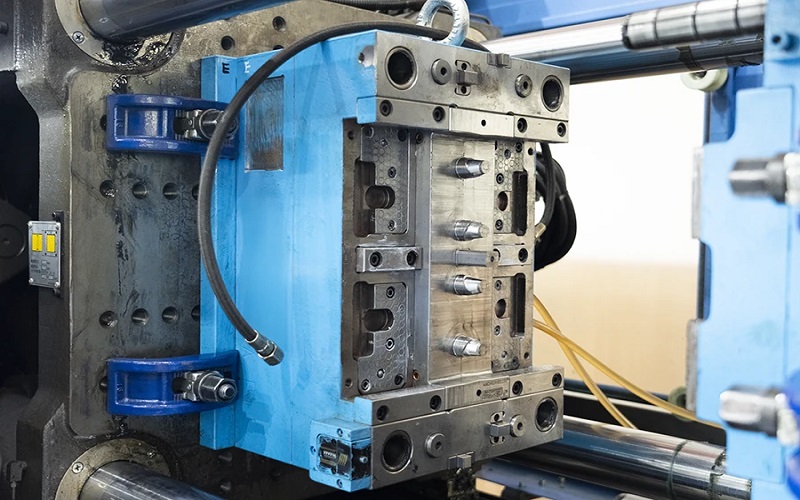
The process of TPU molding involves the use of thermoplastic polyurethane to produce parts that are both flexible and durable. This material stands out for its ability to be remelted and reshaped, setting it apart from other thermoplastic materials.
The TPU molding process includes introducing urethane polymer into a mold and allowing it to cure, which can be achieved through various methods such as injection molding, blow molding, compression molding, and extrusion molding. Among these, the TPU injection molding process is particularly suited for later-stage prototyping and both low to high-volume production runs, making it a versatile choice for manufacturers.
The polyurethane injection molding process, while efficient, often has a slower cycle time compared to other molding techniques, including plastic injection molding. This makes it more suitable for lower production runs where precision and quality are paramount. Understanding these nuances is crucial for optimizing the molding process and ensuring high-quality results.
TPU molding is not a one-size-fits-all solution but a highly adaptable process that can be tailored to meet specific requirements. This adaptability is what makes TPU an invaluable material in various industries. To appreciate its full potential, we need to delve deeper into what TPU is and the benefits it brings to the molding process.
What is TPU?
Thermoplastic polyurethane (TPU) is an organic polymer that can be remelted and reshaped, distinguishing it from thermoset polyurethane. It combines the best attributes of metal, rubber, and plastic, offering a longevity that surpasses traditional plastics.
TPU is known for being lightweight, flexible, resilient, durable, and cost-effective, making it an ideal material for a wide range of applications, including polyurethane resins.
The main components used to form TPU include di- or poly-isocyanate and polyol, which contribute to its superior resistance to impact, abrasion, radiation, and cold flow compared to rubber. These unique properties enable TPU moldings to perform exceptionally well in demanding environments, making them suitable for various industrial applications.
Benefits of TPU in Molding
One of the primary advantages of using TPU in injection molding is its excellent abrasion resistance, which ensures durability across various applications. TPU also exhibits remarkable chemical resistance, maintaining its properties even when exposed to a range of chemical agents, which makes it suitable for diverse environments without compromising its integrity. Additionally, its lightweight and flexible nature enhances the manufacturing processes and applications of molded parts.
The injection molding process facilitated by TPU supports both low and high-volume production, allowing manufacturers to achieve finer details and tighter tolerances in their injection molded products.
This versatility results in higher quality parts with minimal finishing required, and defective parts can be regrinded, melted, and reused, ensuring more efficient manufacturing and reduced waste.
