Understanding the types of injection molding can help you choose the best method for your manufacturing needs. This article provides a clear overview of the most common techniques, their advantages, and typical uses.
Gas-Assisted Injection Molding
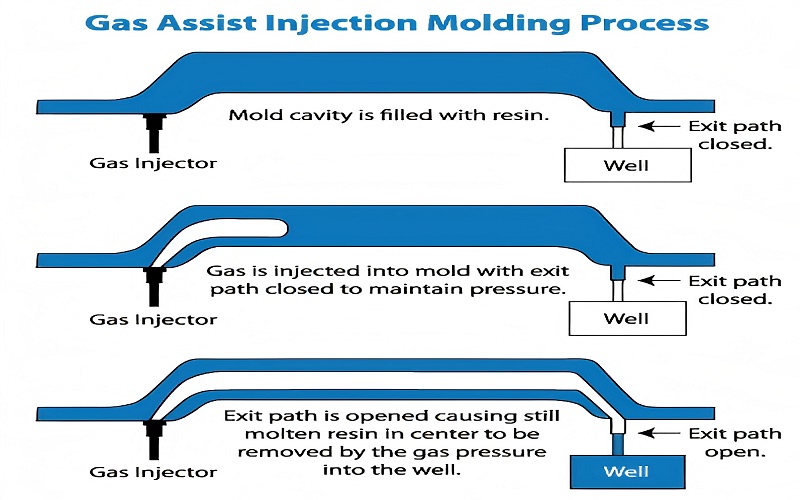
Gas-assisted injection molding is a fascinating technique that integrates pressurized gas into the injection process to create hollow sections within plastic parts. This method is particularly advantageous for manufacturing large and complex components, as it significantly enhances structural integrity while reducing material usage. Imagine the potential savings on your next injection molding project with material requirements slashed by up to 35%.
Molten plastic flows are first injected into the mold cavity during the plastic injection molding process. Then, gas is introduced to push the plastic part into the mold walls, creating a hollow core.
Ideal for large parts, hollow products, and porous designs, this technique, including the two plate mold, is widely used across various industries.
Beyond material savings, gas-assisted injection molding offers improved design flexibility. The hollow sections lighten the parts and enhance their performance and durability. Injection molded manufacturers benefit from optimized production processes and high-quality products.
Thin-Wall Injection Molding
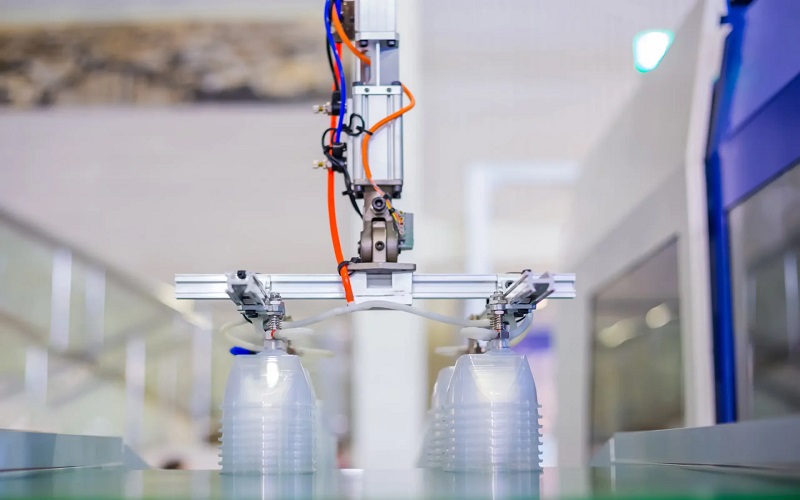
Thin-wall injection molding stands out as a pivotal technique for producing lightweight parts. With reduced material usage and faster cycle times, this method has become essential for industries requiring high-speed production and cost efficiency. Maintaining uniform wall thickness is crucial to prevent warping and ensure consistent cooling, which is essential for this method’s success.
Thin-wall injection molding relies on specialized high-pressure equipment. It ensures that the molten plastic fills the thin cavities swiftly, before the material begins to solidify. This rapid filling process is crucial for maintaining the integrity and quality of the final product, especially when using an injection mold.
Material choice is crucial in thin-wall injection molding. High-density polyethylene and polypropylene are often preferred due to their superior flow characteristics, which are essential for creating parts with narrow dimensional tolerances. From plastic material toys to storage containers, the applications of this injection moulding material technique are vast and varied.
