Vapor smoothing is a crucial post-processing technique in 3D printing that enhances the surface quality of printed parts. By using vaporized solvents, it eliminates layer lines and rough textures, making 3D prints look more polished and professional.
This article will cover how vapor smoothing works, what materials are suitable, and the benefits of using this technique.
Let’s dive in to understand why vapor smoothing is essential for high-quality 3D prints.
Understanding Vapor Smoothing
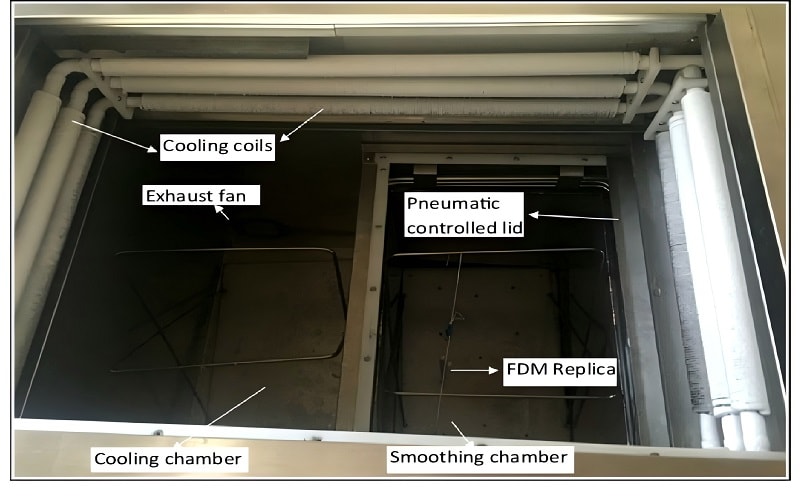
Vapor smoothing is a finishing technique that utilizes vaporized solvent to enhance the surface quality of 3D-printed parts. This process involves post-processing to eliminate visible layer lines and rough surfaces, significantly improving the overall aesthetic quality of the printed parts.
Addressing these common issues has made vapor smoothing work a key technique for achieving high-quality finishes in 3D printing.
The technique works by employing chemical vapors to react with the material’s surface, melting and partially dissolving it. This controlled chemical melt creates a smoother finish primarily on the outer layers, while preserving the inner structure of the printed part. This dual effect ensures that the part retains its original strength and functionality, while appearing more refined.
Vapor smoothing evolved as a solution to the challenges faced by plastic 3D printing, which often results in coarse surface finishes and visible layer lines.
Using a finishing agent and controlled chemical reactions, the process transforms rough, printed surfaces into smooth, polished ones, comparable to those produced by injection molding. This advancement has opened new possibilities for the application of 3D-printed parts in various industries.
The Vapor Smoothing Process Explained
The vapor smoothing process starts with placing the 3D-printed parts in a controlled environment exposed to solvent vapors.
These vapors melt the peaks of the layers, resulting in a more uniform surface finish. The process can vary from simple applications using a brush to more complex setups involving enclosed vapor chambers.
In the smoothing chamber, the effectiveness of the process depends on several variables, including the quantity of solvent, exposure duration, and ambient temperature.
These factors must be carefully controlled to ensure that the surface melts evenly without compromising the part’s original features and geometries. This delicate balance is crucial to achieving a high-quality finish that preserves the integrity of the printed part.
The use of a vapor smoothing machine can automate and streamline the process, making it more efficient and consistent. Regulating temperature and exposure times allows these machines to handle multiple parts simultaneously, ensuring each one achieves the desired level of smoothness.
This fully automated smoothing process is particularly beneficial for large-scale production, where consistency and efficiency are paramount.
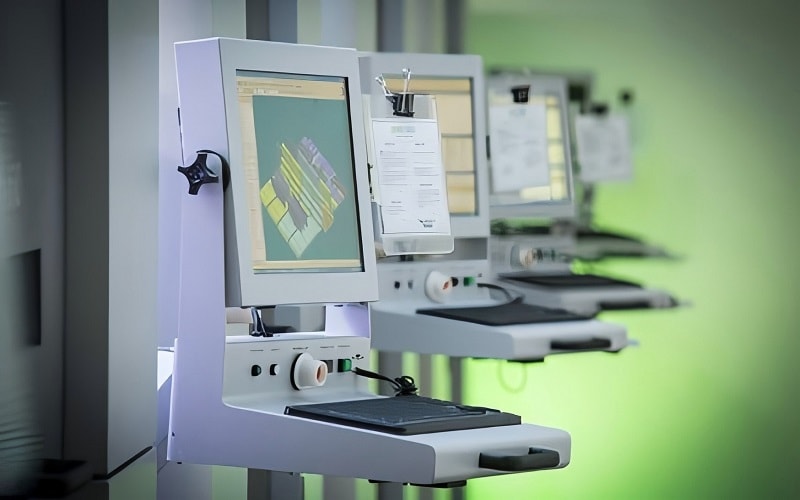
Suitable Materials for Vapor Smoothing
Not all materials are suitable for vapor smoothing. The process is most effective with materials like ABS and ASA, which respond well to solvent exposure.