Applications of TPU Molding
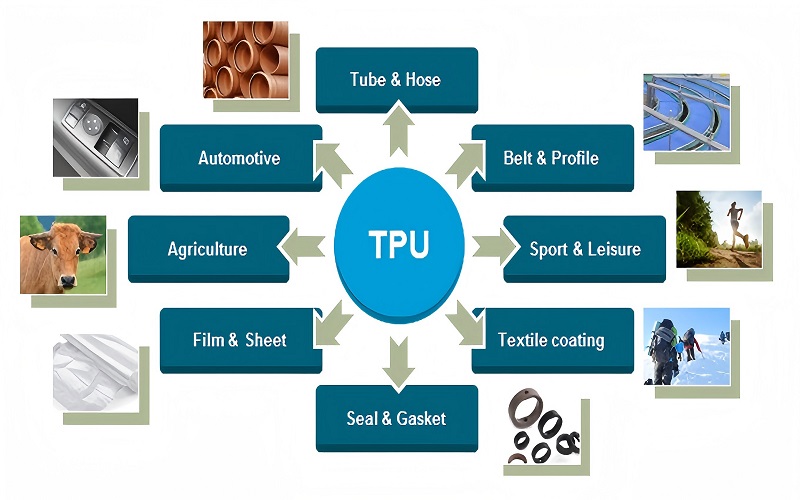
Before: TPU molded products are widely utilized in industries such as automotive, medical devices, and consumer electronics. In the automotive sector, TPU is used for components that require flexibility and durability, while in the medical field, it is employed in devices that benefit from its biocompatibility and resilience. Consumer electronics also leverage TPU for its ability to provide protective, shock-absorbing casings.
After: TPU molded products are widely utilized in various industries, including:
- Automotive: TPU is used for components that require flexibility and durability.
- Medical devices: It is employed in devices that benefit from its biocompatibility and resilience.
- Consumer electronics: TPU provides protective, shock-absorbing casings.
Beyond these industries, TPU is also found in applications like soundproofing padding, mobile phone casings, and agricultural equipment. Micro-molding, a specialized technique for producing very small TPU components with high precision and tight tolerances, is particularly crucial in the medical and electronics industries.
This ability to create intricate and precise components highlights the versatility and importance of TPU molding in modern manufacturing.
The TPU Injection Molding Process
The TPU injection molding process is segmented into three distinct phases: pre-molding, injection, and ejection. Each phase plays a critical role in ensuring the quality and efficiency of the final product.
Controlling factors such as temperature, moisture levels, and mold design is essential for successful TPU molding. These controls help in optimizing process parameters, including temperature and pressure, which are crucial for achieving consistent quality.
TPU’s moisture absorption can lead to defects such as bubbles or surface irregularities if not properly managed. Therefore, stringent testing and rigorous inspection methods are employed throughout the process to ensure that the products meet specified standards. Understanding each phase and its importance helps in refining the injection molding process, leading to better quality and efficiency.
Let’s dive into the specifics of each phase, starting with material preparation.
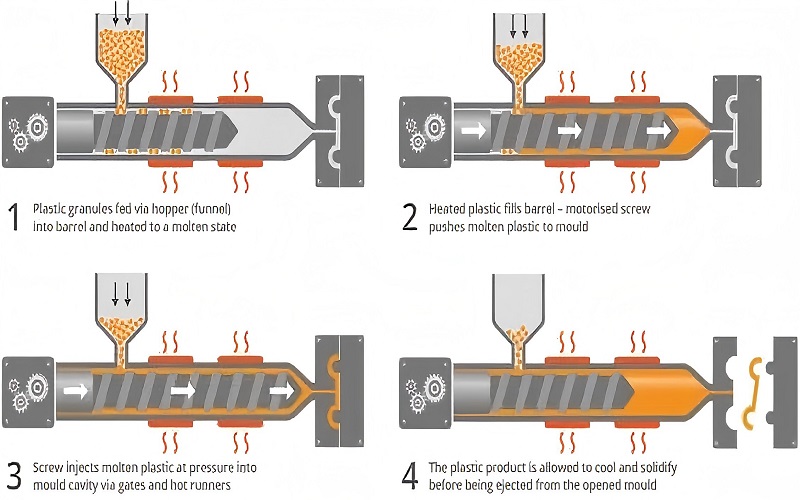
Material Preparation
Before TPU can be used in the injection molding process, the pellets must be thoroughly dried to minimize defects caused by moisture. This step is crucial to prevent issues such as bubbles or surface irregularities in the final product.