Liquid Silicone Rubber (LSR) Injection Molding
Liquid silicone rubber (LSR) injection molding is a game-changer in the production of medical products, sealing devices, and even baking equipment. Specialized equipment, such as heated mold cavities, mixers, and metering systems, are needed to handle silicone’s unique properties. The result? Intricate designs and reduced manufacturing challenges, thanks to LSR’s ability to flow into thin sections.
Known for its versatility, LSR maintains its properties across a wide temperature range from -60°C to 180°C and offers excellent chemical resistance. This makes it suitable for a variety of applications, from medical devices that need to withstand sterilization processes and harsh chemicals to consumer products exposed to extreme temperatures.
One of the standout features of LSR injection molding is its high level of automation. This enhances production consistency and minimizes contamination risks.
However, the vulcanization process in LSR is irreversible, which can pose challenges for recycling. Still, the ability to achieve high-volume production with minimal waste makes LSR injection molding highly efficient.
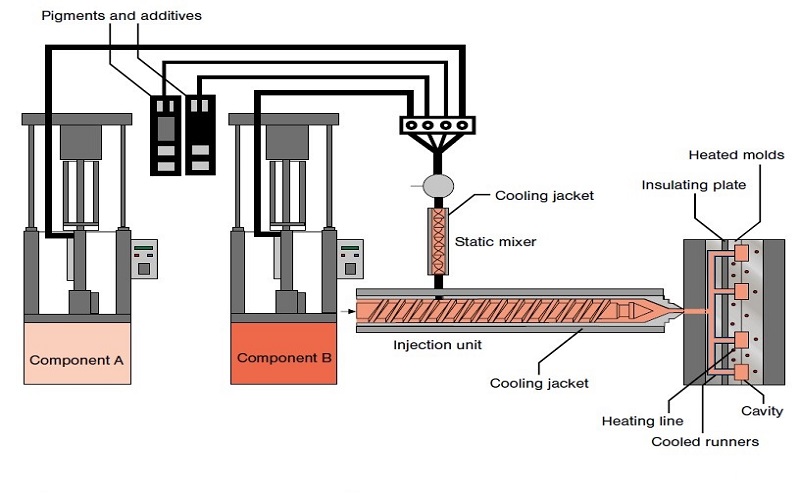
Structural Foam Injection Molding
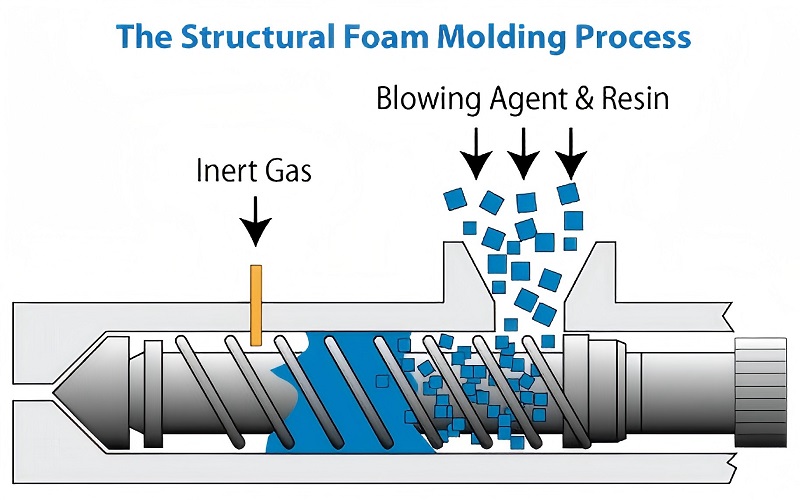
Structural foam injection molding offers a unique approach to creating lightweight, yet strong parts. Incorporating a chemical blowing agent with thermoplastic creates a foam core within the molded part, making products 10-30% lighter than those produced by traditional methods. This technique is particularly beneficial for high-volume production of larger parts, providing significant cost savings.
Structural foam injection molding offers benefits beyond weight reduction. The parts produced are not only lightweight but also flexible and robust. This makes them ideal for applications where strength and durability are paramount.
This method does come with its own set of challenges. The cycle times for structural foam injection molding are generally longer compared to traditional injection molding, due to the time required for the foam to expand.
Despite this, the advantages in terms of material savings and part performance make it a compelling choice for many manufacturers.