Polyamide materials, such as PA 12 and PA 11, are also known for their compatibility with vapor smoothing. These materials, when subjected to a controlled chemical melt, achieve a smooth, polished finish that enhances their aesthetic and functional qualities.
Choosing the right solvent is crucial to the success of the vapor smoothing process. Different materials require specific solvents to achieve optimal results without causing damage.
For instance, acrylic and polycarbonate are suitable for vapor smoothing, provided the appropriate solvent is used. This careful selection ensures that the surface is effectively smoothed while maintaining the part’s structural integrity.
Key Benefits of Vapor Smoothing
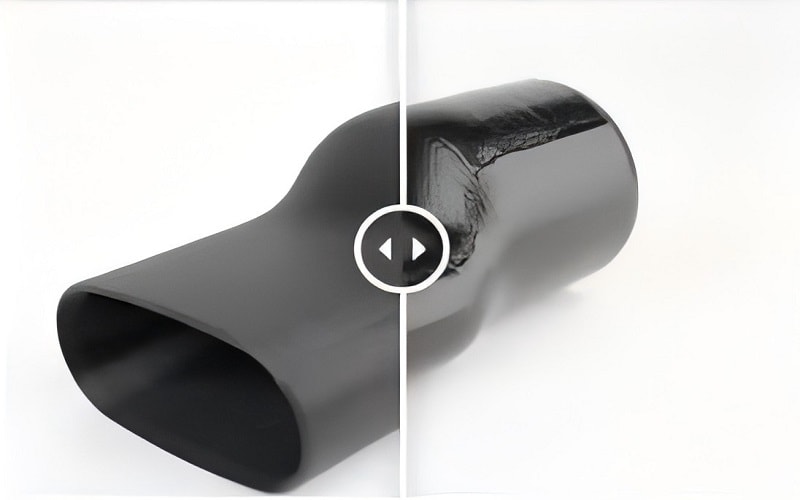
Vapor smoothing offers several key benefits, making it an indispensable post-processing technique in 3D printing.
It significantly enhances the surface quality of printed parts, bringing them to a level akin to injection-molded components.
The process also improves the durability and performance of the parts, while preserving their dimensional accuracy and intricate geometries.
Let’s delve deeper into these benefits.
Improved Surface Finish
One of the most notable advantages of vapor polishing is its ability to drastically reduce surface roughness, transforming rough, printed parts into polished, high-quality surfaces.
This improvement is particularly evident in parts with complex geometries, where traditional sanding or polishing techniques might fall short. The reduction in average surface roughness can be as much as 72-81%, making the parts comparable to those produced through injection molding.
Standard SLS parts typically have a surface roughness greater than 8 m Ra, but post-vapor smoothing, this can be reduced to below 125 uin Ra.
This significant enhancement not only improves the aesthetic appeal of the parts but also enhances their functional qualities, making them suitable for a wide range of applications where a high-quality surface finish is essential.
Enhanced Durability and Performance
Vapor smoothing also enhances the durability and performance of 3D-printed parts. Reducing surface roughness decreases bacterial growth by up to 60%, which is particularly beneficial for applications requiring high hygiene standards. This improvement in hygiene is crucial for medical devices and other applications where cleanliness is paramount.
Additionally, vapor smoothing reduces moisture absorption in 3D printed parts, enhancing their water resistance and overall performance over time. This increased durability makes the parts more reliable and long-lasting, meeting the demands of various industries, from medical to automotive.
Dimensional Accuracy Preservation
Maintaining the dimensional accuracy of parts during post-processing is a critical concern in 3D printing. Vapor smoothing addresses this challenge by using controlled chemical melt through solvent vapors, which interact with the part’s surface to achieve a polished finish without altering the geometry. This technique ensures that the part’s original dimensions are preserved, maintaining the integrity of the complex geometries.
Achieving this requires controlling factors such as temperature, exposure time, and solvent selection during the vapor smoothing process. Properly managing these variables prevents warping or undesirable changes, ensuring that the parts retain their intended design and functionality.
