Die casting is a process where molten metal is injected into a mold under high pressure. It produces parts with high precision and excellent surface finishes, widely used in industries like automotive and aerospace.
This article will explore the die casting process, including what is die cast, its types, benefits, and applications.
Understanding Die Casting
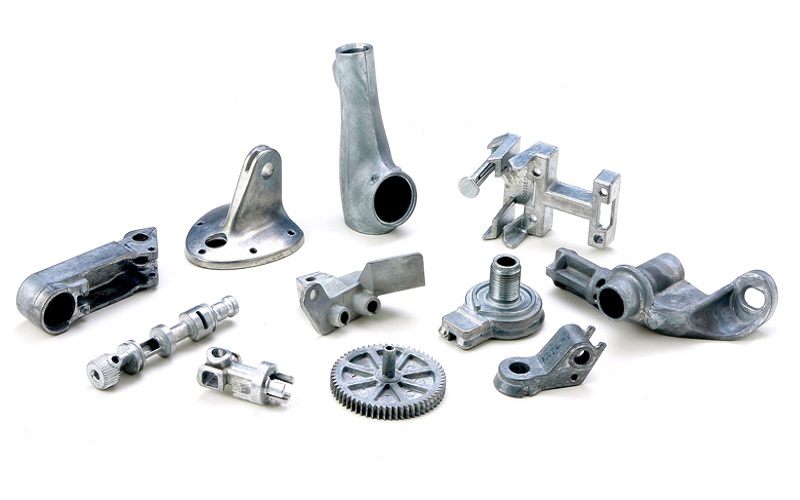
Die casting stands out for its high dimensional accuracy and efficiency in metal die casting. The focus is mainly on non-ferrous metals. This includes materials like zinc, copper, aluminum, magnesium, lead, and tin-based alloys.
One of the most significant advantages of die casting is its ability to produce parts with complex shapes and consistent wall thicknesses, which sets it apart from other casting methods. The process delivers smooth surface finishes and maintains narrow tolerances, making it ideal for manufacturing high-quality components efficiently.
The Die Casting Process Explained
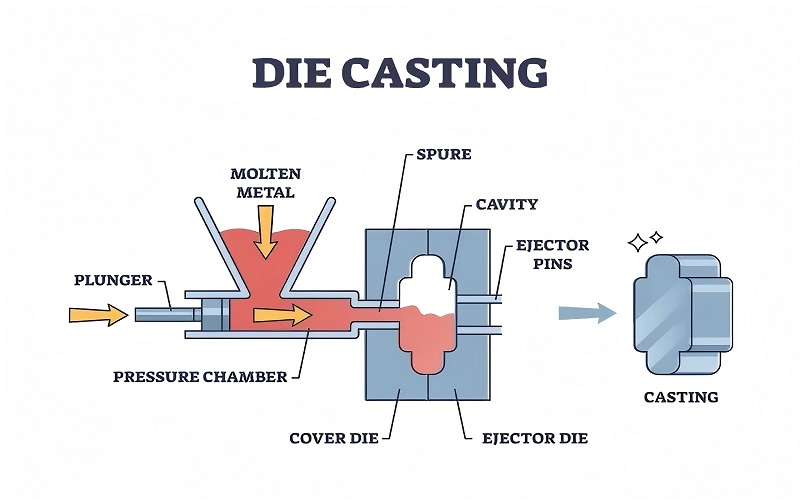
The die casting process involves a marvel of engineering, typically involving four main stages: mold creation, metal injection, cooling and solidification, and ejection and finishing. Each stage is carefully crafted to guarantee precision and efficiency, resulting in high-quality metal parts through the metal casting process.
Here’s a closer look at each stage and their contributions to the overall die casting process.
Mold Creation
Mold creation is the first and crucial stage of the die casting process. Using advanced CAD software, engineers design and simulate the mold to ensure accuracy and efficiency. The molds, typically made from durable materials like steel or aluminum, consist of two halves that form the mold cavity when joined.