Metal Injection Molding (MIM)
Metal injection molding (MIM) bridges the gap between plastic and metal manufacturing, allowing for the production of complex metal parts with high precision. The process begins with mixing metal powder with a binder, which is then molded, debonded, and sintered to form the final product. This technique is perfect for creating parts with intricate internal designs and precise tolerances.
One of the most significant advantages of MIM is its ability to produce high volumes of complex parts with minimal waste in a single step. This efficiency makes it an attractive option for industries requiring detailed metal components, such as automotive and medical.
MIM does have its limitations. The equipment required for this process can be quite expensive, and it is generally better suited for lower volumes and smaller parts. Nevertheless, the ability to produce intricate, high-quality metal parts makes MIM valuable in manufacturing.
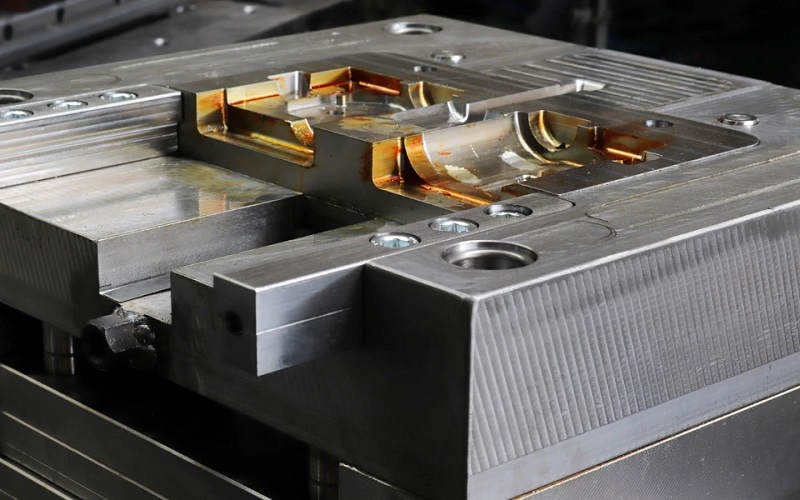
Hot Runner vs. Cold Runner Systems
Choosing between a hot runner injection mold and cold runner systems is a critical decision in the injection molding process. Hot runner systems keep the plastic molten in the runner channels, reducing material waste and offering faster cycle times. This consistency in production quality makes hot runners ideal for high-volume manufacturing.
Often incorporating valve gates, hot runner systems improve the final product’s aesthetics and reduce shear rates during production. However, these systems can be more complex and expensive compared to their cold runner counterparts.
Conversely, cold runner systems are simpler and more budget-friendly. They let the plastic solidify in the runner, which then needs removal and either recycling or disposal. Cold runners are generally preferred for lower volume production and applications where the runner thickness can exceed the part thickness to ensure quality.
Choosing between these systems often depends on balancing the production process volume and budget constraints.
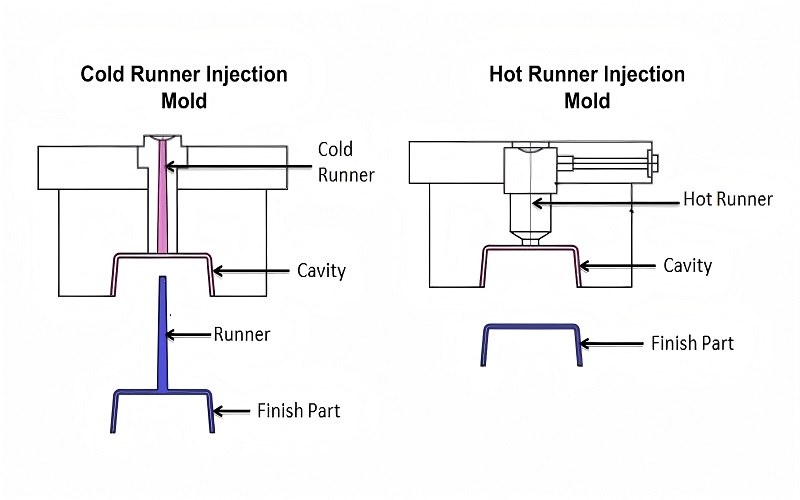
Multi-Material Injection Molding
Multi-material injection molding (MMM) allows for the simultaneous molding of different materials into a single component. This technique is beneficial for creating parts with varying hardness, enhancing functionality and aesthetics.