Proper material preparation ensures that the mechanical properties of the TPU are maintained, leading to high-quality components.
Machine Setup
Setting up the injection molding machine involves critical parameters such as temperature, pressure, and time. The general range of injection pressure for TPU is typically between 20 to 110 MPa, which is essential for successful molding.
Controlling barrel, nozzle, and mold temperatures significantly influences the flow and cooling of TPU during the molding process. For instance, the nozzle temperature should be slightly lower than the maximum barrel temperature to facilitate proper melt flow without solidification.
Additionally, the recommended screw speed for TPU injection molding is approximately 2050 to 2080 r/min to ensure effective processing. The injection volume should typically be within the range of 40% to 80% of the rated volume for effective filling and performance. Equipping the nozzle with controlled heating tape is also recommended to prevent material solidification and ensure consistent flow.
Mold Design
The design of the mold is a critical factor in the TPU injection molding process. Proper design of gates and vents ensures the removal of gas and prevents defects during the injection process.
The typical range of wall thicknesses for urethane casting is 1 to 5 mm, which should be carefully planned to optimize part performance. Designers should determine the minimum and maximum wall thickness based on the specific material to ensure quality and consistency.
Using polished molds and appropriate mold release agents can enhance the surface finish of TPU components. Employing precision machinery in mold creation minimizes gaps that can negatively impact the surface finish of molded TPU parts.
Streamlining the design of molded parts can lead to fewer required molds, thereby decreasing overall expenses in TPU molding.
Key Considerations in TPU Molding
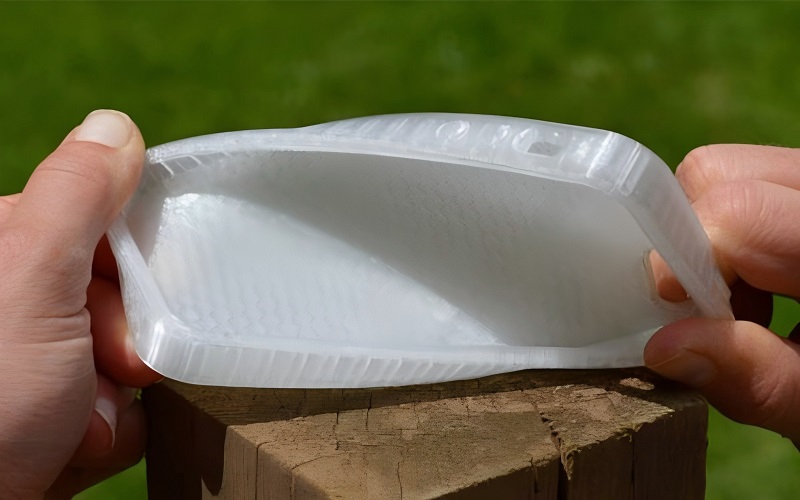
Optimizing the TPU molding process is essential to achieve high production efficiency and product quality. Advanced TPU molding techniques focus on integrating innovative methods to enhance production speed and improve product quality.
However, common issues like shrinkage, warpage, and flash in the mold cavity can significantly affect the quality of the final product.
By adjusting processing parameters such as temperature and pressure, manufacturers can effectively reduce these issues and produce high-quality molded urethane products. Thermoplastic polyurethane can also be tailored to achieve desired properties by adjusting the ratio of hard and soft segments.
Let’s explore some of these key considerations in detail.
Shrinkage and Warpage
The shrinkage of molded TPU parts is influenced by factors such as hardness, part thickness and shape, molding temperature, and mold temperature. The typical shrinkage rate for TPU ranges from 0.005 to 0.020 cm/cm, which can vary based on these factors.
TPU hardness affects shrinkage rates; shrinkage decreases with increasing thickness for hardness levels between 78A to 90A, and slightly increases for hardness 95A to 74D.
