In manufacturing, different types of tooling are essential for efficient and cost-effective production. Tooling includes the tools and equipment used in making products.
This article explains the various types of tooling—prototype, soft, bridge, and hard—and their specific roles in the manufacturing process.
The Importance of Tooling in Manufacturing
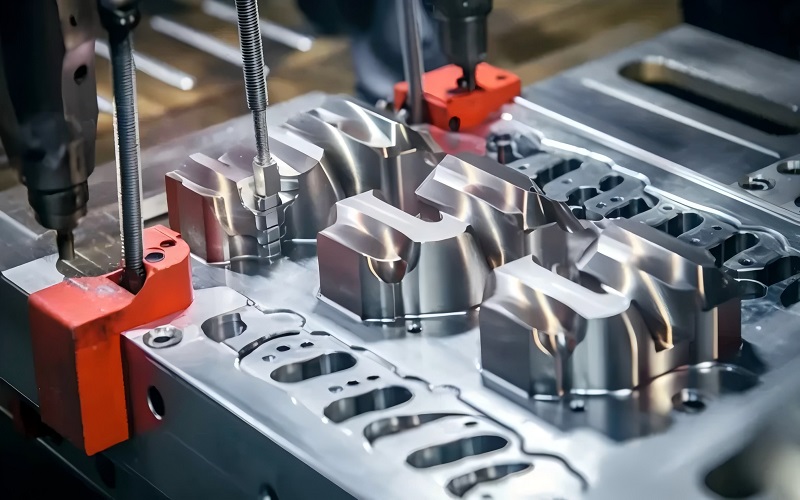
Tooling plays a pivotal role in the manufacturing process. High-quality machine tooling streamlines processes, reduces machine downtime, and minimizes maintenance needs, boosting overall production efficiency. Tooling design directly influences production, impacting defects and product quality. Effective tooling enhances product durability and consistency, which leads to higher customer satisfaction.
Additionally, the choice of tooling material significantly affects both performance and manufacturing costs. Proper tooling ensures quality, efficiency, and cost-effectiveness in manufacturing. Choosing the right tooling materials greatly affects tool durability and performance, which in turn impacts final product quality, including tooling raw material considerations.
Investing in high-quality, well-designed tooling is a strategic move that enhances overall manufacturing efficiency and quality. Such investment pays off by reducing downtime, minimizing defects, and ensuring consistent product quality.
Overview of Tooling Types
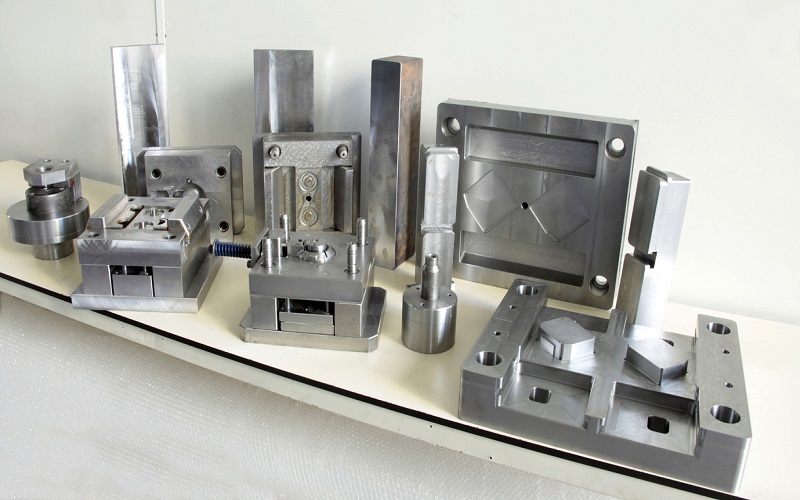
Tooling is fundamental to manufacturing, and understanding its types is key to optimizing production. The three basic types of tooling are prototype tooling, soft tooling, and hard tooling, each suited to different manufacturing stages.