MMM encompasses several methods, including multi-component injection molding, multi-shot injection molding, and over-molding. Multi-component injection molding involves injecting multiple materials simultaneously to create a composite structure. Multi-shot injection molding layers materials sequentially in the mold, ensuring strong inter-layer bonding. Over-molding adds an additional layer of material to a pre-existing component, often to improve grip or appearance.
MMM is used in various applications, from durable automotive parts to consumer products with enhanced grip and aesthetics. This technique not only improves product performance but also streamlines the manufacturing process, reducing costs and cycle times.
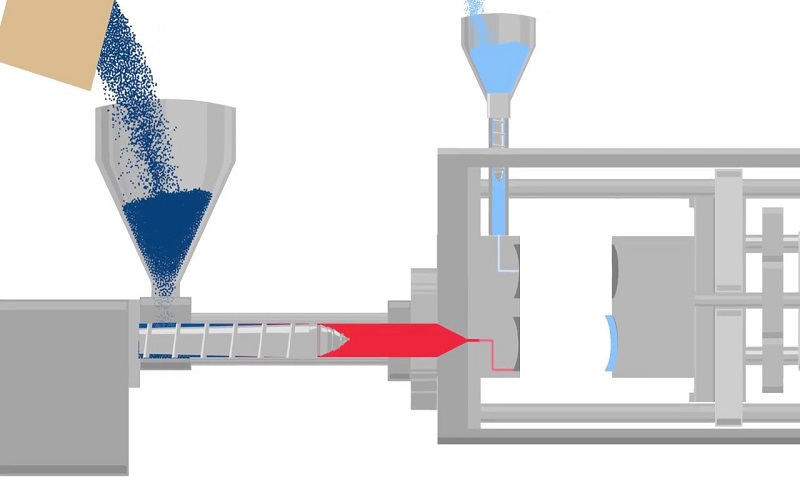
Applications Across Industries
Injection molding finds its way into a multitude of industries, each leveraging its unique advantages for specific applications. In the medical field, injection molding ensures the production of sterile and disposable products, vital for maintaining hygiene and safety standards. The packaging industry relies on this technique for creating containers and caps, benefiting from its reliability and efficiency in mass production.
Household items, from kitchenware to furniture, are often produced using injection molding due to its cost efficiency and design flexibility. In the automotive sector, lightweight parts such as dashboards and bumpers are manufactured through injection molding, contributing to overall vehicle performance and fuel efficiency.
Agriculture and aerospace industries also benefit from injection molding. Agricultural tools and components are designed to be UV-resistant and durable, capable of withstanding harsh conditions. In aerospace, the focus is on producing lightweight, high-performance components that meet stringent safety regulations.
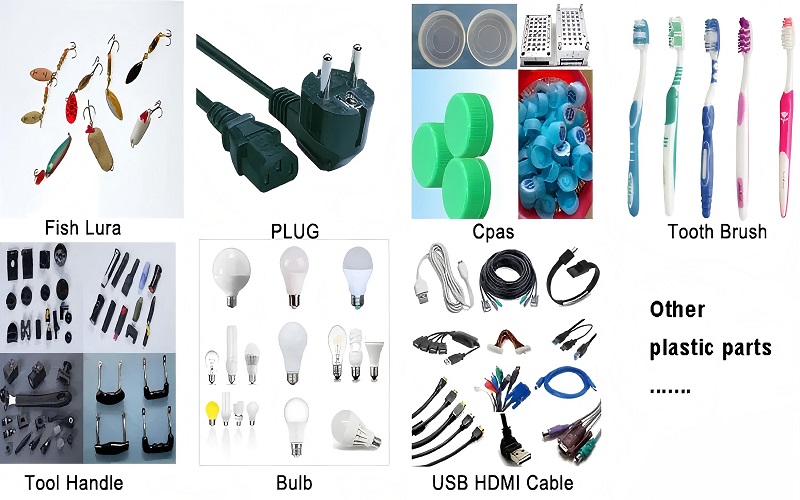
The varied applications of injection molding showcase its indispensability in modern manufacturing.