Thermal expansion in TPU can lead to tolerance issues when the material is heated, which may cause warpage in the final product. High coefficients of thermal expansion in polyurethanes can create challenges in maintaining precision during urethane casting.
Maintaining a consistent wall thickness in injection molding is essential for ensuring part consistency. It also helps with proper stress distribution and reduces the likelihood of defects.
Cycle Time Optimization
Effective cycle time reduction can significantly enhance productivity without sacrificing the quality of TPU parts. Adjustments to cooling time are essential for optimizing cycle time in TPU molding.
The cooling rate of the mold influences overall production efficiency, making efficient mold design and cooling time adjustments crucial strategies for minimizing cycle times in TPU molding.
Post-Processing Techniques
Post-processing steps like annealing are critical in reducing internal stresses within TPU products. Annealing TPU products helps relieve internal stresses, thereby enhancing their mechanical properties and overall performance.
Improving the mechanical properties of TPU can be achieved through techniques like surface treatment and annealing.
Advanced TPU Molding Techniques
Advanced TPU molding techniques offer innovative solutions for creating high-quality products with complex shapes and tight tolerances. These techniques include:
- Overmolding
- Insert molding
- Two-shot molding
- Micro-molding
Each technique offers unique benefits and applications.
Screw type injection molding machines are recommended for TPU to ensure efficient processing. Additionally, glass fibers can be added in reinforced reaction injection molding (RRIM) to enhance the strength and durability of TPU products. Let’s delve into each of these advanced techniques.
Overmolding and Insert Molding
TPU overmolding and insert molding are processes used to create multi-material parts, enhancing the functionality and strength of the final product.
Overmolding involves molding TPU over another material, such as metal or another plastic, while insert molding places a pre-formed part into the mold before injecting TPU around it. These techniques are particularly useful for producing ergonomic grips, seals, and other components that require a combination of materials.
It is crucial to confirm the experience of the injection mold and product suppliers when undertaking projects involving TPU overmolding and insert molding. Material selection is also important; for instance, if the TPU used contains lubricant, it is not suitable for insert molding. Ensuring compatibility between the materials and the molding process can prevent defects and enhance product performance.
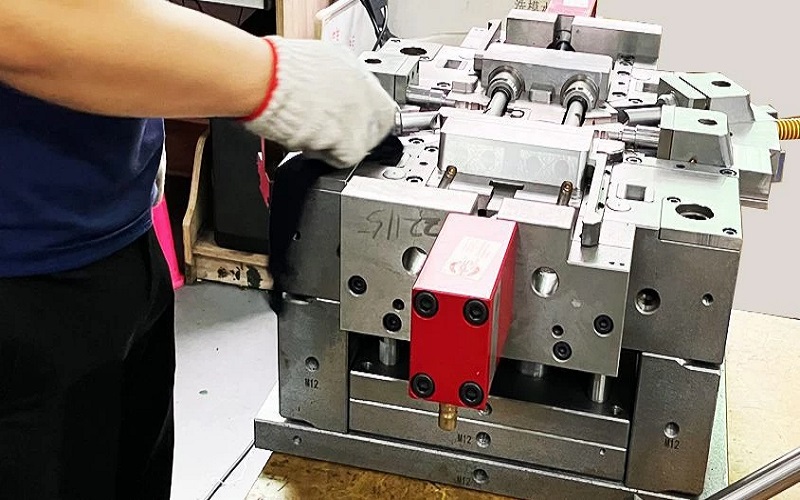
Two-Shot Molding
The two-shot molding process enables the creation of complex part geometries and multi-colored components in a single molding cycle. This process involves injecting two different materials into a mold in a single cycle, allowing manufacturers to create parts with diverse material properties and enhanced aesthetics. For example, a soft TPU layer can be molded over a harder plastic core to produce a part with both rigidity and a comfortable grip.
Two-shot molding allows for the integration of intricate designs and multiple colors, often enhancing product aesthetics and functionality. This technique is widely used in consumer electronics, automotive interiors, and medical devices where both appearance and performance are critical.
