Weld lines form in plastic injection molding when molten plastic flows don’t fully merge, causing visible lines and potential weak spots. Understanding and minimizing them is key to producing high-quality parts.
Understanding Weld Lines in Injection Molding
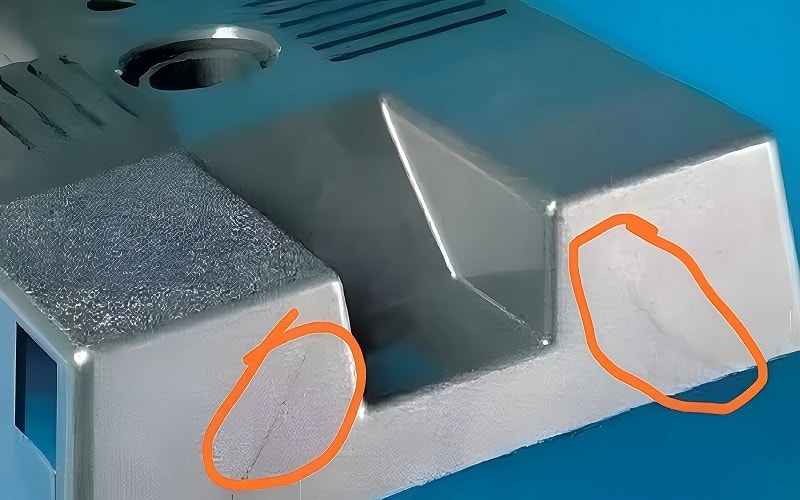
Weld lines are more than just visual blemishes; they are critical indicators of potential weaknesses in injection molded parts. These lines form when two separate flows of molten plastic meet but do not fully merge, creating visible seams or scratches on the surface of the molded part. The incomplete merging of these flows leads to the formation of weld lines and knit lines, often unavoidable in complex designs.
The presence of weld lines can adversely affect both the aesthetics and structural integrity of finished plastic parts. They are not just unsightly but can also signify weaker spots that might fail under stress.
Grasping the nature of weld lines is essential for those in the injection molding process, as it directly impacts the quality of the final product.
What Are Weld Lines?
Weld lines are defects that occur when two separate flows of molten plastic meet but do not fully merge, leading to visible marks on the molded part.
These lines appear as seams or scratches, sometimes with a wavy nature, and are caused by the incomplete merging of plastic flows due to factors like temperature variations, inadequate pressure, or poor mold design.
Variants of weld lines, known as meld lines, form at higher meeting angles during the merging of flow streams, often appearing when the angle between the two flow fronts is greater than 135 degrees.
How Do Weld Lines Form?
Weld lines form when flow fronts divide due to mold features and fail to merge completely. This can result from factors such as cooler resin flow, narrow sections within the mold, or poor design choices like improper wall thickness and gate placement.
Temperature variations can also lead to premature solidification of the molten plastic, preventing proper fusion and resulting in weld line defects.
Impact on Finished Plastic Parts
Weld lines can be critical weak points in molded parts, potentially leading to failure under stress. While they can create unsightly visual defects, their acceptability often depends on the specific application of the part.
Effective management of weld lines can significantly enhance the quality and strength of molded parts, making them more suitable for their intended purposes.
Common Causes of Weld Lines
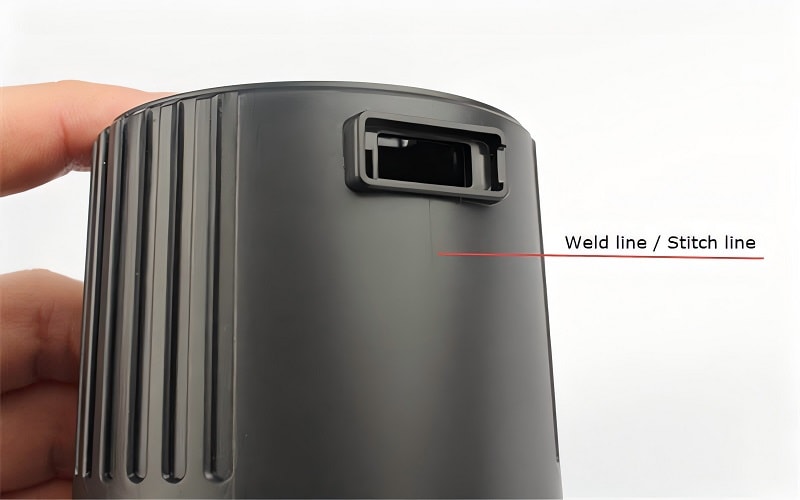
Understanding the common causes of weld lines is the first step in preventing them. Inadequate pressure in the injection molding machine can prevent the proper melding of plastic flows, leading to broad weld lines. Mold design, resin temperature, and injection speed also play critical roles in the formation of these defects.