Benefits of Injection Molding
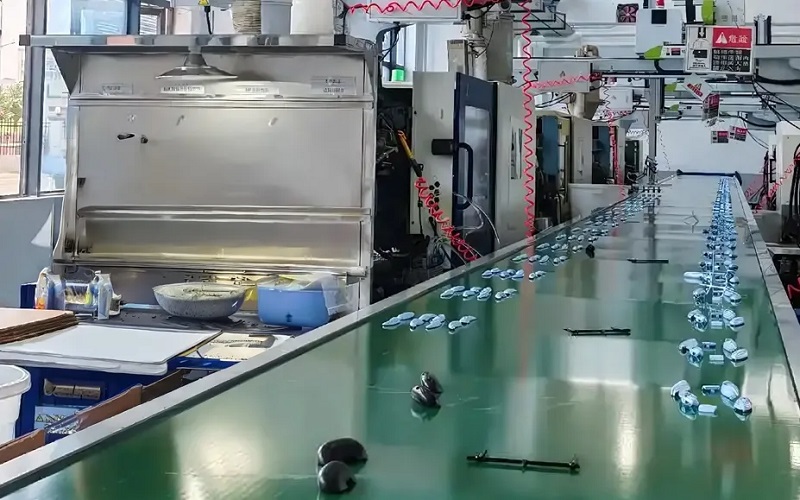
Injection molding offers numerous benefits, making it a preferred choice for large-scale production. A primary advantage is its cost-effectiveness, especially for high-volume manufacturing. After the initial investment in creating the mold, the per-unit cost of production drops significantly. This efficiency is further enhanced by the automation of the process, which minimizes waste and reduces overall production costs.
Injection molding is renowned for its precision and repeatability. The ability to produce parts that meet strict quality standards and tight tolerances is crucial for industries where consistency is key. This precision extends to the production of complex shapes and customized designs, allowing manufacturers to innovate and enhance product functionality.
Additionally, the versatility in material choices makes injection molding suitable for various industries. From thermoplastics to advanced composites, manufacturers can select the best material for their specific needs, ensuring optimal performance and durability of the final product.
The fast production speeds and scalability of multi-cavity molds further add to the appeal of injection molding, catering to varying market demands with ease.
Injection Molding Machine Types
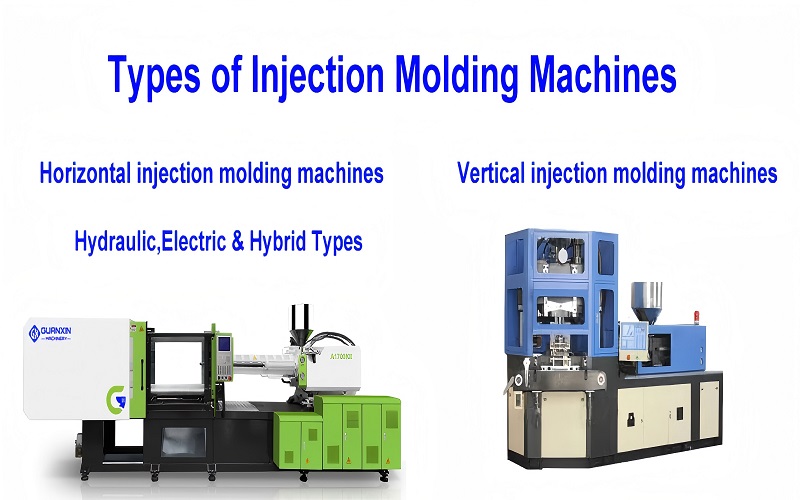
Injection molding machines come in three main types of injection:
- Hydraulic, known for their power and ability to produce high-quality parts, making them suitable for a wide range of applications.
- Electric, which offer precision and energy efficiency, ideal for smaller parts and complex designs.
- Hybrid, combining the benefits of both hydraulic and electric machines, providing versatility and efficiency.
These machines are particularly effective in handling large molds and producing parts that require significant force.
Electric injection molding machines, on the other hand, provide precise control and are typically more energy-efficient than hydraulic models. They are ideal for applications that demand high precision and repeatability, such as the production of intricate components for electronics and medical devices.
Hybrid machines combine the strengths of hydraulic and electric systems, providing flexibility and efficiency. These machines can handle a variety of production requirements, making them a versatile choice for manufacturers looking to optimize their operations.
Choosing an injection molding machine involves considering factors like production volume, part complexity, and energy efficiency to ensure the best fit.
Key Components of Injection Molds
Knowing the key components of injection molds is crucial for optimizing the process. Mold cavities are the specifically shaped areas where the actual part is formed from molten plastic. These single cavity molds must be meticulously designed to ensure the final product meets the desired specifications.