Prototype tooling is essential for creating initial models and testing design concepts, while soft tooling is often used for low to medium production volumes. Hard tooling, on the other hand, is designed for high-volume production and offers greater durability.
Recognizing these distinctions aids in selecting the right tooling for each production phase, thereby enhancing efficiency and product quality.
Prototype Tooling
Prototype tooling is crucial during the product development phase. It enables designers and engineers to create initial models, test, and refine concepts before full production. This stage helps identify design flaws, assess functionality, and improve manufacturing processes, ensuring the final product meets all specifications.
Materials commonly used in prototype tooling include low-cost metals, plastics, and composites, offering flexibility and ease of manufacturing. Prototype tooling offers multiple benefits, including reduced time to market, lower production iteration costs, and improved product quality through early testing. Industries needing rapid prototype development find this tooling particularly beneficial.
Soft Tooling
Soft tooling, often made from soft tool materials like silicone, is typically used for low to medium production volumes. It offers lower initial costs and faster production times compared to hard tooling. Soft tooling supports complex designs and can be easily modified to accommodate changes.
However, soft tooling’s limited lifespan makes it unsuitable for high-volume manufacturing. Soft tooling materials wear out faster, requiring more frequent replacements, which increases overall costs over time.
Despite these limitations, soft tooling remains cost-effective for certain production needs.
Bridge Tooling
Bridge tooling acts as a transition between prototyping and full production. It supports ramp-up volumes, enabling faster market entry. Materials commonly used in bridge tooling include silicone plastics, hard plastics, and aluminum.
Bridge tooling is cost-effective and can be manufactured much faster compared to hard tooling. It offers a practical solution for managing production volumes during the transition from prototype to mass production, ensuring that bores require fewer tools and timelines stay on track. Additionally, a production tool can enhance efficiency in this process.
Hard Tooling
Hard tooling is used for high-volume production and involves resilient materials like tool steel or nickel alloys. These materials are chosen for their toughness and wear resistance, making hard tooling ideal for long-lasting production tools.
Hard tooling is cost-effective for high-volume runs as the initial investment is spread over many units. It ensures precision and longevity in manufacturing, consistently producing high-quality parts. However, higher initial costs and longer production times can be disadvantages for smaller volumes.
Tooling Costs
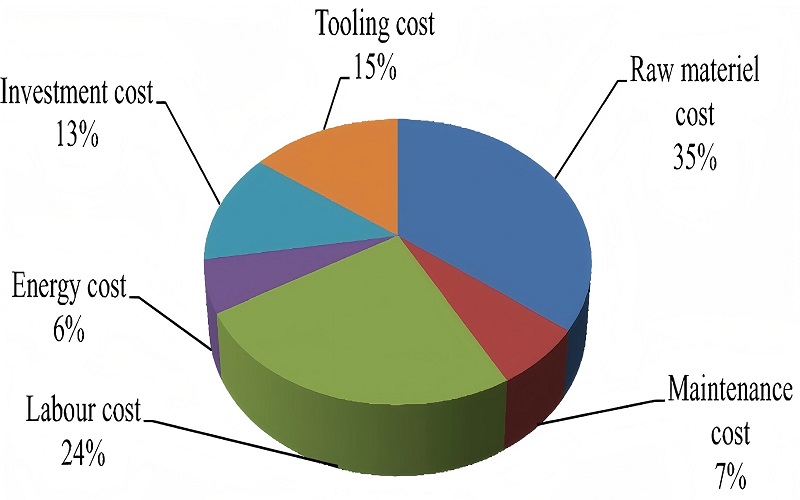
Tooling costs are influenced by factors like material selection, labor expenses, and quality considerations. While soft tooling is cost-effective for small runs, frequent replacements can lead to higher tools cost per unit over time. Tooling cost is often amortized across the total production volume or the tooling’s lifespan.
Bridge tooling is a cost-effective transition between prototype development and full production. As production volume increases, the cost per unit decreases due to optimized processes. Understanding these cost dynamics is essential for making informed tooling decisions for a given production run.
