PBT plastic material, or Polybutylene Terephthalate, is a versatile, high-performance engineering thermoplastic. Known for its strength and heat resistance, it’s widely used in automotive and electrical industries. This article covers what PBT is, its properties, and its applications.
What is Polybutylene Terephthalate (PBT)?
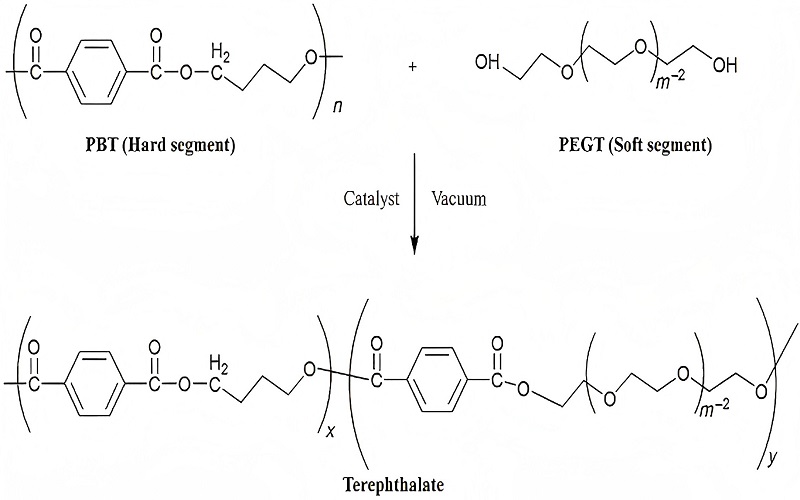
Polybutylene Terephthalate (PBT) is an engineering-grade thermoplastic polyesters plastics within the polyesters polyester family.
Renowned for its:
- High strength
- Stiffness
- Stain resistance
- Low moisture absorption
PBT serves as a versatile engineering pbt plastic classified as a semi crystalline semi-aromatic polyester.
PBT exhibits excellent mechanical properties, good mechanical properties, chemical, electrical properties, and pbt material properties, which are further enhanced by its toughness and ability to operate at high temperatures. This makes PBT a high performance material with improved performance and excellent mechanical properties and property.
The presence of aromatic rings in its structure contributes significantly to its high heat resistance, heat resistant properties, and good electrical properties.
Commonly used in electrical devices, automotive parts, and extrusion molding, PBT comes in various grades, including reinforced and flame-retardant options, to meet specific performance requirements.
One limitation of PBT is its susceptibility to degradation in strong alkalis and hydrolysis in humid environments, affecting its long-term durability in specific applications.
Synthesis of PBT
Synthesizing Polybutylene Terephthalate begins with esterification, where terephthalic acid reacts with butanediol to form esters. The polymerization process then follows, with temperatures lowered to form long polymer chains. PBT’s chemical structure, defined by its repeating unit of (C12H12O4)n, imparts distinctive properties and performance characteristics.
This synthesis method ensures consistent quality and performance across applications. Control over the polymerization process allows manufacturers to tailor PBT’s properties to different industrial needs, making it a versatile material in modern engineering.
Key Properties of PBT
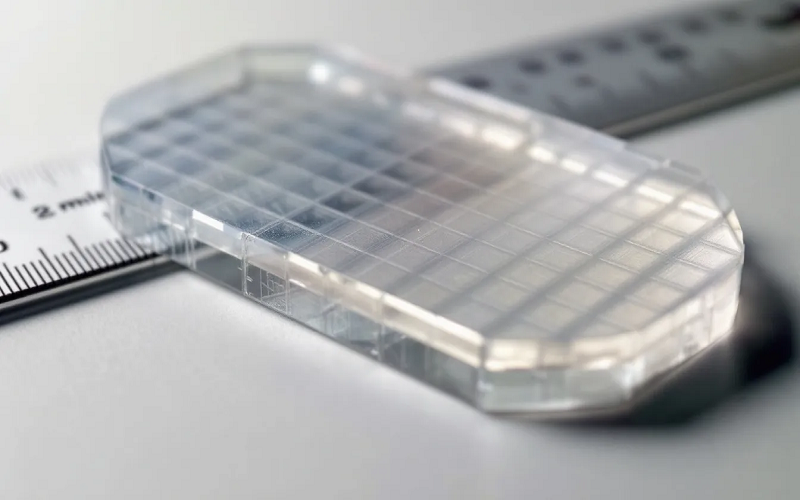
Celebrated for its high heat deflection temperature, PBT is suitable for high-temperature applications. Combined with dimensional stability and low moisture absorption, it remains durable under thermal stress and chemical exposure. With a low coefficient of thermal expansion, PBT experiences minimal dimensional changes with temperature variations, crucial for precision engineering.