Micro-Molding
Micro-molding techniques are designed to produce small TPU components with exacting tolerances, suitable for precision applications. This process is especially important in industries like medical devices and electronics, where very small components with high precision are required.
Micro-molding enables the producing components of intricate, tiny parts that meet stringent specifications, enhancing the performance and reliability of the final products.
Common Challenges and Solutions in TPU Molding
Challenges in TPU molding can include issues like flow lines, flash, and poor surface finish, each requiring targeted solutions. Addressing these issues is crucial for maintaining the quality and appearance of the final products.
By understanding the root causes of these challenges and implementing effective solutions, manufacturers can optimize their molding processes.
Tackling Flow Lines
Adjusting the injection speed and optimizing mold temperature can significantly reduce the occurrence of flow lines in TPU parts. Higher mold temperatures facilitate better material flow during injection, reducing the likelihood of flow lines.
Additionally, choosing the right gate design can control the flow of material into the mold, helping to minimize flow line defects.
Reducing Flash
Achieving precise mold alignment is vital for minimizing flash during the TPU closed mold molding process. Proper mold alignment and maintaining the correct clamping force are crucial methods to minimize flash during TPU molding.
Combining accurate mold alignment with optimal clamping force creates an effective strategy to minimize flash in TPU molding.
Improving Surface Finish
Using appropriate mold release agents can enhance the surface quality of TPU parts. Achieving a smooth surface finish is crucial for the aesthetic and functional quality of TPU parts. Polishing the mold surface can significantly enhance the final surface finish of the molded TPU parts.
Implementing a combination of mold polishing and proper mold release agents is essential for achieving the best surface finish in TPU molding.
Quality Control and Testing in TPU Molding
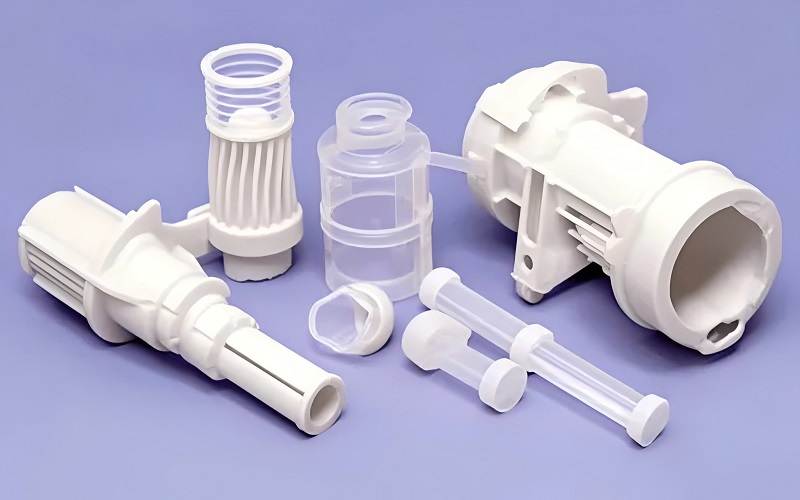
Quality control in TPU molding is essential to ensure that the final products meet specified standards and performance criteria. This involves systematic testing and rigorous inspection methods to maintain consistent quality. The mold temperature significantly influences the intrinsic properties of TPU products. Its effect on the overall quality cannot be understated.
Uneven crystallization can lead to internal stress in TPU, resulting in mechanical property degradation, surface silvering, deformation, and cracking. To mitigate these issues, annealing TPU products can eliminate internal stress and improve their mechanical properties.
Mechanical Properties Testing
Testing for tensile strength, elongation, and hardness of TPU parts is essential to ensure that the material meets performance standards. Tensile strength testing measures how much force a TPU molded part can withstand before breaking, while elongation at break indicates the extent to which TPU materials can stretch before failure.
Hardness testing assesses the resistance of TPU molded parts to indentation or surface deformation.