CNC machining processes, including rough machining, heat treatment, and finish machining, are employed to create these molds, ensuring they can withstand the high pressures involved in die casting. This stage sets the foundation for producing high-quality parts with complex shapes.
Metal Injection
During metal injection, molten metal is injected into the mold cavity under high pressure, typically between 100 to 1800 bars. This high-pressure injection ensures that the molten metal fills the mold completely and uniformly, resulting in parts with excellent dimensional stability and surface finish. Injecting the metal at a slow initial velocity minimizes turbulence and ensures a smooth fill.
High-pressure die casting offers numerous advantages, such as faster filling times, better dimensional stability, and smoother surface finishes. This stage is critical in maintaining the tight tolerances required for high-quality die cast parts.
Cooling and Solidification
The cooling and solidification phase begins immediately after the molten metal fills the mold cavity. During this stage, the molten metal cools and solidifies, taking the desired shape of the mold. Controlling the cooling rate is essential to achieve the desired microstructure and avoid defects like shrinkage and internal voids.
Maintaining continuous pressure during cooling ensures the part retains its shape and dimensions.
Ejection and Finishing
Once the metal has solidified, the mold is unclamped, and the solidified part is ejected from the mold using ejector pins. Finishing operations, such as trimming, surface grinding, and machining, are performed to remove any excess material and achieve the desired surface finish.
Sometimes, die cast parts can be shipped without additional finishing steps, enhancing overall process efficiency.
Types of Die Casting Processes

Die casting employs various methods to suit different materials and applications. The main types of die casting processes include hot chamber, cold chamber, and vacuum die casting. Each method has its unique advantages and is chosen based on the specific requirements of the metal and the desired properties of the final part.
Let’s explore these primary types of die casting processes in more detail.
Hot Chamber Die Casting
Hot chamber die casting, also known as gooseneck casting, is particularly efficient for metals with low melting points, such as zinc and lead. In this process, molten metal is injected directly from a furnace into the die using a gooseneck mechanism. This method allows for rapid production cycles, significantly increasing output.
Ideal for mass production, the hot chamber process efficiently produces small to medium-sized parts.
Cold Chamber Die Casting
Cold chamber die casting is used for metals with higher melting points, such as aluminum and magnesium. In this process, molten metal is ladled into an unheated chamber and then injected into the mold at high pressure. This method is suitable for producing large, sturdy parts with exceptional mechanical properties, making it ideal for demanding applications.
The cold chamber process, however, has a slower cycle time due to the necessity of metal transfer, which can be a disadvantage.
Vacuum Die Casting
Vacuum die casting is a type of high-pressure die casting. In this method, air is removed from the die cavity prior to the injection of molten metal. This process minimizes air entrapment, leading to improved part density and mechanical properties.
Vacuum die casting is ideal for producing high-stress or pressure parts, as it significantly reduces porosity. Common parts manufactured using this method include transmission cases and aluminum implants.
Common Materials Used in Die Casting
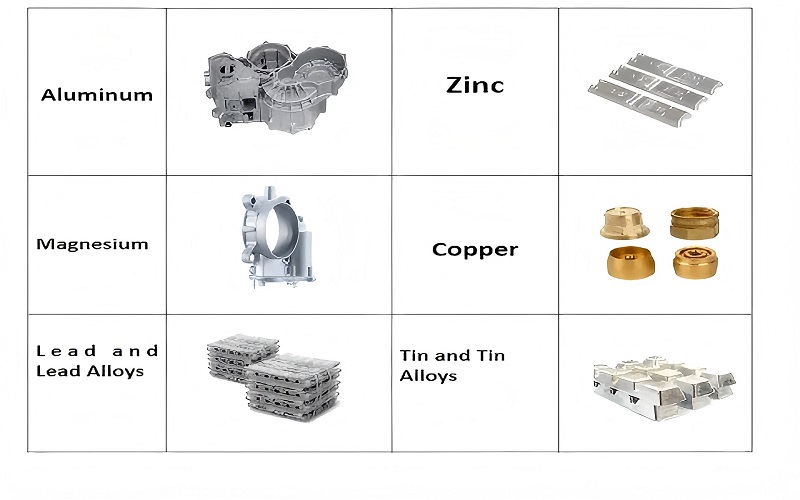
Primarily using non-ferrous metals, die casting prominently features aluminum, magnesium, and zinc alloys. These materials are chosen for their excellent mechanical properties, such as high strength, corrosion resistance, and dimensional stability.