Key Considerations in Tooling Design
Designing tooling for manufacturing requires considering several key factors. Incorporating a draft angle into molded parts improves moldability and helps prevent damage during ejection. Using at least 0.5 degrees of draft for vertical faces in injection molding enhances part release.
Tool complexity significantly impacts cost, with intricate designs typically requiring higher investments. Precision requirements elevate manufacturing costs, as tighter tolerances demand more advanced and expensive tooling. A core-cavity design approach can facilitate easier mold polishing and improve overall efficiency.
Common Tooling Processes
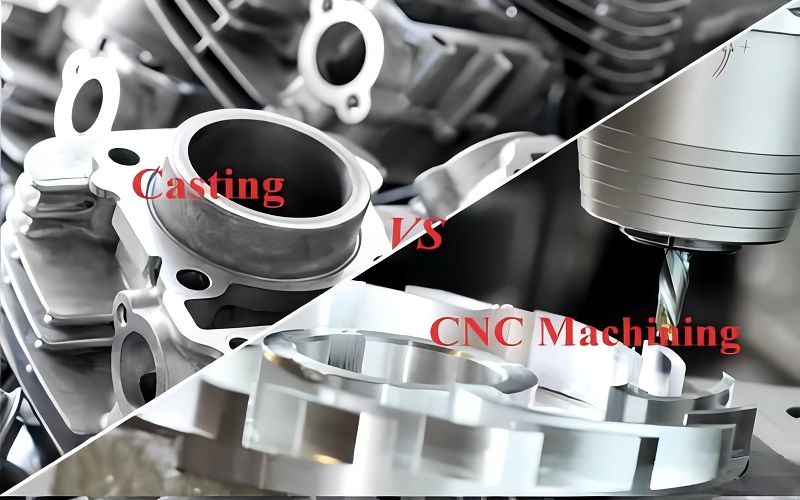
Injection molding is highly efficient, enabling mass production by injecting molten material into injection molds. Cooling is critical in both injection molding and die casting, ensuring materials solidify properly to retain the mold’s shape.
CNC machining is renowned for creating highly precise parts and is widely used across various industries for its versatility. In CNC machining, material is removed from a solid block to create the desired shape, allowing for various finishes and tolerances with a cnc machine.
Pressure die casting involves forcing molten metal into a pressure die casting mold cavity under high pressure, making it suitable for intricate metal parts. This process is preferred for parts requiring high strength and durability, using non-ferrous metals like aluminum and zinc.
Advantages and Disadvantages of Different Tooling Types
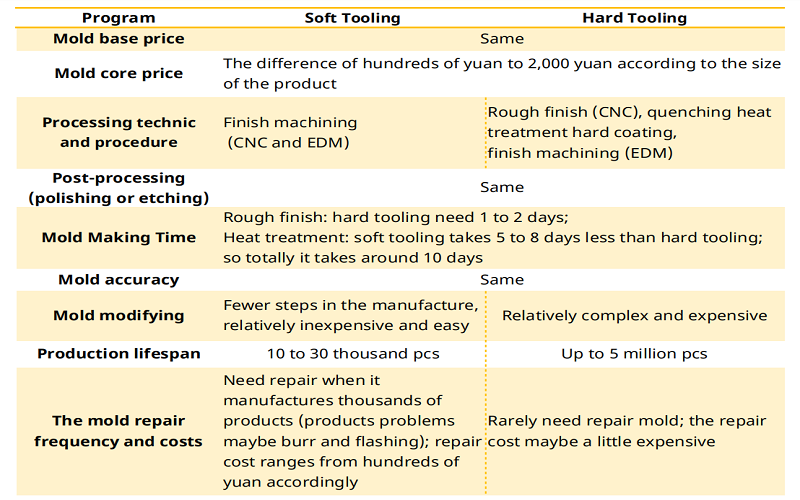
Soft tooling benefits rapid production and supports complex designs but isn’t suitable for high-volume manufacturing due to its limited lifespan. Bridge tooling enables faster market entry and is manufactured much quicker compared to hard tooling.