Dimensional Accuracy
Coordinate Measuring Machines (CMM) are commonly used for high-precision dimensional checks in TPU parts. CMM ensures the precise measurement of molded TPU parts, and laser scanning technology offers non-contact measurement solutions for ensuring dimensional accuracy in TPU molds.
Dimensional accuracy is crucial in TPU molding to ensure that parts fit and function as intended. For injection molding, dimensional tolerances are generally +/- .005” for the first inch. For every inch that follows, the tolerance is usually +/- .002”.
Visual Inspection
Conducting visual inspections is crucial for detecting surface defects and confirming the aesthetic quality of molded TPU products. This step ensures that any visible issues are identified and corrected before the products reach the end user, maintaining high standards of quality and appearance.
Cost Considerations in TPU Molding
Cost considerations in TPU molding are a vital aspect of the manufacturing process. The primary expense in TPU molding is often attributed to the tooling costs associated with mold creation. Design complexity of the parts being produced can also significantly influence TPU molding costs.
By understanding and managing these costs, manufacturers can optimize their production processes and ensure profitability. Let’s explore the specific cost factors in detail.
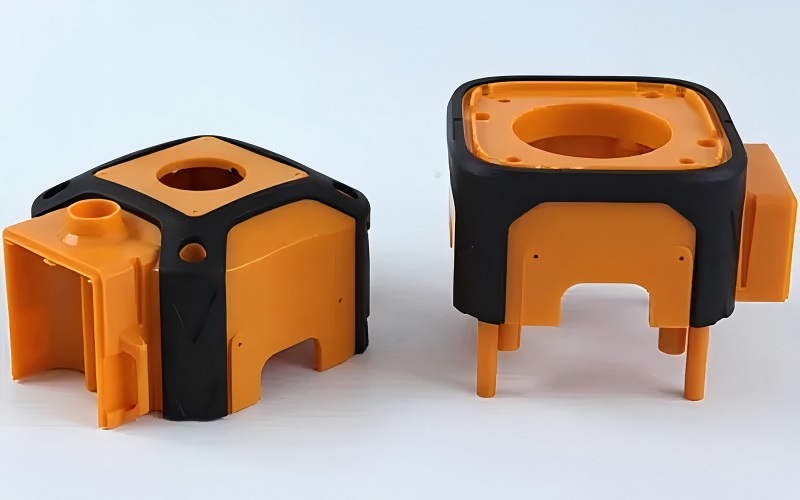
Tooling Costs
Tooling costs can vary significantly based on the complexity of the mold and the materials used. Simple molds can cost as little as $100, while complex molds may exceed $100,000.
3D printed molds can be produced at a fraction of the cost of traditional aluminum or steel molds, especially for low-volume production. CNC machining and electrical discharge machining are common methods for producing precision molds that are crucial for TPU molding.
Production Costs
Material selection plays a crucial role in determining production costs, as different materials have varying prices and characteristics. Using materials with cost-effective properties can significantly reduce the total expenses in the production process.
Cost Optimization Strategies
Implementing lean manufacturing principles can help minimize waste and reduce production costs in TPU molding. These strategies focus on streamlining processes, reducing material waste, and optimizing production efficiency, ultimately leading to cost savings.
Sustainability in TPU Molding
Sustainability is becoming increasingly important in the TPU molding industry, driving the adoption of eco-friendly practices. Unlike rubber, TPU is recyclable and does not require special additives for processing. By adopting recycling practices and using sustainable materials, the TPU molding industry can significantly lessen its environmental footprint.
Bio-TPU is a thermoplastic elastomer derived from renewable resources, such as vegetable oils and food waste, reducing environmental impact. The production of Bio-TPU is expected to grow by 20% annually over the next five years, making it a more sustainable alternative compared to traditional TPU.
Let’s explore the specific aspects of sustainability in TPU molding.