Choosing the right material ensures the desired properties and performance of the final die cast parts.
Aluminum Alloys
Aluminum alloys are highly favored in die casting due to their improved dimensional stability and suitability for intricate components. These alloys offer excellent corrosion resistance and are commonly used in the automotive and aerospace industries for components such as engine parts and structural elements.
Zinc Alloys
Zinc die casting alloys are known for their ability to endure high impact and are often used in applications that require good plating characteristics. These alloys provide a good balance of strength, toughness, and corrosion resistance, making them ideal for consumer products and electronics components.
Magnesium Alloys
Magnesium die casting is favored for its lightweight nature and high machinability, making it suitable for components needing precision. The lightweight nature of magnesium alloys contributes to reduced overall weight in components, enhancing performance in various applications such as automotive and aerospace.
Advantages of Die Casting
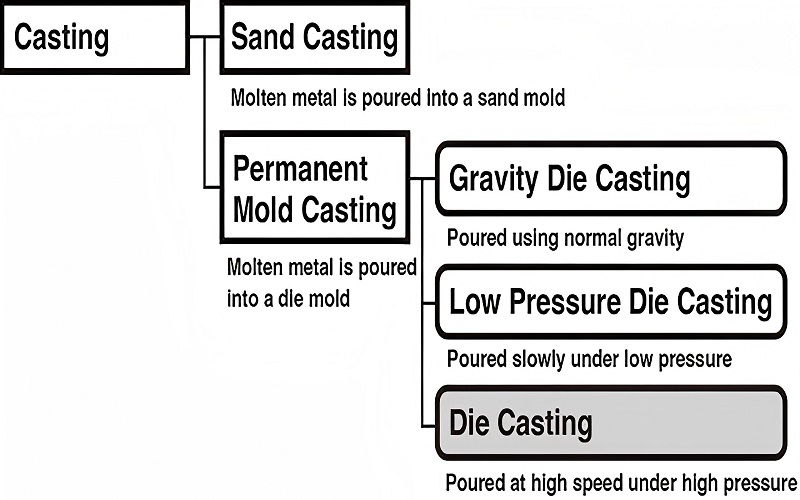
Die casting offers numerous advantages, making it a preferred manufacturing process across various industries. The process is highly efficient, allowing for the production of large quantities of parts with low incremental costs.
Producing parts with smooth surface finishes and precise dimensions, die casting reduces the need for extensive post-processing. Additionally, die casting is beneficial for producing complex shapes with high dimensional accuracy, making it ideal for applications in electronics, aerospace, and consumer products.
Precision and Accuracy
Die casting is renowned for its high dimensional accuracy, ensuring that parts are produced consistently to exact specifications. Advanced CNC machines and die casting machine are vital for achieving tight tolerances, enhancing overall part precision.
The precision of aluminum die casting, for instance, helps create lighter yet strong vehicles, highlighting the manufacturing accuracy benefits.
High Volume Production
Efficient in high-volume manufacturing, die casting becomes more economical as production volume increases, reducing the cost per piece. This process is particularly beneficial for large-scale manufacturing due to its high startup costs, which are offset by the low cost per unit part.
However, addressing defects and additional finishing processes can increase production costs.