Weld lines and knit lines form due to the fountain flow pattern, where melted plastic moves fastest at the center and slower at the edges, leading to incomplete merging.
Inadequate Pressure
Inadequate pressure during the injection molding process can result from machine faults or incorrect settings, leading to broad weld lines due to the incomplete merging of plastic flows. Adequate pressure is necessary for the successful melding of two plastic flows, thereby preventing weak areas in the final product.
Temperature Variations
Temperature variations can cause uneven solidification of the molten plastic, resulting in weld lines. Maintaining the optimal temperature ensures the molten plastic merges effectively, preventing visible defects.
Higher temperatures during injection can improve the fusion of plastic flows, decreasing the likelihood of weld lines.
Mold Design Flaws
Poor mold design, such as uneven wall thickness or improperly positioned gates, can lead to inconsistent flow and the formation of weld lines. Factors like obstructions within the mold cavity and thick walls can significantly contribute to these defects.
Effective mold design practices play a key role in reducing the visibility of weld lines in injection molded parts.
Slow Injection Speed
A slow injection speed can lead to uneven cooling of the molten plastic, increasing the risk of weld line formation. Optimizing injection speed ensures the material fills the mold rapidly, preventing premature cooling and the development of weld line defects.
Impure Resin Materials
The presence of impurities in resin materials can disrupt the continuous resin flow, causing variations that lead to weld line defects. High-purity resins ensure a more consistent flow, decreasing the likelihood of weld lines in finished plastic parts.
Techniques to Minimize Weld Lines
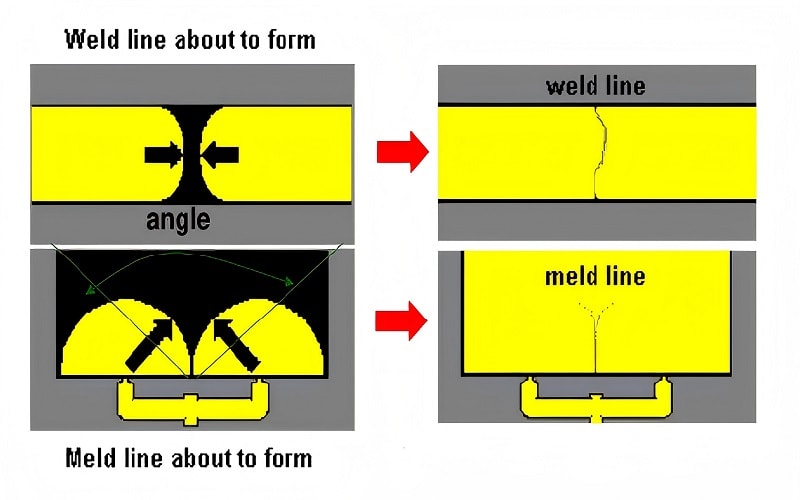
Several techniques can be employed to minimize weld lines, enhancing both the aesthetic appeal and mechanical properties of molded components. Maintaining adequate pressure, controlling temperature, improving mold design, increasing injection speed, and ensuring resin purity are all critical strategies for reducing weld line issues.
These techniques can significantly influence the occurrence and visibility of weld lines in molded parts.
Optimizing Injection Pressure
Proper injection pressure is crucial in the injection molding process to ensure quality outcomes. Adjusting pressure settings can enhance the flow of molten plastic, aiding in the elimination of weld lines using an injection molding press.
Adequate pressure ensures the complete merging of molten plastic flows, reducing the formation of weld lines.
Controlling Temperature
Maintaining the optimal molten plastic temperature is essential for successful injection molding processes. Proper temperature management ensures different flows of molten plastic merge effectively, reducing the risk of weld line formation.
Controlling temperature not only improves the aesthetics of the final product but also enhances its structural integrity.