Additionally, PBT’s significant strength, toughness, and stiffness contribute to its excellent impact resistance and impact strength, making it a reliable choice for demanding applications. Its good creep resistance, even at elevated temperatures, further enhances its performance in high-stress environments. These properties collectively make PBT a standout material in various engineering applications.
Mechanical and Electrical Properties
PBT’s mechanical properties, characterized by high tensile strength, toughness, and stiffness, make it effective for various mechanical applications. Resistance to wear and moisture enhances its long-lasting performance in harsh conditions. The material’s superior mechanical characteristics are a key reason for its extensive use in automotive and industrial applications.
PBT provides strong electrical insulation properties and dielectric strength, protecting electronic components from electrical discharge. These properties are crucial in the electrical and electronic sectors, safeguarding components from electrical leakage and breakdown.
PBT’s low dielectric loss is advantageous for high-frequency electronic applications, minimizing energy absorption and enhancing efficiency. Its excellent heat resistance further enhances its suitability for demanding environments. Its excellent mechanical and electrical properties make it highly sought after for demanding applications. The PBT polymer, often compared to polyethylene terephthalate, is primarily utilized in electrical and electronic components due to its robust characteristics, ensuring reliable performance in critical applications.
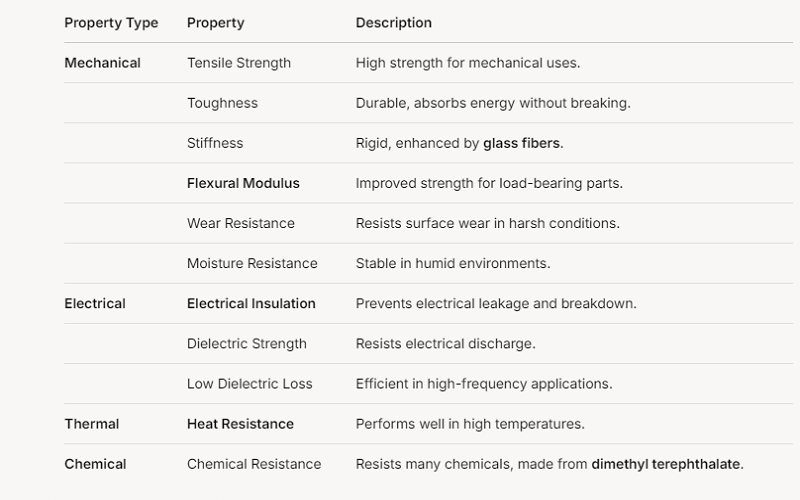
Chemical Resistance and Environmental Stability
PBT exhibits remarkable chemical resistance, withstanding exposure to various chemicals including:
- Acids
- Alcohols
- Oils
- Hydrocarbons like gasoline
- Esters
- Ethers
- Diluted acids
- Fats
This chemical resilience makes PBT a preferred material in environments with frequent exposure to these substances, thanks to its good chemical resistance.
However, PBT is not very resilient against strong alkalis, which can compromise its integrity. It is also not highly resistant to strong acids or strong alkali solutions, which could lead to degradation under such conditions. Despite these limitations, unreinforced PBT and PBT reinforced with glass fibers, which enhance its flexural modulus for improved stiffness and strength, offer overall chemical resistance and environmental stability. These properties, derived from its synthesis using dimethyl terephthalate, make PBT a robust material for many industrial and consumer applications.