Excellent Surface Finish
Surface finish is a crucial aspect of die casting, impacting both the durability and functionality of the part. Die cast parts are known for their excellent surface finish and dimensional consistency compared to other casting processes.
Standard finishing processes in die casting include anodizing, powder coating, and wet plating, which enhance the appearance and performance of the parts. Techniques such as low-pressure casting and gravity casting can further improve the surface finish by reducing air entrapment and minimizing porosity.
Applications of Die Casting
Die casting is a versatile manufacturing process suited for producing a large quantity of small to medium-sized components efficiently. Industries that benefit from die casting include automotive, aerospace, and electronics, where high strength and low porosity are critical in the die casting industry.
This process enables the production of complex, thin-walled parts with a favorable strength-to-weight ratio, essential in high-performance applications.
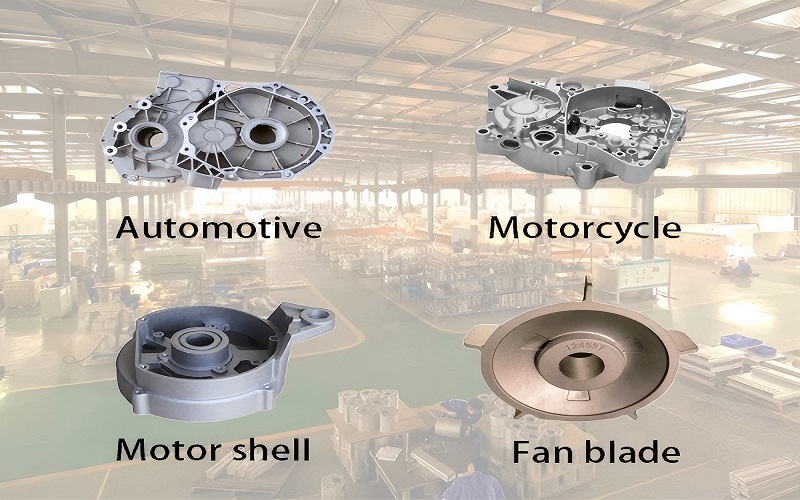
Automotive Industry
In the automotive industry, die casting is widely used to produce components such as engine parts, transmission housings, and structural elements. Squeeze die castings are commonly employed for engine components like cylinder heads, blocks, and wheel rims due to their excellent mechanical properties.
Gravity die casting is suitable for structural parts like engine blocks and gearbox casings, showcasing its versatility in automotive applications.
Aerospace Industry
Die casting plays a crucial role in the aerospace industry, where specialized aluminum alloys are often used to meet stringent performance standards. The process is essential for producing high-performance components that require exceptional dimensional accuracy and compatibility with complex geometries.
Die casting’s ability to produce lightweight yet strong parts makes it ideal for aerospace applications.
Consumer Electronics
The electronics industry employs die casting for manufacturing durable components in devices such as smartphones, personal computers, and other consumer electronics. Die casting’s precision and ability to produce complex shapes with excellent surface finishes make it a preferred method for electronics components, ensuring high-quality and reliable end products.
Limitations of Die Casting
Despite its many advantages, die casting has certain limitations. The high initial investment required for die casting molds can be a significant barrier for many businesses. Additionally, die casting is generally limited to non-ferrous metals due to their melting points, which restricts the range of materials that can be used.
Quality control is essential to minimize common defects such as misruns, cold shuts, porosity, and shrinkage.
High Initial Costs
The cost of die molds is a significant factor contributing to the elevated initial investment for die casting. Smaller production runs are often not feasible due to the high cost involved in setting up die casting, which limits operational flexibility and scalability. This high initial investment can be a deterrent for businesses looking to adopt die casting for their manufacturing needs.
Material Restrictions
Die casting primarily uses metals with lower melting points, which limits the range of materials that can be utilized. This restriction means that ferrous metals, such as steel and iron, are generally not suitable for die casting, limiting the process’s versatility compared to other casting methods that can handle a broader range of materials.