Applications of Vapor Smoothing in Various Industries
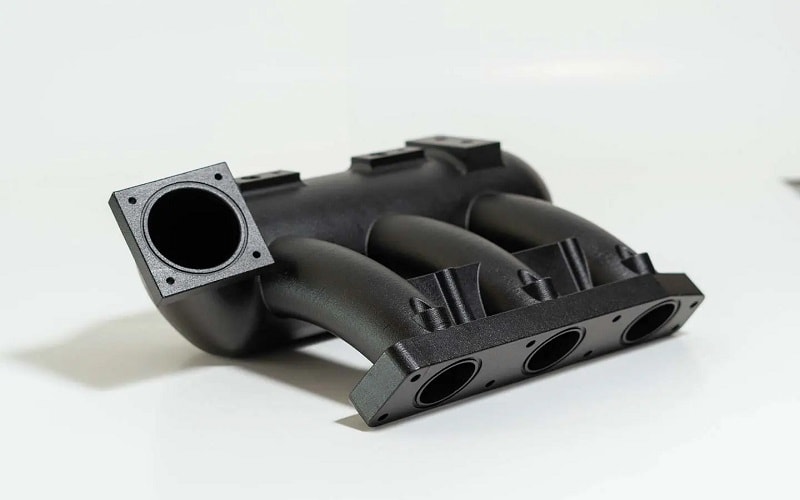
Vapor smoothing finds applications across a wide range of industries, each benefiting from its unique advantages.
In the medical field, it is essential for items like surgical instruments and prosthetics, where smooth surfaces are crucial for patient safety. The industrial sector uses vapor smoothing to enhance the durability and appearance of prototypes, tools, and fixtures.
In the automotive and aerospace industries, vapor smoothing ensures that parts meet the high standards required for quality and precision in automotive and industrial machinery.
Consumer products, including household items and toys, achieve a polished look through vapor smoothing, making them more appealing to end-users.
Additionally, the process has proven beneficial for producing ESD-safe trays for microchips, protecting sensitive components.
Best Practices for Effective Vapor Smoothing

Achieving the best results with vapor smoothing requires adherence to several best practices. Careful control of solvent exposure time and temperature is crucial to achieve the desired surface finish without compromising the object’s integrity. Utilizing automated equipment can streamline the process, ensuring consistency and efficiency.
Let’s delve into the optimal processing parameters and essential safety precautions for effective vapor smoothing.
Optimal Processing Parameters
Maintaining a consistent temperature within the vapor smoothing chamber is essential to prevent warping of the 3D print during the smoothing process.
The temperature should be kept at a level that promotes effective vapor diffusion without causing excessive melting of the print. Adjusting the exposure time is also critical, as it directly impacts the smoothness of the surface finish achieved.
Customized profiles for vapor smoothing are necessary, as they determine the temperature and pressure settings specific to different materials. Tailoring these parameters ensures each material receives optimal treatment, resulting in a high-quality finish that preserves the part’s dimensions.
Safety Precautions
Safety is paramount when dealing with chemical vapor smoothing. A well-ventilated workspace minimizes the inhalation of harmful fumes from the solvents used in the process.
Following safety protocols, such as wearing protective gear, prevents inhalation exposure and skin contact, safeguarding the operator’s health.
Particular attention should be paid to applications involving medical devices and food contact items. These require stringent safety measures to ensure that the finished parts are safe for their intended use. Following these precautions ensures that vapor smoothing can be performed safely and effectively.
Cost and Lead Time Considerations
The cost of vapor smoothing is influenced by various factors, including:
- The process used
- Material chosen
- Quantity of parts
- Geometry of the parts
As order volumes increase, the costs for vapor smoothing generally decrease, making it more cost-effective for larger production runs. Scalability is particularly advantageous for manufacturers looking to optimize production costs.
Lead times for vapor smoothing typically range from 1 to 5 business days, adding minimal time to the overall production process.
Compared to traditional post-processing methods like sanding or polishing, vapor smoothing can significantly reduce the time spent on finishing parts, enhancing overall efficiency.
Challenges and Solutions in Vapor Smoothing
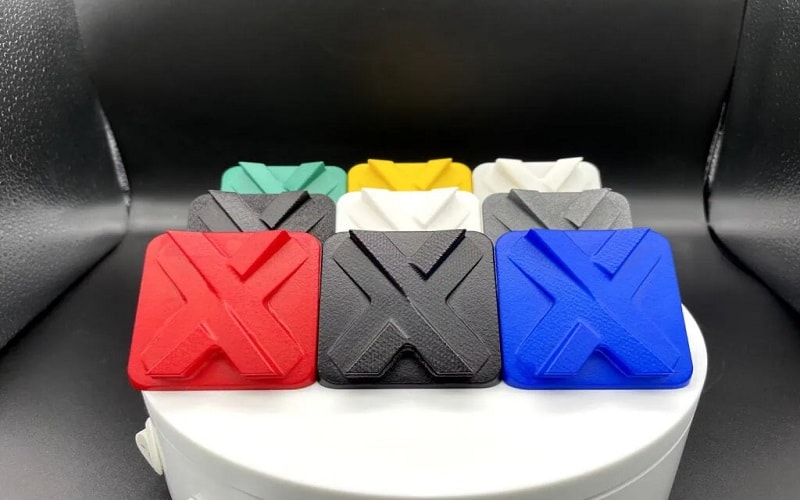
Despite its many advantages, vapor smoothing presents certain challenges that must be addressed to achieve consistent results.