Applications of PBT
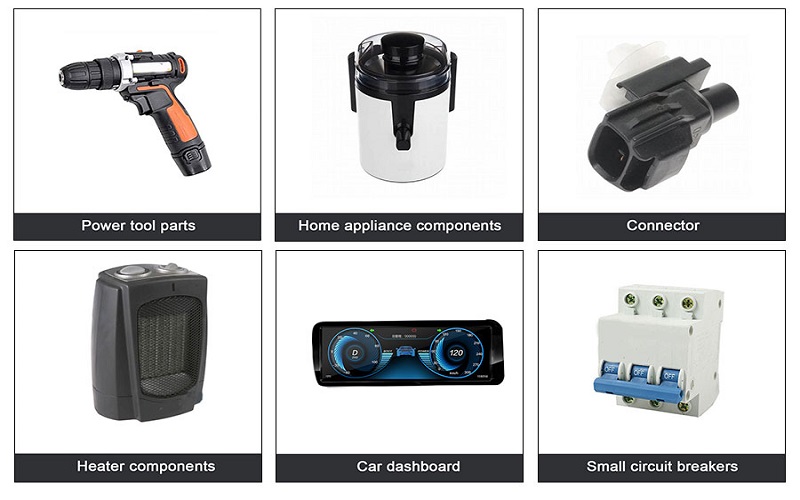
PBT’s diverse applications span across various industries, including automotive components, electrical, medical, and consumer goods. In the automotive sector, PBT is used for both exterior and automotive interiors parts due to its excellent mechanical and thermal properties. It is particularly valuable in electric vehicle components, aiding the transition to sustainable transportation.
In the electrical and electronic sectors, PBT safeguards electrical components from electrical leakage and breakdown, making it suitable for circuit breakers, connectors, and solar panels.
Additionally, PBT is used in consumer goods, including durable items like appliance handles and office furniture components, as well as in household applications. Its high strength and impact resistance make it applicable in industrial settings for items such as lamp bases and pump housings. Companies are increasingly integrating PBT into their products to meet the growing demand for environmentally friendly materials in various industries.
PBT in Injection Molding
PBT’s excellent properties, durability, and heat resistance make it a preferred choice in injection molding applications. The cylinder temperature for injection molding should be maintained between 240-250°C for proper processing. The required mold temperature for PBT should be above 40°C to ensure high performance. Pre-drying PBT before injection molding is recommended to keep moisture content below 0.02%, ensuring high-quality outputs.
PBT can withstand high temperatures, with a maximum service temperature ranging from 80 to 140°C, enhancing its versatility. These processing conditions and properties make PBT reliable for high-precision injection molding applications, ensuring consistent quality and performance.
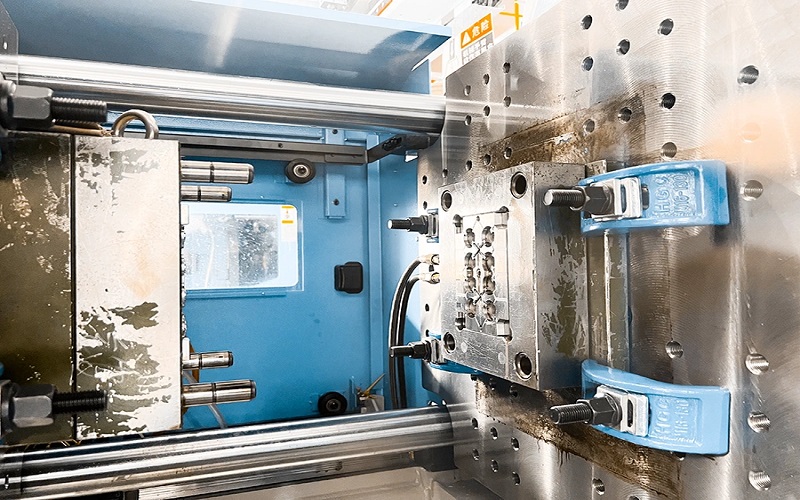
Blends and Reinforcements
Blending PBT with two materials can significantly enhance its properties and performance. For example, blending with polyethylene improves mechanical properties and reduces moisture uptake. Alloys of PBT and polycarbonate maintain toughness at low temperatures and provide excellent resistance to fuels and weather, making them suitable for various applications such as automotive parts.
These blends contribute to a broader range of applications and enhanced performance characteristics. Combining PBT with various thermoplastics allows manufacturers to tailor properties to meet specific needs, ensuring optimal performance in diverse applications.