Improving Mold Design
Manufacturers can minimize weld lines by adjusting mold design specifications such as wall thickness and gate placement. Repositioning gates can minimize barriers to flow, significantly reducing weld lines.
Working with mold design professionals can enhance the design process, reducing weld line occurrences.
Increasing Injection Speed
Faster injection speeds help achieve a more uniform cooling rate across the part, which can prevent weld line formation. Increased injection speed ensures the material fills the mold rapidly, preventing premature cooling and weld line formation.
This is critical for improving the quality of injection molded parts.
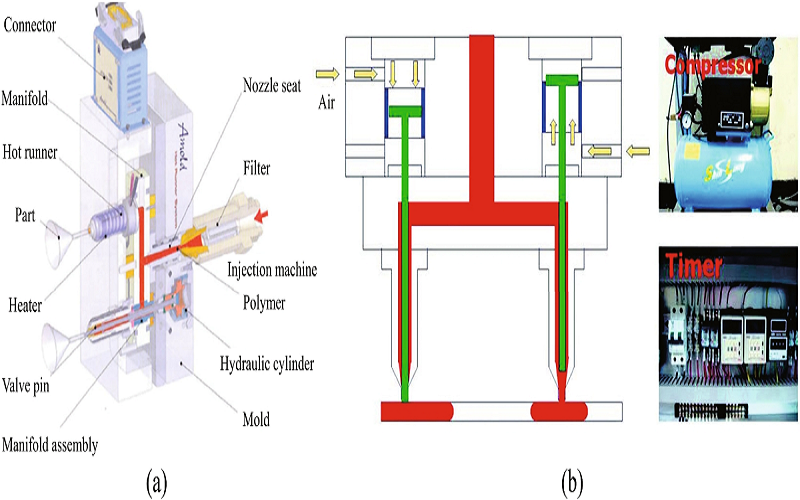
Ensuring Resin Purity
Using high-quality, pure resins is crucial for maintaining smooth plastic flow in injection molding. Impurities in resin materials can disrupt the continuous resin flow, leading to incomplete merging and weld line defects.
Avoid weld line issues by sourcing high-quality resins from reputable suppliers who guarantee material purity.
Advanced Solutions for Weld Line Prevention
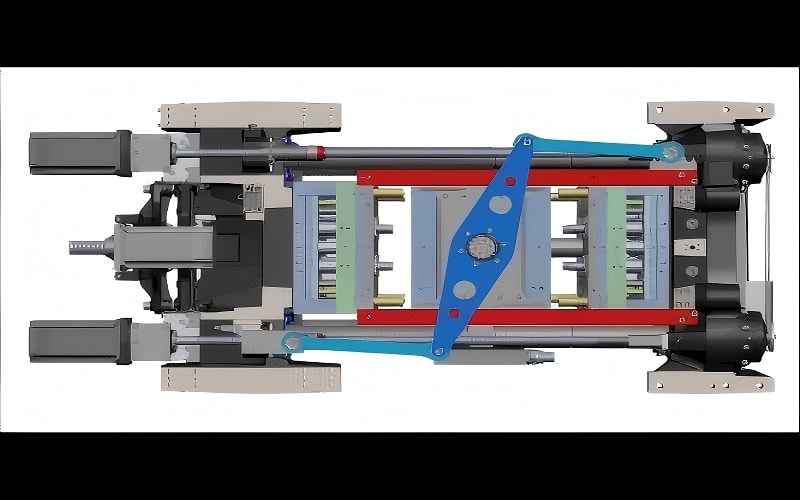
Advanced techniques can significantly reduce the occurrence of weld lines in injection molded parts. Mold flow analysis, gate design optimization, and the use of additives are three advanced solutions that can help prevent weld lines and improve the overall quality of the final product.
Mold Flow Analysis
Mold flow analysis software is an essential tool for predicting potential weld line locations during the design phase, allowing for preemptive adjustments. This analysis simulates resin flow through the mold, predicting weld line locations and potential production issues before manufacturing begins.
Visualizing potential flow issues allows engineers to optimize the design before production, thereby minimizing the risk of weld line formation.
Gate Design Optimization
Careful gate design allows for controlled resin flow, which minimizes the chances of weld lines forming in critical areas of the mold. The strategic placement and size of gates can significantly influence where weld lines form, allowing for better control over their visibility.
Effective direction of molten plastic flow can reduce the likelihood of weld lines in critical areas.