Ejector pins are vital for releasing the molded parts from the mold after cooling. They are part of an ejector system that ensures the parts are ejected smoothly and without damage. The sprue bushing connects the injection machine nozzle to the mold, allowing plastic to flow into the cavities.
Other important components include runners that direct liquid plastic from the sprue to the cavities, and cooling channels that facilitate cooling, speeding up the production cycle. Locating rings position the mold correctly on the machine, ensuring proper alignment during injection. These components, along with guide pins and bushings, ensure accurate alignment of the mold halves during closing.
Mold Longevity and Maintenance
Mold longevity and maintenance are crucial for successful injection molding projects. The SPI mold classification system categorizes molds by durability and expected lifespan, aiding manufacturers in selecting the right mold.
For instance, Class 101 molds can endure over a million cycles, making them suitable for high-volume production, while Class 104 molds are ideal for low-volume applications with a lifespan of 10,000 to 25,000 cycles.
Regular maintenance extends the life of injection molds. This includes basic cleaning after every production run and thorough inspections on a monthly basis. Proper maintenance prevents issues like sink marks and ensures dimensional stability.
Material choice significantly impacts mold longevity. High-grade steel and aluminum are preferred for their durability, with alloy steels like H13 offering exceptional toughness and longevity. Improving mold design, like incorporating uniform wall thickness, enhances durability and reduces wear, ensuring optimal performance throughout the mold’s lifespan.
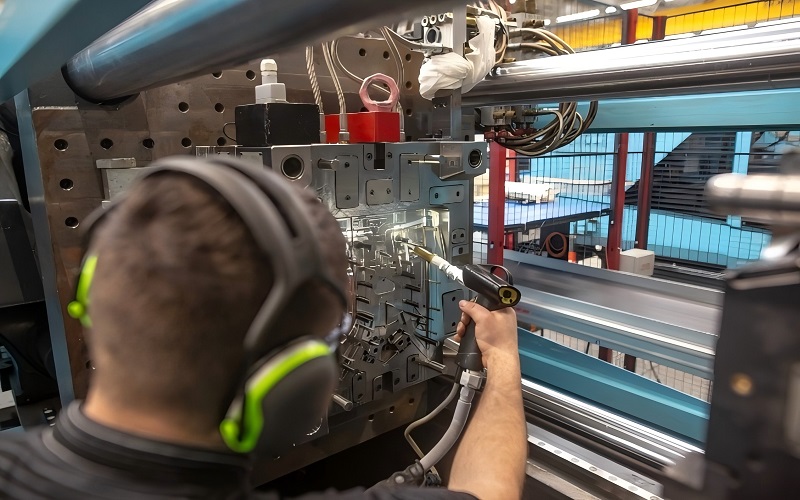
Summary
In summary, injection molding is a versatile and efficient manufacturing process that offers numerous benefits across various industries. From gas-assisted and thin-wall injection molding to liquid silicone rubber and structural foam techniques, each method provides unique advantages tailored to specific applications.
The choice of injection molding technique depends on factors such as material requirements, part complexity, and production volume.
Understanding the key components of injection molds and maintaining them properly is essential for ensuring the success of injection molding projects.
By leveraging the right techniques and equipment, manufacturers can achieve high-quality, cost-effective production, meeting the demands of modern markets.
Frequently Asked Questions
What is gas-assisted injection molding used for?
Gas-assisted injection molding is utilized for producing large, hollow, and porous components, enhancing structural integrity while reducing material use by up to 35%. This technique optimizes efficiency in manufacturing.
What materials are commonly used in thin-wall injection molding?
High-density polyethylene and polypropylene are commonly utilized in thin-wall injection molding because of their excellent flow characteristics, crucial for manufacturing parts with precise dimensional tolerances.
What are the benefits of using LSR in injection molding?
Utilizing liquid silicone rubber (LSR) in injection molding provides significant advantages, including the capacity to fill thin sections efficiently, reduced material waste in large-scale production, and a broad operational temperature range from -60°C to 180°C. These factors make LSR an optimal choice for various applications.
What are the main types of injection molding machines?
The main types of injection molding machines are hydraulic, electric, and hybrid models. Each type has its own advantages, with hydraulic machines offering power, electric machines providing precision and energy efficiency, and hybrid machines combining the benefits of both.
How does the SPI mold classification system help in injection molding?
The SPI mold classification system aids manufacturers in selecting appropriate molds by categorizing them according to durability and lifespan. This ensures optimal choices for production needs, such as Class 101 molds for high-volume applications.