Flame Retardant Grades
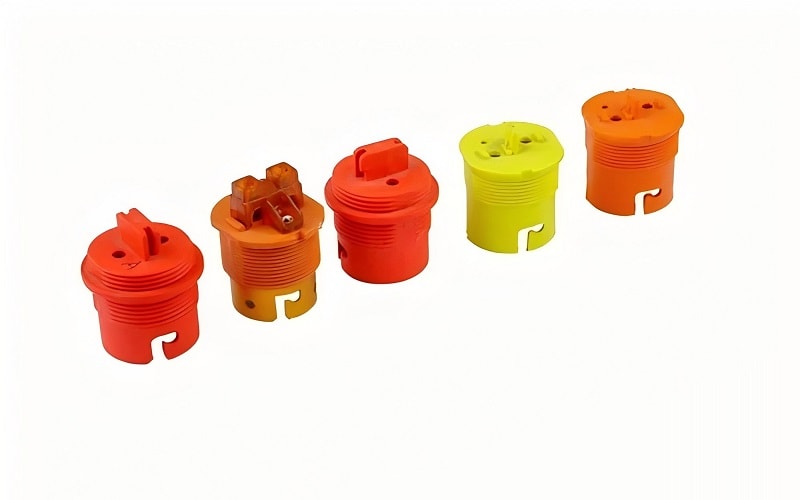
Certain flame retardant grades of PBT possess high glow wire ignition temperatures, ensuring compliance with stringent safety standards for household appliances. These grades maintain the material’s properties while enhancing safety, making PBT reliable for fire-resistant applications.
Developing flame retardant grades of PBT addresses safety and performance requirements, ensuring the material meets high standards demanded by modern applications.
Environmental Impact and Sustainability
Ongoing research focuses on obtaining PBT ingredients from biomass and designing efficient recycling systems, aligning with circular economy principles to minimize waste. PBT demonstrates good resistance to UV radiation but can be affected by moisture and high temperatures, leading to hydrolysis over time.
Recent trends have prompted the development of halogen-free flame retardant grades of PBT, addressing safety and environmental concerns. These advancements ensure PBT remains sustainable and environmentally friendly for diverse applications.
Comparison with Other Thermoplastics
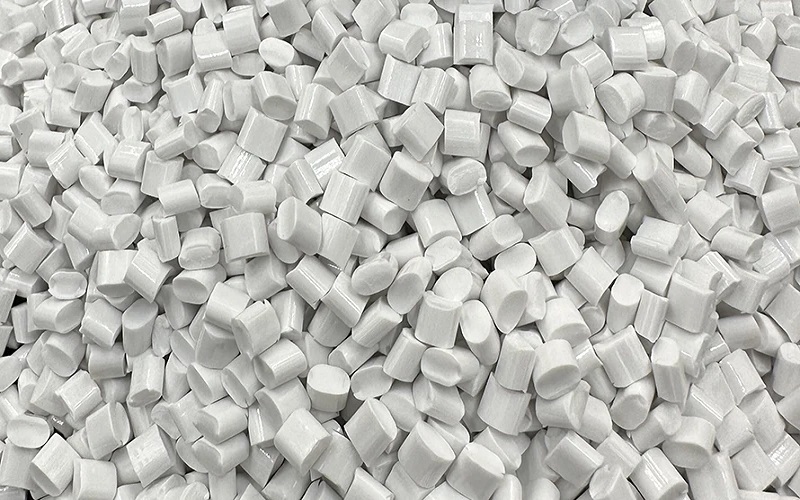
PBT is often compared with Polyamide 66 (PA66) and polypropylene (PP) due to differences in their physical properties and application suitability. Unlike PBT, PA66 has a higher melting point and maintains strength and stiffness at elevated temperatures.
However, PA66 can absorb moisture after molding, influencing its mechanical properties based on environmental conditions.
PBT burns without dripping, while PA66 produces a burning smell and emits a light blue flame during combustion. These differences highlight each material’s unique advantages and limitations, guiding manufacturers in selecting the most suitable thermoplastic for their applications.