Defects and Quality Control
Quality control is critical in die casting to address common defects such as misruns, cold shuts, porosity, and shrinkage. Inadequate process control can cause misruns and cold shuts, resulting in inconsistent part quality.
Pores on the part surface form due to air entrapment during the high-pressure casting process, making it essential to maintain tight tolerances and proper process control to minimize these defects.
Selecting a Die Casting Manufacturer
Choosing the right die casting manufacturer is crucial for ensuring high-quality and reliable parts. Partnering with an experienced die casting firm ensures optimal material decisions tailored to project needs. Outsourcing die casting services can lead to better precision and higher quality.
Many die castings are sourced from the EU or Asia, with EU suppliers often providing higher quality and better service despite slightly higher costs. It’s essential to choose a supplier that offers complete engineering support, from design to delivery, and has in-house tool-making capabilities to manage costs and timelines effectively.
Confirming that your supplier can meet consistent supply needs is also crucial to avoid excess storage and warehousing costs.
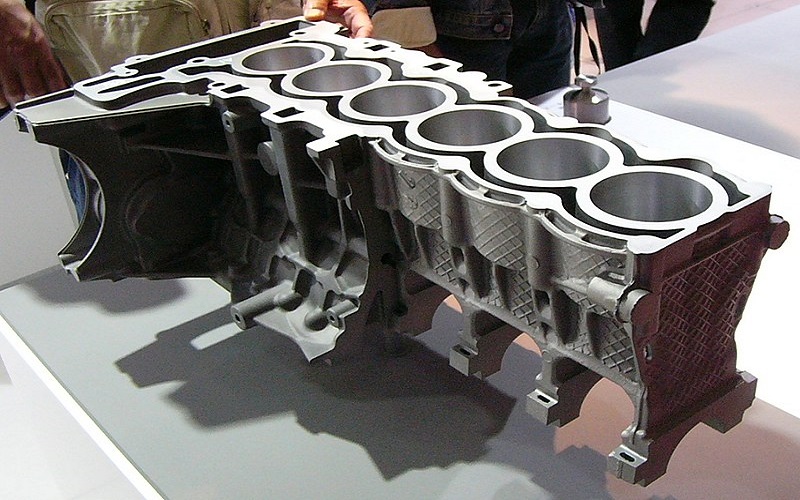
Summary
In summary, die casting is a highly efficient and versatile manufacturing process that offers numerous advantages, including precision, high-volume production, and excellent surface finishes. It is widely used across various industries, including automotive, aerospace, and consumer electronics, for producing complex and high-quality parts. However, it also has limitations, such as high initial costs and material restrictions. By selecting the right die casting manufacturer, businesses can leverage the full potential of this remarkable process to achieve their production goals.
Frequently Asked Questions
What materials are commonly used in die casting?
Aluminum, zinc, and magnesium alloys are commonly used in die casting, thanks to their excellent mechanical properties and compatibility with the process. These materials provide optimal strength and performance for a variety of applications.
What are the main types of die casting processes?
The main types of die casting processes are hot chamber, cold chamber, and vacuum die casting, each offering distinct advantages and suited for various applications. Understanding these processes can help in selecting the most appropriate method for your project needs.
What industries benefit from die casting?
Die casting significantly benefits the automotive, aerospace, and electronics industries by providing high strength, low porosity, and the ability to create complex shapes. These attributes are essential for the performance and durability of components in these sectors.
What are the advantages of die casting?
Die casting provides high precision and efficiency in mass production, along with excellent surface finishes and the capability to create complex shapes. These advantages make it an optimal choice for manufacturers seeking quality and cost-effectiveness.
What are the limitations of die casting?
Die casting has notable limitations such as high initial costs for mold production, restrictions to non-ferrous metals, and the necessity for stringent quality control to reduce defects. These factors can impact the overall feasibility of the process for certain applications.