For example, managing the surface finish to prevent defects such as blistering, edge pooling, and speckling requires careful control of the process parameters. Automated systems can help mitigate these issues by providing precise control over temperature, pressure, and exposure time.
Furthermore, ensuring the mechanical performance of vapor-smoothed parts is crucial, as the process affects tensile strength, elongation at break, and flexural performance.
By addressing these challenges through optimized process parameters and automated systems, manufacturers can maintain high-quality standards in their 3D printed products.
Case Studies and Success Stories
Numerous case studies highlight the transformative impact of vapor smoothing on 3D printed parts. For instance, in the automotive industry, vapor smoothing significantly enhanced engine performance by improving the surface finish and reducing weight.
Similarly, in the medical field, vapor smoothing improved the hygiene and durability of custom medical devices, making them safer and more reliable.
Consumer products have also benefited from vapor smoothing, with items like household goods and toys achieving a polished, professional appearance that meets industry standards. These success stories underscore the versatility and effectiveness of vapor smoothing across various applications.
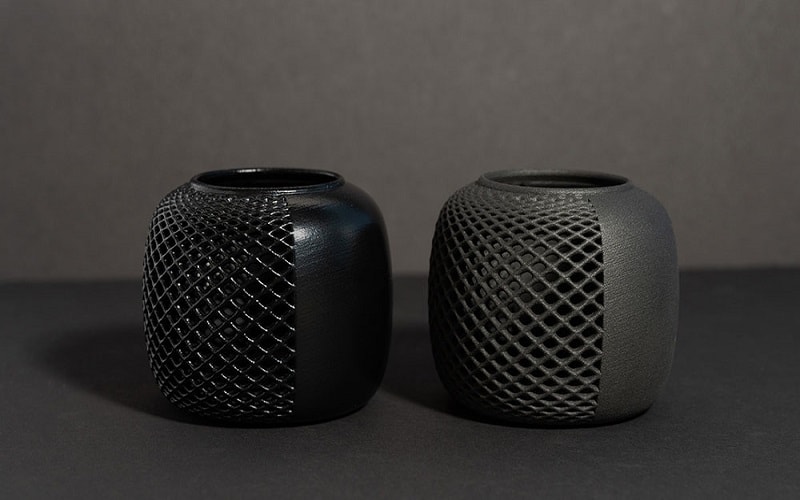
Summary
Vapor smoothing stands out as a powerful post-processing technique that enhances the surface quality, durability, and dimensional accuracy of 3D printed parts.
Its applications across diverse industries, from medical to automotive, demonstrate its transformative potential.
By adhering to best practices and addressing challenges, manufacturers can achieve consistent, high-quality results, making vapor smoothing an invaluable tool in the world of 3D printing.
Frequently Asked Questions
What is vapor smoothing?
Vapor smoothing is a finishing technique employed to improve the surface quality of 3D printed parts by utilizing vaporized solvent to melt and partially dissolve the outer layers.
This process results in a smoother finish and enhances the overall appearance of the printed object.
Which materials are suitable for vapor smoothing?
Materials such as ABS, ASA, polyamides (PA 12, PA 11), acrylic, and polycarbonate are suitable for vapor smoothing when the correct solvent is applied. It is essential to choose the right solvent for effective results.
What are the benefits of vapor smoothing?
Vapor smoothing significantly enhances the surface finish, durability, and hygiene of parts while maintaining dimensional accuracy, ultimately bringing 3D printed components closer in quality to those made by injection molding.
How does vapor smoothing affect production costs and lead times?
Vapor smoothing effectively reduces post-processing time and costs, particularly in larger production runs, leading to typical lead times of 1 to 5 business days. Consequently, this technique can enhance overall production efficiency and cost-effectiveness.
What safety precautions should be taken during vapor smoothing?
During vapor smoothing, it is crucial to ensure proper ventilation and wear protective gear to minimize exposure to harmful fumes and prevent skin contact. These precautions are vital for your safety.