Advantages and Disadvantages
PBT is known for being lightweight and cost-effective in various grades. It exhibits low moisture absorption and dimensional stability, key for durability in harsh environments. PBT is deemed safe for consumer products, having received FDA approval for food-contact applications. The European Chemicals Agency has evaluated PBT and does not classify it as hazardous under REACH regulations.
However, PBT is weak in extreme environments and not suitable for stronger acids and bases. Other engineering-grade materials such as PET and nylon now lead in certain areas. Despite these disadvantages, PBT remains valuable due to its unique properties and performance characteristics.
Health and Safety Considerations
Polybutylene Terephthalate (PBT) can be harmful if swallowed or heated to high temperatures, potentially leading to health risks. It is considered toxic when inhaled.
Additionally, it can be harmful if absorbed through the skin, gets into the eyes, or is swallowed. Additives such as bromine used in PBT manufacturing can lead to serious health concerns including cancer, apoptosis, and mutations.
While PBT is generally stable and non-toxic in normal use, its production may involve handling potentially toxic chemicals. Proper ventilation is essential when handling PBT pellets to prevent respiratory irritation from dust.
During high-temperature processing of PBT, safety measures are vital to manage any released organic solvents. Special care should be taken when using additives such as flame retardants due to potential health risks.
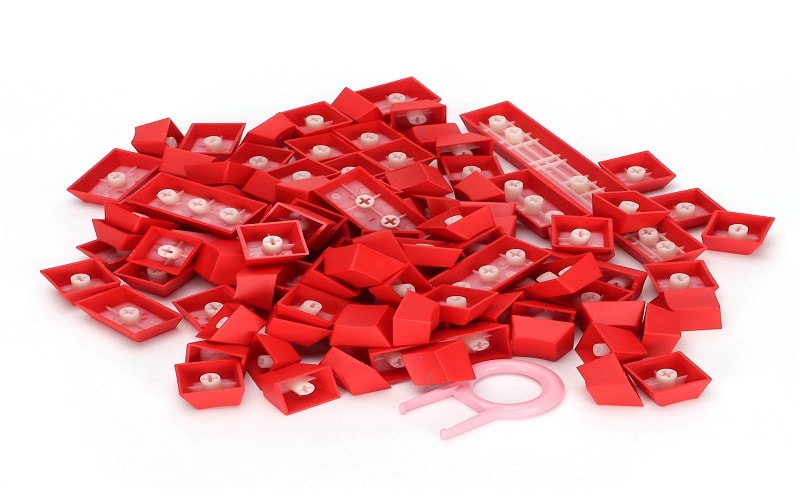
Summary
In summary, Polybutylene Terephthalate (PBT) is a versatile and high-performance engineering-grade thermoplastic with a wide range of applications across various industries.
Its excellent mechanical, electrical, and chemical properties make it a reliable choice for demanding applications. The material’s sustainability and ongoing research efforts further enhance its appeal in today’s environmentally conscious market.
By understanding PBT’s synthesis, properties, applications, and safety considerations, manufacturers and engineers can make informed decisions about its use in their products. As industries continue to evolve, PBT’s unique characteristics and performance will undoubtedly play a crucial role in shaping the future of material science and engineering.
Frequently Asked Questions
What are the key properties of PBT plastic?
The key properties of PBT plastic include high heat deflection temperature, dimensional stability, low moisture absorption, and notable strength, toughness, and impact resistance, making it ideal for demanding applications.
How is PBT synthesized?
PBT is synthesized through an esterification reaction between terephthalic acid and butanediol, followed by polymerization to create long polymer chains. This method effectively produces the desired polymer structure.
What are the common applications of PBT?
PBT is commonly utilized in automotive components, electrical appliances, medical devices, and consumer products, owing to its superior mechanical and thermal characteristics. This versatility makes it a valuable material across various industries.
What are the health and safety considerations when handling PBT?
Handling PBT requires strict adherence to safety measures, including ensuring proper ventilation, as it can be harmful if ingested or exposed to high temperatures. Thus, implementing these precautions is crucial to prevent health risks.
How does PBT compare with other thermoplastics like PA66 and PP?
PBT offers low moisture absorption and dimensional stability, making it advantageous in certain applications; however, PA66 outperforms it at higher temperatures due to its elevated melting point. Therefore, the choice between these thermoplastics depends on the specific application requirements.