Hard tooling offers greater durability and handles larger production volumes but requires higher initial investment and longer production times. While hard tooling allows precise component replication, it limits design change flexibility compared to soft tooling.
Hard tooling’s main advantages are robustness, precision, and compliance with stringent tolerances, while disadvantages include high cost and time-consuming production.
Best Practices for Tooling Management
A feedback loop with maintenance staff can identify inefficiencies and inform ongoing improvements in tooling management. Training staff on inventory systems and organizational practices is crucial for maintaining a productive and efficient storeroom.
Implementing 5S principles—Sort, Set in order, Shine, Standardize, and Sustain—leads to a more organized and efficient storeroom. These best practices ensure tooling is well-maintained, readily available, and effectively utilized, contributing to overall manufacturing efficiency.
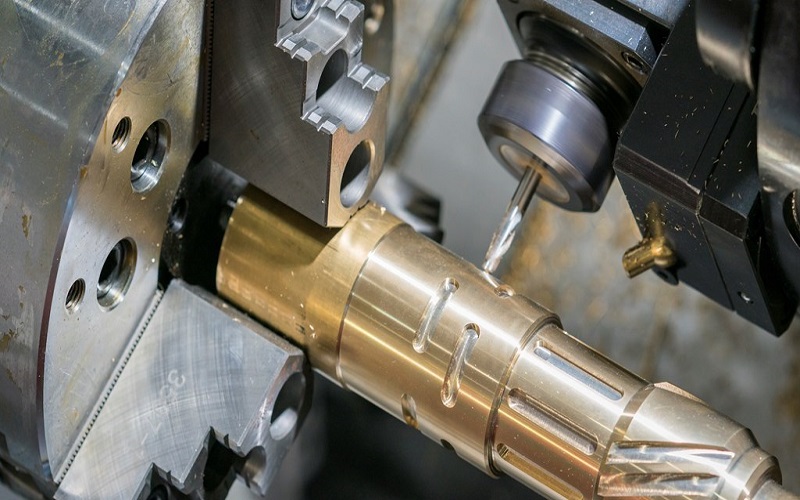
Summary
Understanding the different types of tooling in manufacturing is crucial for optimizing production processes, reducing costs, and improving product quality. From prototype tooling that allows for early testing and design refinement to hard tooling that ensures precision and durability in high-volume production, each type of tooling has its unique advantages and applications.
By considering factors such as tooling costs, design considerations, and best practices for tooling management, manufacturers can make informed decisions that enhance overall efficiency and product quality. Investing in the right tooling is a strategic move that pays off in the long run, ensuring consistent, high-quality production and greater customer satisfaction.
Frequently Asked Questions
What is prototype tooling?
Prototype tooling is essential for developing initial models and refining design concepts prior to full production. It ensures that potential issues are addressed early in the manufacturing process.
What materials are commonly used in soft tooling?
Soft tooling commonly utilizes materials such as silicone, which are ideal for low to medium production volumes. This allows for flexibility and cost-effectiveness in manufacturing processes.
How does bridge tooling support manufacturing processes?
Bridge tooling effectively enhances manufacturing processes by facilitating a smooth transition from prototyping to full production, thereby enabling faster market entry and optimized ramp-up volumes. This approach ensures that manufacturers can efficiently scale production while maintaining quality.
What are the advantages of hard tooling?
Hard tooling provides enhanced durability and precision, making it ideal for high-volume production despite a higher initial investment. This results in improved efficiency and consistency in manufacturing processes.
How can manufacturers manage tooling effectively?
Manufacturers can manage tooling effectively by establishing a feedback loop with maintenance staff and training personnel on inventory systems while implementing 5S principles. This ensures streamlined operations and improved tool management.