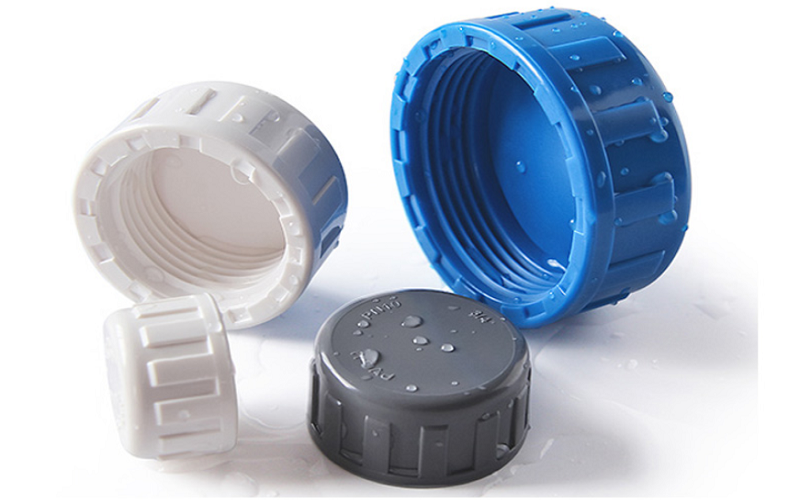
Recyclability of TPU
Mechanical recycling methods, such as grinding and extruding, can effectively process TPU waste back into usable materials. Thermoplastic polyurethane (TPU) recycling is essential for sustainable practices and minimizing waste in the production process.
Energy-Efficient Processes
Utilizing advanced machinery can significantly lower energy consumption during TPU molding processes. Implementing lower processing temperatures is a key strategy for enhancing energy efficiency in TPU molding.
The combined implementation of advanced machinery and lower processing temperatures offers a comprehensive approach to energy efficiency in TPU molding.
Sustainable Material Options
Bio-based TPU materials are an increasingly popular alternative to conventional fossil-derived polymers. Recycled TPU can serve as a viable option for sustainable materials in molding applications.
Recycled TPU can be derived from waste produced in the footwear industry, maintaining strong mechanical properties.
Summary
In summary, TPU molding offers a versatile and efficient solution for producing high-quality, durable parts across various industries. From material preparation and machine setup to advanced molding techniques and sustainability practices, each aspect of the TPU molding process plays a crucial role in achieving optimal results.
By understanding and implementing the best practices discussed in this article, manufacturers can enhance their production efficiency, reduce costs, and contribute to a more sustainable future.
As we move forward, embracing innovative techniques and eco-friendly practices will be key to staying competitive in the ever-evolving manufacturing landscape. Whether you’re optimizing for cost, quality, or sustainability, the insights provided here will guide you in harnessing the full potential of TPU molding. Let’s continue to push the boundaries of what’s possible with TPU and create products that not only meet but exceed expectations.
Frequently Asked Questions
What is TPU and why is it used in molding?
TPU, or thermoplastic polyurethane, is a versatile organic polymer recognized for its flexibility and durability. Its capacity to be remelted and reshaped makes it an excellent choice for high-quality molding applications.
What are the benefits of using TPU in injection molding?
Using TPU in injection molding provides outstanding abrasion and chemical resistance, along with flexibility that supports both low and high-volume production. This material enables the creation of parts with finer details and tighter tolerances, ensuring higher quality with minimal finishing needed.
What industries commonly use TPU molded products?
TPU molded products are commonly utilized in the automotive, medical devices, and consumer electronics industries, as well as for applications such as soundproofing padding and mobile phone casings. Their versatility makes them suitable for various sectors, including agriculture.
How can common challenges in TPU molding, such as flow lines and flash, be addressed?
To effectively address common challenges in TPU molding such as flow lines and flash, it is essential to adjust injection speed and optimize mold temperature while also ensuring precise mold alignment and appropriate clamping force. Additionally, utilizing suitable mold release agents and polishing molds can enhance the surface finish.
What sustainable practices are being adopted in TPU molding?
Sustainable practices in TPU molding encompass recycling TPU waste through mechanical methods, utilizing bio-based TPU materials, and employing advanced machinery to improve energy efficiency. These measures contribute significantly to environmental protection while maintaining productivity.