Use of Additives
Incorporating specific additives can enhance the flow characteristics of resins, which helps to reduce the occurrence of weld lines in molded parts. These additives improve resin flow properties, significantly helping to minimize weld line visibility in the final product.
Practical Tips for Injection Molders
Effective management of weld lines is crucial for optimizing production efficiency and ensuring high-quality finished products. Regular maintenance, ongoing training, and collaboration with experts are practical steps that can help injection molders manage weld lines more effectively and achieve better results in their molding process.
Regular Maintenance
Regular maintenance of injection molding machines maintains consistent performance and enhances product quality. Ongoing training for operators keeps them updated on best practices for machine maintenance and operation.
Collaborating with mold design and material experts can lead to optimized maintenance practices that mitigate potential issues and improve overall efficiency.
Training and Education
Ongoing training empowers operators with the latest techniques to mitigate weld lines during the injection molding process. Continuous education keeps operators informed about the latest techniques to prevent defects like weld lines.
This continuous training is essential to keep operators informed about the latest techniques to prevent weld lines.
Collaboration with Experts
Improving mold design by adjusting wall thickness, gate placement, and ensuring smooth flow paths is crucial in minimizing weld lines.
Mold flow analysis software predicts and addresses potential weld line locations before production, essential for mold design improvement.
Optimized gate designs can control flow fronts and reduce weld lines in critical areas of the mold.
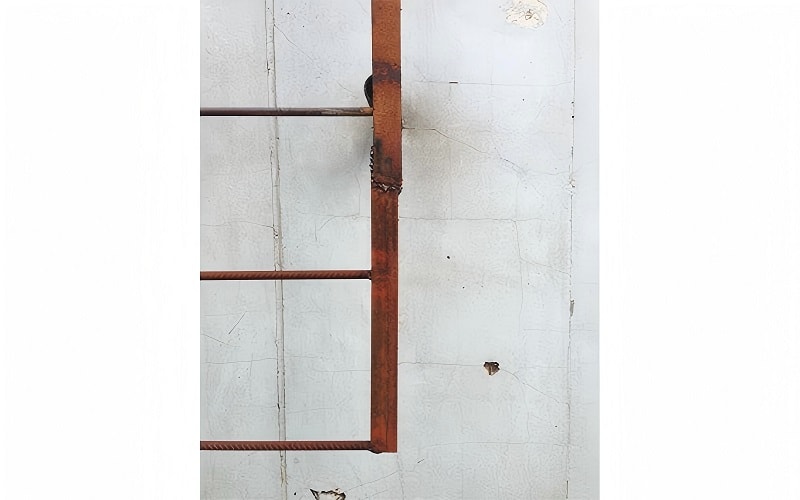
Summary
Mastering the techniques to manage and minimize weld lines is essential for producing high-quality plastic parts. By understanding the formation of weld lines, addressing common causes, and employing both basic and advanced techniques, injection molders can significantly enhance the aesthetic and structural integrity of their products.
Regular maintenance, ongoing training, and collaboration with experts further ensure that weld lines are kept at bay, optimizing production efficiency and product quality.
With these strategies, manufacturers can turn potential weaknesses into strengths, ensuring the success of their injection molding processes.
Frequently Asked Questions
What are weld lines in injection molding?
Weld lines are defects in injection molding that occur when two flows of molten plastic converge but fail to completely fuse, leading to noticeable seams on the final product. This can affect both the aesthetics and structural integrity of the molded part.
How do temperature variations cause weld lines?
Temperature variations lead to uneven solidification of molten plastic, which results in incomplete merging of flows and the formation of weld lines. Such inconsistencies can compromise the integrity of the final product.
What role does mold design play in weld line formation?
Mold design plays a critical role in weld line formation, as factors like uneven wall thickness and gate positioning can result in inconsistent flow, ultimately leading to the development of weld lines. Effective mold design is essential to minimize these defects.
How can optimizing injection speed help prevent weld lines?
Optimizing injection speed is crucial as it allows the material to fill the mold quickly, thereby reducing the risk of premature cooling and preventing the formation of weld lines. This proactive approach enhances the overall quality of the molded part.
Why is resin purity important in minimizing weld lines?
Resin purity is crucial in minimizing weld lines because high-quality, pure resins promote more consistent flow, thereby reducing the chances of imperfections in the final plastic parts. Consistency in material properties leads to better overall product quality.